ROULEAU, Sask. – Heavy clay can be a challenge to farm. Even for sprayers, getting the power down to slick, greasy soil can be tough while also keeping ruts out of direct seeded fields.
“Because we farm so close to the Moose Jaw creek, we need a mechanical drive sprayer, with lots of tires under it,” said Daryl Tiessen.
“When you make a set of ruts every 100 feet, you’ve got them for several years, because we don’t do any tillage to fill them in.
“There’s an advantage to putting duals on and not rutting everything up, especially in lentil fields. If you rut it up and then have to scrape the ground at harvest time, you’re bringing dirt in all the time.”
Read Also
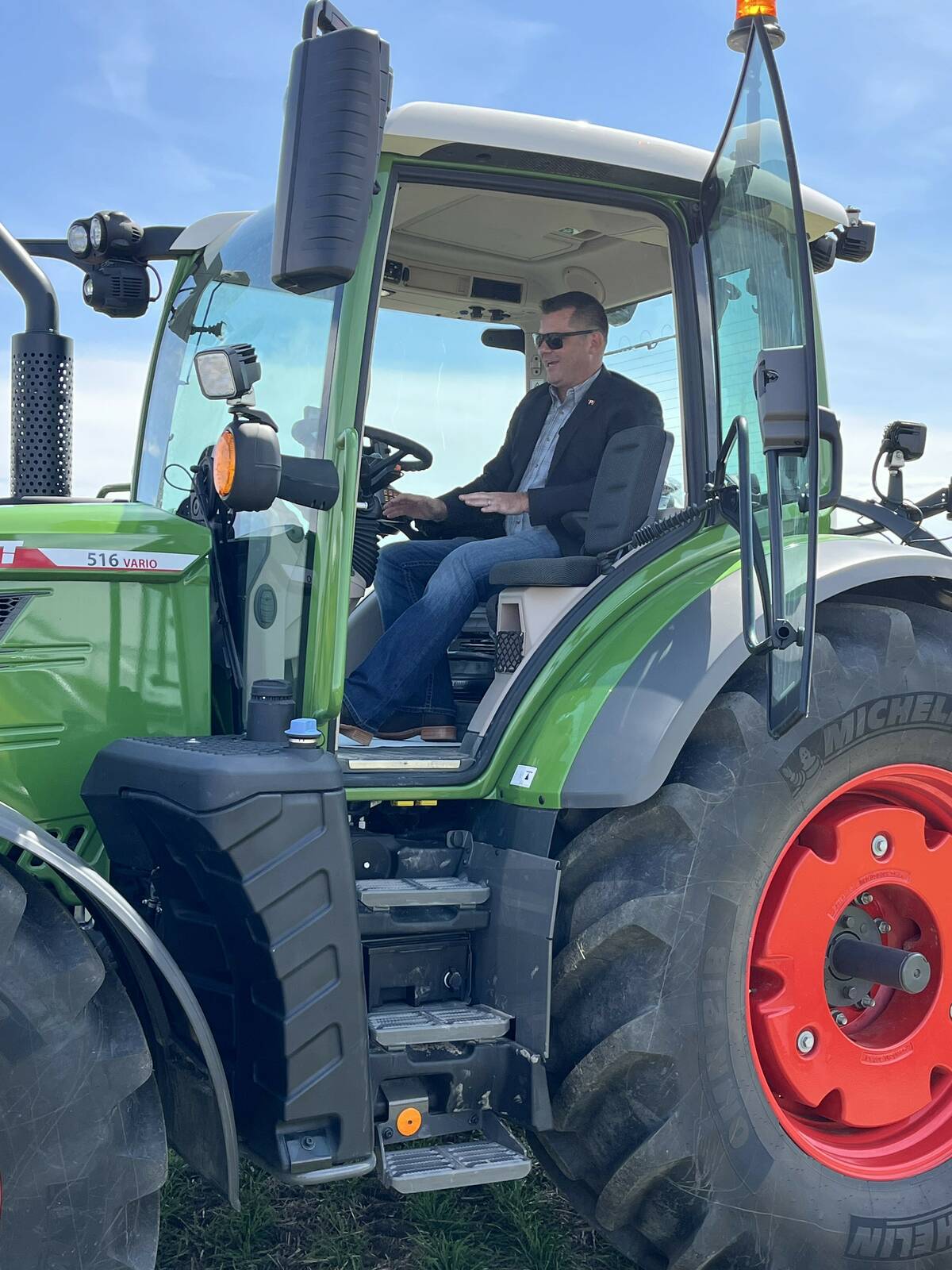
Farming Smarter receives financial boost from Alberta government for potato research
Farming Smarter near Lethbridge got a boost to its research equipment, thanks to the Alberta government’s increase in funding for research associations.
A few years ago, Tiessen bought a 1986 highway tractor at an auction and spent the winter converting it into a sprayer.
The original engine was a 466 International. Tiessen added an intercooler to boost it up to 240 horsepower from 215 hp.
“It was short of power and rather than put more fuel to it, I thought I might as well do it properly,” said Tiessen, who farms near Rouleau.
“We had some wet years and that’s when I noticed the lack of power the most. We ended up putting duals on it just to get flotation for the soft conditions. It was that or pay someone to custom or air spray it, and it made a huge difference.”
The original rear axle gear ratios didn’t work. To provide the sprayer with enough torque, Tiessen spent some time at salvage yards.
“Most tractors have a ratio that’s too low, so it would limit the speed to maybe 25 mph. We found a couple of Steiger tractors at a wrecker that had faster speeds in them, and they’ve worked out well,” he said.
The front axle from the highway tractor was removed and rebuilt.
“The only things original on the front axle are the springs. Everything else we fabricated ourselves. We had to have enough clearance and that didn’t happen with the original dropped axle, so we built an axle out of 3/8 wall, four by six tubing,” he said.
“I had previously built a Hy-Trux type sprayer, with four wheels driving. We copied some of the steering geometry, including the kingpin system. The front spindles are from a 914 combine, so they’re heavy.”
The original front axle dropped about four inches and this one is raised about eight.
“There’s 32 inches of clearance under the front axle. Had we put the same tires on with the original front axle, there would have been 12 inches less clearance in the front.”
For the first while, Tiessen stayed with mechanical steering, but the sprayer was more than the system could handle.
“It overheated the steering fluid, so I put an automatic transmission cooler on the power steering, but it was still heavy steering,” he said.
“I wanted to put autosteering on it, so a few years later, Combine Salvage had a deal where you could put as much stuff as you wanted in the back of a half-ton for $300. We got the steering motor, box and rams off an N7 Gleaner, so we could steer it hydraulically.”
The front wheels on the sprayer are 18.4 x 26, with the rear wheels 18.4 x 42. Tiessen said the wheels could be a bit narrower.
“A friend who built a sprayer at the same time ended up getting 14.9 x 46 tires off an old Willmar. They weren’t any taller so they didn’t give him any more road speed. And with a 90 foot boom (vs. Tiessen’s 100 foot boom), I did the math and we trample the same number of feet per quarter.”
Tiessen used the original 13 speed transmission for a few years, but top end was only about 32 mph and he wanted more road speed.
“I put in a Road Ranger 13 speed with an overdrive. What that did, more than being able to go faster, with the thumb switch on the shifter I can switch from direct to overdrive in the field,” he said.
“I do that often, turning on the corners. I hit the thumb switch and it drops about two mph, you make the corner, then hit the thumb switch again so you don’t have to shift.”
The sprayer, with a 1,000 US gallon tank and a 100 foot boom, can cover a half section in 90 minutes.
“I usually run the full rpm of 2,700 rpm. It goes 15.8, to 17.5, to 20, then 23. You don’t have to go that fast, but I typically spray in that 17.5 mph gear. But at spraying time, it’s usually pretty soft and I’d end up having power issues,” he said.
“When we desiccate or do fall spraying, I’ll spray at 23 or 25 mph. Once the ground firms up, it makes a huge difference in this country.”
The truck originally had air brakes, but the Steiger brake disc had a hydraulic caliper.
“We put the master cylinder off the Steiger under the frame, then attached an air pot to the plunger on the master cylinder where the pedal used to be, then used the air treadle that was already in the highway tractor. That took a little bit of thinking to get it to work,” he said.
The spray tank was bought new from an injection moulding company. Tiessen built the saddle for the tank himself. The boom was originally a front mount unit off a Walker 44 high clearance sprayer. It was modified to fit on the back of Tiessen’s sprayer.
The centre section was originally too wide, plus the hinges and breakaways folded the wrong way, so changes were made to accommodate the rear mount. Tiessen built the parallel link lift and lower system out of four by four square tubing, to attach the boom to the rear of the tank frame.
To provide hydraulics for the product pump and boom controls, Tiessen had a shaft machined that bolts onto the harmonic balancer on the engine. That shaft turns a pulley that belt drives a 28 gallons per minute gear pump.
“Because it’s just a straight gear pump, you have to have the rpm up to meet your requirements, which is no problem when going down the field. But where you notice it is when you have a problem, you let off the gas and try to lift the boom, you’ve lost your hydraulic flow. A pressure compensated pump would be better,” he said.
Because of the belt drive, he said it’s essential to have a pump that has a bearing on the input shaft.
Tiessen originally controlled the boom with a set of hydraulic spools from a MF 1500 tractor. He has since replaced that with a bank of electric solenoids, which improved the function of everything. He’s no longer pulling levers and it’s handier with the toggle switches.
“There were five functions, so originally there were 10 hoses going from the cab back to the boom sections. When we switched to the electric, we only needed two hoses going back, so it tidied things up. And you can custom tailor it to do exactly as you want,” he said.
Tiessen likes the cleanness of the Walker boom.
“They call it a mono boom as opposed to a truss style. The accumulators take a lot of the snap and whip out of the boom if you hit a hole, so it hasn’t ever failed. And we spray a minimum of 15,000 acres a year.”
The boom can spray from 28 inches to about seven feet off the ground, though Tiessen typically sprays at 36 to 40 inches. All the plumbing is two inch, with a standard, off the shelf, hydraulically driven Hypro pump.
Under the hood, beside the steering shaft, Tiessen mounted two hydraulic flow controls.
“One is for the autosteer – how aggressively you want it to steer. The other one splits hydraulic flow between the product pump and the boom,” he said.
“If you want more flow from the product pump, then the boom lift gets slower. But you don’t want to drive the product pump too fast. It took a while, but I’ve got it to where I hardly ever move it now.”
In the cab, there’s a spool for engaging and disengaging the hydraulic pump, but there was another spool on it as a spare. So Tiessen added two
Pioneer couplers to it and now can use the sprayer truck as a hydraulic power pack.
While the steering system is hydraulic, Tiessen set it up to operate independently from the large hydraulic system. He replaced the original power steering pump with a gear pump that had more capacity, to around seven gpm.
Both pumps use the same hydraulic fluid reservoir, so if the boom-pump hydraulic system has problems, he can still steer the unit to get it home.
The 25 gallon reservoir includes an oil cooler mounted between the cab and the spray tank.
“I don’t use the cooler all the time. When it gets hot, I’ll turn it on. But in the fall if you’re spraying it doesn’t seem to bother it. It runs through the cooler all the time, but I only engage the fan when it’s hot.”
Tiessen bought two new blank rims from Unverferth for the rear axle. He had Precision Metals in Regina laser cut the centres, which he then welded into the rims.
“The rear bolt pattern is an odd thing and had to be specific to fit the planetary we’re using on the Steiger rear end,” said Tiessen.
“Then I decided after I got them cut that there wasn’t enough offset to clear the tank, so I added a piece of five inch heavy wall pipe and had Precision cut another smaller piece of steel with the right bolt pattern in it. That gave me enough offset to clear the tank.”
The front wheels are from an 852 MF pull-type combine. The bolt pattern on the rims fit the hubs from the 914 International pull-type combine that Tiessen used when building the front axle.
He estimated he spent $27,000 on the sprayer, not counting his time. If he was to do it again he would try to find a truck that had factory air conditioning in it.