Saskatchewan’s health regions are working to change the way they deliver patient services, with the goal of ending wait times and ensuring services are available when patients need them.
That would be good news for rural residents who sometimes find their hospitals closed or wander through a maze of appointments and waiting rooms to get care.
The lean system of management, adopted from the manufacturing sector, was piloted in the Five Hills Health Region in the Moose Jaw area in 2006. Since 2009, all the regions have come on board.
Read Also
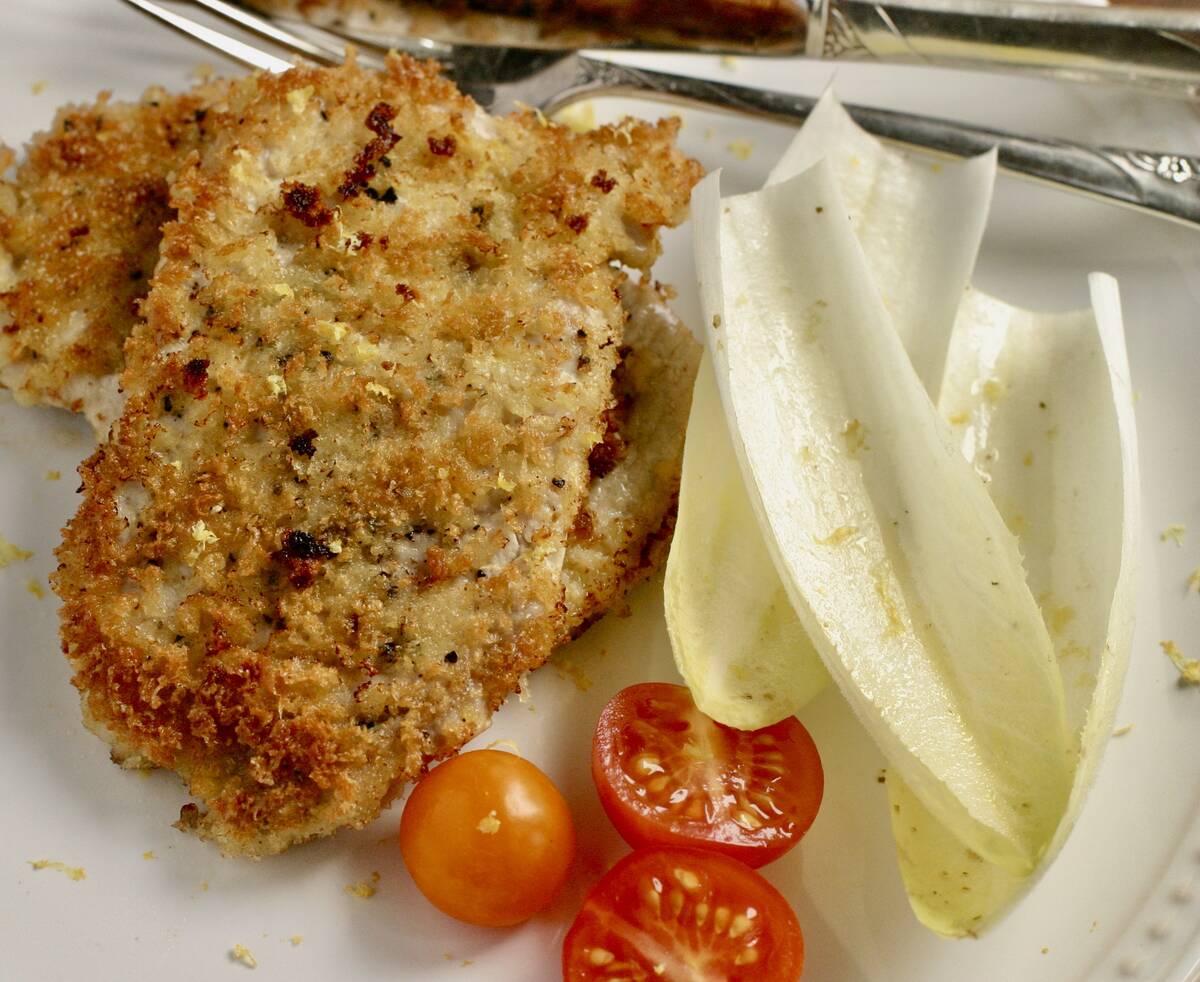
Nutritious pork packed with vitamins, essential minerals
Recipes for pork
Trish Livingstone, the province’s manager of health system quality and efficiency, said it’s important that all the regions participate because patients often seek or require care in more than one region.
She said the methodology applied through lean does result in cost savings but it isn’t about cost cutting.
Lean tools, when applied to health, look at services from the patient perspective to identify and eliminate waste. Patients are the primary customers, said Beth Vachon, chief executive officer of the Cypress Health Region.
The focus on patients ensures quality care and safety while keeping wait times and travel down.
Staff also benefits because they can maximize the amount of time they spend on patient care.
“The whole process of lean is that you take a look at the current state that you’re working in and really talk about what the future state needs to look like,” Vachon said. “Then you work through, using a number of tools and measurements, to determine if there are more efficient ways that we can bring value to our patients.”
In rural health regions, providing safe, consistent service is a priority, she said.
At the Leader hospital, the region has sometimes struggled to do that. A lean project is examining the process from the doctor’s office through the entire health care team to determine how to better move patients through the system.
Vachon said a staff member raised the issue of how cumbersome it can be to have simple tests performed. From checking in at the family doctor’s office, seeing the doctor who requests lab work and X-rays, travelling to the hospital, checking in at the lab, having the test done, checking in at X-ray and having that done, then returning to the doctor’s office and checking in again, the waiting can be extraordinary.
“By the time all is said and done, we can have somebody in and out of eight different waiting rooms in a day to deal with a medical issue,” Vachon said. “There’s got to be more efficient ways to bring value to the patients that we provide care to.”
In Leader, a capital proposal is in the works for an integrated long-term care facility that involves using architects who are familiar with the lean methodology. The building design would focus on how best to flow patient traffic, which is another lean health care principle.
Vachon and Livingstone agree the health care system became un-wieldy over decades as new technologies arose and services were added. Applying lean will also take decades.
Vachon said as health care became increasingly specialized and programs were set up, the system became one of silos. It also focused more on the providers than the patients.
“We need to get back to the point where we’re having discussions across programs,” she said.
Livingstone used appointments as an example of how the system accommodated providers over patients. Applying lean to the Saskatchewan Cancer Agency has created a shift in that thinking.
In the past, patients needing radiation therapy were referred to the agency for a first appointment. Then, they required a second appointment, usually in about a week, for a CT scan to plan the radiation treatment.
The agency staff looked at how to reduce that wait time, and targeted a 50 percent improvement, Livingstone said.
They achieved 92 percent.
“Because of that, they were able to offer a patient their initial appointment and CT scan on the same day.”
Patients were offered the choice to have this option and 60 percent took it. This resulted in less travel for patients, particularly those in rural areas.
But she also said that changing one single thing doesn’t always result in better service. Speeding up the time patients entering an emergency room are assessed doesn’t mean they still won’t be waiting hours for a bed.
“What lean has taught us is to look end to end,” she said.
But it can’t all be done at once, so the lean system will take years to fully implement. Various programs looking at access to primary health care, surgeries and ambulance services are all underway.
While there will be cost savings as a result, saving money is only a side benefit to better patient care and a more efficient health system, said Livingstone.
“Higher quality does, by default, give us a lower cost,” she said.