It was getting tight in Darryl Klassen’s 32- by 64-foot shop south of Kindersley, Sask.
The shop was part of the package deal when he bought what is now his home quarter. It quickly became a critical element in his oil hauling, custom spraying and new farming venture, which is now getting close to 5,400 acres of crop.
But while the old shop did its job well, Klassen decided he needed to get his equipment inside and warm for the winter. It was time to build his dream shop.
Read Also
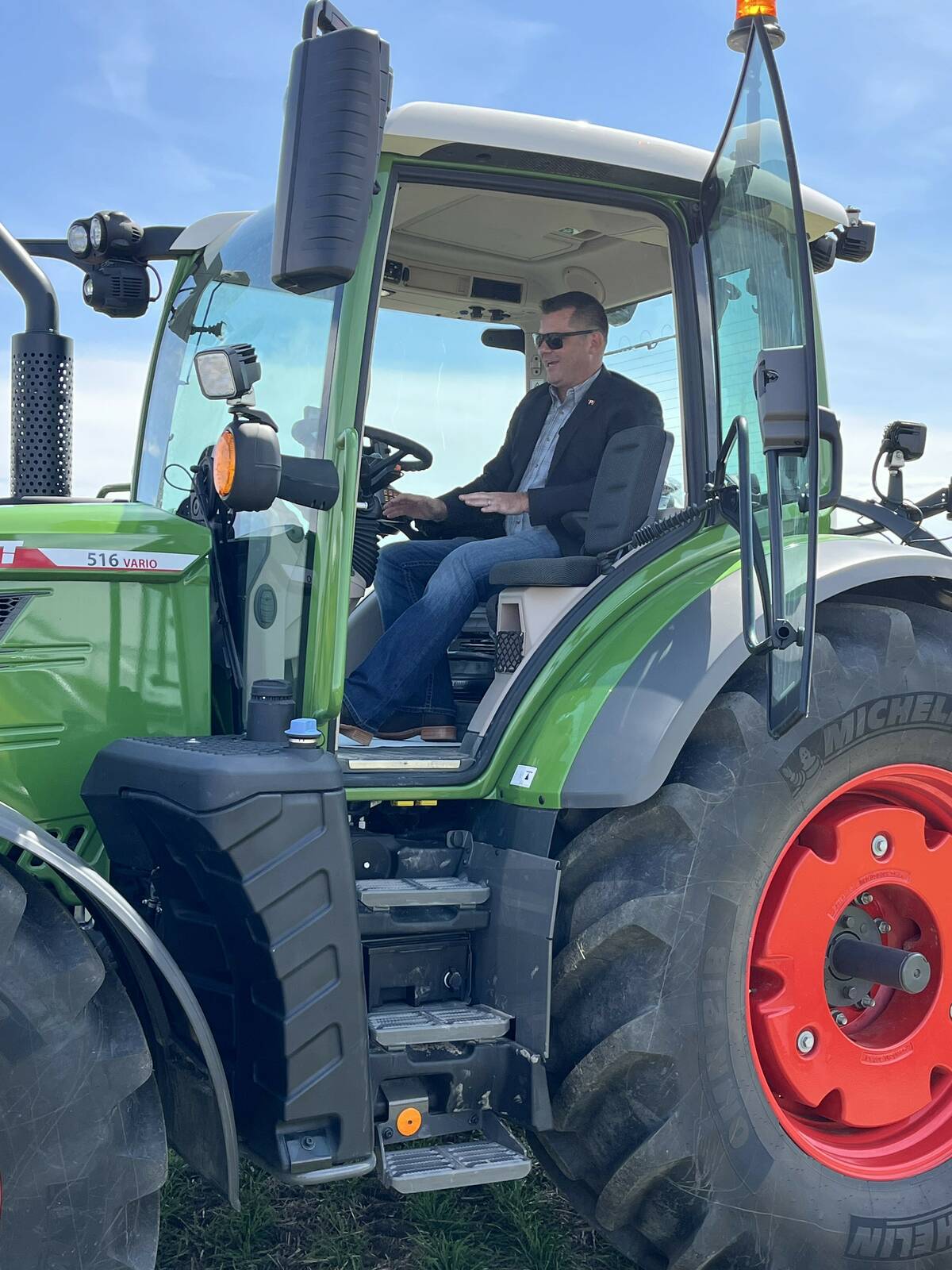
Farming Smarter receives financial boost from Alberta government for potato research
Farming Smarter near Lethbridge got a boost to its research equipment, thanks to the Alberta government’s increase in funding for research associations.
“I always had ideas of what I wanted a shop to be, and I kind of just made it happen. Even the banker thought I was a little nuts spending this kind of money on a shop. But by the time I’m 60 or 65, a shop like this won’t be needed anymore. I wasn’t going to wait until then,” Klassen said.
His new shop is 70 by 80 feet, with three 16 x 16 foot doors on the south side and two 16 x 22 foot doors on the north side. He also moved his existing 32 x 64 foot shop and attached it at a 90-degree angle to the new shop’s west side.
“This smaller portion would be about 12 years old. I had it moved over and moved up another two feet. It was only a 12 foot ceiling before and I changed that to a 14 foot ceiling,” Klassen said.
Before the movers could place his existing shop on its new spot, concrete needed to be poured, and before that could happen the piles had to go in. The shop is built on heavy clay land, so having proper pilings under the foundations and floor was critical.
“We decided to use screw piles rather than cement piles. So I got a hold of a bunch of old drill stem and then got all the disks cut out to make flighting for the screw piles. Then I took it over to the welding shop where they cut all the pipe to length, bent all the disks into flights and did all the welding,” Klassen said.
There are 10-foot-long screw piles, nine feet in the ground and one foot in the foundation, every 10 feet along the foundation, and through the door openings they were installed even deeper.
There are also screw piles installed under the shop floor, one for every 100 sq. feet, to prevent the floor from heaving and cracking.
The crew that built the shop from Zak Ag Buildings installed the piles. Klassen said it was cheaper to build and install the screw piles than to use concrete piling.
Pipes for floor heating were installed in the slab.
“I’ve always had a bad back. Even though a shop can be heated, being on a cold floor kills my back. Automatically, there was no question it was getting floor heat. We run that with a natural gas boiler. It heats all our domestic water for the shop and our water for the pressure washing system,” he said.
Air lines and the water lines for pressure washing were also placed down in the floor.
“The more stuff I can get off the floor the more efficient the shop is,” he said.
Once the concrete was poured, building movers came in and placed the older shop in its new position, with one end open and connected to the new shop.
The older shop is primarily a work area where tools are kept, which lessens clutter in the large shop.
Along the south wall of the old shop is a workbench and along the north wall are rooms including a bathroom, an office, lunchroom and a mechanical room. The boiler, air compressor and pressure washer are located in the mechanical room, which helps keep the noise down in the shop.
“Now this shop has a 14-foot ceiling, I didn’t’ see any need to have 14 foot ceiling in the bathroom or mechanical room, so we ended up with another 800 sq. feet of mezzanine above all the rooms, the bathroom, office, and lunchroom,” Klassen said.
This five foot space above the rooms is used for objects that need to be inside but don’t have to take up space on the floor. With his telehandler, Klassen can reach objects on the shelf, which are on a pallet.
Klassen had two older, 53-foot tandem van trailers that he also connected to the main shop beside where his smaller shop ties in.
“So I got to thinking, let’s just take the chassis off, put more screw piles in the ground, throw some I-beam down, set them down, and let’s have some accessible cold storage right from the heated shop. I don’t need to store parts in a heated shop,” Klassen said.
One of the vans has 53 feet of shelving on one side, while the other van has been left wide open, for larger items.
“The cement floor ties right into the floor on those vans, we can drive in there with a forklift if we have something heavy,” Klassen said.
The original plan was to have a wash bay on the east side of the shop, on the opposite side from where the smaller shop with the mechanic area and storage trailers connect.Then after visiting a friend’s shop, he changed his mind.
“He had a retractable curtain that come off the ceiling. I thought that was a good idea, I never liked the idea of a slide curtain; they’re always messy and they make a mess of the wall. So that changed my plan in the shop. That’s why there are two big doors on the back end.”
However, Klassen doesn’t regret installing the extra 16 x 22 door at the back of the shop.
“Last winter, when we got the building up I thought, wow, maybe it’s a little overkill. But you know what? We’ve had it jammed corner to corner so many times this winter already,” he said.
Klassen is also custom floating fertilizer throughout the winter, so he needs to keep his 4949 high clearance John Deere with a New Leader spin spreader box inside.
“Now, all of the sudden you have four semis that are leaving in the morning. You have six pieces of iron that have to go out. Never mind the other stuff you’re storing in here. I’m very thankful I put in as many doors as I did,” he said.
The shop is crucial for Klassen and his hands to maintain his heavy trucks.
“Labour rates around here for a shop, you’re going to range from around $100 to $130 per hour,” he said.
Renting a bay for a truck in the Kindersley area costs about $1,000 per month.
“I looked at renting a 50 x 80 shop by town that was $5,000 per month, so at $60,000 per year you can pay for a shop pretty quick,” he said.
Being able to fix his own machine is an important part of Klassen’s business model, which is why he prefers to run pre-emission standard trucks that he and his employees can easily work on.
“It doesn’t’ matter if it’s new or old, that stuff is all going to wear out and it all needs replacing within a few years. We’re not driving on the highway. We’re driving 90 percent gravel roads, and being a busy hub like Kindersley (means) the road maintenance crew does not keep up to the truck traffic,” Klassen said.
An added benefit to a large shop is that he is able to keep his employees busy during spring helping to service and maintain equipment. As well, the shop will be big enough to meet the needs of his businesses as it expands in the future.