Innovations to come | New hydraulics, power take-off and electrical parts will drive how future tractor models are used
KANSAS CITY, Mo. — Tractors have been evolving since the first mobile farm power source was allowed to drive itself forward rather than be pulled by horses.
“It’s an iron horse that evolved over time, from pulling to powering. Now it’s an office too,” said Ed Kreis of John Deere Waterloo Works in Waterloo, Iowa.
“It is much more than a drawbar and a belt (drive) of bygone days. More than a p.t.o. More than a set of hydraulics. And it will be more yet as we develop new ways to think about the tractor and what it means to food, fuel and fibre production.”
Read Also
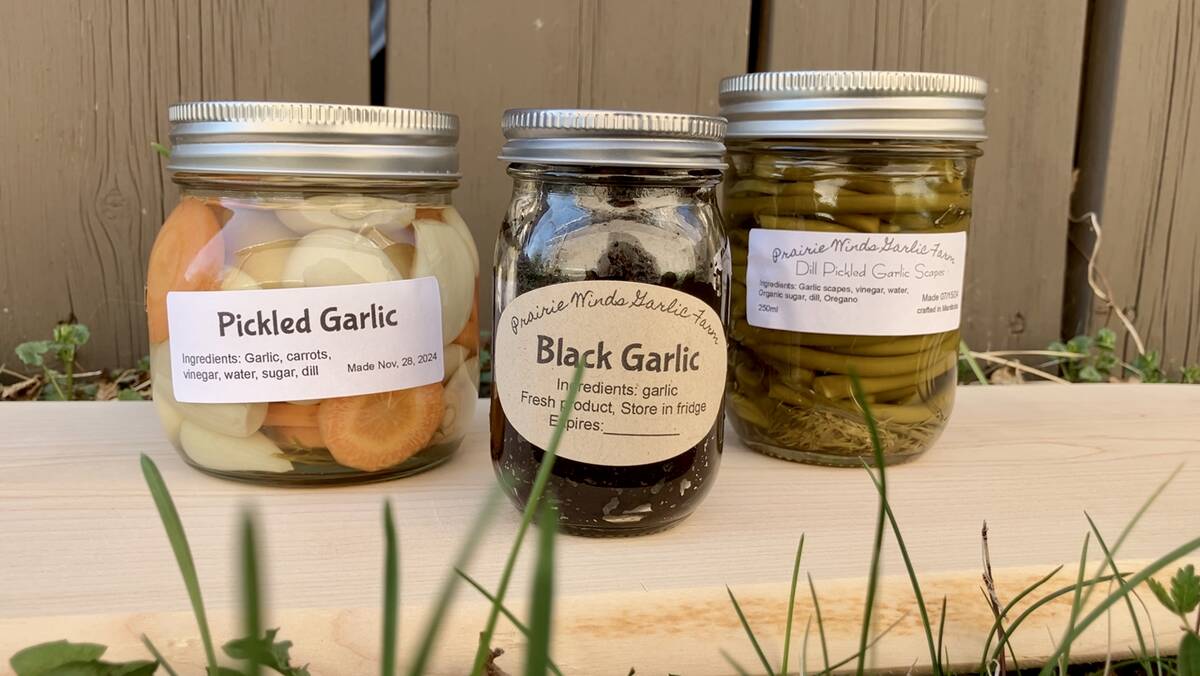
Growing garlic by the thousands in Manitoba
Grower holds a planting party day every fall as a crowd gathers to help put 28,000 plants, and sometimes more, into theground
Here’s what changes to expect as the tractor continues to evolve.
The first power take-off units began showing up in the early 1920s on IHC tractors, augmenting drawbar and belt drives. Farmers and manufacturers have been finding ways to make more use of tractors ever since.
“It was something a team of horses didn’t have and stationary machines couldn’t do,” said Kreis.
It also helped end the debate about the role of the tractor in the field versus the traditional horse. Horsepower in the field would forever be mechanized.
The American Society of Agricultural Engineers created a standard for the p.t.o. in 1927, and Cockshutt made them safer with the creation of the live p.t.o. after the Second World War.
Divorcing engine and ground speed from the p.t.o. through gearing, CVTs and electronics has allowed producers to reap fuel efficiencies from the latest generation of tractors. Boosting engine power during p.t.o. applications is another way to allow for drawbar fuel efficiency and higher power draws during processing activities.
While 540 and 1,000 r.p.m. are the current standards, a new 1,300 r.p.m. is being explored and is expected to arrive on farms shortly. That will be the new Type 4, with a 57.5 millimetre shaft, which is aimed at higher power consumption applications.
Front mounted implements are standard fare in other parts of the world, but in North America most of the implements run in the wrong direction, clockwise, when mounted up front.
New demand for large triple hay mowers and other nifty European tools will likely mean that North American market tractors will shift to a front p.t.o. international standard, counter clockwise.
However North America and the European Union still have differing numbers of splines, speeds and, in some cases, shaft sizes.
Kreis said hydraulics have made life on the farm safer, more productive and cheaper to automate.
“The future is adopting some things that farmers have done themselves and some technologies from other industries such as construction,” he said.
Hydraulics of the late 1940s and early 1950s were crude and low-powered by current standards. Open centre circuits fed by vane and gear pumps with pressures below 1,000 pounds per sq. inch were the rule of the day.
The Deere H put out 555 pounds per sq. inch, while the B worked at 610 with a flow of 7.7 gallons per minute.
Pumps were run off the clutched side of the transmission, so stepping on the clutch halted the hydraulics. Live power and open centre systems made hydraulics more user friendly and, when not in use, allowed the engine to be freed from much of the loss due to pumping duties.
Pressures now reach more than 3,000 p.s.i., even with open centred systems, although they are typically found on smaller tractors.
Radial piston pumps took over in the 1960s, and with that came the move to 2,250 p.s.i. Those pumps can maintain a maximum pressure at all times while de-stroking the pump to drop the flow when demand isn’t required. This reduces the heat and engine draw when not using all of the flow generated power.
Hydraulic flow and pressure demands in the 1980s meant that most systems moved to 3,000 p.s.i. Closed centre systems and radial pumps are the favoured choices to this day.
Multiple pumps, rather than just prioritizing valves, are also a trend. These are intended for instances where high pressure and instant demand needs, such as steering, braking and implement down-pressure, are separate from continuous high flow rates for tools such as air seeder fans.
Today’s hydraulics are moving to higher flow and return rates with the move away from the standard .5 inch hydraulic coupler models and the introduction of the .75 inch model, in which the male is on the implement and the female is on the tractor.
As well, flat faced couplers are moving into some agricultural applications and might be a future trend to reduce flow restrictions.
Power-beyond situations are finding their way onto tractors, in which the implement runs the show, taking direct flow from the tractors’ pumps and handling the valving and controls electronically at the implement.
Higher pressure systems, such as the construction industry’s 4,000 p.s.i. hydraulics, will likely soon find their way into farming, said Ken Stoss, also of Deere’s Waterloo Works tractor facility.
Growing supplies of electricity in rural areas resulted in the first electric tractors tethered to transformers with long extension cords. By the end of the 1930s, war and the impracticality of the technology silenced the quiet field power.
After the Second World War, North America became fascinated with electricity’s adaptability and ability to reduce labour. Its motors could be right-sized for nearly any job, from turning a washing machine to rolling a steel mill. Agriculture was not immune to its magnetic attractions.
In 1954, International Harvester rolled out a diesel tractor with a built-in generator. The idea was that the tractor’s engine would provide drawbar power while the generator would feed remote power to electric motors mounted on driven implements such as balers.
Farmers who weren’t ready to buy a new Farmall 450 Electrall could pick up a p.t.o. driven generator and add it to an existing Farmall. A lack of interest during a time of low cost fuel relegated the International and others, such as the 1959 Allis-Chalmers D-12 fuel cell tractor, to the history books.
However, generator and fuel cell tractors have returned in the past few years. Deere, Deutz and others have released hybrid units. New Holland has prototype hydrogen fuel cell units, which emit water as exhaust.
Agco has its Electrogator, a hybrid that generates electricity to drive wheel motors on a high-capacity sprayer. The company says it believes the technology would also be appropriate for combines and baling tools.
These are made possible by the invention of moderately priced, high density transistors called IGBTs. A product of the early 1990s, they made it possible to have the modern inverters we use today to efficiently control or valve power.
Joachim Sobotzik of Deere’s technology development centre in Kaiserlautern, Germany, has been working with the electrical powered side of the agricultural machinery future.
“Tractors and implements are becoming so tied together it can be hard to know where they are two or one,” he said.
“Smart implements, like in hydraulic innovations, can demand only the power they need, and tractors only make what is needed. Better than hydraulics. Better even than in engines precisely feeding a drawbar its needs.”
Deere’s versions are the 7430 and 7530. They came out in 2007 and provide high voltage power that can be used to run implements.
The new standard for hybrid power or machines that produce electricity to solely run implements will likely be the 700 V DC or 480 AC format. They are common in industrial applications.
Electrical systems like it cool, so adding electricity to diesels will require additional cooling circuits that hold temperatures down to 65 C, said Sobotzik.
“Powering large implements and machines can be done very efficiently. A combine, for instance, or a large baler. Air (seeding) fans, (spraying) equipment.” he said.
Engineers say fertilizer applicators towed by tractors or mounted on the sprayer-applicator chassis might be one of the first field tools adopted by producers.
The applicator box and meters might cost $40,000 but will apply up to $200,000 in fertilizer annually.
“Electrically operated and managed with an ISOBUS linked (GIS) system, it would be one to four percent more accurate, able to vary its load and spread accuracy precisely and instantly,” Sobotzik said.
“It would pay the farmer or applicator to buy one, as the technology pays for itself right away.”
Stoss said the near future won’t see a rush to replace hydraulics and p.t.o. systems with electricity.
It will supplant mechanical and hydraulic transmission where appropriate, but more likely it will be a hybrid of all three, adapting to meet the needs of industry based on convenience or efficiency.