Interest is growing in turning nuisance flax straw into high-priced fibre, but farmers will have to change their work habits to get the big bucks.
“We have to manage flax straw like it’s a cash crop because that’s what it is,” says Alvin Ulrich, president of Biolin Research in Saskatoon.
“When we view flax straw as a nuisance and burn it, that’s like burning money.”
Flax fibre for paper sells for $400 per tonne. Higher quality flax fibre sells into the industrial market at $600 to $1,200 per tonne, while specialty flax fibre can sell for up to $5,000 per tonne.
Read Also
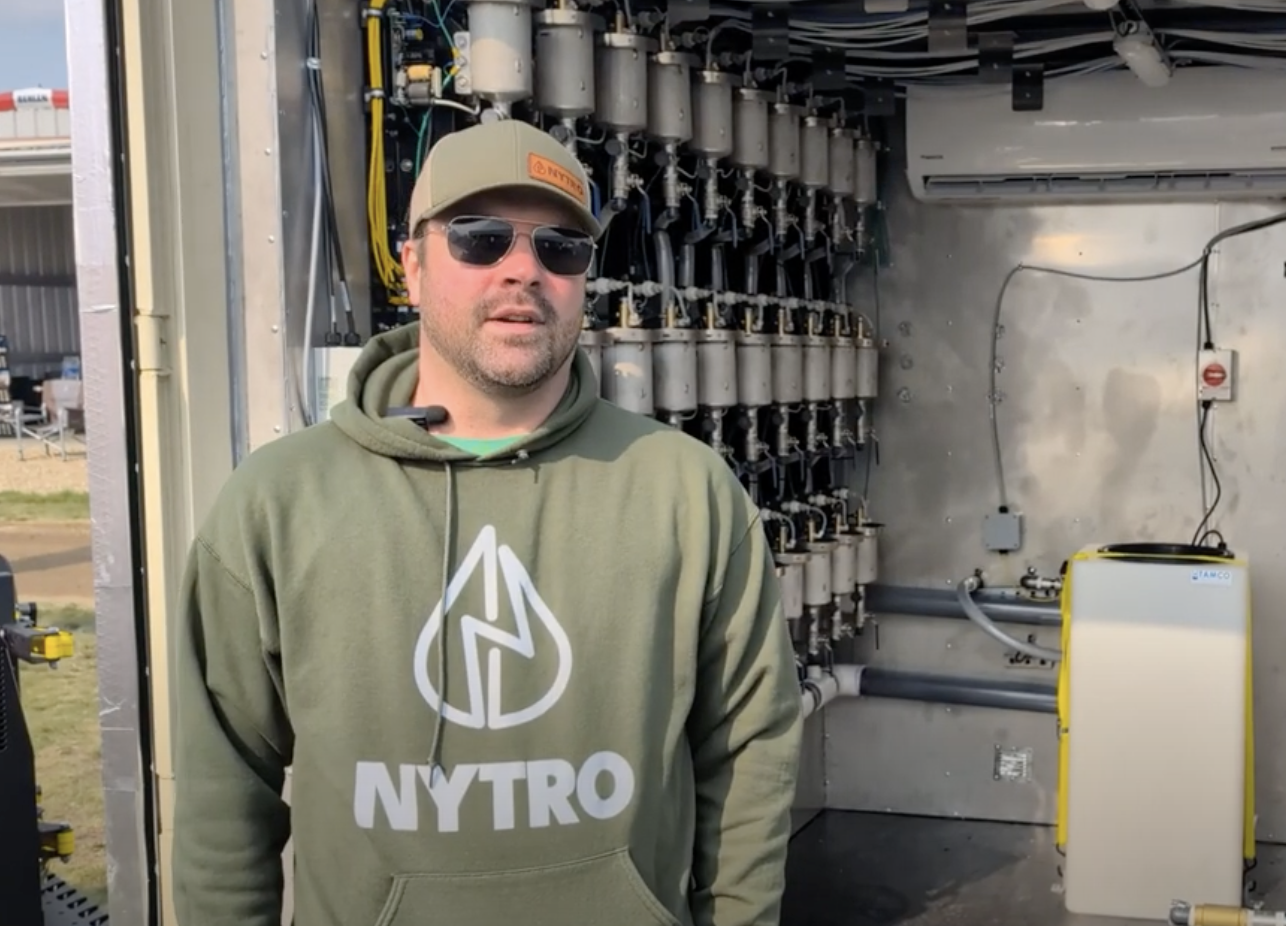
VIDEO: Green Lightning and Nytro Ag win sustainability innovation award
Nytro Ag Corp and Green Lightning recieved an innovation award at Ag in Motion 2025 for the Green Lightning Nitrogen Machine, which converts atmospheric nitrogen into a plant-usable form.
Ulrich said European manufacturers are moving away from glass-based fibreglass and toward flax fibre for making products such as cars, trucks, trains, airplanes and boats. Flax is used wherever weight and strength are important as well as insulation and in textiles.
He said the growing European enthusiasm for flax fibre is fueled by the fact that it’s a renewable product and because of its weight. A product made of flax fibre weighs about half as much as the same item made of conventional fibreglass.
The length and strength of flax fibre must meet high standards to sell into the manufacturing sector, but Ulrich said Canadian farmers don’t have to grow the European high fibre, low oil varieties to get a good price.
“We’ve looked at those fibre varieties and we know they grow well in Western Canada, but the reality is that we grow oilseed varieties here, and that won’t change. So that’s the straw we work with,” he said.
“Our flax produces nice fibre, just not as much of it compared to the special fibre varieties. But if we do a good job of managing our oilseed flax straw in the field, our fibre can fetch prices in the range of $600 to $1,200 per tonne.”
Ulrich said there’s nothing new about the science of managing flax straw to obtain maximum length, strength and utility. The key is to let it start rotting just a little before working with it.
He said the process of preliminary rotting, called retting, happens when soil-borne microbes attach themselves to the straw and begin feeding.
“Over 5,000 years ago, the Egyptians had already come to realize they had better success if their flax straw was partially retted, if the soil microbes were allowed to get into the straw for a while.
“Next they dried it to stop the retting process and then they hit it with a mortar and pestle or hit it over the edge of a table.
“The fibre was strong enough to hang there and the shives would fall out. That gave them a good fibre to work with.”
Ulrich said dealing with flax fibre is the opposite of dealing with fruit, vegetables and grain. With those crops, farmers remove the peelings and throw them away. With flax straw, the peelings are the good part.
“With flax straw, I want the wrapping around the outside. I don’t really care as much about what’s inside. The fibres are in a ring on the outside of the stem, just below the cuticle. The cuticle is that waxy coating on the surface that protects the plant.”
The waxy coating is thicker in a dry summer because the natural tendency is for the plant to protect itself.
The waxy cuticle coating can be too much of a good thing, continuing to protect the straw long after harvest and preventing soil microbes from beginning their retting feast.
If the straw is chopped into short pieces, the soil microbes can easily get at it. However, short straw has no commercial value because the market demands long straw.
Ulrich said the challenge is to keep the straw long but get the soil microbes into their target feeding area.
“You’ve got to think like a soil microbe when you’re managing flax straw to be processed for fibre. Don’t think like a farmer.”
Ulrich said the natural tendency for microbes is to eat straw while the natural tendency for farmers is to preserve straw.
For soil microbes to do their job well, straw should lie flat on the ground in a thin layer. Greater contact between soil and straw allows more microbes to begin feeding.
“Unfortunately, microbes can’t penetrate the waxy cuticle. I suspect that’s one of the reasons flax is always so healthy and free of problems.”
Ulrich said flax straw should be exposed to rain and dew to break down the protective cuticle.
“Ideally, we want a thin layer of straw on the ground with every piece touching the soil so the microbes can climb on board.
“The worst thing for us is chopped straw falling from a rotary combine, dropped in a windrow on top of four inch high stubble. There’s no soil contact, no retting. And besides, we can’t process short pieces anyway.
“Flax straw is notorious for longevity. But that’s not always a good thing. If you pick it up and bale it right away before the retting starts, it will not be suitable for processing into fibre.”
A warm wet fall provides the best environment for retting.
Ultraviolet rays from the sun help break down the cuticle, as does the shrinking and expanding that come with temperature changes.
However, if harvest is late and followed by cold, dry weather, retting might not begin until April, when straw management will interfere with spring seeding.
“Microbes go dormant in the winter. In the spring, some become active at plus two or three degrees. Some need plus 20. Others need plus 30.”
Millions of different kinds of soil microbes have evolved for every combination of plants, soil and weather conditions.
“In every situation, there is a succession of microbes,” Ulrich said.
“We want to rake and bale the straw to stop the retting before the next succession comes along. The next microbe armies are the cellulose eaters. They eat the cellulose and destroy the valuable fibre. Once that happens, you’d might as well burn the straw. But if you rake and bale it at the right stage and then keep it dry, it can wait many years to be processed.”
Harvest schedules and the short period between harvest and the onset of winter are the biggest obstacles to success.
Ulrich said his company has worked out a good straw management system – straight cutting the flaxseed with a stripper header, followed the next day by a mowing operation that leaves the straw evenly distributed in a flat layer on the ground.
“Many farmers seed flax last, often the end of May. That means it’s the last crop to be combined. Even if it’s seeded early and is ready early, flax can stand and wait for a late harvest because it resists pests so well. That works against us. Flax is about 100 days to mature, but regardless of when it’s ready, the other crops always take precedence because they lose grade so easily.
“The result of all this is that flax often waits until October before it’s combined. That doesn’t leave enough time for it to lie on the ground and play host to the microbes. And by October, the temperatures are often too cold for proper retting. So we have a problem.”
Ulrich said his company is considering a plan that would harvest flax early without disrupting farmers’ regular harvest schedule.
“We would arrange for custom combine operators with stripper headers to travel around doing flax fields only. They could start in August when the first fields were ready.
“Next, we’d have a rotary mower crew come along the following day to cut the straw short and leave it on the ground.
“This would guarantee the flax harvest is completed early enough to allow time for retting. It also removes one crop from the farmers’ busy harvest season. Most guys would appreciate that.”
Raking and baling flax straw costs $30 per acre. To make sure this step is done on time, Ulrich said Biolin would pay farmers $60 per acre for those operations.
Biolin operates a small pilot processing facility that separates the shives from the fibre. The shives are easy to remove because they are so brittle.
Although the main product is the fibre, the shives can be sold to the horticultural industry and as livestock bedding. Ulrich said the fibre produced at the facility is flexible.
Western Canada is one of the few places in the world where flax is grown as a food product, he added. About 75 percent is grown in Saskatchewan, 20 percent in Manitoba and five percent in Alberta.
For more information, contact Alvin Ulrich at 306-668-0130 or visit biolin.sasktelwebsite.net/.