FARGO, N.D. — Within the overall realm of cultivation and seed and fertilizer placement equipment, the in-ground working tool is the one singular component that continues to evolve rapidly. Every farm show seems to feature new soil-working steel.
Money is a chief reason for the on-going focus on developing new soil-working tools. When dealing with trash management and seed bed preparation, it’s more cost-effective for a research and development team to fine tune in-ground tools than to design a whole new machine. Costs aside, fine-tuning in and of itself can give engineers greater performance benefits than modifications to the basic drill or cultivator. After all, it’s the in-ground tool that does the actual work.
Read Also
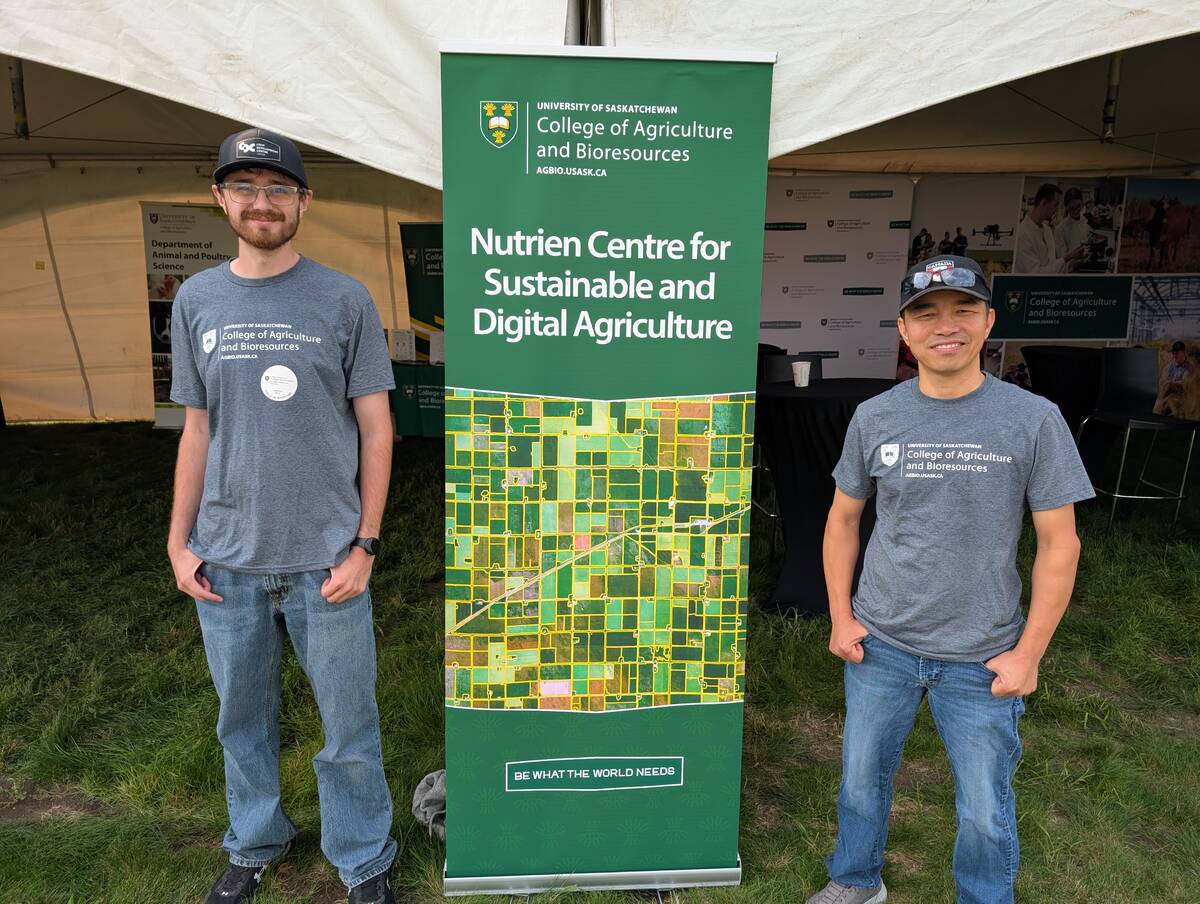
Field-by-field mapping could improve yield, productivity predictions
University of Saskatchewan researchers are using field border mapping to collect data on field variability, including problematic weeds, and to predict things like yields.
Trying different options and combinations are your best bet when you get right down to the nitty gritty of extracting optimal performance from your seeder or cultivator, says Wade Oman, territory manager for Kuhn Krause in Hutchinson, Kansas. Farmers from Western Canada and the U.S. Plains and Canadian Prairies got to experience the gear at the Big Iron farm show in Fargo this past fall.
The Kuhn machine that attracted the most attention at the show was the Excelerator 8005 vertical till cultivator, which mixes soil and residue and prepares the seed bed in a single pass. Kuhn claims its Excalibur blades are designed to cut tough GMO residue to promote maximum residue decomposition over winter.
There’s no denying it, the Excalibur blades look vicious with their scalloped circumference, self-sharpening edge and 32-flute design. The geometry of the cutting edge is engineered to penetrate the soil and residue, leaving only small clods of dirt. If there’s time in the spring, a second field pass will create superior seed bed preparation in high residue situations, Oman said.
“This Excalibur blade at the front is from Ingersoll, and it’s an excellent choice for that position,” he said.
“The steel is a boron composite. It’s not flat. There’s a little bit of a dish to it, giving it 40 percent more strength in rocky conditions. And, because it’s self-sharpening, they’re typically good for 20,000 acres.”
Until recently, most manufacturers built their vertical till cultivators with the coulters at a fixed angle. That pre-determined angle might be ideal in some field conditions but totally wrong in other situations.
Oman said farmers wanted a wider range of coulter angles so they could do more soil disturbance in certain conditions. In addressing the issue, Kuhn devised an adjustable system for the 8005 with a range of one to five degrees.
“It’s hydraulically controlled from the cab of the tractor. Once you go beyond five degrees, it’s really not what you’d call vertical tillage anymore. The whole dynamics of the machine change. Then it’s more like a disc machine,” he said.
“You adjust soil movement and residue mixing by adjusting the gangs. One degree gives you maximum residue retention with minimum soil disturbance. Five degrees gives you maximum soil movement and maximum residue mixing. Shallow angles like this prevent soil smearing, especially when compared to older disc harrow technology with gang angles typically from 10 degrees to 22 degrees.”
Another unique feature on the 8005 is the star wheel that follows between the paths of every pair of coulters. Oman said that on any vertical till machine, the soil strip between any two coulters is not disturbed. The mid-section surface crust remains hard.
“So we’ve designed these star wheels to break up that centre crust to give you a uniform seed bed,” he said.
“They aggressively mix soil and residue, they pulverize large clods and they remove soil from root balls. Plus, they catch residue flowing through and spread it evenly. The star wheel gangs are spring mounted to follow the contour over varying field surfaces, provide a uniform finish and evenly distribute residue across the soil surface. They’re on hydraulic cylinders so you adjust the down pressure from the cab.”
With baskets at the rear of the 8005, one pass in the fall usually creates a good seed bed without further harrowing. If the field is still too rough, the 8005 can run at 40 m.p.h., so a second spring pass is an option. The 8005 requires 10 horsepower per foot. Maximum size is 50 feet. To help save time, the spherical pivot bearings in the walking beams do not require daily greasing.
The 40 foot 8005 on display at Big Iron carried a price tag of about US$139,000.