Leading-edge technology remains a focus, but metering and distribution changes for new model’s design and function
Clean Seed Capital group redesigned its Smart Seeder with the help of some blunt farmer feedback, and it plans to have two seeders on the market in the spring of 2021, the Smart Seeder Max and the Smart Seeder Max-S.
“There was a tweet where someone said I don’t understand how you can keep throwing millions of dollars at this and never sell one of these,” said Noel Lempriere of Clean Seed.
“The reality is our investors, our (research and development) team, our software people, and me in marketing and everybody involved know what we have.”
Read Also
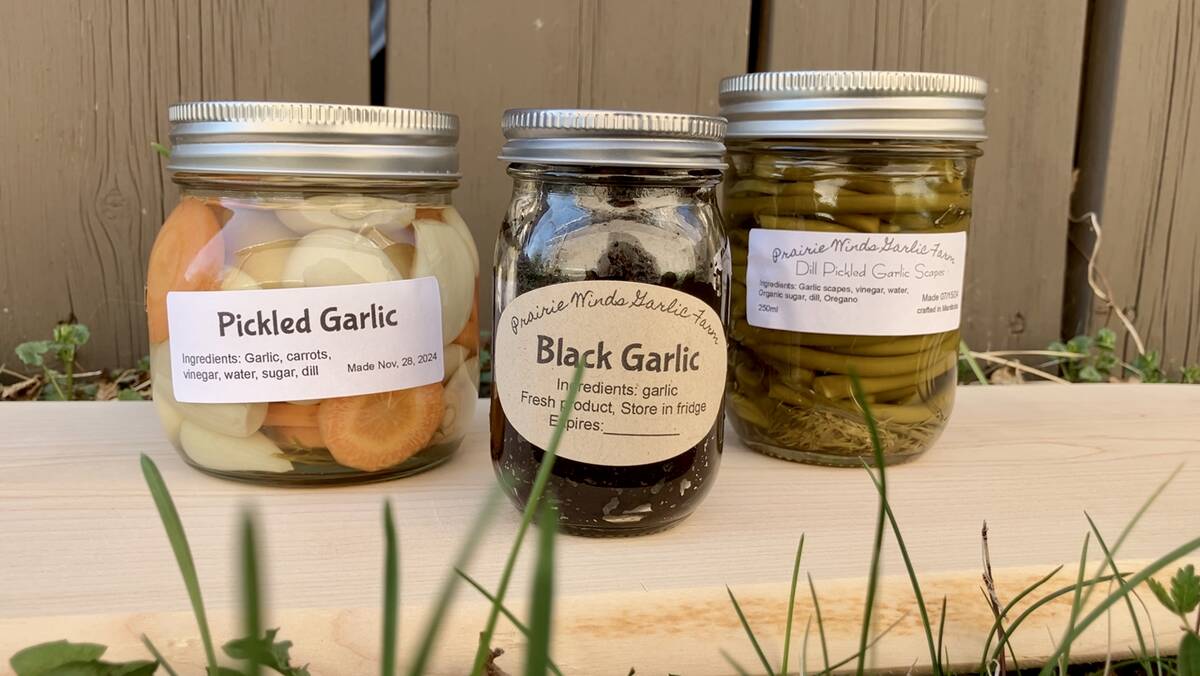
Growing garlic by the thousands in Manitoba
Grower holds a planting party day every fall as a crowd gathers to help put 28,000 plants, and sometimes more, into theground
Some of the feedback growers gave Clean Seed on the previous rendition of the Smart Seeder, the CS6, was that it was far too wide to transport safely on the road.
“It was quite a learning curve we had, especially in the frame size and transport, where we were primarily a technology company and we came away with some great customer feedback, on this needs to be narrower width for transport,” said Colin Rush of Clean Seed.
“We narrowed down almost 10 feet from the CS6.”
The company decided to go with a frame that’s been on the market for a decade, the YieldTrac planter frame distributed by Norwood Sales in Fargo, North Dakota, that folds forward to a transport width of 18 feet.
Both the Max and the Max S are 60 feet wide, have 12-inch row spacing and two rows offset by 24 inches.
Clean Seed was also told by farmers the CS6 design was far too heavy, which was in part due to the 500 bushel commodity tank set on the toolbar.
The company ended up walking away from the planter-frame-mounted tanks and instead developed its 7605 bulk transfer cart .
The previous CS6 design had a commodity fill tank called the Smart Cart that was also scratched from the company’s plans for the time being, but its commodity transfer airflow system lives on and is used in the bulk transfer cart.
The bulk transfer cart has five tanks; a 325, 205, 120, 70 and 40 bushel tanks with a total capacity of 760 bushels. Each has load cells to manage inventory and delivery.
Its rear wheels are 800s with the possibility of putting on duals on with a 69 percent weight split on the rear axle, and growers will have to fill it with a tender truck or auger because a conveyer option won’t be available until after the seeders are delivered to the first customers this spring.
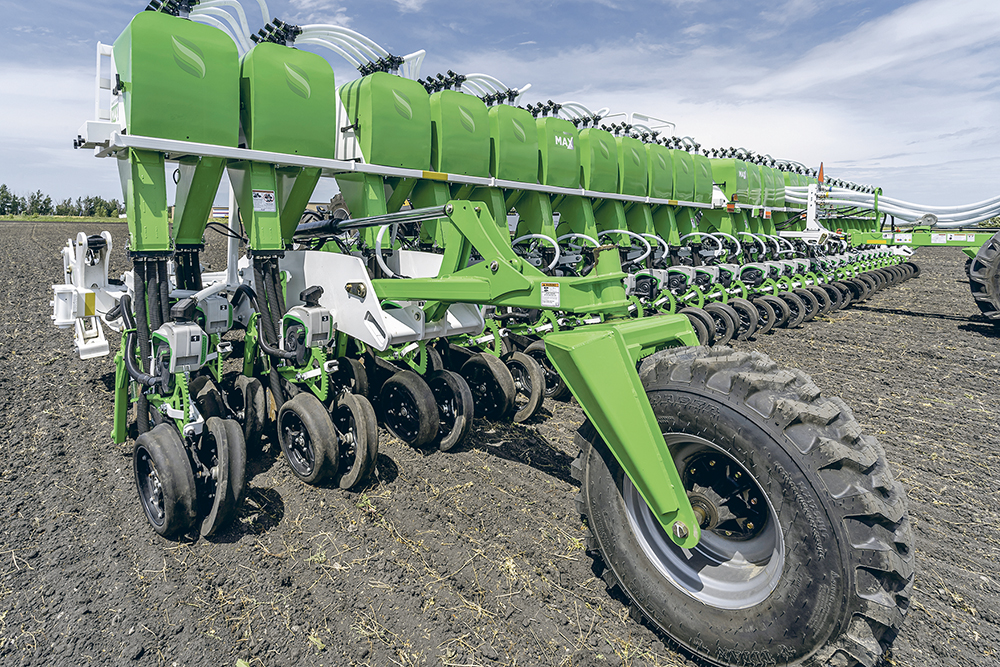
With the YieldTrac planter frame and the bulk transfer cart, the new offering looks much more like the traditional air seeder or drill and commodity cart forms that have been a mainstay on the Prairies for decades.
But the Clean Seed offerings provide a sophisticated air distribution system and app-based control capable of precise placement of up to five inputs on a row-by-row basis.
The only difference between the SmartSeeder Max and the Smart Seeder Max-S, is the Max-S singulates one of the five inputs it applies, another big upgrade over the CS6, while the Max relies on volumetric metering for its four product streams.
The CS6 applied six products with volumetric meters, but in the grower consultation, producers said the ability to apply four products per row with independent volumetric meters and singulate another product per row was a more attractive set up.
At the front and on top of the Smart Seeder frame is a platform where the air distribution system sits that controls the amount of bulk product the bulk transfer cart feeds forward.
Small quantity products can be fed into the air system from this front platform.
“Whether it be an inoculants or an amendment or micronutrient, we will allow you to place that product directly into the air distribution on the unit,” Rush said.
The platform also allows operators access to the electronics, to perform maintenance, and to help unplug the system if it gets backed up.
The air distribution system takes either four or five bulk transfers from the bulk transfer cart, depending on model, and distributes them to one of 30 pods on the toolbar.
Inside each of these pods are eight meters, enough to distribute four products to two rows.
“The bulk transfer cart does a continuous transfer of five different tanks of product into our air distribution system and those air distribution systems work as a bulk fill on demand as our meters at each individual point call for product,” Rush said.
Air flow is stopped at the meters and gravity drop is used once the product has been metered.
“Each of those meters meter out independently so it’s like having 240 volumetric individual seeders on there that work based on a prescription. If you wanted to write a foot by foot prescription you can absolutely do that,” Rush said.
Each product drops down funnels that go down into a port on the DX openers, which gives operators multiple product placement options.
The DX paired row opener has a total width of four inches, and there is also a carbide tip that goes down 2.5 inches below the paired row rear ports that has another port.
“We dump our volumetric seed into three different funnels, and we can put those funnels in five different positions. So we can actually go out the left port, the right port and down deep. So that’s three settings,” Rush said.
“Then any of those four volumetric products we can actually split. So we can split the paired row from one tank. We can go on both the left and right hand because we can put the meter right on top of the funnel where it splits it. We can also do deep band and side band over four inches. So there are actually five positions for that opener.”
He said he hasn’t seen any seedling injury due to high rates of fertilizer deep-banded 2.5 inches below and to the side of where the seed is placed.
The seed singulator is attached to the vacuum meter that is located below the volumetric meters and flares out to the side of the right opener because the singulated seed is generally placed out the right port, Rush said.
“We want to put it on that loose ledge where we place a lot of our seed out the right side for the majority of the people who want 12 inch spacing for things like canola, peas, etcetera,” he said.
With the addition of the singulated product there are up to six different furrow placement for up to five different products and operators can quickly change where the product that is measured by the volumetric meters is placed by moving adjustment rods on the side of the seeder that move the banks of hoses into different ports.
Rush said gravity drop works well for their purposes because the seeder is designed to work at five miles per hour.
Each of the 240 meters in the Cushion Drive digital metering system are electrically powered and can be precisely controlled by the seeder’s SeedSync Max operations dashboard, so features such as turn compensation and row-by-row sectional control are simple to achieve.
Low-voltage stepper motors power the meters to help keep the systems power draw feasible.
Rush said the company recommends at least a 500 horsepower tractor to pull these seeders.
“What is the great equalizer is our saw tooth coulters that open our furrow up first. They actually open it up below that carbide tip. So we are actually cutting a slit in that soil and opening up which reduces the horsepower massively”.
The 24-inch saw tooth coulter is set straight forward, 90 degrees to the toolbar.
Rush said the coulter opens up the soil like butter, however rocks do not tend to cut like butter so a trip system on the shank is used, and bending a tooth on the coulter is possible.
“Because the coulter is held in tight against the shank opener, and it runs just a fraction below the shank opener, so if you run into a rock the opener will actually roll up over on the coulter over the rock,” Rush said.
“If the coulter doesn’t roll over and it hooks the shank, the carbide tip, then we have a built in trip and vertical travel where it will trip up over that rock.”
The moving coulters also help the DX opener keep trash flowing through the seeder.
“We have a moving part beside a stationary part. The cast opener is stationery right beside on either side we will have two moving coulters which allows that trash to be cut and pulled through,” Rush said.
Clean Seed decided to go with a closing wheel system instead of packing wheels because it wanted to keep a very loose bed of soil, with lots of pour spacing that allows water to penetrate after it rains.
Because the DX openers does open up a fair amount of soil in the rows, the seed is placed in tilled soil that tends to dry up instead of on undisturbed moist soil at the bottom of the trench, and there are no packing wheels pushing moist soil up to the seed, Clean Seed has taken a different approach to moisture conservation.
Instead of keeping as much soil and soil structure together as possible, Clean Seed uses what it calls bio wings behind the carbide tip to agitate and break up the soil to make a soft soil bed for the seed.
“By shattering the soil instead of just scrapping the trench with a knife blade and smearing the soil as you go through it like a lot of air drills do. We actually don’t seal the bottom of the trench, which allows effective root development,” Rush said.
The DX openers also enables paired row seeding four inches apart that leaves only an eight-inch spacing to then next seed row.
“That’s going to allow you to keep that crop cover in between, keep that bare ground to a minimum in those early days while those plants get established. So you can have maximum seed bed utilization,” Rush said.
The meters are wirelessly connected to the SeedSync operations dashboard, which is made up of a suite of apps including SeedSync UI that connects to the core system to manage everything on the drill, SeedSync Core that is the onboard control system that manages the products, and SeedSync Cloud that manages telematics transfer to the cloud.
Further width options for the Max and Max-S are planned, including a 40-foot version that may be unveiled next summer, and there is a larger version up to 80-feet wide that is also being planned.