The opposed piston engine employs two pistons meeting TDC in the middle of a common cylinder for explosive power
Farm equipment will someday be powered by a truly revolutionary opposed piston (OP) diesel engine with fewer parts, developing more power than your current conventional diesel.
The OP engine is also smaller, lighter, more fuel efficient, reduces normal diesel pollutants, brings nitrous oxide down to near zero and should cost less than a conventional diesel engine.
If you’re envisioning the “boxer” type layout of conventional opposed piston engines, then you’re likely thinking Lycoming, Continental, Porsche, Formula One, VW Bug or Subaru. These flat opposed piston engines have a crankshaft revolving in the centre of a crankcase, with combustion chambers, pistons, rods, heads and cams all located at the two outer sides of the engine. The force of each controlled explosion is directed inward to the crankshaft, and it creates rpm.
Read Also
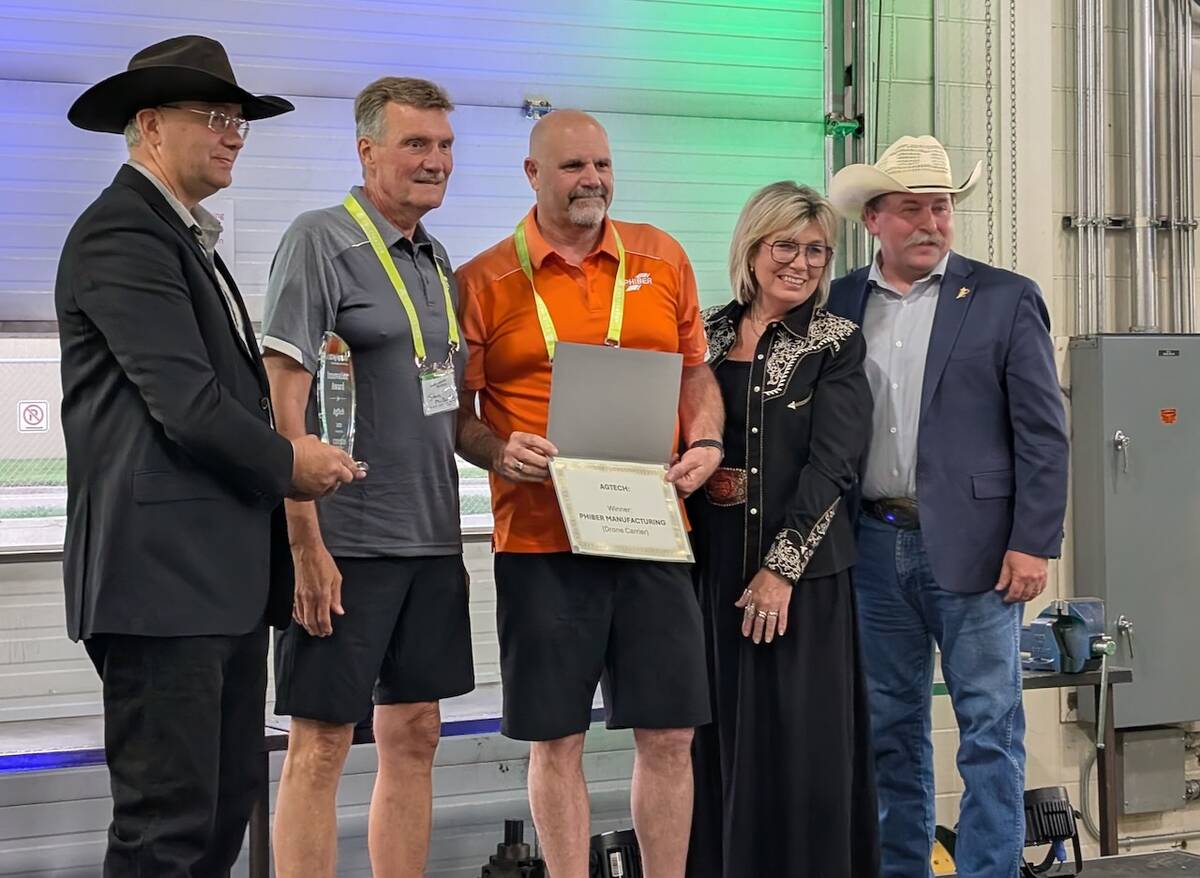
Ag in Motion innovation awards showcase top 2025 ag technology
The 2025 Ag in Motion Innovation Awards celebrated winners across five categories: agronomics, agtech, business solutions, environmental sustainability and equipment.
The AchatesPower OP engine is nothing like that. The California-based company has turned the conventional internal combustion engine inside-out.
The basic layout employs a long cylinder with two pistons running up and down in the vertical layout. The two pistons meet each other in the centre of their cylinder, which is the equivalent of TDC. At that point the two piston tops are nearly touching, and the injector squirts diesel into the gap, creating the explosion.
As with any diesel, ignition is triggered by the compression heat. The blast forces the two pistons apart, and they each rotate the big end of their connecting rod back to their respective crankshafts where they hit bottom dead centre.
OP engines are all two-stroke, so the pair of pistons meet TDC and experience the compression explosion with every revolution of their crankshafts. OP engines are always mounted in a vertical plane, never horizontal. There’s a crankshaft for the top connecting rods and a crankshaft for the bottom connecting rods. The two crankshafts are located at the outer ends of the OP where we might have normally expected to see camshafts, according to the Engineering Explained website.
Reciprocating action of the connecting rod converts piston motion into revolving motion, as it does in any internal combustion engine. The top crankshaft is linked to the bottom crankshaft with gears feeding power into a common output shaft or a flywheel. OP engines have been built in many configurations, ranging from single-cylinder with two pistons, up to 12-cylinders with 24 pistons.
The AchatesPower company started in 2004, with the intent of developing cleaner more efficient diesel engines that would fill the market void created by the limitations of electric-powered vehicles and heavy equipment.
AP executive vice-president Larry Fromm is one of the founders.
Fromm says two distinct paths of new technology allowed AP to revolutionize the opposed piston engine.
The OP concept actually dates back 140 years. Fairbanks Morse OP marine engines introduced 85 years ago are still in production today.
“The first challenge we faced was that nobody ever thought a diesel engine could be made clean enough to meet future emission standards,” said Fromm in a phone interview from his office in California.
“But we had two breakthroughs going for us. First, modern simulation tools allowed us to fine tune configuration of machine itself. We could locate our components and modify them to create the best possible burn of the fuel. Super computers let us analytically design the combustion system and then experimentally validate and refine it. We created a diesel with the efficiency that opposed pistons have always been known for.
“Super computer simulation let us design a combustion chamber that expelled very few emissions. We reduced nitrous oxide and particulate matter to near zero. That’s why the California Air Resources Board has help fund our demonstration in a heavy diesel truck.”
The second major breakthrough came in engine management. Specifically, the injector spray pattern is a key factor. In all, AP has about 300 patents on their version of the OP engine.
Fromm says AP is first focusing on military vehicles and heavy commercial trucks. The United States Army wants to have OP in heavy combat vehicles by 2024. “We don’t do manufacturing ourselves. We’re a development company. We license our technology to various engine manufacturers. We’re right now working with some vehicle manufacturers to have our engines available for installation in 2027.”
Fromm says the U.S. Environmental Protection Agency has a mandate to write regulations that reflect the best technology for cleaner air. EPA has witnessed near zero emissions from the OP, while it also reduces CO2.
He says that in 2027, the European Union, the EPA, California and other regulating bodies will enforce much stricter standards for diesel engines.
“The companies building conventional diesel engines will add a lot of extra equipment to meet the tougher criteria, and that means extra cost. We’ve already met those tougher standards by eliminating parts, not adding them. We already meet the 2027 standard for low nitrous oxide, low particulate matter and low CO2, with a comfortable margin. But we do require SCR AdBlue diesel emissions fluid. And we do need to occasionally stop to regenerate, but we have 75 percent less soot.
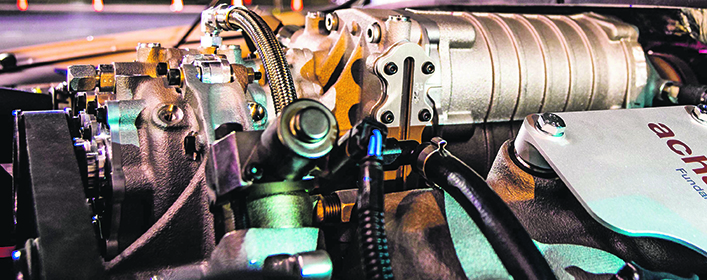
“The Engine Manufacturers Association calculates that 2027 standards will add $58,000 to the cost of a new heavy duty truck. They will need to add a second SCR system, a second DEF doser, circuits to electrically heat the exhaust and cylinder de-activation. All this technology is very complex and it’s expensive.”
AP hired SUD Consulting to conduct a study comparing the OP engine to a conventional diesel engine. With all inputs being equal, and power and torque also being equal, the opposed piston engine costs 11 percent less than today’s conventional diesel.
“That’s because we’ve eliminated the most expensive component, which is the cylinder head. And we’ve eliminated the part of the engine with the most parts, the valve train. We have no camshaft, lifters, rocker arms, valves, springs or timing assembly. It’s all absent from our engines.
“Historically, the reason we’ve seen opposed piston engines in aircraft, submarines and remote power generation is that they’ve always been known as the most efficient engines. By eliminating the cylinder head, the opposed piston engine eliminates the heat loss from that head. All that energy went to the head and was wasted. Then it had to dissipate through the cooling system. Now that energy is applied to useful work.
“We now have a better surface area-to-volume ratio. We still create a lot of heat, but it’s in the heart of the engine where it forces piston motion that generates work. We don’t go to a lot of expense or trouble trying to get rid of the heat. Our cooling system requirements are 30 percent lower. At our current state of tuning, our opposed piston engine consumes seven percent less fuel than current EPA standard for heavy trucks with comparable power.”
All tests and comparisons were conducted using diesel from local suppliers. AP has not yet tested with bio-diesel, but Fromm is confident the results will be even better when they take that step. He says bio-diesel offers a good solution for the transition to a more sustainable global transportation system for highway, rail and shipping.
“We get a lot of interest in hydrogen. That is the ultimate zero-carbon fuel. We’re working on that with about a half-dozen research institutes from around the world. They have already run trials fueling opposed piston engines with hydrogen. They have independently come to the conclusion that an opposed piston engine fueled by hydrogen could be the most efficient engine ever created, and also the cleanest.”