The Technotill packer plate introduced by Walter and Betty Schoenhofer in 1996 has been re-developed with assistance from Saskatchewan farmers and a 3D printer.
TNT Version 2 will be available for spring seeding.
Where the original TNT had a fertilizer port on only one side, Version 2 is symmetrical with dual band ports. The previous design put side pressure on the in-ground working tools, causing the cultivator to crab walk, thus creating excessive wear on all components in the seed-fertilizer placement system. Version 1 has been discontinued, says TNT president and co-inventor Betty Schoenhofer, and Version 2 units are on the boat coming from the factory in China.
Read Also
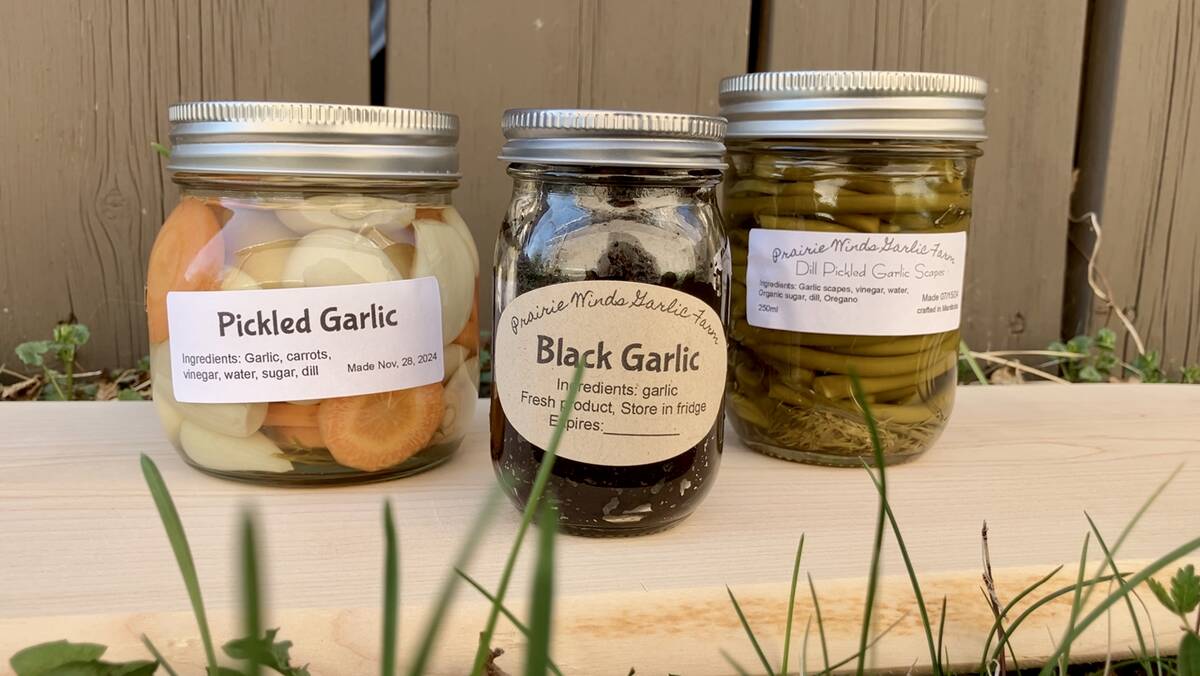
Growing garlic by the thousands in Manitoba
Grower holds a planting party day every fall as a crowd gathers to help put 28,000 plants, and sometimes more, into theground
The TNT plate is 1.25 by 4.75 inches of hardened steel. The actual packing surface is Hi Chrome with 1.25 by 1.25 inch tungsten carbide brazed on at the rear where the greatest pressure is applied to pack the soil. It can be adjusted to place and pack a ribbon of soil over the seed. Depth of this soil cover can be adjusted from 1/4 to 1/2 inches.
“Customers have always told us the packing plate design works especially well with shallow seeded crops like canola, and it’s good in difficult seeding conditions, such as extreme dry and extreme wet,” said Schoenhofer.
“But that single side port is the one factor that’s prevented more farmers from trying it. Changing to dual side band solves that side pressure problem, plus it allows farmers to put down more fertilizer with better seed separation. So now we have the advantages of the packer plate along with dual side banding.”
Developing and improving in-soil working tools has always been a tedious, expensive and time-consuming process. Minor changes are made to iron prototypes in the shop and then it’s back to the soil bins or the field for testing. It’s especially frustrating when engineers get down to the fine tuning stages.
All that changed with the advent of 3D printers. Design data is fed into the printer, the engineer presses the start button and the printer starts putting down layer upon layer of hot plastic. The product can be an airplane part, a handgun, a guitar or a new packing system. As the product is tested, engineers can make tiny changes in the design and feed those changes into the machine for a new prototype within hours.
“Jason Knott at Framework Animation in Lethbridge did all our 3D printing,” Schoenhofer said.
“After the first tests, we realized his 3D prints were strong enough to be tested under actual field conditions. We used downward pressure and speed that you’d actually use in the field.”
Multiple prototype versions were tested in 2016 in soil bins at Lethbridge, PAMI and AgQuest west of Saskatoon.
AgQuest research agronomist Ted Nodge installed Version 2.0 plastic packers on its plot seeder, which was similar to the type of cultivator frame commonly outfitted with TNT packers. When they ran the test, the seeder had some TNT prototypes and some older Version 1.0 packers. They tested on fallow and wheat stubble.
“This let us compare seeding depth, fertilizer placement and consistency,” said Nodge.
There was no significant difference in draft requirement. They’re a little bigger because of the extra fertilizer port, but the new design is more streamlined, so that equalled out.
“We found we could put down more than double the fertilizer volume we’d been putting down with the older ones,” he said.
“We were putting down 100 kilograms per hectare (540 pounds per acre) without plugging. They were pretty impressive.”
Schoenhofer said the 3D process allowed her to achieve her goals relatively quickly. Version 2 has improved fertilizer placement, more precise coverage when seeding shallow and no side force issue.
“Final field testing was done by a group of our customers in the spring of 2017. These are farmers who’ve had years of experience with the original Technotill, but they didn’t do side-by-side yield comparisons,” he said.
“Yield comparisons with other systems is step two. That will start in 2018. I had to make sure I got the design right first. We’ll hold our own. In difficult conditions we’ll do better than other systems. And with simpler technology and less cost, I’m pretty confident about our future.”