Lighter booms can offer several advantages. Among them are less boom bounce, more water capacity, wider booms, lower boom height and the potential to slow down for a better spray job.
A conventional 120 foot steel boom, weighing about 2,500 pounds, can withstand a fair bit of abuse, but all that weight hung out 55 feet from the rack ultimately succumbs to the torturous twisting and goes for scrap steel, sometimes within the first year on the job.
As more companies turn to aluminum, they find the lower weight improves boom longevity. The same 120 foot boom built of aluminum weighs about 1,750 pounds, about one-third less than the steel boom.
Read Also
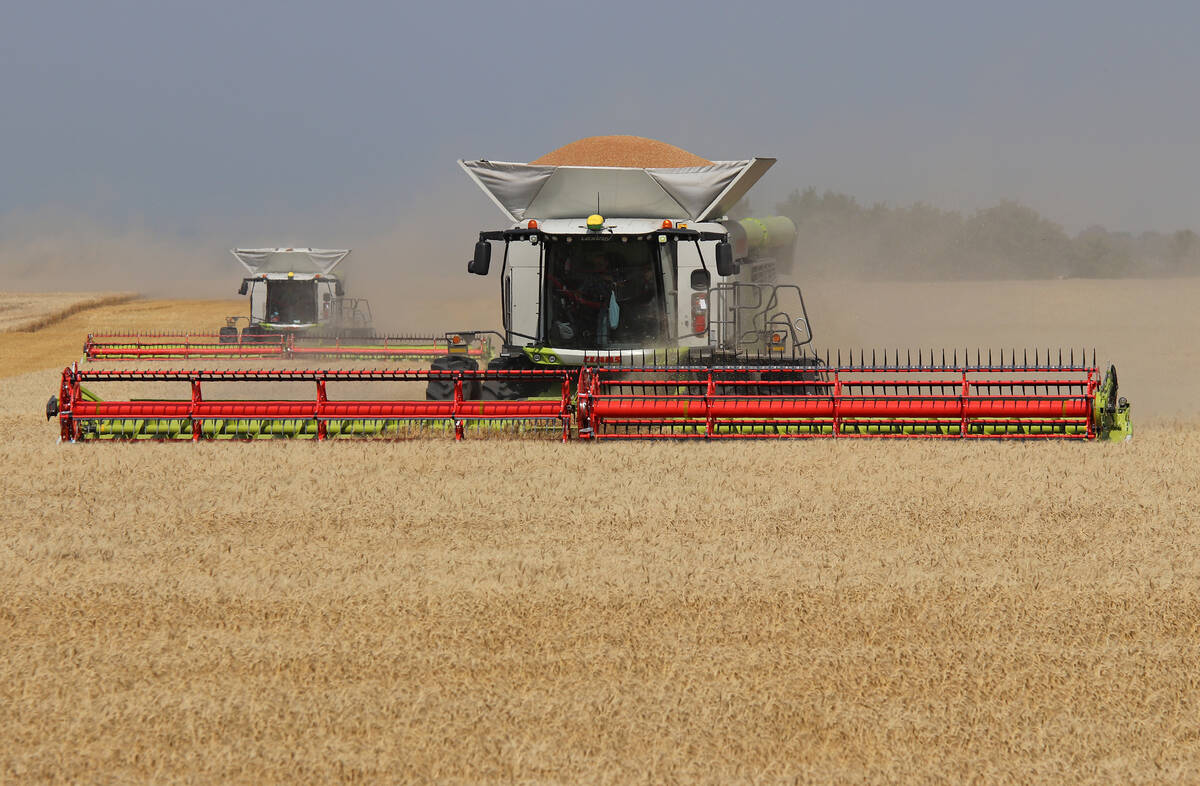
China’s grain imports have slumped big-time
China purchased just over 20 million tonnes of wheat, corn, barley and sorghum last year, that is well below the 60 million tonnes purchased in 2021-22.
While some people are concerned about work hardening, aluminum boom manufacturers use subtly different engineering and geometry to give the booms longer life.
For now, aluminum seems to be state of the art for the North American boom market.
However, according to British company Altek International, True weight savings don’t come from alloys at all.
They are in carbon fibre.
Altek says a 120 foot boom built of carbon fibre weighs only 850 pounds, for a two-thirds weight reduction from the steel model. Altek did the pencil work in comparing the materials and weights of the three different booms.
In addition, an Argentine company called King Agro points out that the weight reduction allows producers to run a wider boom with a less powerful, cheaper sprayer model that consumes less fuel.
The hypothetical, 120 foot boom we’ve been comparing is real at the King Agro plant in Buenos Aires.
King Agro has been building carbon fibre spray booms for the South American market for three years, in which time they have sold about 250 of the ultralight booms.
Its 120 foot carbon fibre boom sells for US$50,000, says the company’s Geronimo Garvie.
In making materials comparisons, they use the internationally accepted unit of megapascals (MPa) to measure breaking strength. Low numbers indicate a material breaks easily. High numbers mean it takes more force to break the material.
Because the carbon fibre formula can be mixed in a variety of resistance and stiffness ratings, different compounds are used in different parts of its boom assembly. But King’s carbon fibre is considerably stronger than steel.
Garvie said low resistance carbon fibre employed by King Agro has a breaking strength of 2,500 MPa. The company’s high resistance mixes have values of around 6,000 MPa. In contrast, steel 1010 is rated at 300 MPa and stainless steel 316 is rated at 500 MPa.
In designing a lightweight apparatus such as an airplane or a spray boom, engineers look for materials that are strong yet light, with a low density measured in kilograms per cubic metre (Kg/m3). A low number means the material is lighter than a higher number.
Garvie said King Agro’s carbon fibre mixture has an average density of 1,450 Kg/m3.
In contrast, steel 1010 has a density of 7,800 Kg/m3, which is about five times heavier than carbon fibre per unit of material.
Carbon fibre is more resistant to fatigue than steel, therefore it increases the lifespan of spray booms, according to the company. Carbon fibre is also very stable, therefore a good material for standing up to exposure to weather and agrochemicals.
Because epoxy resin is chemically stable, it’s widely used in paints that will be exposed to chemicals. King Agro says the malleability of carbon fibre allows them to take a design and build a stronger and lighter component compared to any other mainstream material. Applying this to spray booms, they say it allows them to build the strongest, lightest booms available.
For more information, see www.kingagro.com or email geronimo.garvie@kingagro.com.
Contact ron.lyseng@producer.com