HANNOVER, Germany — Justifying modifications of existing farm equipment and systems is generally is done by looking at cost savings, yield gains or both.
And when positive cash flow is tight, even the choices that pay can be hard to make.
A British company says that despite the difficult times for European dairy farmers, it is continuing to see “very respectable sales” for its product.
“The (milk price) and dairy market is the worst its been, maybe ever, no doubt about that, but what we sell pays for itself, usually within the year,” James Duke, inventor and company founder of ADF Milking, said at last week’s EuroTier livestock technology event in Hannover.
Read Also
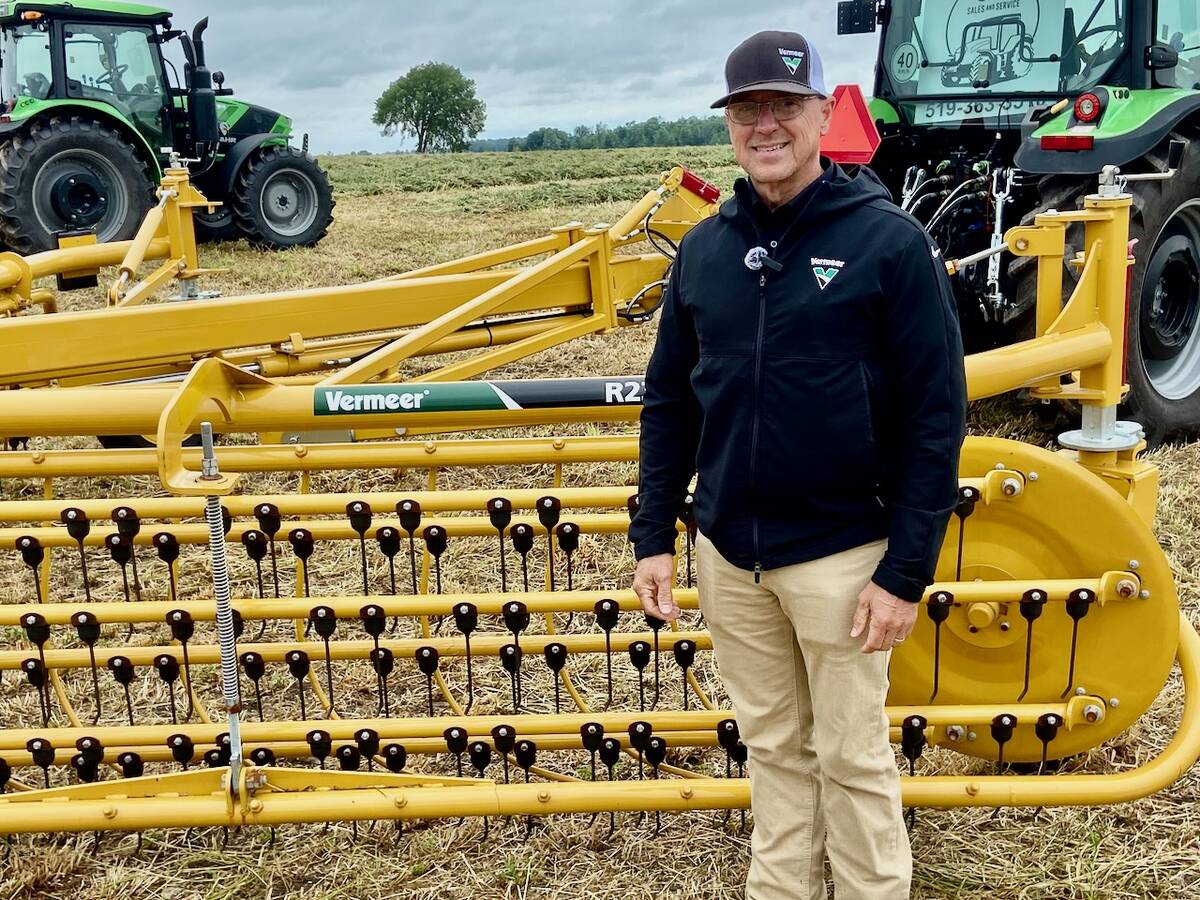
Basket rakes pitched for top-quality windrows
Boxy, clean windrows help make better hay bales for livestock farms and forage growers, and a basket rake excels in those areas, says Bart Elder of Vermeer.
There are about 20 patents on his product, which would lead one to believe that it would be a complicated piece of gear.
“(However), we’ve kept making it simpler, and that has led to high reliability,” Duke said.
The automatic teat dipping and liner flushing clusters that ADF builds improve the sanitation of the teats and the milk line over traditional approaches.
His equipment’s work starts as soon as the flow of milk stops and vacuum loss is detected on the line. Rather than manually washing and disinfecting the teats and gear as each animal is released from the draw of the milking line, dairy cattle receive an automated application of emollients and disinfectant at the top of the teat cup at the base of the teat.
This ensures that the remaining vacuum in the liner doesn’t get the chance to introduce bacteria into the teat canal while it is still open.
A gravity operated check valve determines that the cluster is still upright on the teat.
“A little puff of (compressed) air is delivered (to the liner) and any remaining vacuum is gone and the clusters come off gently, not with tugging and no smart cows kicking them (off) on their own in anticipation of having the farmer yanking them off,” he said.
The check valves select for a flow of disinfectant and water from a second set of jets at the bottom of the cups and the now inverted liners rinse out, ready for the next animal.
This replaces a manual process of washing and rinsing by producers as well as some steps in the process used by semi-automatic systems.
Making a technology pay for farmers has been the trick to selling his equipment in 26 countries.
“We’ve got more than 50,000 of them out there now, so we know it works,” said Duke.
Sales of Duke’s system relies on farmers producing more milk with lower somatic cell counts and having fewer cases of cow-career shortening and expensive-to-treat mastitis.
“The first milking after installing the equipment in a parlor, farmers go to change their milk filters and find them clean,” the West Sussex inventor said.
“They figure it must a (perforation), but the system stops the (vacuuming of manure) into the lines.
“This a sustainable farming tool,” Duke said.
“Sustainability isn’t just a fancy of the week. It’s survival for all of us.”
He said the system can be retrofitted to any existing milking system on the market.
“And we do now sell it in Canada,” he said about the technology that just recently received Food and Drug Administration approval in the United States.