Sprayers can run at 25 m.p.h. | A lack of innovation means nozzle technology hasn’t kept up with high sprayer speeds
Air turbulence and wind created by high sprayer speeds can destroy spray patterns and adversely affect spray coverage.
Farmers seed at 4.5 m.p.h. or less, even though they can go faster. They combine at five m.p.h., even though they can go faster. That’s because they know that prudent machine speed puts more money in the bank.
So why do many producers run their high clearance sprayers at top speed, regardless of how much product hits the target? asked Tom Wolf, a crop spray researcher.
Read Also
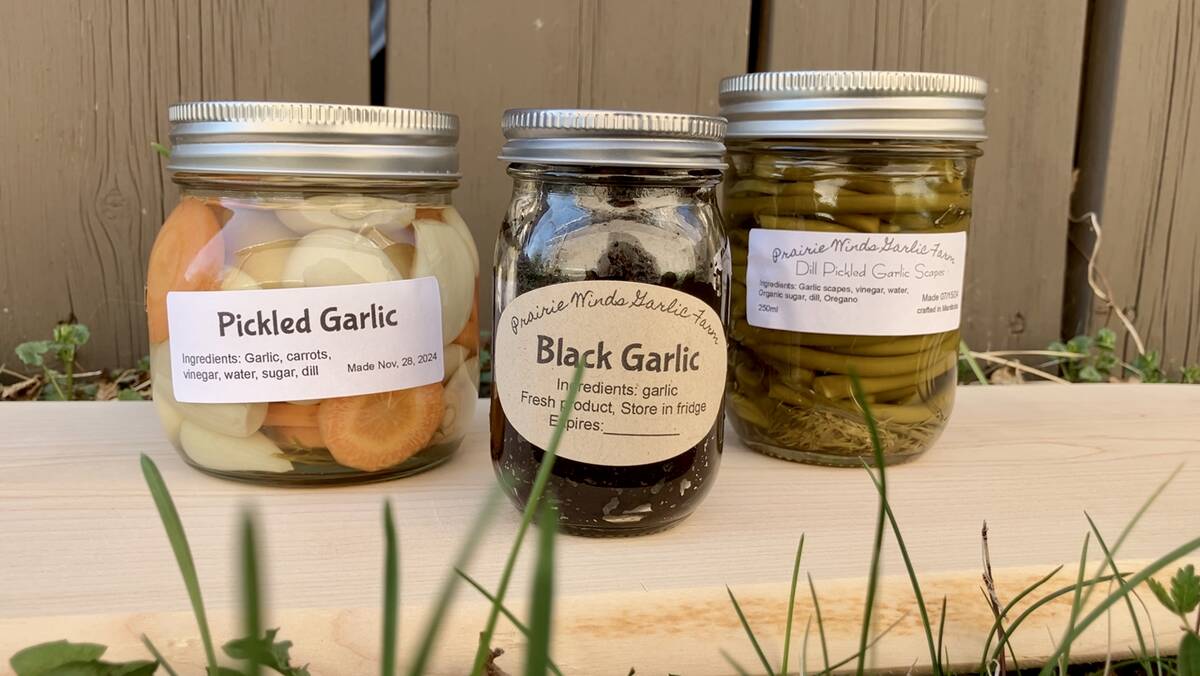
Growing garlic by the thousands in Manitoba
Grower holds a planting party day every fall as a crowd gathers to help put 28,000 plants, and sometimes more, into theground
“Farmers can get down out of the cab to dig up a few seed rows and actually see where the seed and fertilizer are being placed. With that knowledge, they can determine their maximum seeding speed,” he said.
As well, he said the Canola Council of Canada and drill manufacturers have done an excellent extension job on the Prairies when it comes to explaining the importance of prudent ground speed.
“It’s the same thing on the combine,” he said. “You can look at your monitors and look in the bin and then figure out if you can go faster or if you should slow down. But with the sprayer, it’s a different story. It’s difficult to get out of the cab and do any kind of accurate assessment of how much crop protection product is actually landing on target.”
The reality is that spraying is often a matter of time rather than quality. As well, many farmers admit they just hate spraying and want to get it done as soon as possible.
Those issues are compounded by the fact that manufacturers have made huge improvements in sprayer suspension systems, allowing operators to run at 25 m.p.h. without de-stroying their machines.
But do those speeds destroy the quality of the spray job?
“Manufacturers have invested tremendously in chassis improvements, strength, power, liquid capacity, hydraulics, electronics, cabs and everything else, but there is absolutely no relationship between these improvements and a farmer’s ability to kill the pests,” Wolf said.
“All they’ve accomplished is increased capacity and increased speed and create more problems for nozzles. The fundamental problems we’ve always had are not being resolved. In general, spray deposition is getting worse, not better, and it’s largely because of travel speed.”
Wolf said problems caused by high-speed spraying include poor canopy penetration, more dust from faster tire rotation and higher boom heights, which contribute to poor spray targeting and spray drift. Given the state of today’s nozzle technology, the only way to address those problems is to slow down.
Wolf thinks sprayers are now large enough and fast enough to create significant air turbulence of their own.
“High clearance sprayers have aerodynamic properties that affect spray deposition, just like the aerodynamic properties of spray planes. Things like wing shape and boom shape affect deposition,” he said.
“We may have to start looking at the aerodynamics of ground sprayers in the same way we deal with aircraft. Aerodynamics were never a factor when we ran our ground sprayers at eight m.p.h., but it’s a whole new ballgame when you double or triple that speed.
“Let’s say you’re spraying at 20 m.p.h., which is too fast by the way, and you’re facing a 10 m.p.h. head wind. You are generating a ton of air movement around that tractor unit and boom as one air flow hits the other air flow. That has a huge impact on the spray pattern and its ability to penetrate the canopy. But do we know what that impact is? No.”
Another problem is caused by the traditional sprayer’s reliance on pressure to control liquid flow.
Pressure in the system might be 50 to 60 pounds per sq. inch when a farmer sprays at 20 m.p.h., which is where most modern low-drift nozzles work well.
Pressure drops by 25 percent when the operator slows to 10 m.p.h. for rough ground, a hill or a turn because of the square root relationship between pressure and flow rate. As a result, nozzle patterns collapse and sprays become too coarse.
The square root relationship means that if operators want a two-fold range of travel speed, from 10 to 20 m.p.h., they will also need a four-fold range of pressures, from 30 to 120 p.s.i.
“We’re pushing the envelope with this example because most pumps won’t do 120 p.s.i. Most nozzles start to give a drift-prone spray at that pressure. And when you drop to 30 p.s.i., you get extremely coarse droplets,” Wolf said.
“Most operators want that travel range of 10 to 20 m.p.h., but that range will give you a dramatically different range of spray qualities. And of course that has a major impact on the quality of the spray application in terms of drift, efficacy, canopy penetration and uniform coverage.”
He said a silver lining to this story is that air induction technology has expanded the speed range at which today’s farmers typically spray. The benefit is that air induction nozzles do a better job at higher pressures than conventional nozzles, and they do it without too much drift.
“Air induction technology has essentially given us a 1.8:1 ratio for our travel speed. If your maximum travel speed is 18 m.p.h., then your lowest possible spraying speed is 10 m.p.h.,” he said.
“But that’s not enough of a range for some. If you want a wider range of travel speed, then you have the Pulse Width Modulation systems. There’s the SharpShooter from Capstan and AIM Command from Case. We also have VariTarget variable rate nozzles with flexible orifices that open up just a little to allow more flow under higher pressure.
“A new technology from Pentair (Hypro) that will be ready for introduction in 2015 or 2016 is a nozzle body that will hold a number of nozzles and turn them on or off according to the requirement.”
Wolf said that despite these innovations, there is a lack of investment in nozzle research and development, which is why nozzles can’t keep pace with sprayer speeds.
“The major sprayer manufacturers are in a race,” he said. “They’re all telling farmers, ‘hey, we can go faster than the other guys.’ That’s not the message they should be sending. They should be talking about quality of the spray application.
“They’re able to duck that question because they don’t make nozzles. They leave that to someone else. And this is an interesting point. Most of the world’s major nozzle manufacturers are small family-owned businesses.
“That includes Agrotop (Greenleaf), Billericay Farm Services (Air Bubble Jet) and Wilger (ComboJet). T-Jet is the world’s biggest nozzle manufacturer, and I believe they’re still family owned.”
Wolf said some of these companies have research and development budgets in the tens of thousands of dollars rather than tens of millions.
“Given the size of these companies, I’d have to say that we get tremendous value when we spend $10 to buy a nozzle,” Wolf said.
“I’ve been in some of these plants and watched them flow test every single nozzle by hand. That’s probably millions of nozzles in a year flow tested manually.”
For more information, contact Tom Wolf at agrimetrix@gmail.com.