FARGO, N.D. — Central tire inflation systems are gaining ground with operators who see the value of running maximum allowable tire pressure in transit and minimum allowable tire pressure in the field.
Adjustable tire pressure has become a major factor because of the growing awareness of the impact that soil compaction has on yield. Changing pressure up and down in a hurry has become more important as farming operations become more spread out with fields 20 or 30 kilometres apart.
Rubber tracks were the first obvious solution. To a great extent, tracks solved the problems of compaction and keeping equipment from getting stuck as often in muddy conditions.
Read Also
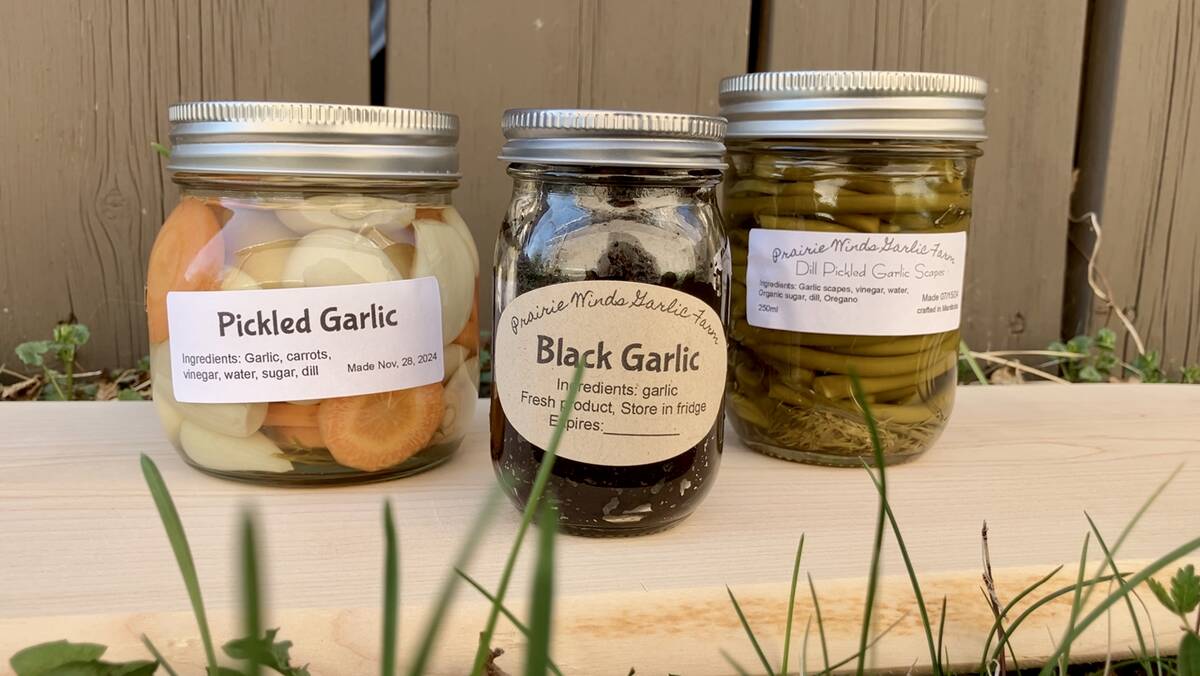
Growing garlic by the thousands in Manitoba
Grower holds a planting party day every fall as a crowd gathers to help put 28,000 plants, and sometimes more, into theground
However, just as obvious was the fact that rubber track machines could not keep up with round rubber tires on the road. As distance between fields increased, farmers have gradually begun to take tires seriously again.
The latest generation of extreme low pressure technology meant that tires were once again on a roll.
Like rubber tracks, ultra-low pressure tires reduced transit speed to a slow crawl. To the rescue came central tire inflation systems. Approximately 10 years ago, using a variety of different engineering approaches, companies devised compressors and air relief valves so operators could make those tire pressure adjustments.
However, time is money. Wasting five or 10 minutes at the edge of the field waiting for the pressure to go up or down was a big negative factor that prevented many farmers from buying into the central inflation concept. As more companies entered the marketplace, competition heated up for the title of “fastest central inflation system.”
The company with the fastest system will sell the most units, according to Sally Brodbeck, owner of Precision Inflation in Des Moines, Iowa. Brodbeck said she imports the CTIS/radial dual line system that was developed in Germany 25 years ago and is one of the leading systems in Europe.
“Farmers in North America are trading in their rubber tracked tractors and buying tractors with tires,” Brodbeck said. “Tracks are heavy, they cost more, they consume more fuel, there’s a lot of maintenance and you get dinged on the trade-in.”
Brodbeck said farmers who travel to Europe notice there are no tractors with rubber tracks.
Instead, they all have tires. This is because when North American farmers were first introduced to rubber tracks, European farmers already had access to central inflation systems. They considered the two options and decided in favour or central inflation. The main reason is that European farmers do a lot of road transit.
“I love tracks, I really do. They’re trying to do the right thing for farmers and for the soil, and they do a good job of it,” she said.
“But I look at tracks and think to myself, ‘I can give them a better product for less money.’ Our system is re-useable. When you go to trade your tractor, you can easily remove the system and put it on your next tractor.
“Farmers tell us they want to make the best use of the new tire technology, like the VF tires. They want to keep their pressure at the recommended pressure of six or seven p.s.i. But during the day, those tires heat up and the pressure goes up by four or five p.s.i. higher. Now they’ve lost the advantage of the high tech tire which they paid a premium price for.
“Those tires are great in the field, but when you get on the road, they’re squishy. They squirm around very badly, and they wear out very quickly. Now we see companies like Michelin coming out with tires designed specifically for central inflation. That trend will continue to grow. Their new Evo Bib can only go on tractors with central inflation.”
She said these tires are designed so the sidewall does not contact the road surface in transit. Higher air pressure raises the tire so the centre of the tire carries the weight and the sidewalls are stiff.
In field mode, the sidewall softens and squishes out to reduce pressure on the soil. Central inflation is required for these new generation tires, she added.
Brodbeck said precision is critical. The tires need to stay within the recommended range, and they must all carry the same pressure.
She said that when her Precision Inflation system has completed it’s inflating or deflating process, it equalizes tire pressure right across the axle so all tires are within half a pound p.s.i. s of each other, even if you’re running triples.
She said her system can handle three axles concurrently. Three pressure zones let the operator control two axles on the tractor and one additional zone for the implement.
“Our CTIS/radial dual line uses what we call a two line system,” she said. “The lines are under pressure only when you’re pumping the tires up for the road or deflating the tires for the field.
“The seals are designed for 10,000 hours without any maintenance. I’ve been bringing these over for six years, and in that time we’ve had virtually no trouble with the seals. I talked to one farmer in Germany who has 15 years service on his system and he’s done no maintenance at all. It still has the original seals.”
One unique feature of the CTIS design is the rotary union installed between the axle and centre of the wheel. This sheltered location protects the seal and helps it stay healthy for 10,000 hours of operation. The air lines run from the rotary union through the centre of the wheels so all lines remain protected regardless of conditions.