Slippery liners cover rust and holes caused by friction
Polyethylene is a slippery solution to the normal wear and tear that occurs with farm implement parts.
Pat Reinhart of PolyTech Industries in Minnesota, who has 37 years experience providing slick and slippery polyethylene solutions to farmer’s friction problems, said poly replacement parts typically last longer than original metal parts in spots where abrasion and corrosion are prevalent.
“For one thing, UHMW (ultra-high molecular weight polyethylene) parts last longer because they’re slippery. There are no pores,” he said.
“That’s what gives it such high wearability.”
Read Also
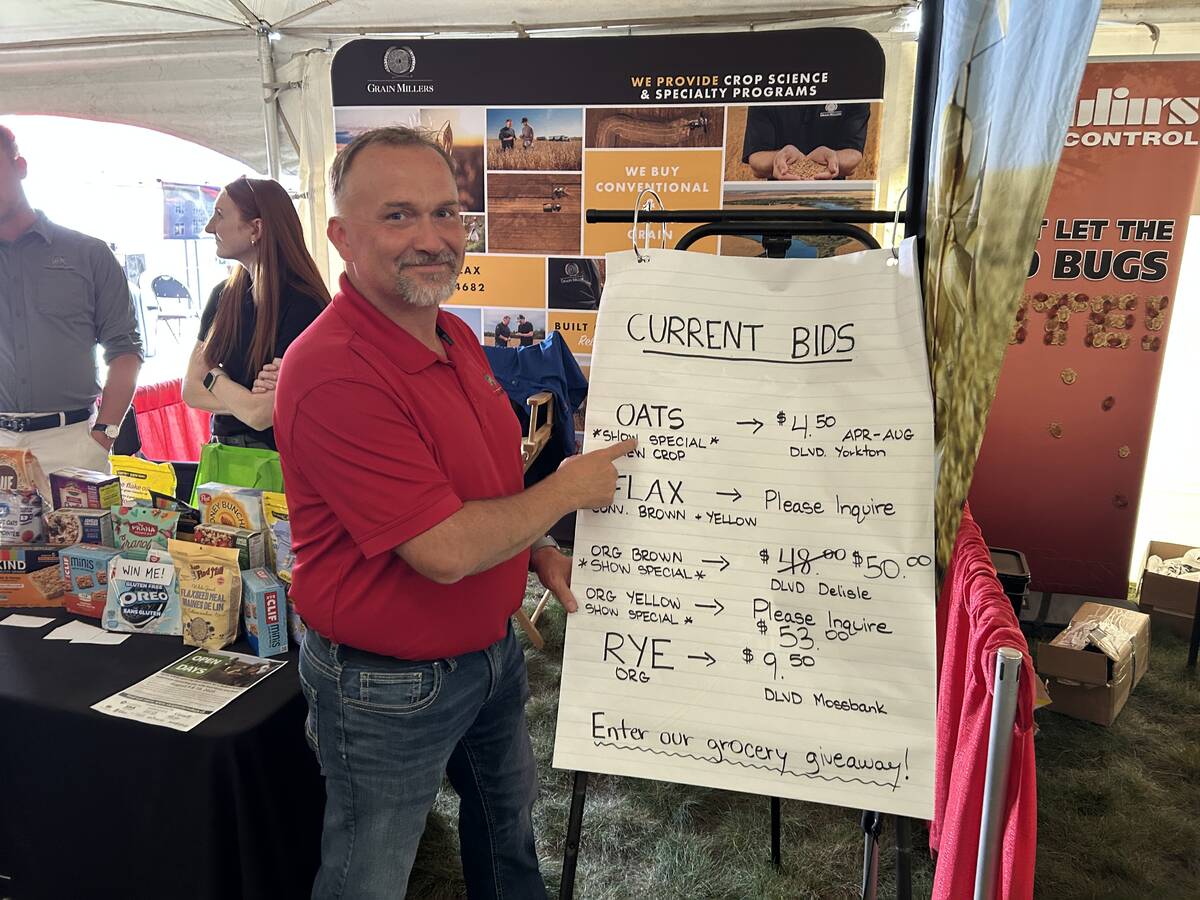
Canada’s oat crop looks promising
The oat crop looks promising and that’s a good thing because demand is strong.
Reinhart said farmers first want to know about price and then how long the component will last. They often do a quick mental calculation on upgrading an older machine with poly versus buying a new machine, he added.
“It used to be that guys only came to a company like us when they had wear problems with older equipment, but now we’re seeing farmers putting UHMW parts in brand new equipment as a matter of preventive maintenance,” he said.
“Farms are a lot bigger. They’re growing more acres. They’re putting a lot more grain and fertilizer through the machines in a shorter period of time. UHMW parts are a lot slipperier, so everything runs smoother and more efficiently. It keeps your planting equipment and harvest equipment in better condition for trade in time.”
It can also increase production.
“Custom harvesters doing edible corn equip the whole combine with UHMW parts because they get less damage on the kernels,” Reinhart said.
“The premium for undamaged kernels can run 50 cents to 75 cents extra per bushel.”
However, it’s not as simple as replacing iron with plastic. PolyTech must carefully examine the basic mechanical engineering that went into a part before tackling its poly counterpart.
For example, the purpose of the original JD skid plate was to let the cutter bar ride on the surface during bean harvest without sticking or pushing.
PolyTech took a look at how the skids fit the header and found the original equipment manufacturer products needed a tighter fit to keep soil and trash from pushing up the cutter bar.
The result was PolyTech’s patented Living Hinge, which keeps plates tucked up tight against the cutter bar and reduced wear and dirt clinging.
Auger bed liners are another spot where poly is a better material than metal, said Reinhart.
The abrasive nature of grain quickly removes the original paint from the trough, leaving the bare metal exposed to the atmosphere, even in a shed. Corrosion can begin during a combine’s first year, and grain will eventually will end up on the ground.
Reinhart said prices from US$450 to $650 means the investment in a poly auger bed liner can be recovered quickly, especially from middle-aged machines.
The poly also improves grain clean out in many cases.
The Grain Grabber 2 is a polyethylene protrusion that bolts to grain head augers, with one grabber installed between each flight.
Reinhart said the extra grain-moving capacity makes the auger perform more like a full-finger auger and allows the operator to run the reel higher, which reduces shattering.
However, some farmers report that grain is thrown out at the centre of the auger in heavy crops because the grabber is too aggressive, in which case they can be re-moved temporarily.
Auger flighting is one of the fastest wear components on the farm, affecting combines, grain carts, transport augers, air carts and bins.
To help deal with this ongoing expense, PolyTech offers more than 300 flighting wear shoe sizes with diameters from six to 24 inches.
PolyTech shank guards are manufactured with a radius that matches the contour of the shovel on which it will be installed. Reinhart said this feature means they install easier and stay on better with less re-tightening.
This combination of shape and material improves soil flow, reduces drag, reduces stress on equipment and sheds roots and soil so there are fewer clumps, he added.
For more information, contact Reinhart at 866-834-6703 or visit www.polyskid.com.