The flameless dryers are retrofitted to dry grain without transferring it from the bin, saving time and reducing kernel damage
A slowdown in the oil and gas sector provided the impetus for an innovation in grain drying.
ConleyMax, a company that rents its patented flameless air heaters to the oil and gas sector, started looking for alternative income streams when that sector of the economy took a downturn.
Chief executive officer Kevin Baker noticed that many of his farmer employees had to take time off to go back to the farm to haul grain to a commercial dryer, or shuttle it back and forth from the bin to their own on-farm grain dryer.
Read Also
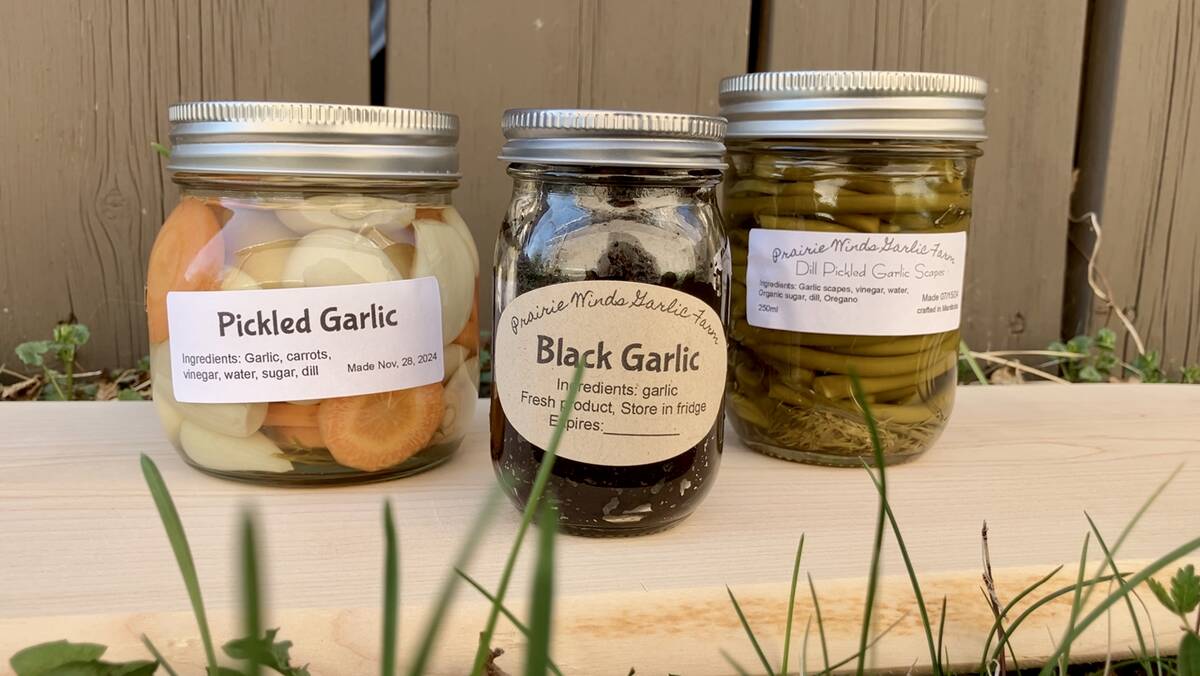
Growing garlic by the thousands in Manitoba
Grower holds a planting party day every fall as a crowd gathers to help put 28,000 plants, and sometimes more, into theground
“We were just talking to them and saying there’s a better way of doing this,” he said.
Baker knew that his collection of 300 portable, flameless dryers could be retrofitted to hook up to aeration systems on modern grain bins.
“We just said, ‘We should go and hook one of these babies up to your bins and see how it works,’ ” said Baker.
It worked so well that the company set about designing equipment and hoses to connect the units to the bins. This is the second year the friction-based dryers are being used in the agriculture sector. Baker said 30 large farming operations have rented the machines.
The biggest advantage they provide farmers is the ability to dry down grain without having to move it out of bins, saving time and trucking costs.
Baker said it works particularly well with a crop like lentils because it eliminates the risk of chipping, cracking or splitting the crop, as can happen when using traditional mechanical dryers.
“When you put it in a normal drying operation, it spins like a washing machine and it chips the lentils and that takes the grade off of them,” he said.
Baker has calculated that the savings of maintaining a No. 1 quality lentil instead of downgrading to a No. 2 is $7.57 a bushel, or $36,000 per quarter section, based on an average yield of 30 bushels per acre.
The machines also work well for drying barley, a crop sensitive to heat. The automated dryers can be set to limit the maximum drying temperature, reducing the risk of downgrading the crop from malt to feed.
“We never started this business to be in the agriculture business at all, but what we’ve been able to accomplish is something that is pretty spectacular,” said Baker.
In addition to the potential for increased revenue and decreased costs, the heaters are safer to operate around grain dust than flame-based heaters.
The ConleyMax machines intrigue Ron Palmer, a retired University of Regina engineering professor, who has conducted extensive research on grain drying.
“The concept is excellent,” he said.
Palmer appreciates that the machines are portable, can be towed from bin to bin and do not require power. He believes they would be ideal for remote sites that lack access to power.
But he doesn’t believe it is a technological revolution.
“You could easily build this yourself (for) a whole lot less money,” said Palmer.
“This is nothing more than if I took a genset and stuck it in front of an existing aeration fan. I could achieve the same thing for a whole lot less.”
He acknowledged that the homemade version would require hoses, fittings and a trailer, and for that reason some farmers may prefer renting the equipment.
Baker said Palmer’s genset version doesn’t have the safety features of the ConleyMax dryers, such as a brushless alternator, positive air shut-off and over-speed shut down.
“You could do what he says, but it’s a huge safety risk,” he said.
And it would require supervision, while the ConleyMax machines are automated and can be set to run at a certain temperature all night, if desired.
Rental rates for the machines start at $1,450 per week. Monthly rates are negotiable.
They have to be returned by Nov. 1, so they can go back into service in the oilfield. It takes about 10 to 12 hours to dry a bin full of grain at a cost of about 70 to 80 cents per bushel.
The company rents the machines from its main offices in Alberta and Saskatchewan, as well as a variety of satellite locations across the Prairies.
The machines vary from 350,000 BTUs to 1.4 million BTUs, but the most common is the 700,000 BTU unit.