Tractor pushes leading edge of two-track technology a little deeper into the industry but not the soil
Agco’s new MT800 series provides up to 673 horsepower along with a step-less transmission and front suspension system that provide a more comfortable ride than previous parallel track Challengers.
It’s a tractor designed for deep ripping, sub-soiling, installing tile or pulling high-speed seeding equipment, Agco engineer Adam Sills said in a recent phone interview. Sills added there are four MAN engines available in the big tractor, three based on the 15.2 litre displacement:
- MT851- 511 h.p. 15.2 litre 6-cylinder
- MT856 – 564 h.p. 15.2 litre 6-cylinder
- MT862 – 618 h.p. 15.2 litre 6-cylinder
- MT867 – 673 h.p. 16.2-liter 6-cylinder
Read Also
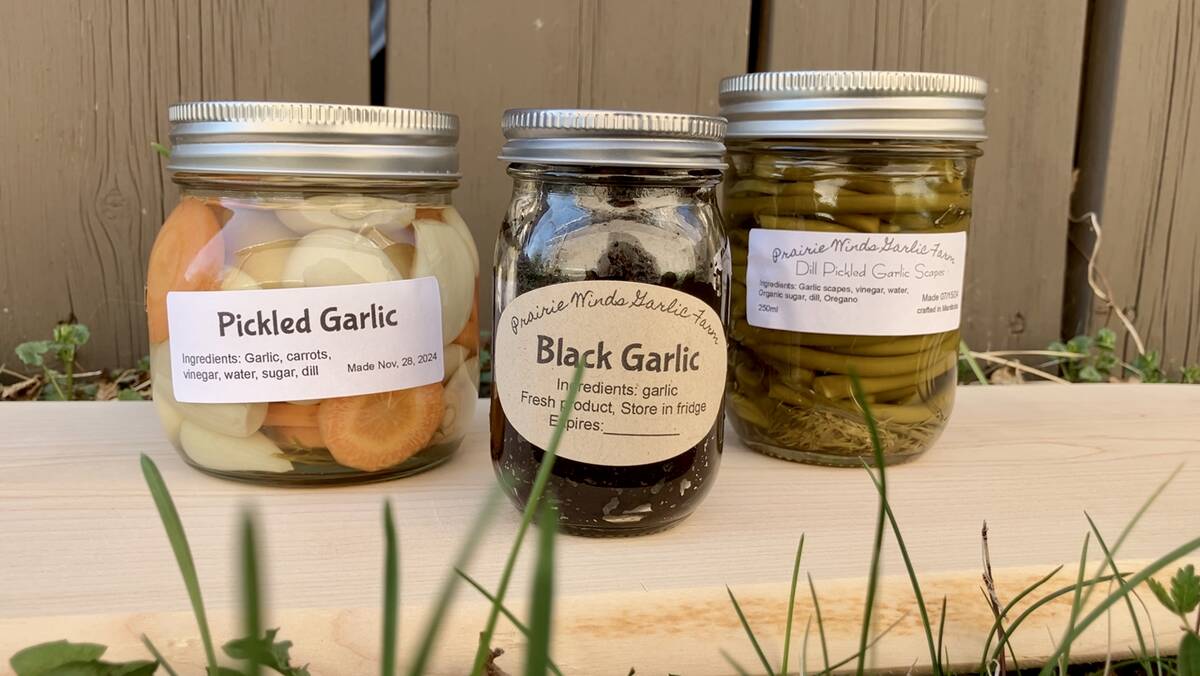
Growing garlic by the thousands in Manitoba
Grower holds a planting party day every fall as a crowd gathers to help put 28,000 plants, and sometimes more, into theground
These engines and configurations are part of the new generation of engines that create higher torque at lower speeds.
Agco’s AccuDrive allows for an engine speed range of 1,000 to 1,700 r.p.m., providing maximum torque from 1,100 to 1,450 r.p.m.
The Challenger Accu-VT continuously variable transmission is engineered to run at ground speeds as slow as 65 feet per hour up to 25 mph, all at reduced engine speed. The Tractor Management System automatically controls engine speed and transmission ratio to ensure constant ground speed.
Accu-VT lets the operator pull heavy implements through tough conditions with maximum torque and minimum fuel use. The transmission continually adjusts to optimize fuel consumption based on load.
When no torque is needed, fuel savings are even more significant.”
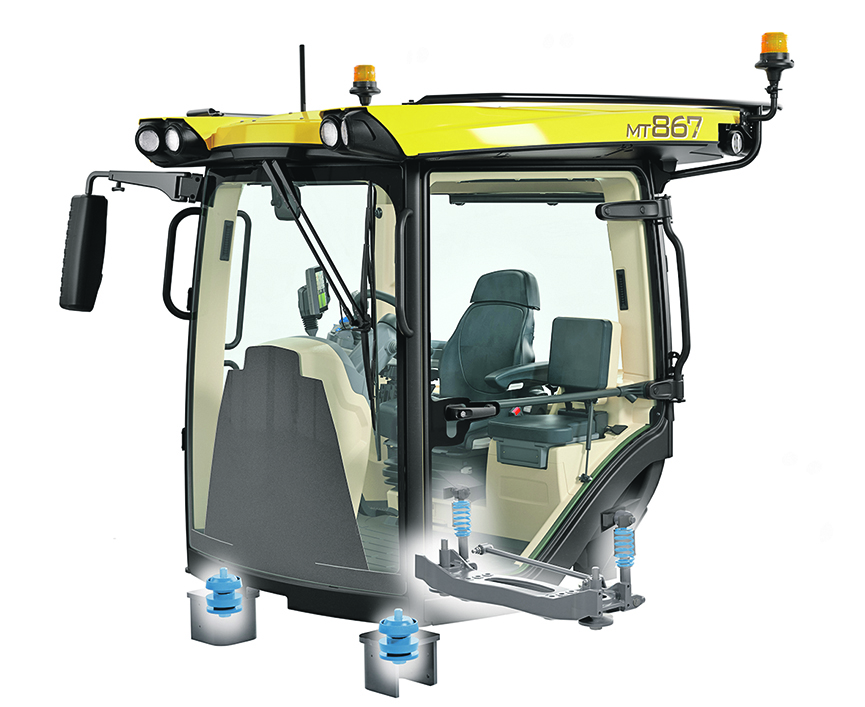
Sills said the new undercarriage suspension evolved after more than three decades of twin track experience. The extended wheelbase provides better ground contact, improving flotation while minimizing soil disturbance and compaction. Suspended mid-wheels help to maintain constant contact on all surfaces, providing ride comfort.
“The front axle itself is basically the same. It still has the coil springs like we had on the older tractors, but we’ve added an option called SmartRide Plus,” said Sills.
“We put a hydraulic cylinder down the middle of the coil spring on each side. Its sort of acts like a shock absorber. The main advantage of the hydraulic front suspension is that you can use those cylinders to raise or lower the front end. This shifts weight to the rear or back up to the front. That can compensate for weight balance that isn’t quite right, or you use it to transfer more weight to the rear.”
There’s a variety of ballasting options, including front weights and chassis weights, to improve machine balance, headland quality and drawbar pull capacity.
The MT800 allows for track widths from 88 inches to 128 inches, so operators can select a width for the specific task at hand or maintain controlled traffic lanes to reduce soil compaction across a field. There are four styles of track with belt widths from 18 inches to 36 inches.
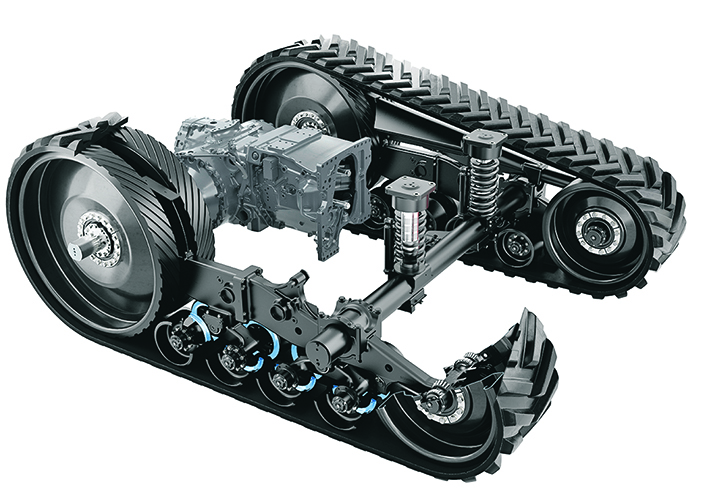
Sills said the new SmartRide suspension allows the tractor’s pitch to be controlled, which helps maintain the correct implement and linkage geometry. It also provides an improved ride. He said that a rough ride and berming in the headlands had been a problem in previous years, but engineering has overcome those drawbacks.
“We’ve done side-by-side in-field trials with our two track tractors compared to four-track tractors. The same operator would drive both tractors. The two styles of tractor ended up equal in ride and driver comfort.
“What it came down to was the driver. If the driver isn’t overly aggressive, then there’s no difference in headland berming. But a guy with a two-track tractor can be a lot more aggressive. He can turn a lot sharper and faster than the guy with a four-track. It’s just human nature. If you can yank that wheel harder to make your turn, then that’s what you’ll do. That’s why we see berming from a two-track Challenger.”
The all-new cab is available with either the four-point shock absorber system with rubber elements or a two-point cab suspension. The four-point system has coil springs with integrated shock absorbers at the rear and two shock absorbers with rubber bumpers on the front. With nearly four inches of travel at the rear of the cab, the cushioning absorbs vibrations sent from the ground.
There are five different rear hitch systems. Customers can choose from three drawbars and a pair of three-point hitches. The drawbars offer 28 degrees of horizontal swing both left and right, so the tractor can turn more smoothly while under load.
A Category 5 fixed drawbar with 11,000-pound vertical load rating.
A wide-swinging roller drawbar with 11,000-lb. load rating.
A hydraulic-controlled drawbar with 15,000-lb. load rating.
A 15,000 lb. lift capacity steerable three-point hitch.
A 20,000 lb. lift capacity steerable three-point hitch.
A steerable three-point hitch and drawbar allows the tractor to make headland turns closer to the centre point of wide implements when under high draft loads. It also reduces the amount of steering power needed while maintaining a higher draft force. It gives an operator the ability to make steering adjustments and continue pulling a ground-engaged implement forward instead of sideways, thus reducing stress on the implement.
“If you’re working in Washington where they farm those steep hills and your drill wants to run downhill, you can set it so it’s offset and lock it over there so you can run straight. We had this on the previous MT800 Challenger, but we didn’t do a very good job of marketing it, so nobody knew about it.
Both the15,000-lb. and the high-capacity 20,000-lb. hitches include a Category 5 free-swinging drawbar with 15,000-lb. vertical load rating. With the drawbar unpinned and the hitch allowed to swing, the combination can achieve 23.5 degrees of horizontal swing both left and right.
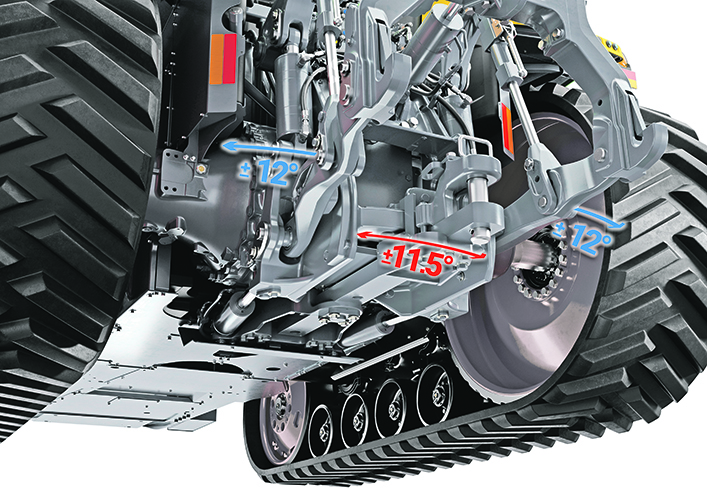
Sills said the MT800 has three separate hydraulic systems, a major benefit compared to other tractors.
“Over the years, every CVT transmission tractor we’ve designed was built with an individual separate hydraulic system dedicated to the transmission. We do that to prevent cross contamination with the other hydraulic fluids. The CVT has such tight tolerances, we don’t want any foreign matter getting in there. The old PowerShift we had on the old MT wasn’t quite as refined so it wasn’t an issue.
“The motor has it’s own dedicated oil system. It doesn’t share oil with any other device. We have another isolated hydraulic system for the CVT. And another isolated dedicated hydraulic system just for the implement, remotes and three-point hitch. The service interval is now 2,000 hours.”
The system delivers 116.2 gallons per hour. The implement system dedicates one pump to the left valve block and one pump to the right valve block. This allows implements to be connected according to their flow requirements. Each pump delivers only the required flow, whether it’s high or low.
The system allows an operator to increase hydraulic efficiency and not work the pumps any harder than needed for the implement’s operation. For example, a central-fill planter will have a high-flow hydraulic requirement for its vacuum system and a low-flow requirement for the cylinders raising and lowering the transport wheels.
The MT800 is the mechanical sibling to the Fendt 1100 Vario MT series.