HAVANA, N.D. – The typical V formation of a big snowplow or the bow of a boat is designed to disperse the wave of material outward. The pinch point on press drills is a good example of how the tight, leading edge of the V spreads material sideways.
But if the geometry was flip-flopped so the open end was travelling forward and the pinch point was at the back of the V formation, all the material would be thrown into the middle instead.
The idea might not work on a snowplow or boat, but it may have merit on a seed drill.
Read Also
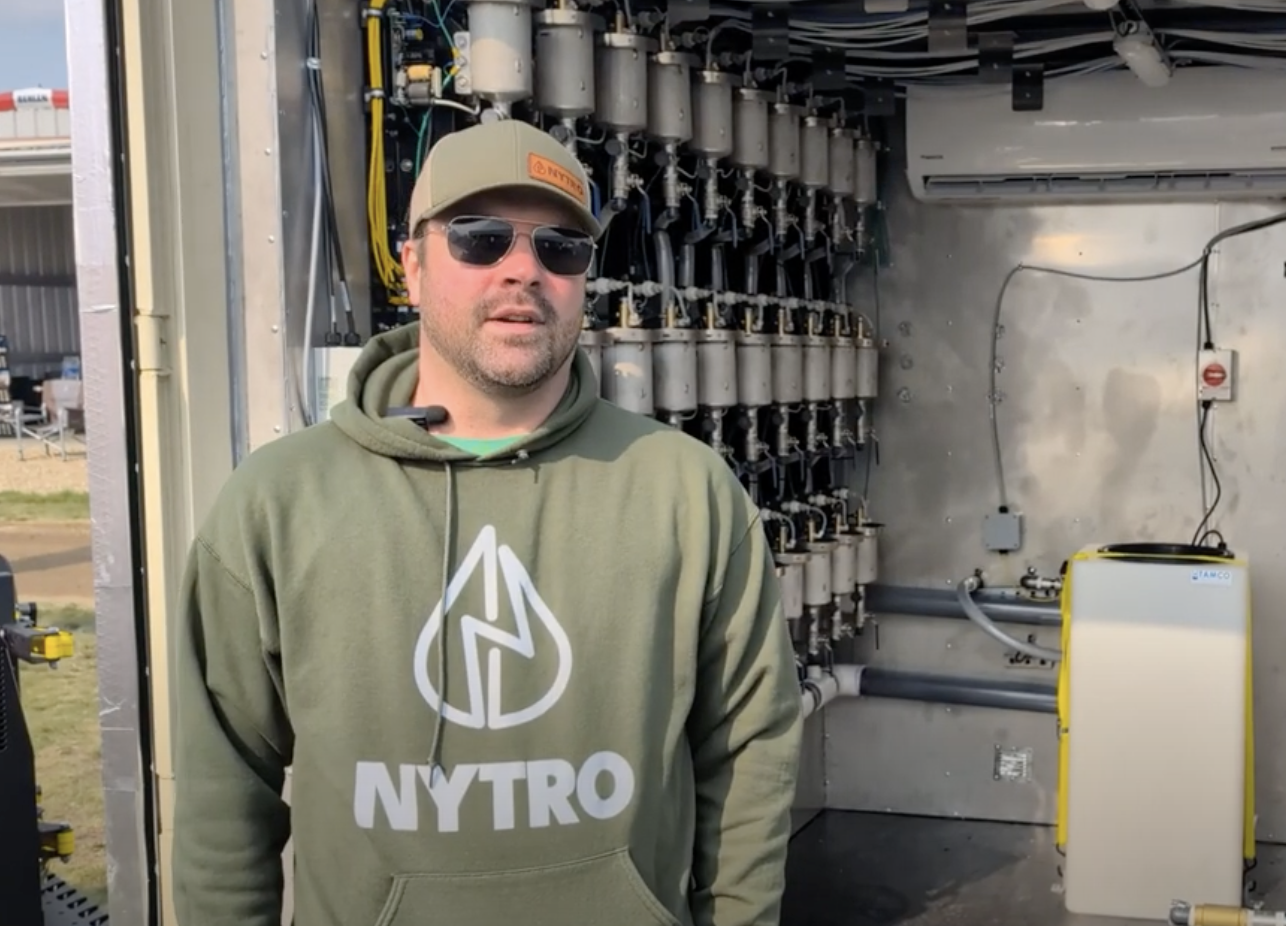
VIDEO: Green Lightning and Nytro Ag win sustainability innovation award
Nytro Ag Corp and Green Lightning recieved an innovation award at Ag in Motion 2025 for the Green Lightning Nitrogen Machine, which converts atmospheric nitrogen into a plant-usable form.
This reversed V geometry, applied to twin disc openers on a paired row air drill, would channel the disturbed soil into a narrow strip at the pinch point just as the soil was leaving the confines of the two discs.
There would be no outward wake of soil and the surface beyond reach of the discs would remain undisturbed.
That’s the concept Fargo Products has been developing for its new Twin Disc air drill. The paired row drill was previewed for a small group at Havana, North Dakota, in July. It will make its first public appearance at the Big Iron Show in Fargo on Sept. 11-13.
Each paired row is created by two opposing discs running at an angle to each other, with the open end of the V facing forward. The exact geometry of these discs was determined by trial and error on prototypes in the field.
As the open end travels forward in the soil, each disc kicks up a wake of disturbed soil and throws it inward toward the opposing disc.
“The two wakes cancel each other out because of the way they face each other at a slight angle,” says Eugene Breker of Fargo Products.
“They roll the disturbed soil into the centre instead of out to the sides. We call it self-cancellation of the wakes. The effect is that you have absolute zero soil disturbance between each set of paired rows.”
In a field just seeded by the drill, the untouched strips between each set of paired rows look much like a city sidewalk. If it was hard, caked soil before the drill pass, it is still hard-caked soil afterward.
Trash clearance is good enough that even standing corn stubble remains intact in the undisturbed strips.
The paired rows are centred on a 15-inch spacing. This leaves a six-inch strip of loose soil, a nine-inch strip of undisturbed soil, then another six-inch strip of loose soil. This pattern repeats itself across the entire 40-foot width of the drill.
“It creates an unusual seed trench,” says Breker. “There’s nothing else like it anywhere. The only disturbed soil is the six inch strip between each disc pair.”
The discs cut straight to the required seeding depth, giving the trench a sharp, well-defined wall. If the machine is set at an inch and a half, that’s how deep the discs will cut. The seed boot on each disc drops the seed along these two freshly cut trench walls.
Because of the pinch point at the rear of the two discs, there is a slight crowned area in the middle of the soil strip. However, once the machine has passed, the field surface is flat and smooth, suitable for spraying and combining.
“Our pinch point is where the discs are the closest, at the back. It’s where the soil is released from the rear of the discs and allowed to flow backwards,” says Breker.
He says the company designed the pinch point to be as close as possible to the level of the soil surface before the drill passes.
The packer wheel follows immediately after the twin discs. The two outer edges of the pneumatic tire are six inches apart, so they pack the soil directly above the two seed rows.
The ribbed tires, which are off-the-shelf items, also serve to catch the flowing soil and smooth it out. The Concord packing tires have a distinct raised rib down the middle.
Fargo Products has not documented the draft requirements, but it did a lot of seeding in the spring of 2007, with five different tractors.
Breker says a mechanical front assist tractor in the 250 to 275 horsepower range easily pulls the 40-foot prototype.
“The tractors ranged from a 255 Magnum to a 480 QuadTrak. The Quad was extreme overkill. The 255 handled it just fine,” he says.
“When we build the 50-foot units, they’ll still work with a mechanical front assist tractor. But when we get up to 60 feet, I think then we’ll be looking at a big four by four tractor.”
Depth control is achieved with basic hydraulics, Breker says.
“Make sure you have enough down force to keep the packer wheels on the ground at the back end of the tool bar. At the front, depth control is adjusted by the height of the frame. You just raise or lower the frame hydraulically to adjust opener depth.
“It’s a little like the old Concords. It’s got four stops and we run maximum depth at each stop. The tool bar just floats. It’s beautiful at shallow depths for things like canola. And it’s quick to change from shallow to deep if you’re going from something like canola over to peas.”
On the prototype machine, Breker used a simple air delivery system to drop granular nitrogen into the six inch disturbed strip between each pair of discs.
“There was no need for an opener of any kind. We just dropped the fertilizer in there and let the soil movement incorporate it into that six-inch zone. Then the packer wheel comes along and presses it in.
“The tire has a centre rib that does a really nice job of pressing the middle of the disturbed strip. You could do that with liquid or granular. It’s not at all complicated.
“But for the wheat guys and the canola guys, we need to have a way to apply all types of nitrogen fertilizer – liquid, dry and anhydrous. So we designed the frame to have lots of space for mid-row banders between the paired six inch rows. This will be a single disc running right down the middle of that nine inch strip of undisturbed soil.”
He says the mid-row band will feed nitrogen to the seed rows four and a half inches to each side.
The replaceable tool bar is another unique feature. Using the universal Bobcat QuickTach system, the operator can easily remove the twin disc floating tool bar and install a different one at the back. All options will be discs because shanks likely create too much side load.
“We want to make the frame as versatile as possible so guys can use it for wheat, canola, row crops, different row spacing or a corn planter. We plan a lot of tool bar options for different cropping situations,” Breker says.
“The other factor is that the Twin Disc is less complicated and has fewer parts than other disc drills. Consequently, it costs less to manufacture. The implicit understanding here is that if it costs less to manufacture, it’s more affordable to buy.”
Fargo Products already has other double disc drills and hoe drills on the market, so why would it develop another seeding implement?
Says Breker: “It’s actually simple. We recognized the shortcoming of the other drill designs in terms of hairpinning and their inability to accurately place seed in a variety of tillage conditions.
“For the most part, the drills that farmers can buy today are strictly no-till machines. They do not seed very well in a conventional tillage situation. This drill seeds comfortably in all conditions.”
Breker says it’s a “one or the other” situation. The no-till drills are not suitable if a farmer needs to cultivate to dry out wet soil or manage excessive residue.
“We’ve got two years of prototyping and fine tuning, and we’ve got the system working well for North American soils and North American residue levels. The original unit is in Australia, and it now has eight seasons on it, with good results.”
The concept of putting the pinch point at the back of two opposing discs originated with an Australian farmer about eight years ago.
“As you find so often in this industry, a farmer has an idea for a better implement. This fellow has heavy soil and the shank drills just weren’t working for him. He needed something for no-tilling on heavy soils, and this is what he came up with.”
Breker says Fargo has signed an agreement, with the inventor holding worldwide patents on the design and Fargo Products holding worldwide manufacturing and marketing rights.
Fargo Products is building the first 10 Twin Disc drills, all 40-foot units, which will be available this fall. Next year, it plans to add 30-foot and 50-foot machines to the lineup.
Breker says that once Fargo moves up to a 60-foot unit, it will need a new frame design, so those larger drills may be a year or two away. No prices have been established.
Last week, Amity Technology bought the entire line of air seeding equipment from Fargo Products. Amity is another Fargo-based manufacturing company specializing in seeding and tillage equipment.
The agreement with Amity includes continued production of the full line of Fargo Products machines, including the new Twin Disc air drill.
For more information, contact Eugene Breker at 701-235-0124.