Corn growers who want individual row control without the expense of a new planter can make it happen with an aftermarket electric motor drive.
The Graham Electric Planter Drive (EPD) is available as a retrofit for all brands and model years of planters sold in North America, including finger type and vacuum type.
The modification was invented by Jerry Graham and his son, Toby, who farm 2,000 acres of irrigated corn in eastern Colorado. They plant the crop with a Monosem twin row planter, which they modified six years ago for electric drive.
Read Also
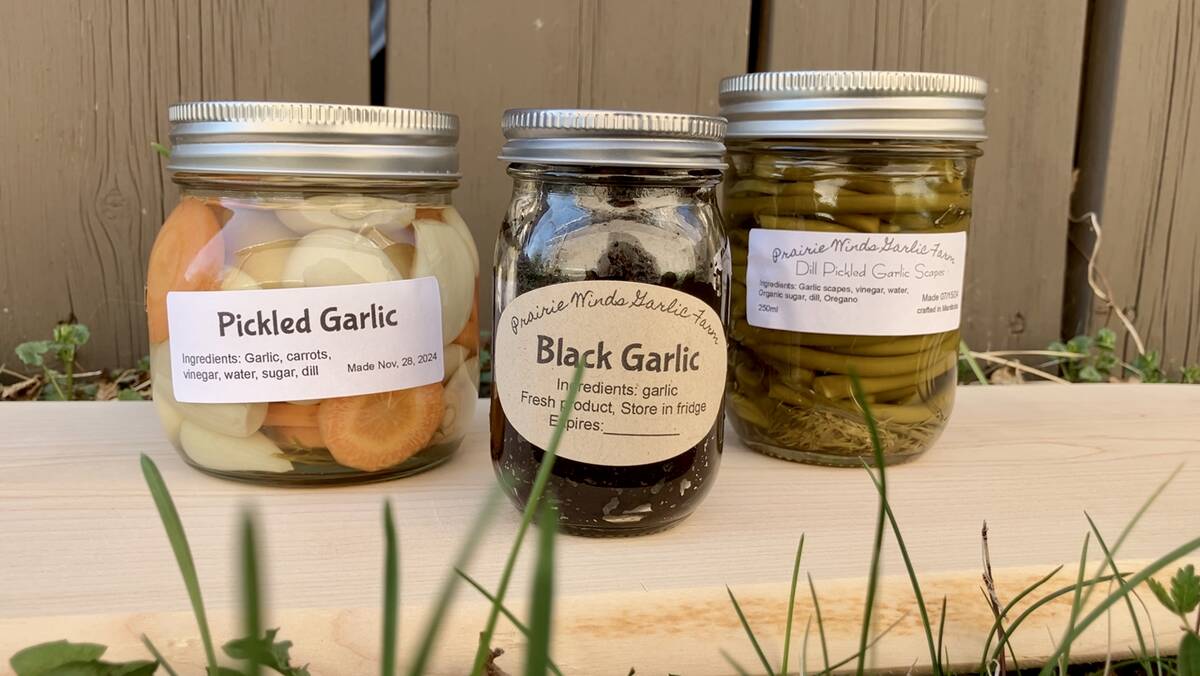
Growing garlic by the thousands in Manitoba
Grower holds a planting party day every fall as a crowd gathers to help put 28,000 plants, and sometimes more, into theground
The family also sells the Graham Command rate controller, which is designed specifically for the electric motor drive system.
Corn planters are built in multiples of four row units, so the Graham system is ordered in multiples of four.
Each EPD kit includes four weatherproof electric drive motors, one control board and the wire harness necessary to tie it all together. A control board is built to manage four rows.
The kit also includes the interface between the electric motor and seed plate shaft. Each four-row kit is custom assembled to fit the customer’s specific planter.
One kit sells for $4,000 and the Graham Command rate controller is an additional $1,300.
The Graham EPD is available for single or double row planters. Most single row planters require no drive chains or sprockets in the upgrade. An additional alternator may be required for larger planters.
“Individual row control with electric drive lets you do very precise variable rate fertilizer and plant population,” said Toby Graham.
Each row is configured by the Graham Command rate controller, he added.
“Basically, each row in our system is its own individual planter, based on its geographical position on your prescription map. You can write a prescription map with different plant populations, even on a row by row basis if you want,” he said.
“It’s really handy for guys planting male and female rows at the same time. You don’t have to change sprockets or mess around changing seed plates. If you have our rate controller, you just change the population on the prescription map.”
Graham said the EPD will work with any rate controller that has section controls and a PWL style outlet. The interface boards that he builds work only with PWL plugs, he added.
“We designed it so our interface board fools the rate controller into thinking there’s a hydraulic drive and clutches all hooked up,” he said.
“We calculate how fast the rate controller will spin the hydraulic drive, and that’s the r.p.m. we make the electric motor spin. And it’s an instant response.”
There are two levels of controllers: GrahamCommandLight only does plant population management, while GrahamCommandPro does plant population plus turn compensation and individual row prescription planting.
For more information, contact Toby Graham at 303-885-7428 or visit www.grahamelectricplanter.com.