FARGO, N.D. – As Kevin Anderson pulls his 60 foot drill over a field, his variable rate controller automatically gives him the seed variety blend he wants for the lowlands, mid-slopes and knolls. And, when he put in his winter wheat crop this fall, he used his prescription maps to vary the seed rate.
If this sounds like futuristic technology, then the future is now, because the equipment to do select-a-seed and variable rate seeding is available to any farmer who owns one of Anderson’s drills.
“We can now vary the rate from three different seed tanks on-the-go,” said the farmer and inventor from Andover, South Dakota.
Read Also
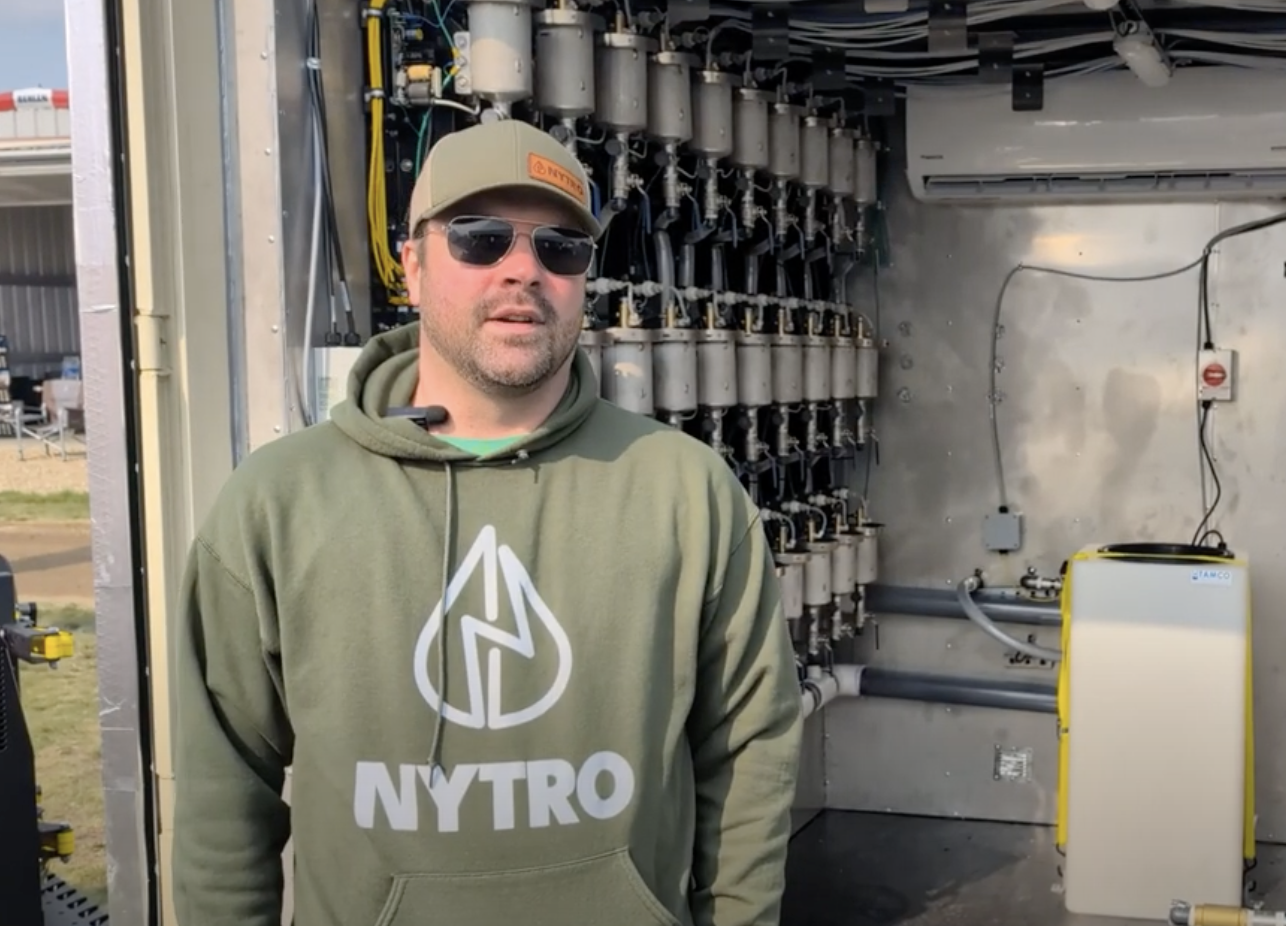
VIDEO: Green Lightning and Nytro Ag win sustainability innovation award
Nytro Ag Corp and Green Lightning recieved an innovation award at Ag in Motion 2025 for the Green Lightning Nitrogen Machine, which converts atmospheric nitrogen into a plant-usable form.
“The prescription map can call for virtually any blend of three seeds we need, depending on the soil characteristics at that specific point in the field.”
Anderson has devised a simple field test to demonstrate how the equipment works. He starts with a prescription map that defines the different soil types, usually based on topography.
“We’ll have what I call a racehorse variety that performs really well on the heavy soils in the bottomland. We treat those seeds with a red inoculant so we can identify them after the drill pass.”
For mid-slopes, he uses a green inoculant to identify the seeds that should have better agronomic performance on those soil types. There’s no racehorse for the eroded knolls. Rather, he uses a mule variety best suited for sandy soil and leaves these seeds in their natural colour.
“As the drill goes up the hill, we see how the prescription map tells the controller to gradually change the variety,” he said.
“We make a gradual transition from red seeds to green seeds and then from green seeds to natural colour seeds. On a third-mile run on my farm, I’ll see a 25 to 30 foot change in elevation. In that run, the drill will go through the whole programmed range of three varieties as well as different rates.”
He said the software tells the meters how much seed to distribute from each of the three seed compartments, regardless of which direction he drives or where he is in the field.
“Each meter is infinitely variable from zero seeds up to the highest rate you might ever imagine.”
Anderson said it’s not possible to achieve a fast rate change with precise accuracy using gears, hydraulics or chains and sprockets.
“We have no gates to open and close on this system, no time delays and nothing to jam up. We drive each metering flute with its own variable speed electric motor. Each motor responds instantly to inputs from the software. It speeds up, slows down or stops dead, all depending on what the software tells it to do. That’s how we totally turn off each compartment.”
Each electric motor drives a planetary gear reduction with a 50:1 ratio, thus giving the system the torque it needs to turn the meters. The metering flute is attached directly to the output shaft of the planetary and there is only one bearing in each metering unit.
Anderson said his electric motor system is less costly to build and less costly to maintain than a more conventional metering machine with chains and sprockets.
“The motors are extremely sensitive to rpm instructions sent from the prescription map; that is essential,” he said.
“The motors give the flutes an infinitely variable speed that goes from 25 rpm to 150 rpm. That gives us the full range we need for any type of seed or fertilizer. Everything is either stainless steel or polyurethane, so corrosion should not be a problem.”
While most of the ideas, research and development and fabricated components come from Anderson’s factory in South Dakota, he will use outside suppliers if he feels they have a better product.
For example, the electronics that allow operators to control electric motor speed from the cab are built by Agtron in Saskatoon.
“So if a producer has an older seeder from us, all he needs to get the whole variable rate package is simply buy the software and plug it into his Agtron,” Anderson said.
“It’s not a high dollar item. The cost will range from $1,500 to $5,000 depending on which software a producer wants. Each compartment on every drill we sell already has the electric motor hardware, so it’s simply a matter of plugging in the control data.”
Anderson said it doesn’t make sense for producers to consider variable rate fertilizer or variable variety select-a-seed unless they are willing to put together good prescription maps for every field. Understanding and controlling the information is essential.
It’s the prescription map, based on overlay maps that make precision farming workable, he added. Correct, precise information is essential for the map to be of value. Like most producers who take variable rate seriously, Anderson collected field information from as many sources as possible.
Topographical maps charted elevation while the Veris machine charted electrical conductivity of the soil. He did extensive soil testing to identify each soil type, soil pH and organic matter and had high quality infrared photos taken for as many fields as possible.
The data comes together in the shape file, resulting in six or more overlays for each field. The goal is to chart soil productivity potential and problems that limit potential so that Anderson can make the best use of his seed, fertilizer and soil.
When overlays were put together, the lower potential in areas with a known history of tillage and erosion became obvious.
While the poor performance of the eroded areas did not shock Anderson, the salinity spots were a surprise.
“We have saline areas all across the northern Great Plains, all the way through your northern farming areas in Canada,” he said.
“Until we did this mapping, we had never done this kind of extensive soil testing on our farm. I thought we had a lot of high salt spots. That’s what you naturally assume when you see that white crust on the surface. It turned out the salinity was real, but that was the least of my problems. The spots I assumed were saline turned out to have extremely high levels of residual fertilizer. Salinity started the problem. Cropping those areas just made it worse.”
In the zero to 24 inch samples, Anderson had areas with 762 pounds per acre of available nitrate nitrogen. There were 360 lb. of sulfur, 40 parts per million phosphorus and the soluble salts in the worst areas ran from 3.6 to 5.6.
“We had organic matter in the range of 3.3 percent, and that’s not too bad, but it points out that organic matter alone is not the answer. Now that we’re mapping, I can see there’s a reason for those white surface areas. I was going in every year and putting down 80 or 90 lb. of N and I’d only take off maybe 20 lb. N with my combine. Every time I fertilized, I was shooting myself in the foot again.
“Until recently, there was no practical way to deal with these spots. Now we have the technology to control the rate and the type of both the fertilizer and the seed that we put down throughout each field.”
Last spring Anderson set up a 12-row John Deere corn planter for Dwayne Beck at the Dakota Lakes Research Farm east of Pierre, S.D.
“Nobody takes seed spacing more seriously than corn growers,” Anderson said.
“It’s always assumed the only way you can get even seed spacing in the row is with those corn drums. So we took 12 of our electric motor meters and stuck them on Beck’s 12 row corn drill and eliminated the drum.”
He said he achieved better spacing and eliminated the pulling and jerking of chains and sprockets.
Accuracy also increased.
“If you calibrate it for precise 12 inch seed placement, that’s exactly what you get,” he said.
“They were seeding corn in and out of an irrigation circle. The program told the meters the very moment they were in the high productivity irrigated area so the meters put out the prescribed high rate of seed. When they hit the areas without sprinkler, the seed rate cut back to match the expected natural rainfall. Corn seed is expensive seed. This can make a huge dent in the seed bill.”
Anderson said the concept of putting different varieties into different parts of the field is still in its infancy. Corn, soybean and wheat breeders are all working on variety development that will turn this type of seed management into a regular practice.
He said soybeans make a good case study because soybean hybrid that is suited for low, heavy soil will produce a lot of foliage, but will also produce a lot of pods if the moisture is available. When that same hybrid seed is planted in sandy soil in the same field, it still grows a lot of foliage but won’t produce pods because there’s not enough moisture.
“For the sandy areas, you need the hybrid that has been developed for just that soil type,” Anderson said.
“In the last three or four years, we’ve started seeing corn hybrids developed with this idea in mind.”
Target disease
Another case study is wheat that has been developed for disease resistance. These varieties can be planted in lower areas where disease is most likely to thrive while more appropriate varieties can be seeded mid-slope and on the knolls.
He said cereal breeders are already working on wheat varieties that are tailored for different soil types.
“We’re not far from the day when it will be common practice to plant three wheat varieties in the same field in order to take maximum advantage of the soil productivity potential,” he said.
“We’re really at the start of this whole change. Right now, we know for sure that certain crop varieties will fail on certain soil types. So it’s simple. We program the software so we do not put down that certain combination of seed and soil.”
For more information, phone Anderson at 605-298-5663 or visit www.horschanderson.com.