Biggar, Sask. – Richard Elenko uses a four-compartment trailer with a conveyor system as the main feeder for one air drill and he has another seed and fertilizer tender for his second air drill.
He modified a tandem truck, dividing the box into three compartments and adding three remote end gate chute controls and a swiveling 10-inch auger.
Like the trailer system, controls are available at ground level and at the top of the auger. The system can fill all three tanks in the air seeder cart from one position.
Read Also
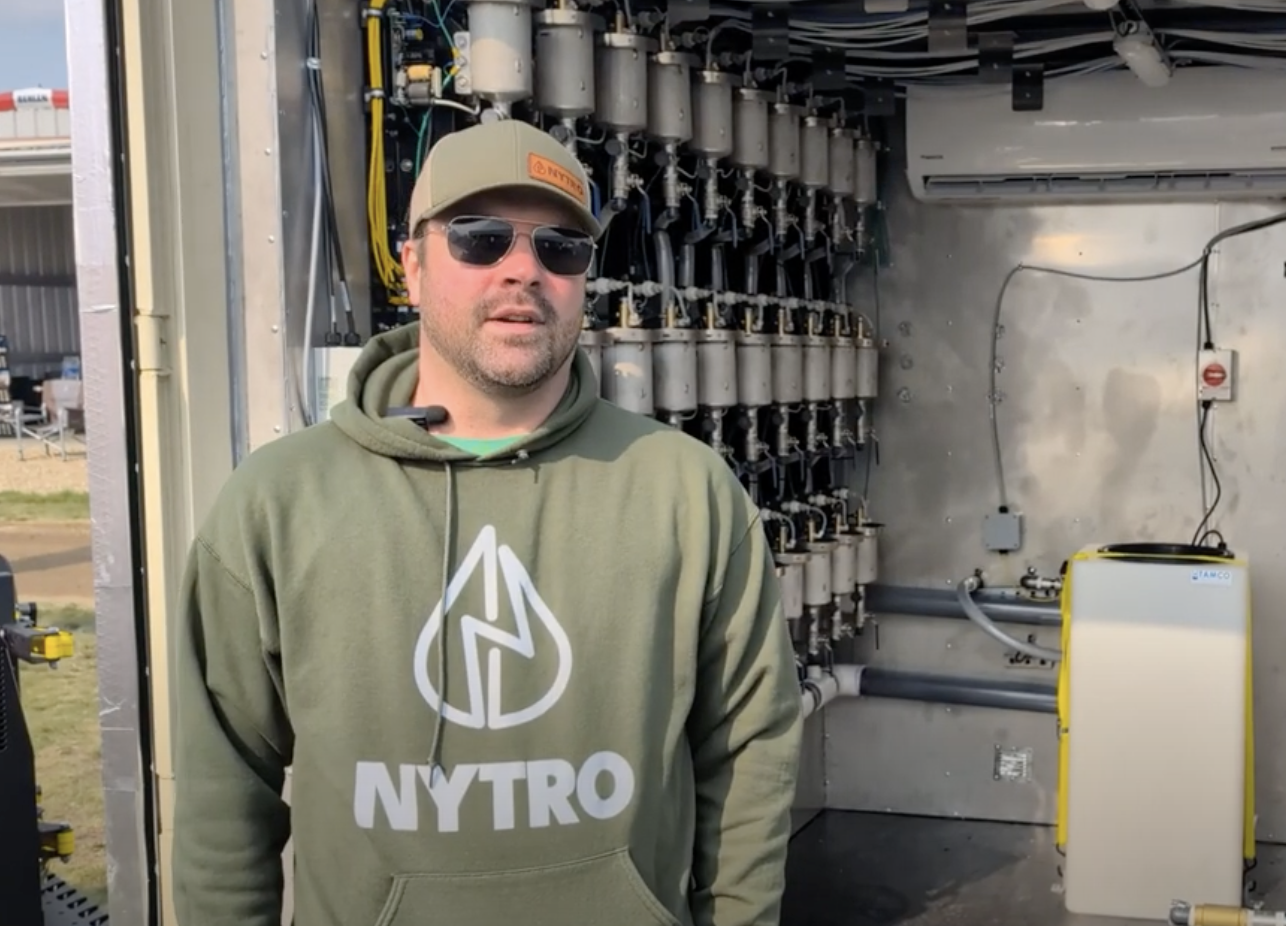
VIDEO: Green Lightning and Nytro Ag win sustainability innovation award
Nytro Ag Corp and Green Lightning recieved an innovation award at Ag in Motion 2025 for the Green Lightning Nitrogen Machine, which converts atmospheric nitrogen into a plant-usable form.
Elenko said like the trailer system, the tandem box is split into compartments that are the same ratio as the tanks in the air seeder cart.
The small one carries phosphorus, the middle carries seed and the largest compartment holds his nitrogen blend.
He can get almost two fills from the box, which holds 800 bushels and is 20 feet long with 70 inch sides.
“When filling your air drill, all three chutes on the end gate are controlled from the top with electric over hydraulic controls. And on that truck, we have controls for the hoist on the top, as well. So when you’re on top of your seeder, you never have to get off.”
Elenko originally located the auger transport position along the side of the box, thinking it would be out of the way and easier to fill each compartment properly.
“That turned out to be a red herring. It’s better to run it in the middle. The mechanism design to fold it to the side, it’s a bit tricky for the operator to fold it in and get it to rest in the cradle. To fold it in the middle, you just bring it to the centre, fold it up and lower it.”
This year he plans to install an electric tarp on the truck and modify the auger so it will fold up and lay in the middle of the box.
The trailer has one large pump for all the hydraulic functions, but the tandem has two hydraulic pumps.
“If you run it off one pump and you’re lifting your hoist, it’s tricky to set your bypass, otherwise you’re starving one circuit and your auger stops,” he said. “We have one pump that runs the hydraulic hoist, so there’s no impact on the hydraulic controls. The hoist pump is a conventional one, about 15 gpm. The other one is about 30 gpm, to err on the larger size.”
Before harvest, Elenko removed the auger from the back of the box, but left the dividers in to see if they would affect loading. It wasn’t a big problem and he doesn’t plan to take them out for the next harvest.
“There’s a little bit of an issue when you unload. The front hopper tends to hang up a little bit. We have a 45 degree angle on the top hopper and we’re going to round those corners so it doesn’t bridge and then come rushing down on you.”
Elenko based his truck design around the fact that he seeds with two separate drills and typically is seeding different crops at the same time.
“I want to get my peas in early and my canola in early. My eight inch spacing (drill) works better for peas than the 9.8 inch (drill). I like to get my peas closer. As a result we’re doing two different crops at the same time.”
When seeding wheat or canola with the big unit, he puts the trailer on the pea unit and uses the belt conveyor.
When Elenko seeds the same crop with both drills, he will often use the tandem to supply the conveyor trailer.
“We use that as a tender unit a lot. We can jump in the tandem, go to the bins, fill up, we’ve got no augers and we can top up my big trailer. We can load it in the morning and our spray operator or whoever is free can top up the trailer at his convenience after lunch, if the wind comes up and he can’t spray. It’s a handy unit.”