Plant recognition has been the biggest technological hurdle as leading-edge companies strive to develop autonomous weed control machines. Any system is bound to fail if it can’t master image recognition.
Lemken recognizes this and recently took a step forward in answering the challenge by partnering with an ag tech company called Track32. This Dutch company specializes in merging powerful cameras or sensors with intelligent algorithms to facilitate camera-controlled cultivation in row crops.
The precision sensors allow the blades to cultivate weeds within two centimetres of beets within the rows.
Lemken’s IC-Weeder AI is the first commercial application of the Track32 software. The company says its row crop hoeing machine reliably distinguishes between sugar beets and weeds, even under high weed pressure.
Track32’s expertise will allow Lemken implements to be used more precisely and in more versatile ways so intelligent machines can be controlled by human operators and eventually by robots.
Cameras on the IC-Weeder AI are mounted under the cover to prevent disruption from shadows, said Lemken spokesperson Mathieu Vallieres in a phone interview.
“The field of view is illuminated by LED lights, giving uniform illumination in changing light conditions and at night. With this standardized light wave, high resolution images detect the precise position of plants based on their hue, size and position.
“The two cameras on the IC-Weeder AI are the same as in the regular non-AI version of the IC-Weeder. It makes high resolution pictures in green hues or the RGB-colour spectrum. The images are transferred to the job computer and visualized on the terminal,” said Vallieres.
“The special feature of the AI is the software for single plant recognition, which is based on artificial intelligence. It can create clean fields even in sown crops with extensive weed infestation within rows.”
To achieve autonomous plant recognition, the software first learns certain features of the crop plants. It combines these features to produce complex contexts in a second step using an algorithm based on the principle of deep learning.
For this particular machine, sugar beet plants were manually marked at various stages of development. The algorithm used this data to autonomously create a method for identifying sugar beet plants based on their colour profile, texture, shape, size and leaf position.
This allows the hoeing machine to work even in challenging conditions that are too complex for conventional image recognition systems. It distinguishes between crop plants and weeds.
During a pass with the IC-Weeder AI, the cameras transmit 30 images per second to the on-board computer, producing a plant recognition ratio better than 95 percent. The sickle-shaped pneumatically controlled knives move into the rows and hoe as close as two cm from each plant. A hydraulic parallel sliding frame ensures precise machine control in the crop, according to Lemken.
The new AI unit employs two cameras on each row to complement each other. The Combi Cam generates a superimposed image from both cameras. As a result, the system works from twice as much visual information, ensuring more precise detection especially in patchy crops.
Manual switching between the two cameras is not necessary. It’s possible to select only one camera with a good view if the other one is outside the field boundary, the company said.
Depending on mode settings, the integrated software searches for green hues or a calibrated colour hue. Each camera covers a field of view of 60 cm. These images are transferred to the job computer and visualized on the terminal, which processes them to produce precise steering signals. The actual plant position is calculated from the camera image, the plant size and the expected plant position.
This results in a steering signal being transmitted to the parallel steering frame to ensure that rows are followed precisely and to the active hoe blades that remove weeds within the row.
The touch screen terminal is used to control the job computer. Operating the IC-Weeder via the terminal is simple and intuitive, according to Lemken.
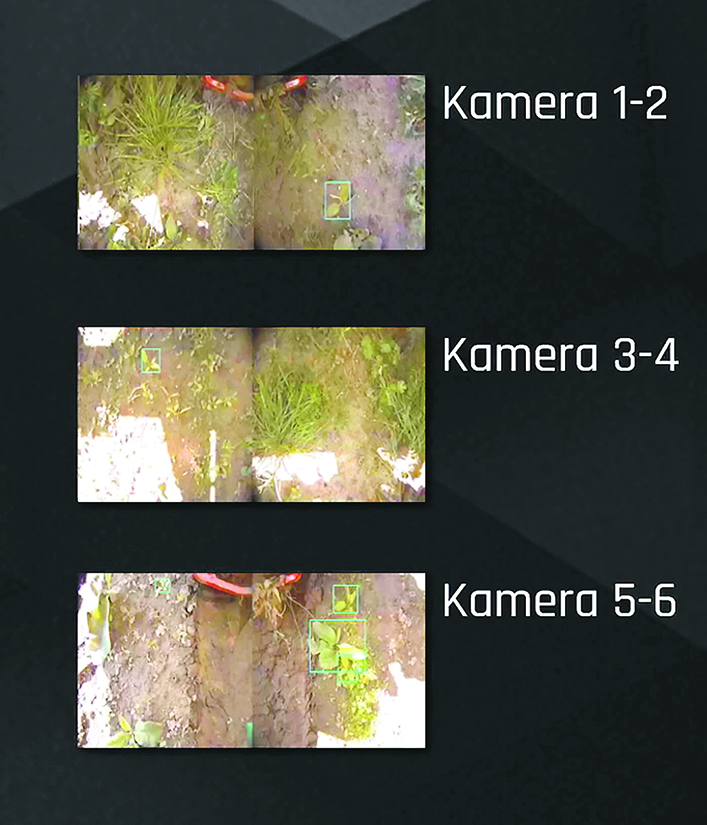
The parallel steering frame has a swivel range of 20 cm left and right. When the IC-Weeder is raised, the hoeing machine automatically centres itself behind the tractor. Support wheels prevent the transfer of movement between the tractor and steering frame.
The parallelogram element is equipped with either three or four tool holders for inter-row and intra-row tools. The front tool holder features a rigid or Vibro mount with hoe blades for working between rows.
Smart sickle whacks weeds
Lemken’s IC Weeder AI uses advanced imaging and machine learning to wield its crescent-shaped blades. It offers:
- Minimal row width: 25 cm
- Minimal planting distance: 20 cm
- Working widths: up to 6 m
- Forward speeds: up to 4 km/h
- Hoeing: as close as 2 cm from crop plants
- Multiple cameras, each covering a 60-cm field of view
- Recognition of green hues and the RGB colour spectrum
- Remote maintenance for direct support in the field
Behind it are two crescent-shaped blades, which remove weeds between plants within a row. The entire mechanism is pneumatic, with a PTO-driven compressor that provides the pneumatic cylinders of the sickle shaped intra-row hoeing knifes with sufficient air.
Once the area around a plant has been hoed, a blast of air blows dust and soil from the plant. Ground pressure can be adjusted with pneumatic cylinders.
Two support wheels hydraulically correct the height of the machine and transmit speed signals to the job computer. They also ensure lateral stability of the machine.
Vallieres said the AI version is available in Canada for beets only, but Lemken is working on new algorithms for potatoes and other crops.
“Once we have a pattern worked out for beets, then it’s easier to adapt the AI to other crops.”