Leading edge grain dryer technology, originally aimed at the U.S. cornbelt, is migrating to the Canadian Prairies.
Dave Wall of Wall Grain in Winnipeg recently sold two MC tower dryers to Manitoba customers. He said there are at least a half dozen such tower dryers in Manitoba.
A tower dryer reduces fuel consumption by 40 percent while re-capturing heat as it cools the warm, dried grain.
Wall agrees that tower dryers reduce energy consumption and can also cool grain to safe storage temperatures, yet he is reluctant to give them an all-out endorsement.
Read Also
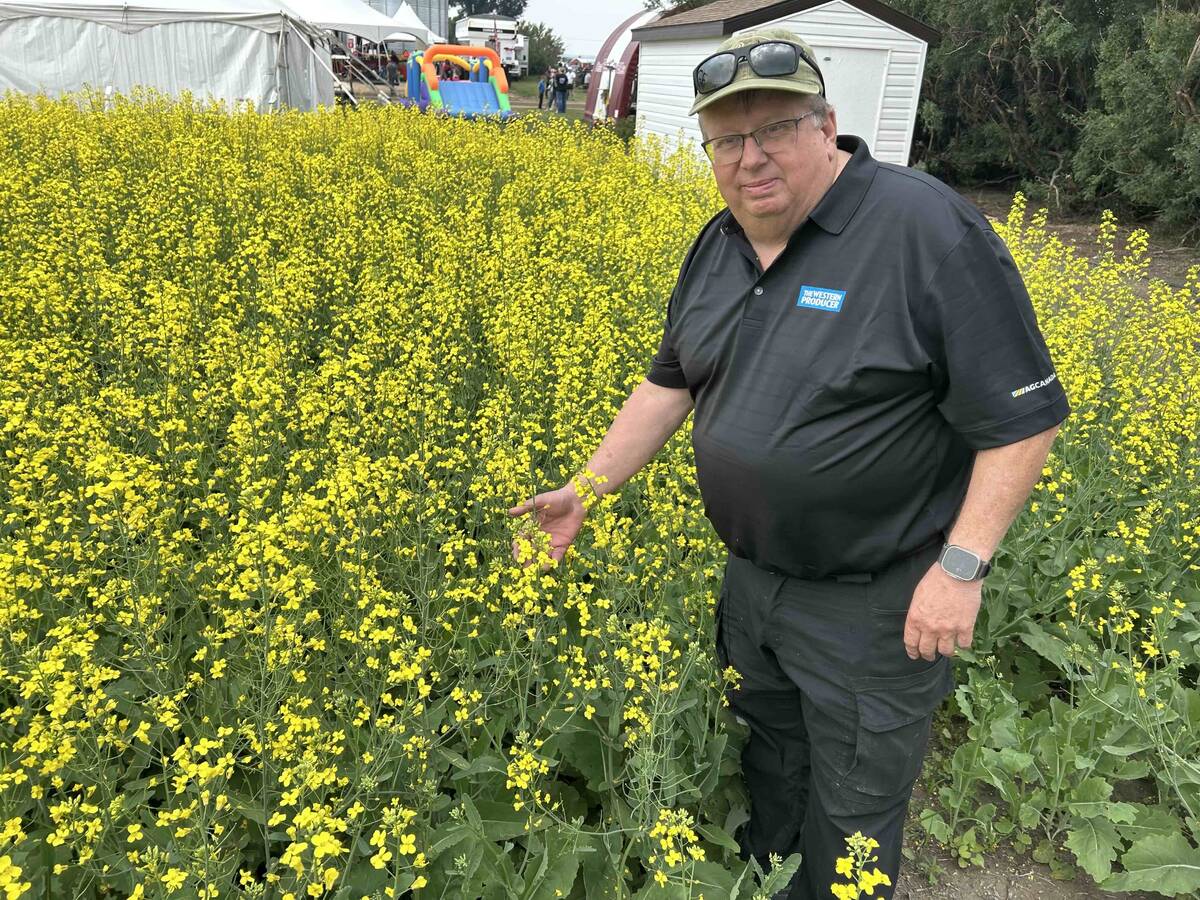
Crop conditions a pleasant surprise
Market analysts found some stressed crops and some good ones on pre-Ag In Motion 2025 crop tours,
“It’s mainly a corn dryer. It’s not really designed for our prairie conditions unless you have a lot of corn,” he said.
“They do handle wheat, but you absolutely cannot put in canola or flax or sunflowers. Period. Any of those crops will burn for sure.”
Wall said people like tower dryers because they suck fresh air for the burner through the warm, dried grain. This cools the grain before it’s augered out. All the re-captured heat goes back into the dryer where it’s put to good use on the next incoming layer of grain.
The two MC tower dryers Wall sold include what he calls a “small one” measuring 10 feet in diameter by 50 feet high and a “big one” that measures 12 feet in diameter by 70 feet high. Prices run from $150,000 to $200,000 Cdn.
“In most situations, I think a conventional dryer is more suited for farmers,” said Wall. “You need to be a commercial operator or else a really big farmer to justify that kind of investment. For example, the Weyburn Inland Terminal. They’ve had a tower dryer of some sort for many years.”
Volume needed
The Weyburn Inland Terminal, one of the largest grain gathering facilities on the Prairies, bought one of the first tower dryers.
Terminal manager Gordon Anderson said they paid about $250,000 for the French-built unit, which dries 50 tonnes per hour.
“We bought it eight years ago, but we haven’t used it for the past three or four years,” said Anderson.
“On average, you need a grain dryer on the Prairies only two years out of 10. That’s a rule of thumb that I think applies to most of the prairie provinces.”
He said a big facility like Weyburn has less use for a dryer than smaller operations. Their high throughput allows them to blend tough grain with dry grain to get an acceptable average.
(Continued on next page)
“We need a lot of tough grain to justify firing up the dryer. But if we run it for a six-month period, it pays for itself.
“The computer monitors the temperature and moisture of the incoming grain. It makes all the adjustments automatically. It knows when to bring grain in and when to augur it out.”
Sucking air
The MC tower dryers sold by Wall are also fully automated. MC calls them vacuum dryers because they suck cool incoming air through the warm grain.
This is the only route available for fresh atmospheric air to be drawn into the combustion chamber.
An elevator brings high moisture grain to the top two-thirds of the tower. This top section is the only compartment that receives heat from the burners, located just below the two-thirds mark.
Naturally, the driest grain is the layer at the bottom of this drying compartment. Sensors tell the computer when this bottom layer is dried down to the specified moisture content, at which time the computer allows grain to flow through the floor of the compartment.
The computer accomplishes this by controlling the speed of a rotating sweep on the floor of the drying compartment, thus sending the warm dry grain down into the lower one third of the dryer via gravity.
If the grain is drying quickly, the sweep moves faster. If the grain is slow to dry, the sweep slows down.
Constant temperatures
The computer continuously monitors the temperature and moisture content of grain at all levels in the tower, making the appropriate adjustments to the volume entering at the top, the volume exiting the bottom and fuel to the burner.
Plenum temperatures remain at the level the operator has programmed into the computer.
As incoming grain becomes warmer and drier during the heat of the day, the computer puts more grain into the top, speeds up the sweep and lowers the fuel input.
Conversely, when grain becomes cooler and damper later in the day and at night, less grain goes in the top, the sweep slows down and the burner runs hotter.
As the burner naturally sucks in fresh air at ground level, pulling it through the cooling chamber, the extracted heat rises to the drying chamber above.
If that heat were to remain with the grain all the way into the bins, it would require energy at a later date to cool it, thus wasting the heat.
MC sales rep Michael Larson said that air coming off the top of the cooling pile is warmer than when it was pulled in at ground level.
“In effect, it’s free heat because we reclaim it through this reverse cooling process,” said Larson.
“If we’ve got our dryer set at 93 C and we have -1 C outside, then we need to make up 94 C of heat with our burners.
“With reverse cooling, we’ve got this extra 22 C of recaptured heat available to us, so now we only need to make up 72 C of heat.
“In real life, this system cuts fuel consumption by 30 to 40 percent. Also, when you’re putting cool grain in the bin, it lets you ignore aeration so you can concentrate on the harvest operation.”
He cautions that the system only works on grains with plenty of air space between the kernels. Flax and canola pack too tightly.
For more information, contact Dave Wall at 204-269-7616 or visit www.mathewscompany.com.
For information on Zimmerman tower dryers, visit www.fficorp.com/.