Biofuel production is having a profound impact on water demand, according to a United Nations report.
“Despite their potential to help reduce dependence on fossil energy, biofuels with current technology are likely to place a disproportionate amount of pressure on biodiversity and the environment,” says the UN’s World Water Development Report 3.
“The major problem is the need for large quantities of water and fertilizers to grow the crops. Between 1,000 and 4,000 litres of water are needed to produce a single litre of biofuel.”
Read Also
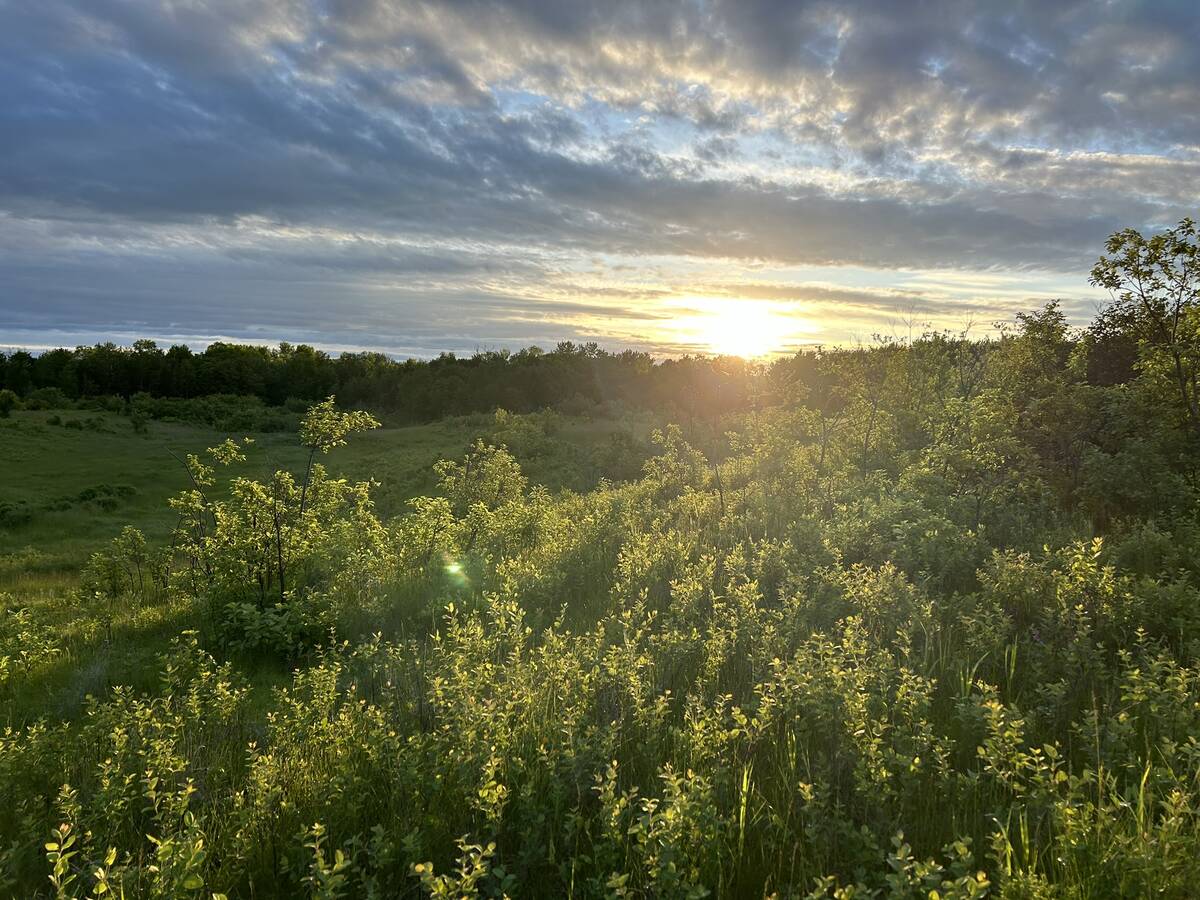
Manitoba farm group named finalist for national water innovation award
The Manitoba Forage and Grassland Association’s Aquanty Project for local hydrological modelling has earned them one of three finalist spots for a national award from Water Canada.
Global energy demands are expected to grow by as much as 55 percent by 2030, putting further pressure on an already stressed resource.
The UN predicted that in 2030, 47 percent of world population will be living in areas of high water stress because of climate change. Water scarcity will displace 24 million to 700 million people in arid and semi-arid regions, it added.
Don O’Connor, president of (S&T)2 Consultants Inc., said the UN study is flawed because it incorporates rainfall into the estimates of water use.
“That water would be falling on the land whether you were growing corn or not,” said O’Connor, a mechanical engineer recognized as a strong advocate of the biofuel industry.
“That’s just bad science.”
He doesn’t think the ethanol industry, which has a history of taking it on the chin for its water consumption, should be under the microscope in a world where no government regulations govern such matters.
“People are getting criticized for things that nobody has cared about before,” he said.
O’Connor wondered why the same critics haven’t been as concerned about how much water the oil industry uses.
A U.S. Department of Energy lab has studied both industries and has concluded that all forms of fuel production are heavy users of water.
“Our analysis indicates that conservation measures to reduce consumptive water use are needed to achieve sustainable biofuel and gasoline production,” said a report released earlier this year by Argonne National Laboratory.
However, it is clear from the results that ethanol is the bigger culprit, at least with today’s technologies.
The study shows corn ethanol plants consume 10 to 324 litres of water to produce a litre of ethanol. By contrast, gasoline production uses 2.8 to 6.6 litres of water, depending on whether it is produced from U.S. crude, Saudi crude or Canadian oilsands.
The large range in corn ethanol’s water requirements depends on where the corn is produced. Some production areas are far more dependent on irrigation than others. The study did not account for the use of rainwater.
Approximately 70 percent of U.S. corn and 68 percent of U.S. corn ethanol are produced in a region where seven to 14 litres of irrigation water is consumed per litre of ethanol produced.
Another three litres of water are consumed for every litre produced in the ethanol production process, which is a dramatic improvement over what it used to be in the early days of the industry.
Average water consumption in ethanol plants has declined from 6.8 litres per litre of ethanol to three litres per litre of ethanol in the past 10 years, the report said.
However, the end result is still 10 to 17 litres of water used to make one litre of corn ethanol in the key corn and ethanol production regions of the United States, far more than what the petroleum industry uses to make one litre of gasoline.
“That’s why we think cellulosic ethanol is more promising,” said report author May Wu.
O’Connor said the wheat-based ethanol plants being built in Western Canada have the advantage of using grain from nonirrigated crops.
However, the production process uses a little more water because wheat produces more distillers grain, which needs to be dried. He estimated the use rate would be in range of four litres of water per litre of ethanol.
But each plant is different. Some produce wet distillers grain instead of dry, others use technology that condenses water vapour going out the stack and some are recycling cooling water blow-down. As a result, it is difficult to apply an industry average to individual plants.
O’Connor said one certainty is that ethanol plants have become more economical in their water use over time, a trend that will continue in what is still an emerging industry.
Researchers say cellulose ethanol, which uses perennial grasses, wood and agriculture residues, algae and municipal wastes, could greatly improve the industry’s track record, depending on what production process is used.
Argonne had to estimate water requirements based on pilot plant results because cellulose ethanol technology has not been commercialized.
Plants using a biochemical conversion process will use an average of 9.8 litres of water to produce one litre of ethanol, assuming the feedstock was nonirrigated switchgrass. Once the technology advances, water use should drop to 5.9 litres to one litre. In either case, the process will use more water than most of today’s gasoline producers.
However, when a thermochemical gasification process is used, water use drops to 1.9 litres, which is better than any gasoline production method.
O’Connor is skeptical about that number. He said the thermochemical process produces a lot of waste heat, which needs cooling water to eliminate.
“Anybody is fooling themselves if they think that they can take 1.9 (litres) to the bank,” he said.