Crop material that should be feeding directly into the front concaves of a Case IH Flagship, 7230, 8230 or 9320 might be jumping the grates without the operator suspecting a thing.
A new modification is designed to put that crop material onto the front grates where it belongs.
Improvements in farm machinery often happen by accident. So it is with the Integrated Feed Lip developed by Sunnybrook Welding owner Gerald Foster, along with one of his customers, Alberta farmer Ray Hittinger.
Prototypes tested in 30 Series combines in 2013 field trials by Krumbach Harvesting of South Dakota reduced engine draw by seven percent compared to similar 8230 combines in the fleet. All Krumbach’s combines ran the same Sunnybrook MaxThresh concaves.
Read Also
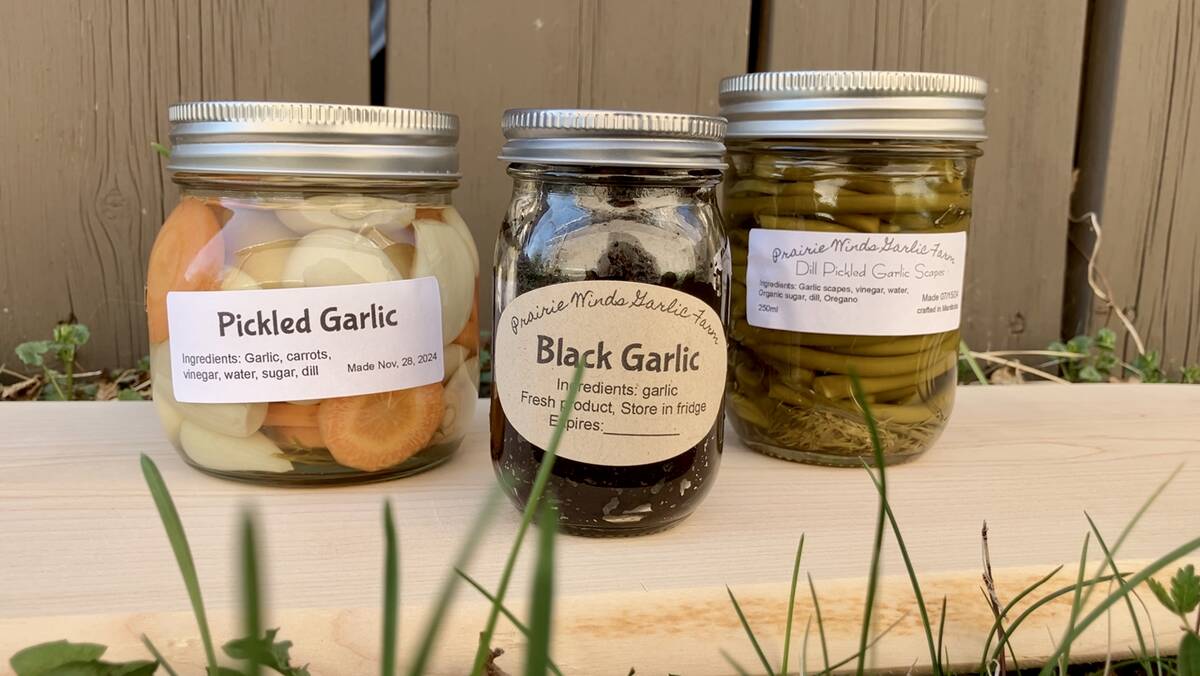
Growing garlic by the thousands in Manitoba
Grower holds a planting party day every fall as a crowd gathers to help put 28,000 plants, and sometimes more, into theground
The Integrated Feed Lip is a relatively minor modification that Foster and Hittinger thought up to compensate for changes Case IH made to its rotary combines a few years ago.
“The feed lip had previously been part of the front concave up at the front of the H-frame,” Foster said.
“That meant those concaves could not be used anywhere else in the system. Those concaves were unique to that front position.”
Removing the lip from the concave and installing it on the H-frame allowed Case IH to reduce its parts inventory. The concaves can now be used anywhere in the system.
However, that created a problem. The lip was now a fixed part of the H-frame as the concaves were adjusted up and down to set the clearances. It was stationary and did not follow the front concaves.
That meant the front side of the front concaves obstructed incoming crop. The obstruction became greater the more the concave was raised to achieve clearance for small grains and oilseeds. The dam can be as much as one inch if the operator is running tight clearance at the front of the processor.
It’s not as much of a problem when the concaves are lowered to open up the clearances.
Foster said he had never seen this particular manufacturing deviation turn into such a major problem until two years ago when Hittinger brought in an H-frame that needed work. It was from an 8120 with high hours and held four concaves.
“It was the first time I’d seen this. We thought the H-frame had maybe been bent or damaged somehow because the concaves didn’t sit flush,” said Foster. “But then we noticed that crop material had been grinding along the lip and wearing a groove into the front lip of the H-frame. It looked like it was cavitating around the side of the H-frame.
“His concaves had cracks at the front and showed severe wear at the front. That told us crop material was not easily carried into the front of the processor. The leading edges of the front concaves were like a dam stopping crop material from being brought into the thresher.”
Foster concluded that the dam created by the front surface of the concave could launch the crop material over those concaves. He said the crop material could sail right over the top of the rotor and become wrapped up for one complete revolution before being fed into the concaves.
“That’s a bad thing. The material travels one extra revolution for nothing. It wastes a lot of energy and it’s obviously hard on the machine.
“I have another customer, Danny Crow, who runs four 30 Series combines and a service trailer to keep them running. One day I happened to notice a bunch of cracked concaves in his trailer. He said it happens all the time. The front concaves on these combines take a beating because of that lip that’s part of the H-frame.”
Foster said the solution wasn’t difficult once he and Hittinger figured out the problem.
“Centrifugal force is always being applied to the crop material, pushing it up the lip and into the processor. It’s supposed to be swept right into the processor without delay or hangup of any kind,” he said.
“But if your crop material runs into that dam, if it hits the side of the concave frame, even if it’s half an inch, then the system isn’t working for you the way it’s supposed to.
“We just needed to modify the existing lip with an extension so crop material flows into the processor instead banging up against the front of the concave. So we modify the Flag Ship H-frame by adding to the original lip.”
The front concave box in the Sunnybrook modification is shorter to accommodate the increased dimension of the Integrated Feed Lip. Foster said that’s not an issue because the front box is the exact same one already manufactured for older Case IH and John Deere STS combines.
For more information, contact Foster at 780-789-3855 or visit www.sunnybrookwelding.com.