FARGO, N.D. – Farmers may be among the world’s best welders, but they’re facing new challenges as more stainless steel and aluminum is incorporated into farm equipment.
Increasing steel prices are behind the move as farm equipment manufacturers reconsider a variety of other metals and materials.
“Price is causing us to consider other products that we thought were out of reach before,” said Robert Fagnou of Bourgault Industries in St. Brieux, Sask.
“They haven’t come down any, but as they compare to steel they have become more competitive, and many have some great weight and wear properties we like.”
Read Also
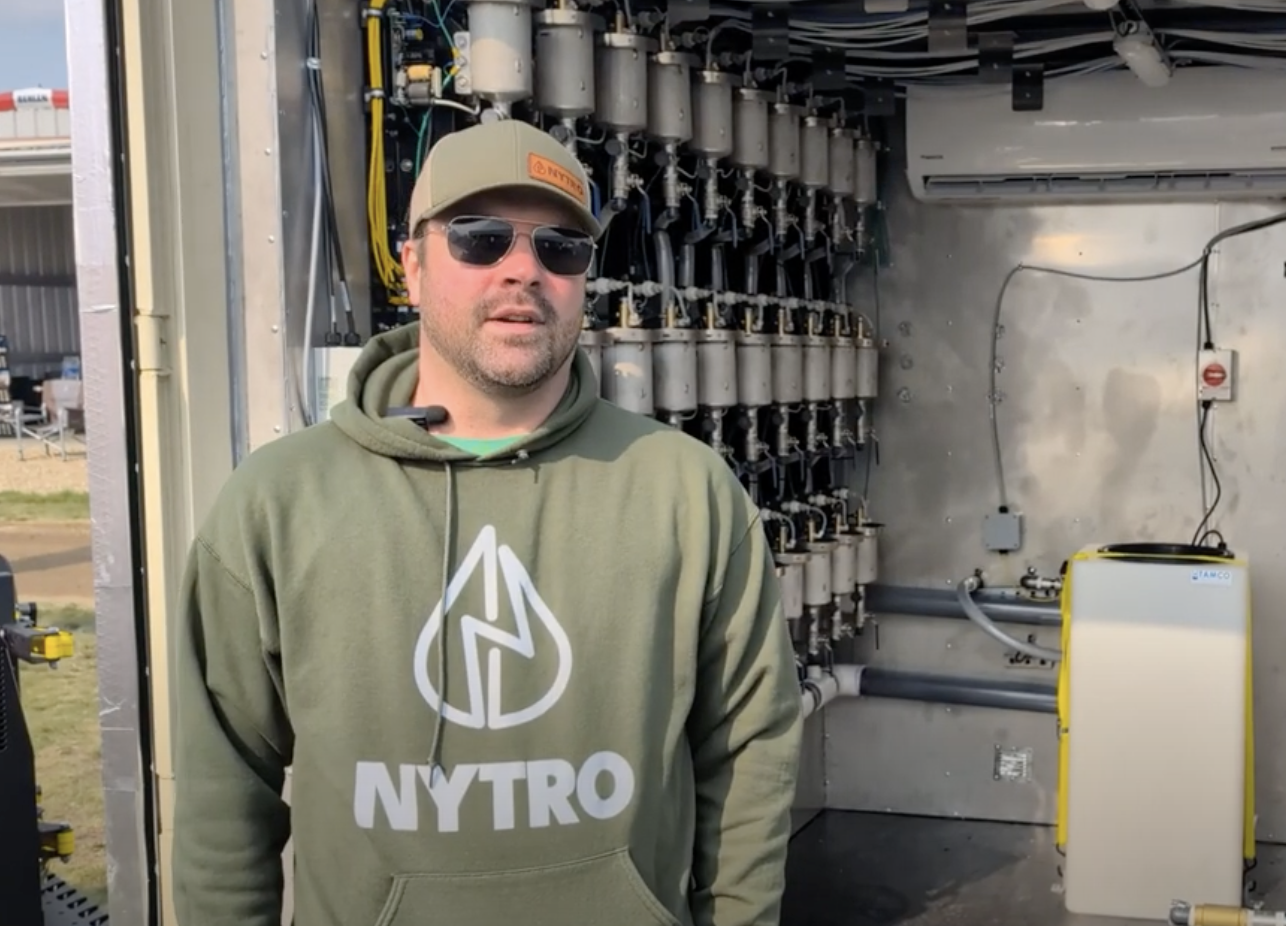
VIDEO: Green Lightning and Nytro Ag win sustainability innovation award
Nytro Ag Corp and Green Lightning recieved an innovation award at Ag in Motion 2025 for the Green Lightning Nitrogen Machine, which converts atmospheric nitrogen into a plant-usable form.
Marflex, an equipment manufacturer in Brooks, Minnesota, is using stainless steel to make all the metal components that come in direct contact with chemicals on its new Marflex truck sprayer.
“We use stainless wherever we can because we know it should last virtually forever,” said Marflex president Jay Mercil.
“We build sprayers for export to Russia and Eastern Europe. It’s expensive and difficult to provide good quick service if something breaks or corrodes prematurely, so we start out with the best metal for the job, and we think that’s stainless steel.”
Brent Friesen, manager of Novid, which manufactures stainless steel fertilizer tanks in Morris, Man., said stainless steel will last two to three times longer than mild steel.
“People are used to thinking the cost is extremely high, but in reality stainless steel is only slightly higher than mild steel. So when you consider the longevity, it’s a good investment.”
Friesen thinks farmers can expect to see more stainless steel on components subject to corrosion or heavy wear.
Staff at Seed Hawk in Langbank, Sask., say the now affordable alternatives to steel in many cases are improving their products because of higher durability, reduced manufacturing costs and reduced weight.
The increase in aluminum comes partially from the need to reduce the weight of some types of components and partially because of the escalating price of steel.
“We’re seeing more aluminum in the corn heads we import from Europe,” said Stewart Peterson of North Country Marketing in Fargo.
“Weight is a big factor on a combine head or any other mechanism that’s hung out away from the implement like that. On our new Cressoni Roto heads, all the gearboxes are made with tempered aluminum alloy to save weight.
“With a 10-row header, a weight reduction of 50 pounds per row means 500 lb. less weight bouncing around way out in front of your combine.”
In working applications such as gearboxes, where heat can be a problem, aluminum transfers heat to the atmosphere better than cast iron or mild steel.
“Farmers aren’t afraid of aluminum the way they used to be,” said Dwayne Bulizuik of Gaber Distributors in Dauphin, Man.
“Just look at all the aluminum trailers we see on the road now. We’re finally getting used to the fact that aluminum has some advantages over steel.”
Ilie Irinici of Acklands Grainger in Saskatoon, which sells welding equipment and supplies, said farmer welders aren’t having any trouble adapting to aluminum and stainless steel.
“They are learning to work with the new metals they have in their machines,” he said.
“The new (MIG) welders are very easy to operate and most can be simply upgraded to a spool gun for welding these materials.”
Bulizuik, whose company has sold aluminum spray booms for 10 years, said farmers who need structurally significant parts repaired should use a certified aluminum welder.
“Don’t do it yourself unless you’ve got the training.”