New study includes recommendations for energy-efficient boilers, larger or variable drive fans and LED lighting
A recent study of 38 Alberta hog operations showed energy costs could be trimmed by an average of 26 percent.
Alberta Pork commissioned Dandelion Renewables, an energy consulting firm, to study hog barn energy costs and suggest potential ways for producers to reduce them.
Steve Gladwin, director of engineering for the company, took inventories of electrical load and gas consumption at each of the 38 farms.
Among them all, the average energy cost was $40,000 per year, not including the fixed costs indicated on bills, such as delivery and administration.
Read Also
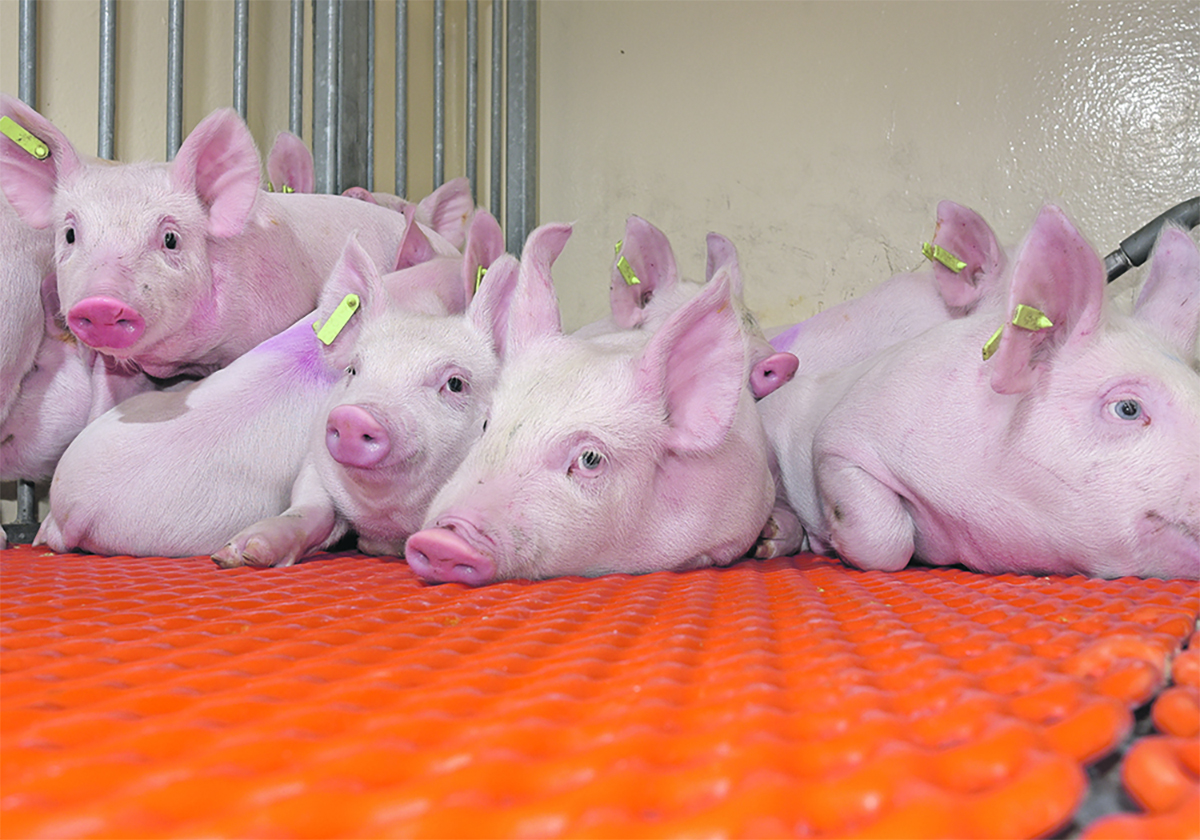
The Western Producer Livestock Report: July 17, 2025
U.S. hogs averaged $106.69 on a carcass basis July 11, down from $110.21 July 4.
“That’s a reasonable estimate, $40,000 on average,” said Gladwin.
“Forty-two percent of that $40,000 is primarily natural gas for heating the barns, and the rest would be electricity, primarily.”
Those costs are the equivalent of energy use in about 50 residential homes, he added.
Because so much energy goes into barn heating, Gladwin said he looked closely at air flow and pig comfort levels related to hot and cold pockets that can make heating systems work harder than necessary.
Natural gas boilers were the most common heating units on the farms surveyed, and Gladwin said more efficient condensing boilers might be a money saving option in some cases.
Exhaust fans make up about 34 percent of electrical energy costs and are vital for summer use. Gladwin said savings might be possible by using larger diameter fans, but retrofitting existing fans is unlikely to pay off. However, farmers erecting new barns might want to consider them.
Most barns use variable speed exhaust fans for winter ventilation, most commonly Triac units that don’t provide as much energy savings at low speeds as some other technologies.
Gladwin suggested variable frequency drive fans as an option because they use less energy at low speeds.
The most efficient of all is the electronically commutated motor (ECM) fan, but it is five times more expensive than Triac so it would take a long time to get a payback on energy savings.
Barn lighting was part of the study, and Gladwin found T12 and T8 fluorescent tubes were used on about 25 percent of the farms surveyed. Compact fluorescent lamp (CFL) bulbs and light emitting diode (LED) bulbs or tubes were also common.
LED tubes use half the electrical power to emit the same amount of light as fluorescent tubes, he said.
“But just as a caveat to ‘let’s just run through all the barns and change all the light bulbs,’ probably every farm (that) has started introducing LED lighting to their barns can probably talk about maybe having trial and error at sourcing different bulbs.”
Gladwin said the colour of light from LED bulbs can vary and so can the light distribution. He did not identify energy savings from replacing CFL bulbs with LEDs because the latter are about 25 percent more expensive. There might be an advantage when the cost of LED bulbs comes down.
Gladwin found that heat mats in farrowing pens were common in many barns, and use of heat lamps varied. He saw some energy savings potential in relying solely on mats, or in using heat lamps only for the first 24 hours of piglets’ life. Use of a drying powder might also reduce the need for lamps for an extended period after birth.
After the assessments, Gladwin examined potential renewable energy options for hog operations, among them geo-exchange, solar, solar-thermal, solar wall, wind, biogas, biomass and heat recovery ventilation.
He found that solar and heat recovery ventilation showed the most promise to reduce energy costs in many operations.
Gladwin said all 38 producers received assessment results and recommendations, but not all have acted upon them. At the time of the study, some funding was available through Growing Forward 2 to fund energy-saving upgrades.