$150 worth of hardware could keep you from climbing into that bin and making a fatal error unclogging the flow
A tool to unplug bin augers would keep people out of bins and could potentially save someone’s life someday. The solution is an air compressor and some cheap pipe.
Nebraska corn grower Guy Mills explained how it works in the Jan. 29 issue of Farm Journal AgWeb. Mills states that entrapment kills and he does everything possible to keep people out of his bins.
That means unplugging floor augers and getting them hung up grain safely, with his feet on the ground outside the bin.
Read Also
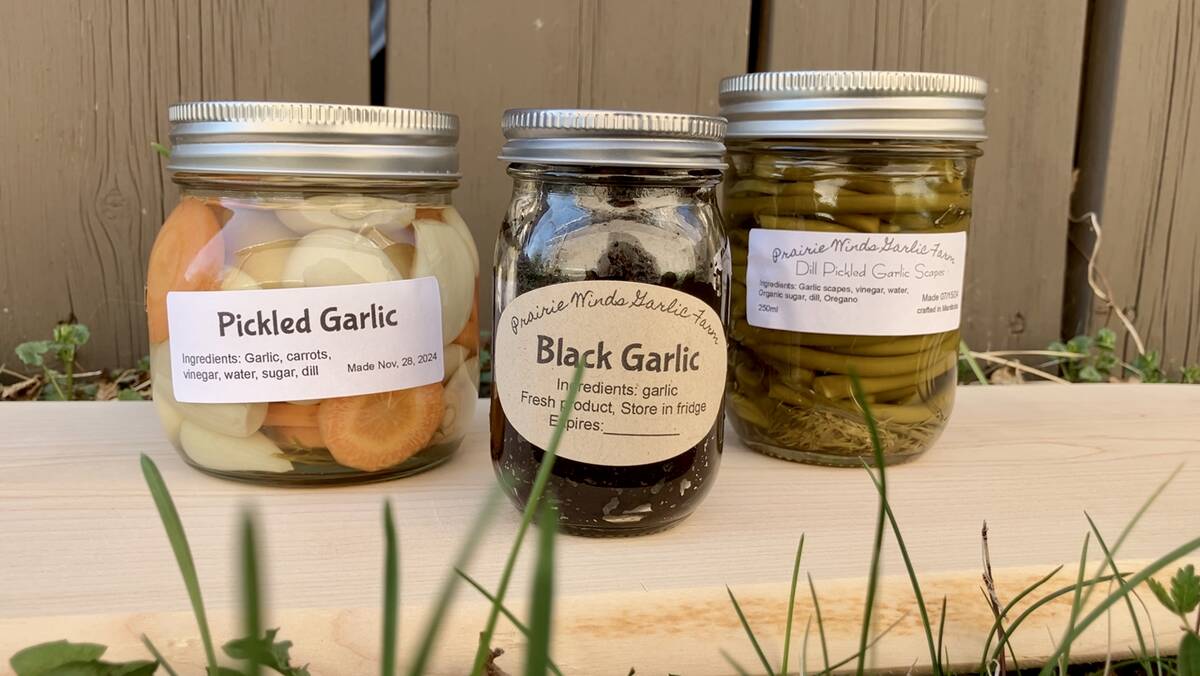
Growing garlic by the thousands in Manitoba
Grower holds a planting party day every fall as a crowd gathers to help put 28,000 plants, and sometimes more, into theground
To do this, Mills runs high pressure air through a three-quarter inch steel pipe inserted into the plugged auger. He operates the pipe from outside the bin.
“Nobody has to go inside the bin. Pressure from the compressor breaks all the chunks so no one has to crawl over the corn or push anything down,” says Mills.
“Remove your auger and insert the three-quarter inch pipe with one elbow and stem. Blow out the plug by rotating the pipe back and forth in the sump. Use vice-grips to mark the stem position. The corn is going to fill the sump.
“Then take out the three-quarter inch pipe and replace the stem with the second elbow. Close the trap and insert the three-quarter inch pipe with both elbows in the tube. Blow the crop out of the tube. Be careful because the force is unreal and corn will shoot 50 feet. Then open the trap and if the corn falls into the sump, the process is complete. The whole procedure takes three or four minutes.”
In extreme cases with crop pillars, he drills a one-inch hole into the side of the bin.
Then he inserts a shorter pipe to reach the intermediate well.
In this case, he takes a three-quarter inch pipe, flattens one end and drills a three-eighth inch hole in the pipe’s side. He works this short pipe back and forth over the intermediate well and the crop flows.
Mills says he spent about $150 in total for all the pipe and fittings. That included a hose, three-quarter inch steel pipe the length of bin tube, two elbows, stem the length of auger width, valve, vice-grip and claw hooks.
The downside is the large amount of pressure required to loosen and move the grain. The typical farm shop compressor puts out about 50 cu. feet per minute. Mills’ system works, but it requires 250 CFM.
His solution is to rent a commercial compressor.
U.S. farmers are more regulated than Canadian farmers, which is why Mills says there’s one other feature of the system he really like.
“There’s no patents, no intellectual property, no legal hurdles. This can keep people from getting killed and it can keep OSHA off our farms. The farm shop solution is available to everyone.”