LOUISVILLE, Ky. – North American farmers bought 13,000 combines in 1998. Last year they bought only 8,400.
“The drop in combine numbers does not correspond to the drop in farm numbers,” says Jeff Gray of Lexion Claas Omaha Inc.
“Combine sales are dropping off at a faster rate than total farm numbers. There’s a number of factors: drought, commodity prices and industry adjustments in the late ’90s. But combine size is also a major factor. Each combine sold today does more work. You simply don’t need as many.”
Read Also
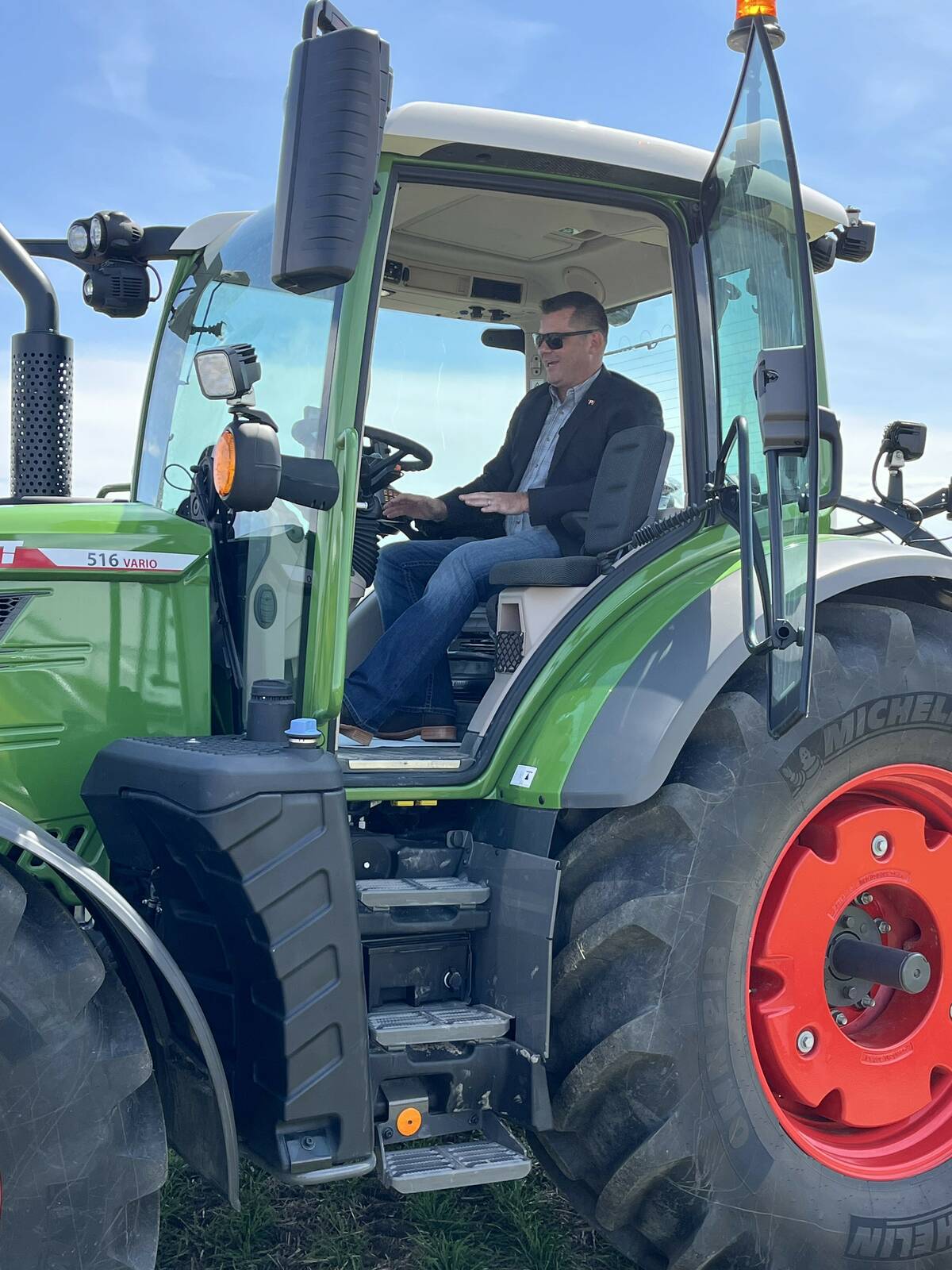
Farming Smarter receives financial boost from Alberta government for potato research
Farming Smarter near Lethbridge got a boost to its research equipment, thanks to the Alberta government’s increase in funding for research associations.
At the recent International Conference on Crop Harvesting, Gray said the Class 4 combine has become extinct. The Class 5 combine, with only 900 sales per year, is on the endangered species list and is expected to move to the extinct list soon.
“By the late ’90s there were already combines doing 4,000 bushels per hour in corn. When we went to the Class 9 combine, we enhanced our clean grain handling system to allow it to breathe better. It’s now rated at 6,000 bushels per hour in corn.”
But is 6,000 bu. per hour realistic?
“No, it’s not,” Gray said. “But many operators say they regularly do up to 5,500 bu. in good harvest conditions.”
Most producers would feel it’s a major accomplishment if one big combine could replace two smaller sized units because it would cut labour requirements, fuel costs and investment.
But what about one big combine replacing three smaller units? Gray said it’s possible in rare situations.
“We have one customer who has managed to do that in his corn, but not his other crops. He had been running three Class 6 combines with eight-row corn heads. He replaced those with a single Class 9 with a 16-row head.
“The reason it worked out so well was the increased fuel efficiency and manpower efficiency. He said his tractor drivers were no longer pulling the grain carts all around the field, chasing three combines, trying to figure out which one would dump next.
“He no longer had one or two full combines sitting idle waiting for their carts. For him, it was just the right combine capacity to keep his trucks and carts rotating on an even schedule. Nobody was sitting idle anymore.”
Gray said bigger combines can also reduce the number of operators in the field.
“A few farmers take some of the money they’re saving by signing fewer paycheques and they use it to pay a better salary to the smaller number of more highly qualified operators. Those extra few dollars can go a long way toward paying the operator you really want running your combine.”
But a bigger combine doesn’t necessarily become a better combine.
“The sheer size and weight of a bigger machine, along with the weight of more grain in the tank, creates some very real limitations. I’d say we’ve probably reached a plateau for now.
“If we do get bigger, we’ve got to maintain some sort of practicality. It has to be cost-efficient for the customer and it has to be efficient in the field.
“But you never know what will happen down the road. Twenty years ago, who could have possibly guessed we’d have combines like the Class 8 and 9 we have today.”
Increasing power requirements are one major factor to consider, Gray said. At the current state of combine technology, more power is needed nearly every year for multi-task chopping heads, faster unload augers, higher ground speeds, bigger straw choppers and spreaders and other emerging electrical and hydraulic features.
If a larger combine is on the drawing board, more power will be needed because larger combines will be heavier. As well, more weight amplifies the nagging question of soil compaction.
A larger combine would likely require a major breakthrough in the use of lightweight materials.
“We would see some alloys and aluminum, but we would need to employ materials that are stronger, lighter and cheaper than steel. I think we will definitely see a spillover effect from the automotive industry when it comes to lightweight materials.
“We’re already starting to see some of this in the ag machinery industry. We’re using alternate materials for sheet metal panels, for instance. All of this will eventually serve to increase our payload.”
For more information, contact Jeff Gray at 402-861-1107 or e-mail Jeff.Gray@claas.com.