There’s no doubt anaerobic digesters work, but making them economically viable in Canada’s extreme prairie winter is another matter.
Anaerobic digesters use heat to convert biomass, whether it’s for generating electricity or producing environmentally friendly materials.
There are two types of digesters: the more common mesophillic digestion system that functions at 35 C and thermophillic digestion that functions at 55 C.
“The higher 55 C temperature in a thermophillic system gives you higher biogas production, creates more total energy and gives you a higher rate of biodegradation,” said University of Manitoba PhD candidate Elsie Jordaan, who recently presented her findings after touring a dairy-based mesophillic anaerobic digester in Wisconsin.
Read Also
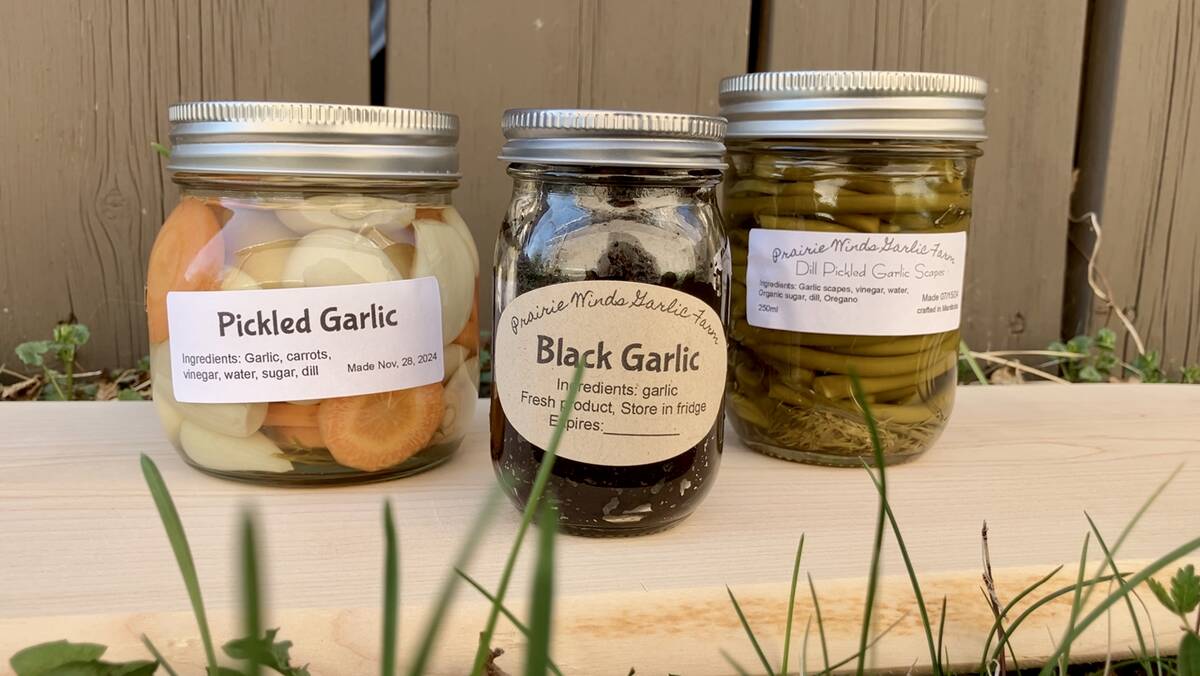
Growing garlic by the thousands in Manitoba
Grower holds a planting party day every fall as a crowd gathers to help put 28,000 plants, and sometimes more, into theground
She said there are fewer of these in North America, even though they maximize the efficiency of the feedstock and the facility.
“Thermophillic digestion is a lot trickier than mesophillic,” she said.
“It’s more difficult to nurse the bacteria all the way up to 55 C than to 35 C. The higher you go with the temperature, the more chance of accidentally killing off the whole population. It takes a long time to get that bacteria community working for you.”
Wisconsin, where winter conditions are similar to those in Canada, has more dairy-fed anaerobic digesters than any other state, including those in much warmer climates.
Making sure enough biomass feedstock is on hand to dump into the digester the moment it’s needed is the key to keeping the bacteria warm, healthy and hungry in any system, especially in winter conditions.
Many Wisconsin dairy farms ensure an adequate supply of feedstock by using co-digestates consisting of additional straw, waste corn silage and mouldy feed along with off-farm materials such as cheese whey, food waste grease and glycerol from biodiesel production.
Most farms buy back their dried digested solids to reuse as bedding.
“Yes, they are running the same material through the digester, but for good reasons,” Jordaan said.
“It’s cheaper than buying fresh straw for bedding and the recycled material is right there in the yard, so transportation costs are minimal.”
She said straw is an intractable organic substance and difficult to break down by anaerobic digestion. There is enough good material to serve as bedding, even when it goes through the digester a couple of times.
Remaining digested solids that don’t go back to the point of origin are sold as bedding to neighbouring farmers or as soil amendments, with prices ranging from $10 to $35 per ton.
Dairy farms use some of the electricity that they generate and sell the rest into the local power grid. The 29 Wisconsin dairy digesters generate 121,000 megawatt hours of power, all the while cleaning dairy manure to acceptable standards.
The 29 Wisconsin dairy digesters are set up exclusively for dairy and other non-hog co-digestates.
Dairy-based digesters are typically mesophillic and thus cheaper to build, faster to start up and easier to manage over the long term.
The Dane County Community Digester project was developed after the county banned winter manure spreading.
It was set up as a community project because none of the three farms involved had enough cows on their own to justify a stand-alone system. The three together have a total of 3,000 head, all located within the maximum recommended distance of 600 metres from the digester, thus making the system economically viable.
The Dane County Community Digester produces 19,000 kilowatt hours of power at a value of $2 million.
The facility is designed, owned and operated by Clear Horizons, a private energy company. Under a 15 year agreement with the three farms, Clear Horizon owns all the biogas and electricity and is responsible for all plant and business operations.
The three farms must provide enough manure feedstock, which they pump to the plant through eight inch diameter underground pipes. They also accept the liquid digestate, which can be sold or used on-farm.
The Dane County facility might be considered a simple, off-the-shelf low-temperature mesophillic digester, but it still took 18 months to tune in the physics, mechanics, electronics, chemistry and digestate factors so that the system functioned as Clear Horizon intended.
During that time, the cost to Clear Horizon was an additional $5 million. Although the initial projection was a 15 percent return on investment, the extra start-up cost affected the original number.
Jordaan said tuning a biodigester is no easy task.
“The exact feed recipe is determined through trial and error and is adjusted at the operators discretion to optimize biogas production,” she said. “When required, additional bio material is trucked to the plant.”
There are three collection components:
- The underground lines run to the manure reception tank.
- An above ground tank stores additional waste products.
- A below-ground open pit holds additional manure and other feedstock products.
Jordaan said nearly everything is covered so there is little odour, unless standing next to the open pit and looking down.
There are three digester tanks, each holding 4,500 cubic metres of biomass. Stirring is constant with two top mixers and three mixers within the tank.
The tanks have elastic, inflatable type covers to capture the methane coming off the top of the soup. The walls are nearly eight metres high, so there are six to eight hours of methane storage within the flexible cover at the top of each tank.
After the methane is extracted from the flexible roof, it goes through a scrubber to remove hydrogen sulfide, which would prove to be fatally corrosive to the generators.
The methane is then ready to serve as the primary fuel for the two one megawatt GE Jenbacher generators.
Once the maximum amount of methane has been extracted from each digestion tank, the remaining soggy digestate goes into a Centrisys centrifuge to separate solids from liquids. Liquids are pumped back to the farm of origin and solids go to the drying drums to extract remaining liquid.
“The liquid concentrate is stored in lagoons for land application,” Jordaan said. “The phosphorus has been reduced by 60 to 70 percent. Waste heat at any point in the system is utilized to heat the digesters and the other buildings.”
For more information, contact Elsie Jordaan at umjordaa@cc.umanitoba.ca.