A yield monitor that measures paddle heap works fine for most flatland farmers, but farming in places like Idaho and Oregon, where they farm up the sides of mountains, requires a different approach.
However, the challenges of worn rubber paddles and side slopes can be overcome.
When it comes to paddles, the obvious fix is to replace them. With individual rubber paddles costing a couple dollars each, and complete chain assemblies listing for less than $700, there’s no excuse for running worn-out rubber paddles.
The grain that spills over isn’t lost, it just makes an extra trip or two up the elevator. It’s less of a problem with cereals, but larger, delicate crops like peas and beans can get beat up pretty badly wedging in between a paddle and the elevator wall.
Read Also
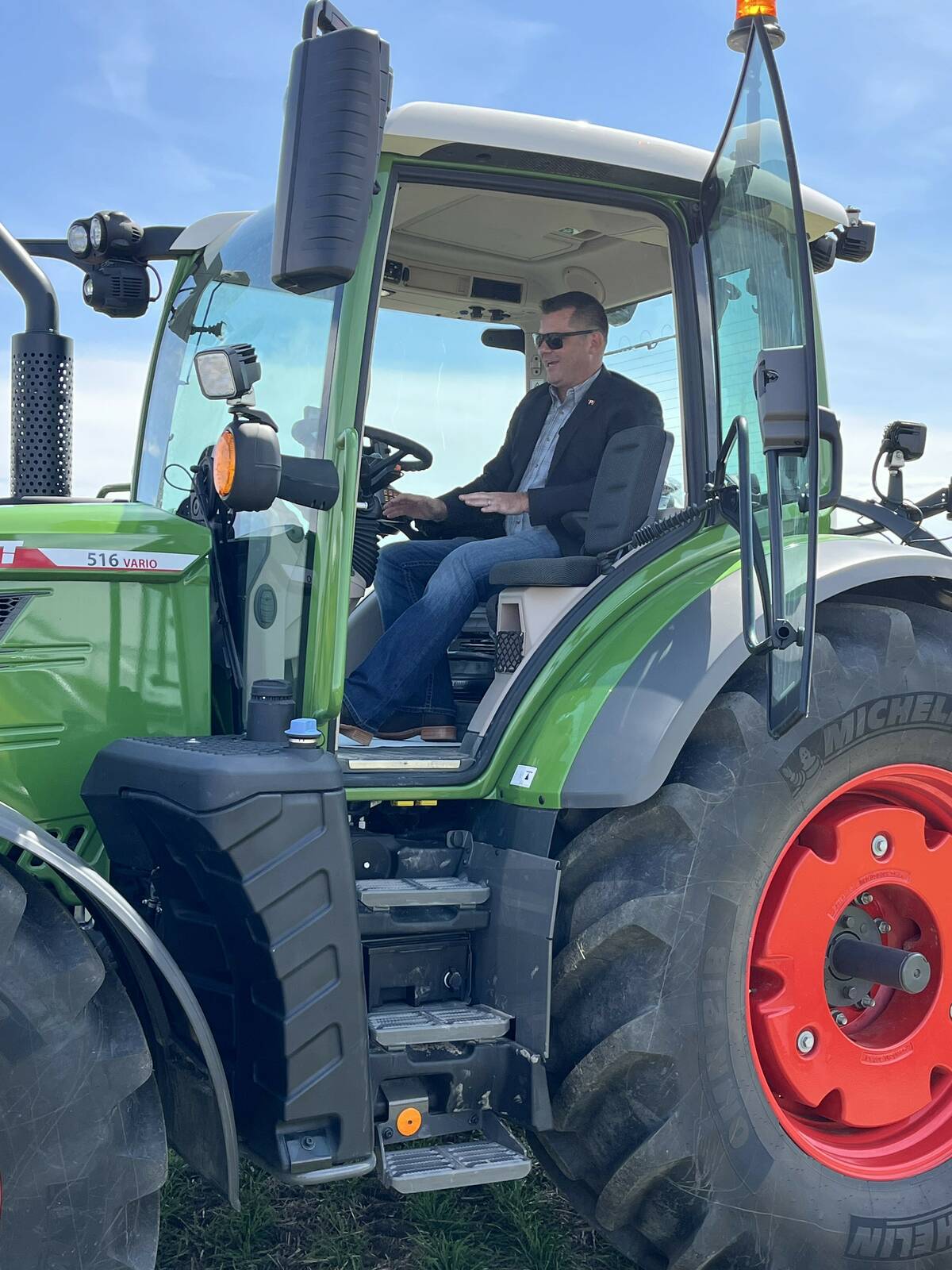
Farming Smarter receives financial boost from Alberta government for potato research
Farming Smarter near Lethbridge got a boost to its research equipment, thanks to the Alberta government’s increase in funding for research associations.
Other considerations are fuel consumption and wear on the combine. You’re asking the combine to do double duty by lifting that grain twice if you’re running worn paddles.
The twin challenges of compensating for side slopes and for worn paddles were at the front of Perry Casson’s mind when he designed his FarmTRX yield monitor.
Casson found the system maintained accuracy on any slopes they found in Western Canada, so they went looking for really big hills. That’s where northern Idaho enters the picture.
“We brought a system down there last year. Most of their fields are on a 35 percent side slope. Some are 40 percent,” says FarmTRX’s Mark Hammer, adding that even on severe slopes, they found that the peak of the grain shifts so slightly that it’s almost imperceptible in the sensor reading.
“Before we went to Idaho, we expected that to handle those slopes, we’d have to add RTK and accelerometers to know the exact attitude of the combine to compensate for slope in our post processing routines.
“The grower and his agronomist and all of us were shocked at how well the system mapped the geomorphology of the hills. There was no reason to add RTK or other slope compensation.”
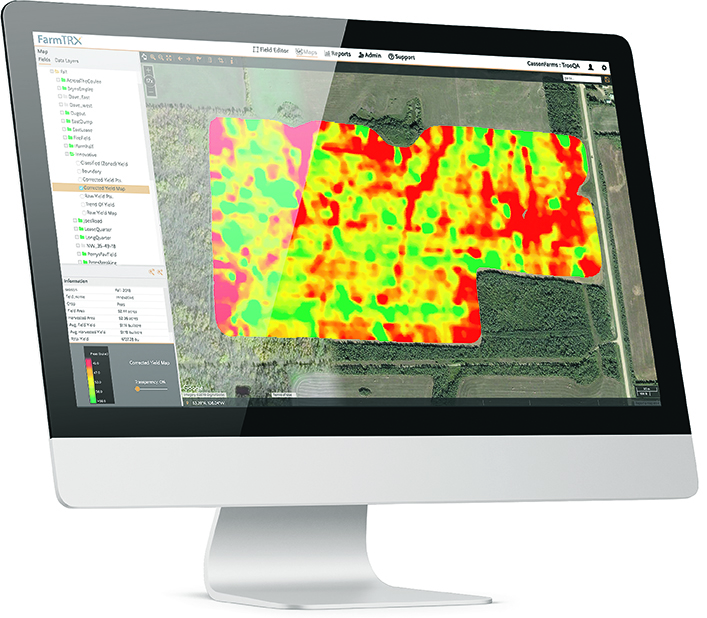
Worn rubber paddles is another issue, even if you farm totally flat land.
Hammer says that, like the slope challenge, there’s no need to build compensation into the monitor. However, it is necessary to mount the sensor as high up in the clean grain elevator as possible.
“We measure the actual grain dropping into the hopper itself. Typically, what happens with curved paddles is you lose grain down the sides as the paddles go up. There’s not as much loss with large seeds like corn, but small seeds like canola have more of an issue. By the time a paddle gets to the top, its load is stable. It’s lost all the grain it’s going to lose.
“As the grain rains down in front of the sensors, and your paddles need replacement, we can actually see the distribution of the frequency of yield points. The signal-to-noise ratio tells us the readings are false. We can filter that out if it’s not too bad. But once it reaches a certain point, it blocks the sensor completely because all it sees is a continuous shower of grain. It can’t turn on and off like it’s supposed to.
“That tells the operator he needs to change the clean elevator chain. With a bad elevator chain, you’re going through so much extra fuel and you’re working the combine so hard. And damaging grain. For $600 you can bring it back to new condition.”