These are not the screw piles you employed to build your new deck, these can reach 65 feet down, carry 45,000 pounds
Galvanized earth screw piles are taking the place of conventional concrete piles for some farm applications, including guide wire anchors for leg elevators, grain dryers and foundations for heavy structures.
Helical screw piles made their appearance in Manitoba 12 years ago when Emile Desrochers began bringing in the Techno Metal Post metal earth piles. He says the posts are actually giant metal screws that are twisted deep into the soil with special drilling machines.
From an engineering point of view, an important factor is that sensors on the drill machine make an accurate torque measurement, which is tested and validated on site. This ensures the foundation meets the exact load bearing capacity specified by engineers for each application.
Read Also
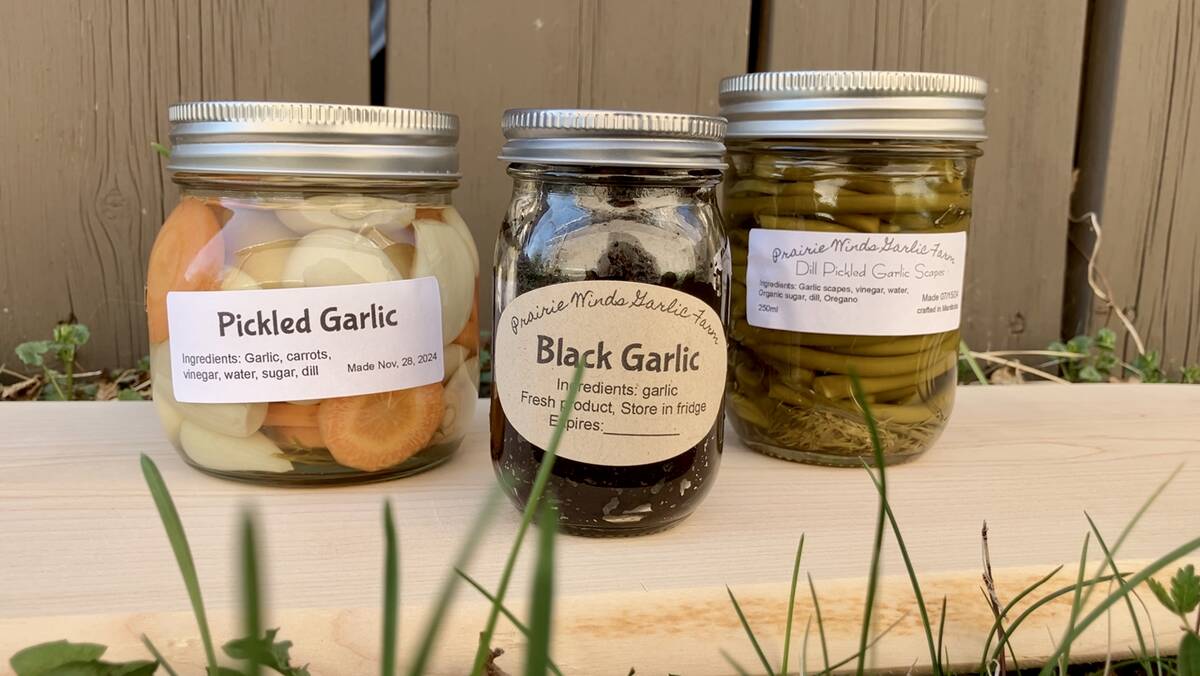
Growing garlic by the thousands in Manitoba
Grower holds a planting party day every fall as a crowd gathers to help put 28,000 plants, and sometimes more, into theground
“The torque reading on our machine automatically converts to psi. From there we go to the engineer’s chart, which tells us load bearing capacity of that specific pile. We can install helical screw piles with a load bearing capacity up to 45,000 pounds,” said Desrochers in a phone interview.
“Engineers dictate what capacity we need to meet. But the soil structure itself dictates the depth and load we need to go to meet those specs. For smaller applications, sometimes all we need is a 10-foot pile if it’s a tight soil, like a granular or sandy soil.
“In Winnipeg, we raise houses with our helical piles. We go down to glacial till, as far as 65 feet with the screw. We do that for farm buildings also.”
An observer can’t help but wonder why the torque generated turning the pile through so much soil doesn’t snap the shaft. Desrochers says that in 20 years experience with the system, he has yet to snap a shaft. There are a variety of different sizes, diameters and steel alloys, each designed for a specific task. The biggest helix is two feet in diameter. The kind of screw used to anchor a grain dryer would not be the same screw used to lift a house in Winnipeg.
“The company has in-house engineers to deal with each situation. And we always get the drawings and geo-technical soils report before going to a site. With this information, the engineers make their recommendations on size of piles, how deep we have to go and also lateral capacity. The torque readings on the machine tell us when we hit our target.”
He explains that for a 65-foot pile, they do not use a single 65-foot shaft. The shafts come in lengths of seven feet and 10.5 feet and they are welded together on the job site. For example, a four-inch pipe will have a 4.5-inch coupler at the top. The next four-inch pipe fits into the coupler, the two pieces are welded together and the pipe is screwed further into the soil.
That process is repeated until the gauge on the machine says they’ve hit the target for that pile. If they hit the anticipated depth and the gauge doesn’t show the expected soil resistance, it means they’ve hit silt. They have to go deeper. Maybe much deeper. They cannot leave the site until the gauge gives them the required torque resistance reading.
“If deeper isn’t an option for some reason, then we go down with double or even triple helixes. We did one shop where we used two 24-inch helix discs to get the right psi.
“The screw doesn’t actually compress the soil. It just rotates through the soil. The flight has either a three-inch or a 5.5-inch mouth. It just slices through the soil. As it gets tougher to screw in, then you’ve hit denser soil.”
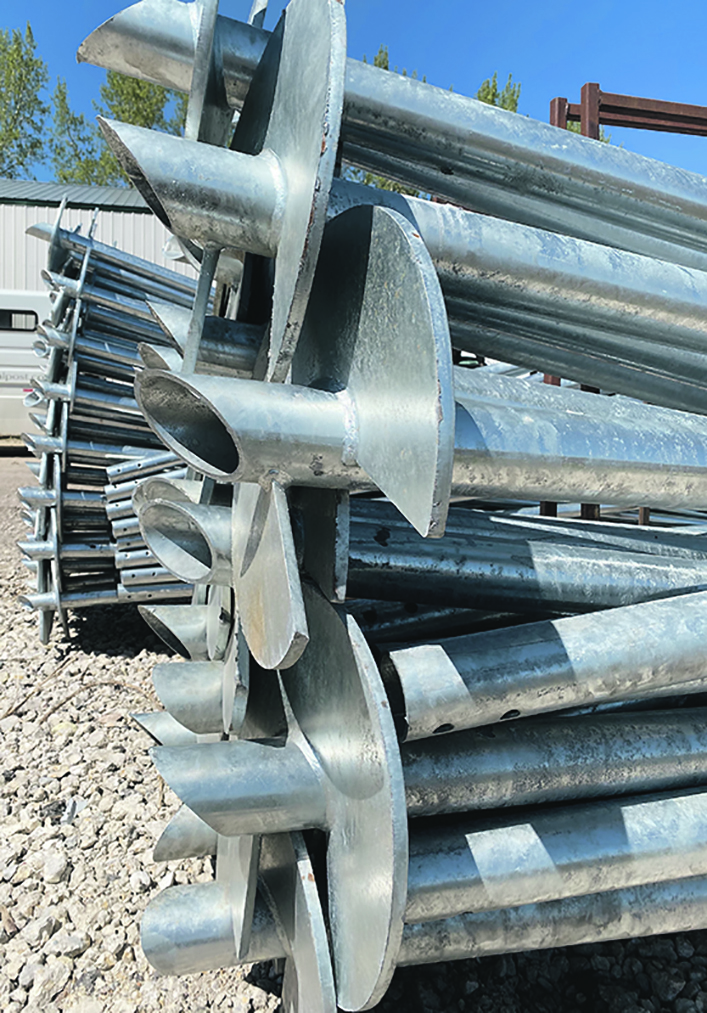
For a major grain dryer project, guide wire anchors go in at a 45-degree angle, while piles to support the two parallel steel beam foundation go straight into the ground. The beams set on top of the exposed piles.
One of the benefits of steel screw piles over concrete is actually short-lived. There is no drilling or excavation and thus no mud or mess, but any build site is cleaned up anyway within a short time.
Desrochers says after his crew has installed 40 piles, they leave. The only indication they were ever at the site is 40 tops of strategically placed steel piles sticking out of the ground. No mud and no annoying tailing dumps from the concrete trucks.
Corrosion is always a concern when driving steel into soil. Most of the piles are galvanized, but the zinc must be ground off at the junctions for the weld to take. That point remains vulnerable to corrosion. Without optional protection, the steel piles are expected to last about 50 years. With the optional protection, that lifespan can double.
“One thing we do is apply a sacrificial anode, something like you have in a water heater or an outboard motor. Ours is an eight-inch diameter by 30-inch high sauna tube filled with magnesium. We connect that to the piles. Magnesium is a less noble metal, so it deteriorates before steel starts to corrode.”
Sacrificial anodes are highly active metals used to prevent a less active material surface from corroding. Sacrificial anodes are created from a more negative electrochemical potential than the premium metal it’s used to protect. This cathodic protection can extend to a wide pattern of steel piles.
Desrochers says the more active system to protect piles uses something like a conventional trickle charge battery charger plugged into a wall receptacle. It charges steel piles to give them an extra half-century corrosion protection. It uses a rectifier attached to extra helix screws installed into the soil. The screw piles are all connected by re-bar, so the whole project is protected by the token charge. This minor current prevents the corrosion process.
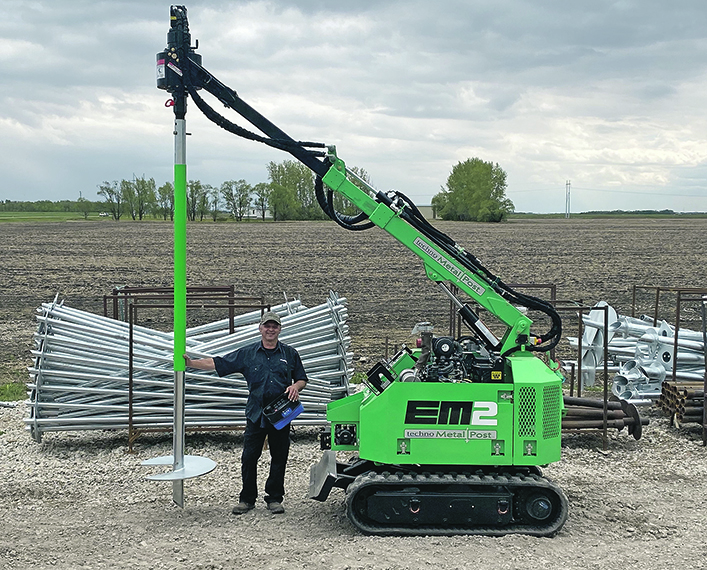
He adds that Techno Metal also has another significant option. Tight-fitting poly sleeves over the shafts protect these seven-foot or 10.5-foot sections from corroding. However, their main purpose is to prevent frost heaving by resisting ground movement.
The green sleeves reduce the grip of ground movements. Sleeve size is adapted to that of the pile and installed around the shaft when it’s screwed into the soil. The sleeve slides up and down with natural ground movements, allowing the pile to remain stable during freezing, thawing or drought.
“There’s no need to mobilize special equipment, such as a crane with a pile hammer, a large drilled shaft rig or a concrete pump. We have fast mobilization. Typically, only an operator and one laborer are needed.
“Cost is tricky. It all depends on the soil report and application. Sometimes we’re cheaper than concrete. Sometimes we’re more money than concrete. There’s maybe a half-dozen companies in Manitoba that do this, but a lot of them just do decks and garages. Some farmers are aware of this technology, but not all of them.”