ASSINIBOIA, Sask. – With moderate fertilizer rates, Kevin Gronsdahl was able to seed a decent chunk of acres before stopping to fill his air drill. As fertilizer application rates climbed, however, the time between fills dropped. So in the spring of 2003, he and his father Irvine decided to change their seeding setup.
“We were getting to the point where after 30 or 35 acres we’d be running out of fertilizer,” said Kevin Gronsdahl, who farms near Assiniboia, Sask.
“We wanted to get more distance between the fills.”
Read Also
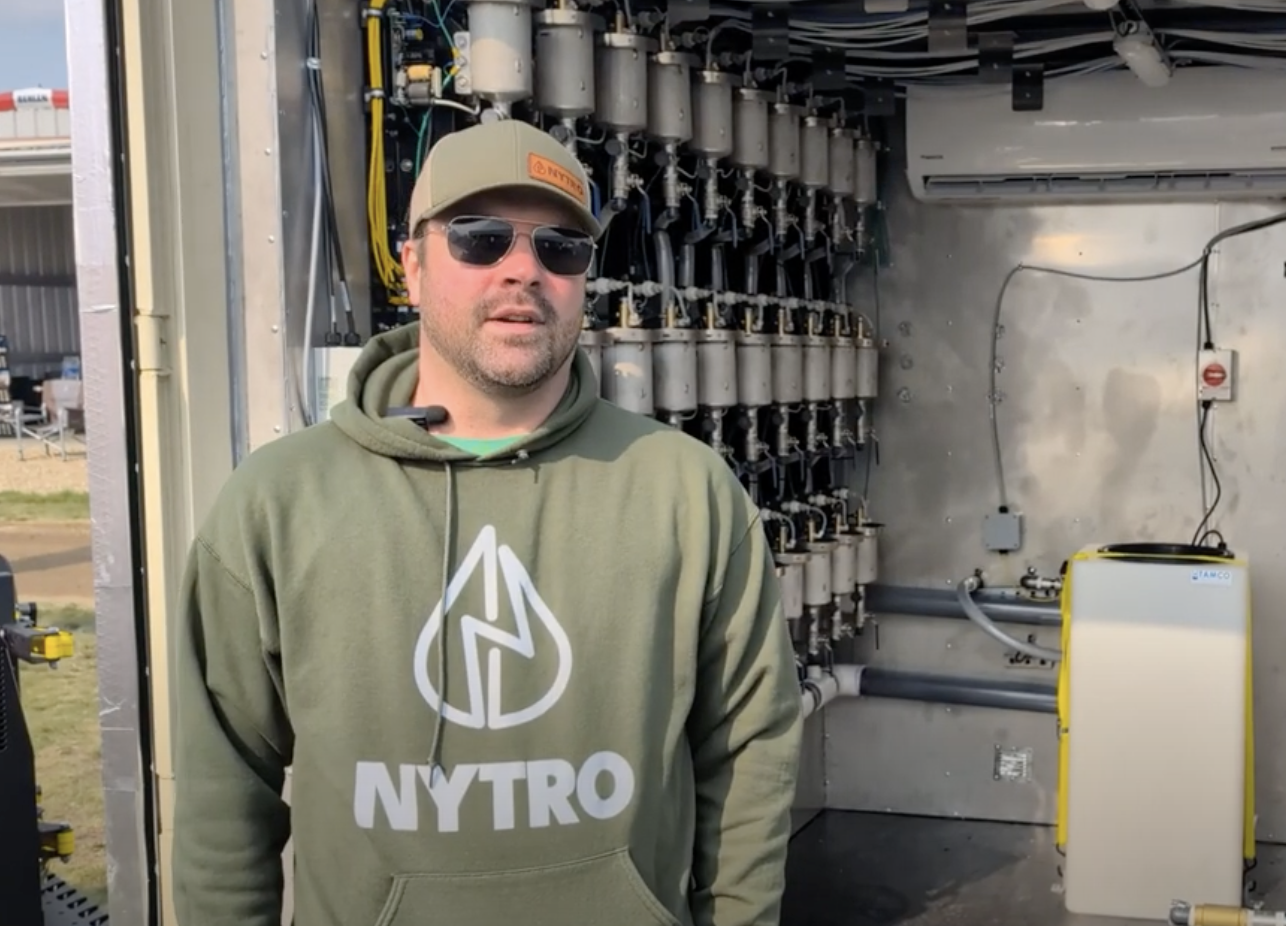
VIDEO: Green Lightning and Nytro Ag win sustainability innovation award
Nytro Ag Corp and Green Lightning recieved an innovation award at Ag in Motion 2025 for the Green Lightning Nitrogen Machine, which converts atmospheric nitrogen into a plant-usable form.
Gronsdahl likes liquid fertilizer because it’s easy to handle. So rather than get rid of his 10-year-old two-tank, 200-bushel Concord 2000 series air cart, he and his father built a frame, mounted a 1,500 Imperial gallon liquid fertilizer tank on the back and put the original seed cart on the front.
“We got the tank from FreeForm Plastics at St. Brieux, Sask. It’s a hopper-cone bottom on a slope of maybe 10 degrees, with a base that came with it,” Gronsdahl said.
“This gives us more capacity. Now we’re up to 60 or 80 acres between fills.”
The front spindle and hub for the cart came from a pull-type John Deere combine. The rear spindles are off a 1482 International combine and the 30.5L x 32 rear wheels are off a TR 96 New Holland combine. The front tires are the original 16.5L x 16.1 tires that came off the Concord cart.
“All the combine parts came from a salvage operation. Steel for the frame was purchased new. The main frame and the rear axle are eight-inch by six-inch by 3/4 -inch steel. We originally wanted to go with four by eight by 1/4-inch, but we couldn’t get any,” he said.
The Gronsdahls made the frame level with barrels and blocks and then Irvine started welding. They wanted to put the liquid tank over the rear axle for support.
“The liquid tank went on first, followed by the seed cart up front. We took the wheels and axles off, got a bin crane and hoisted it up on the frame,” Gronsdahl said.
“The tricky part was the front axle. The spindle sits upside down and the hardest part was making a brake for it. In the field it’s OK, but driving down the road it would wobble all around.
“We used half-inch steel and made a circle a little bit bigger than the bottom of the spindle. Then we got an automotive brake shoe and a couple of pieces of square tubing – one that would fit inside the other – with some springs on it that we can adjust to put pressure down on it.”
The brake setup can’t be controlled from the tractor cab. Gronsdahl loosens it in the field and tightens it before transport.
“It’s just there to provide some resistance.”
A new hitch was also in order.
“We tried to use the original hitch, but the old cart had automotive steering on it and this one doesn’t. So we made an A hitch from two points on the cultivator back to one point on the cart.”
Gronsdahl built his own ground drive system on the cart’s rear axle.
“When we bought the liquid kit from Pattison’s in Lemberg, (Sask.) they’ve got the same kind of tires on one outfit, so they gave us the size of sprockets we needed to get the proper calibration,” he said.
“There’s a large sprocket bolted to the inside of the right hand hub, with a double 60 chain going around that, and a small sprocket going around inside that on a jack shaft. It runs the liquid metering pump and the seed cart. We haven’t figured out how to remove the drive when we’re going down the road with the liquid cart, so we just take the chain off.”
An electric clutch allows the seed tank to be turned on and off from the tractor cab. As well, an electric valve on the liquid tank, controlled from the cab, will either return fertilizer to the tank or send it to the drill.
Because the new cart is taller than the original, the Gronsdahls had to lengthen the fill auger. They also added a low-profile hopper at the end of the fill auger to get under semis. One problem is that now the auger can’t swing under the cart to clean out the air tanks.
“We have to either get another auger to slide underneath it or empty it into a pail.”
The Gronsdahls added a hydraulic oil cooler from an old Massey tractor to the seed cart.
“We’ve got it so when the air seeder fan is running, it draws air through the cooler,” he said.
“You have to get out and stretch your legs once in a while. We’re seeding twice as much per fill. If you get a plugged run, you want to get out and have a look. Before we were out every two hours. Now it’s four. But it’s much more efficient.”