OAK BLUFF, Man. – Biological growth promoters are nothing more than highly trained, naturally occurring soil microbes.
How these commercialized bacteria boost crop yields more than their wild cousins that live naturally in the soil is a process that has remained largely behind the curtain.
BioBoost is one such commercial product. It is classified as a plant growth promoting rhizobacteria but is not a fertilizer or conventional fungi type inoculant.
Rather, it is a true soil-borne microbe. Or as they say at Brett Young Seeds, “it’s a bug.”
Read Also
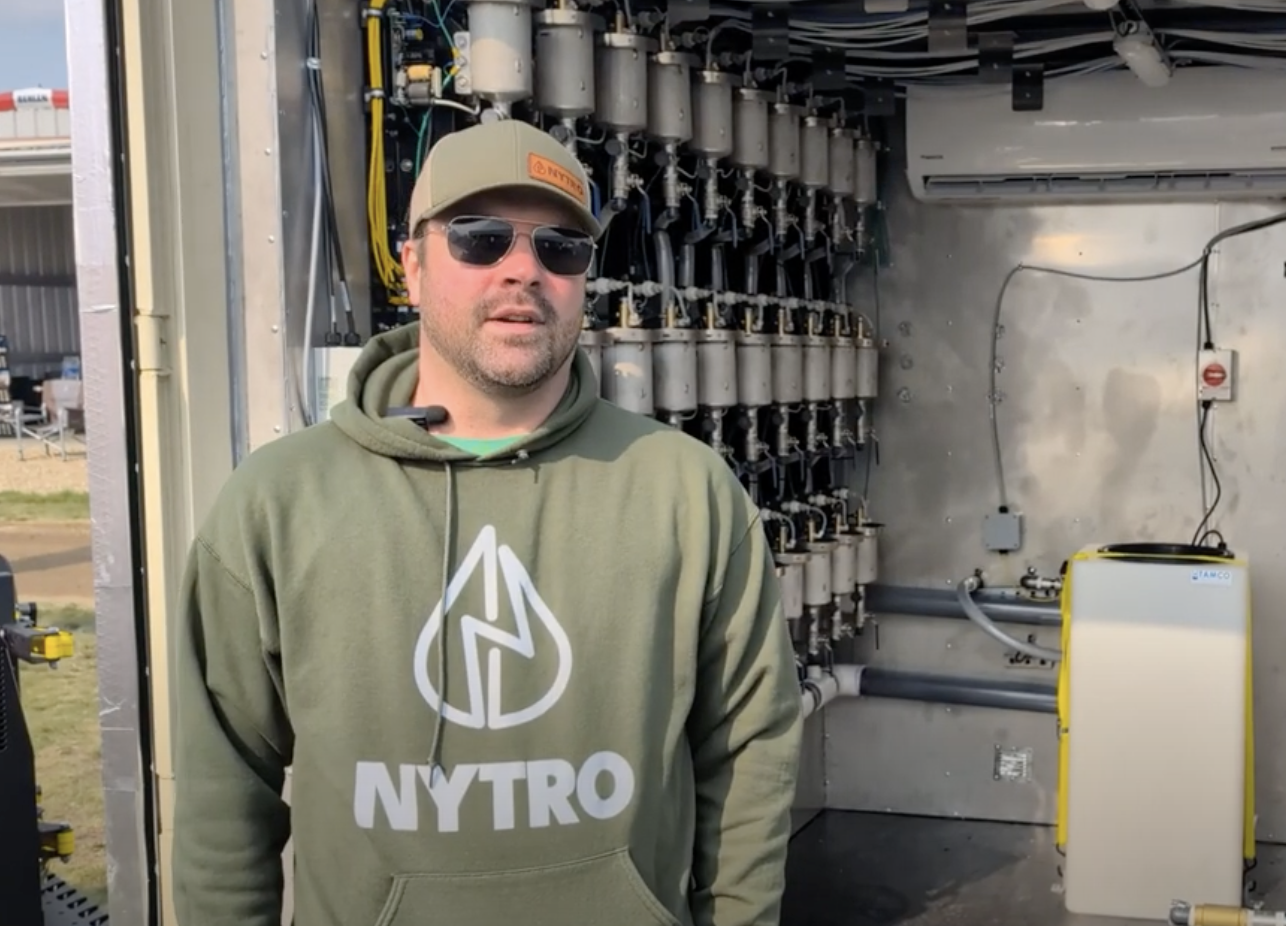
VIDEO: Green Lightning and Nytro Ag win sustainability innovation award
Nytro Ag Corp and Green Lightning recieved an innovation award at Ag in Motion 2025 for the Green Lightning Nitrogen Machine, which converts atmospheric nitrogen into a plant-usable form.
But it’s not a bug that can be caught with a sweep net. Like all bacteria, it’s small and difficult to work with.
The challenge for microbiologists is knowing how to capture, identify, test and tame the soil microbes they find in nature.
If they hit their target, they can offer farmers an environmentally friendly product that increases yield by giving roots better access to nutrients.
“As microbiologists, we must find an isolate in the soil that has a positive impact on plant growth,” said Manas Banerjee, head of research at Brett Young in Oak Bluff, which manufactures BioBoost.
“We must find it, isolate it from other bacteria, extract it, test it and reproduce it in small quantities in the lab. We must also be able to reproduce it in large volumes, then go through the registration process, plus make sure it lives long enough to do its work in the farmer’s field. If it doesn’t survive, it has no value.”
Sorting through the millions of microscopic bacteria found in prairie soils in search of one that’s worth pursuing is a bit like looking for the proverbial needle in the haystack.
Banerjee began that search in 2000 when he joined Brett Young specifically to investigate the possibility of a biological growth promoting agent for canola.
To accommodate this unique line of research, Brett Young built a state-of-the-art microbiology lab to house the project.
Microbiologist Laila Yesmin, who runs the facility with Banerjee, said the process starts with clean water because contamination is the biggest enemy in a microbiology lab.
The lab’s filtration system reduces water to nothing more than two parts hydrogen bound to one part oxygen, also known as H2O. It’s the closest thing to pure water, containing no minerals or living organisms to throw off test results.
Inside the Oak Bluff lab is an appliance that closely resembles a domestic clothes dryer. In fact, the Stovall RC 5C Plus centrifuge is similar, except that it spins at 20,000 r.p.m. instead of 200. The high-speed spin is necessary to extract bacteria from solutions.
For a commercialized bacterial product to receive federal registration, it must meet strict Canadian Food Inspection Agency standards for a variety of factors, including population count. A low count indicates that the strain is not hardy enough to proceed to the registration stage.
Another lab tool steps up to help. The Leica Colony Counter ensures that weak bacteria are culled before they have a chance to enter the breeding program.
Precision is mandatory in all microbiology lab work.
Measuring what researchers have and don’t have in the lab is critical. Sartorius digital scales are delicate enough that air movement in the room distorts readings. For that reason, they are fitted with an airtight glass shield so people moving around at the other end of the lab don’t affect the readings.
Once a promising bug has been identified, it is frozen at -86 C until needed again, sometimes years later.
Called an -86 ULT, it looks like a domestic chest freezer but it is much colder. It shakes the flasks of bacterial liquid, which keeps the bacteria in contact with air.
One of the most important tools in a microbiology lab is the fermentation tank. At Brett Young, the Biostat Cplus is designed to multiply bacterial cultures 30 litres at a time. Only the most promising microbes make it this far.
The $100,000 stainless steel device comes with its own steam generator that is plumbed into every component of the tank. It automatically sterilizes itself before and after each batch.
The few bugs that pass this intensive scrutiny go to the next stage of elimination, the growth room. This stage is more like real life.
In those final steps, researchers also test for reproductive capability.
An outstanding strain of bacteria has no commercial value to Brett Young if it cannot be reproduced with absolute identical traits. If it doesn’t meet the propagation criteria, it goes to the trash before it ever sees field tests.
Banerjee said this step-by-step selection process moves from the lab to the growth room to the greenhouse to the company’s 600-acre research farm and finally to field tests across the prairie provinces, North Dakota and Minnesota.
To speed up the process and to make sure no flukes enter the data, some of the work is contracted out to private research firms, Canadian universities, eight U.S. universities and European partners.
This is the in-house proving ground that will determine whether all the work will have a hope of paying off on the farm.
Banerjee said the potential benefit to prairie agriculture prompted the Manitoba Rural Adaptation Council to contribute $130,000 to the Brett Young lab project.
He said that without this fully equipped lab, commercialization work that has taken five years would have taken 10.
The facility allows Banerjee’s team of 10 researchers and technicians to efficiently concentrate their efforts on extracting bacteria from soil specimens and putting them through intensive tests to screen out the duds and foster those with potential.
Microbe communities are different from one soil zone to the next, from one depth to the next and within short distances of one another. So the first question for scientists was where to dig.
The researchers knew their first target crop was canola, so canola fields were the logical place to start.
“We started with thousands upon thousands of different soil bacteria, all from the prairie parkland region because that’s where most of the canola is grown,” Banerjee said.
“In the screening process, we went from thousands of individual bacteria, down to hundreds, then to dozens. First they get tested on canola for visual enhancement of the plant. We grow a canola plant and examine the roots. We study the different soil bacteria associated with roots of the healthiest plants. If one bug looks good, then we take the next step and test for yield benefits.”
Banerjee said the first principle laid down when Brett Young embarked on the biological initiative was that the final product must be farmer friendly.
“If it’s an extra task at seeding time, then it might not happen. It must fit the normal farm management system without adding more work,” he said.
“And to make it commercially viable, the product has to work beyond the lab. It has to work in farmers’ fields consistently, year after year, always the same. That means we have to keep the bugs alive until they get into the soil where they thrive.”
Yesmin said the only method they have found is to house and transport the living BioBoost microbes in flat plastic bags that lay horizontally.
The microbes don’t survive in a conventional upright container because they don’t have enough surface contact with the air.
“In this sense, they are very different from the rhizofungi inoculants used on legumes like beans,” Yesmin said. “These bacteria are more sensitive.”
Banerjee said one of the lab’s next projects is to get rhizofungi and micro bacteria to work together for greater enhancement of plant growth.
“We know the rhizofungi benefit some plants like legumes, and we know the micro bacteria benefit plants like canola,” he said.
“Now, if we can get them both to work together at the same time on the same plant, we should get much better performance. It will be a special new synergy. It will be like one plus one equals three.”
The lab is also exploring other paths.
Banerjee said the soil microbes that have been examined for wheat should be similar to the microbes for corn.
“If our current candidates don’t work out, we’ll dig in another soil zone to find different microbes.”
He said the lab is also looking at combinations of rhizofungi and soil microbes for soybeans. Canada grows 3.5 million acres of beans and the United States grows another 75 million acres.
“Indiana and Iowa together have 20 million acres of soybeans, but their normal rhizobium inoculants are not working very well. Maybe we can find a bacteria that can work in conjunction with their rhizobium.”
Biopesticides are also high on the priority list for future exploration. Banerjee thinks plant disease will be one of the first targets.
“There should be a natural enemy of root-borne and seed-borne fungi and fusarium. That’s a good possibility. We already have some things we’re looking at in that direction.
“The important thing to remember is that all these products we’re looking at are natural bacteria that we find in the soil, not chemical products.
“If we can help farmers grow healthier crops with less commercial fertilizer and less chemical product for crop protection, then their farms become more environment friendly.”