FOSSTON, Sask. – Most of the self-propelled swathers built in the mid-1980s can do just as good a job of swathing as a brand new unit. But at least 80 percent of them risk becoming obsolete because they have a built-in problem, according to Herbert Hallman. They are gas powered.
“Most everyone who owns one of these machines has the same complaints. They really like the swather, but cite the high price of gas, poor fuel economy, shortage of power, downtime over piddly gas engine problems such as plugs, points, carburetor problems.”
Read Also
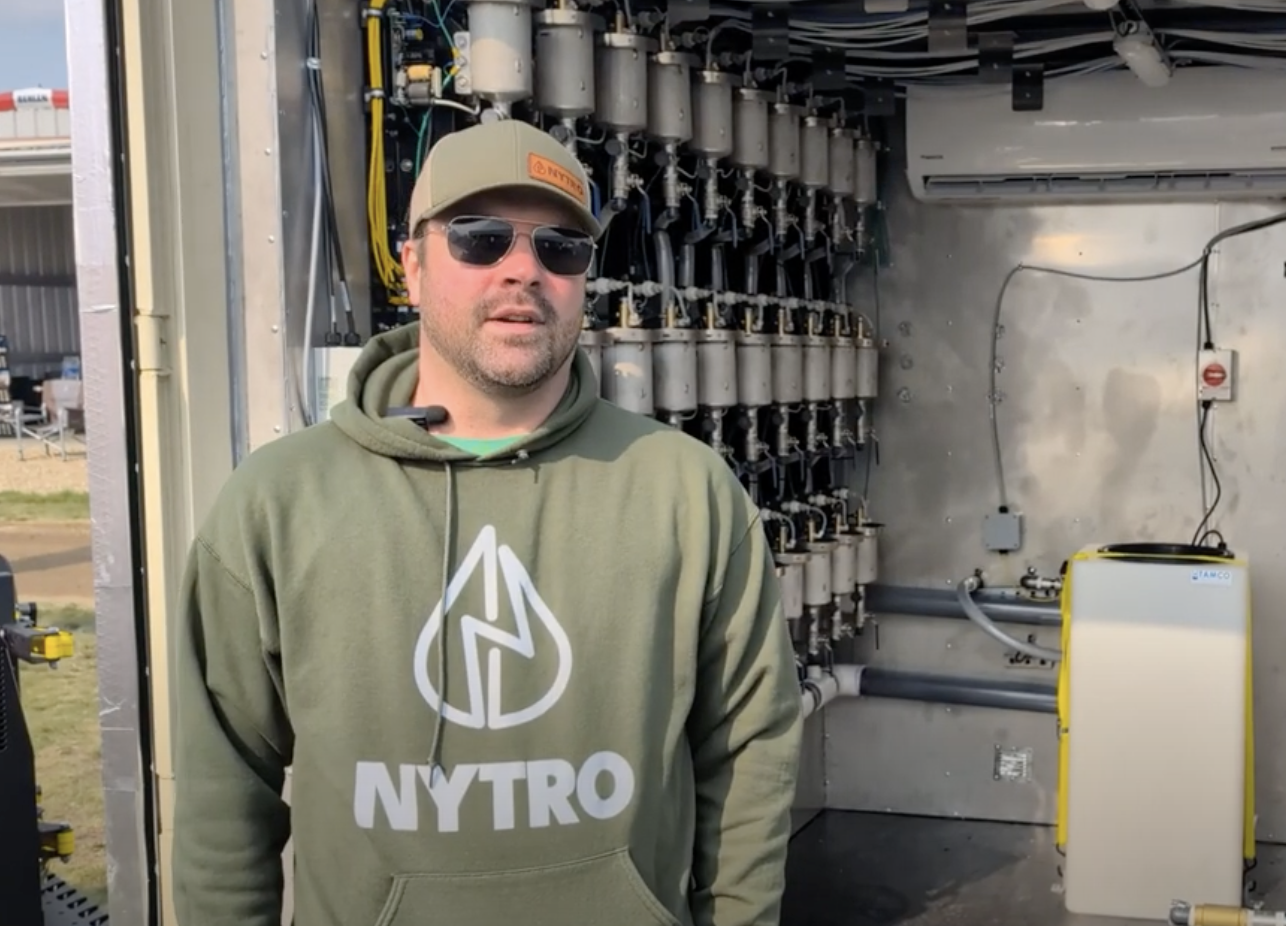
VIDEO: Green Lightning and Nytro Ag win sustainability innovation award
Nytro Ag Corp and Green Lightning recieved an innovation award at Ag in Motion 2025 for the Green Lightning Nitrogen Machine, which converts atmospheric nitrogen into a plant-usable form.
With a large header and pickup reel, they are too light on the rear end, said Hallman, who farms and operates an equipment salvage business near Fosston.
Hallman considered buying an IHC 4000 or Versatile 4400 swather and converting it to diesel to use on his own farm. He liked the fact the engine sits in the long way and hooks up to the drive with a shaft.
“Once the drive shaft is mounted to the diesel flywheel, it can be lengthened or shortened to make the installation as efficient as possible. The engine can be mounted higher, lower or even at a slight angle if need be,” he said.
This spring, Ray Hanson, a Tisdale, Sask., farmer and custom harvester, stopped in at Hallman’s to talk about his John Deere 2360 swather. He liked the swather, but it was approaching 2,500 hours, about the lifespan of a gas engine in a large swather. It was running poorly and oil consumption was getting excessive.
He didn’t want to pay $70,000 to $80,000 for a newer diesel model, and wasn’t prepared to spend money on the old slant six Chrysler gas engine, either. He asked if it was possible to convert his swather to diesel.
The swather was a MacDon, with the engine mounted crossways and everything belt-driven directly off a pulley on the flywheel.
“This system gives you no flexibility at all as the back of the new engine has to go back in exactly where the old one was, to retain proper belt alignment and tensioning,” said Hallman.
After looking at the swather, he felt engine length would be a problem, especially if a six cylinder diesel was used.
“I said a four cylinder engine would be best, but I didn’t have one, as they are hard to find and quite pricey. I suggested we use a six cylinder Perkins 372 engine out of a low hour 850 MF combine we had in stock,” said Hallman.
“He agreed that was a little big, but it wouldn’t be working very hard so it should get excellent fuel economy. He was also enthusiastic about the extra weight that it would put on the rear axle, as he was having trouble with the rear end coming up after he installed a pickup reel.”
The sheet metal around the engine was removed and the engine pulled out. The welded motor mount brackets of the gas engine were cut out to make an opening for the diesel engine.
The engine, along with all the radiator pipes and hoses, air cleaner, precleaner, intake pipes, and hoses and the complete exhaust system, plus the fuel lines to the tank, were mostly reused, either whole or in part.
“We took the swather engine output pulley and the Perkins flywheel to the local machine shop, where they mounted the pulley onto the flywheel. We cut out the combine bell housing with the plasma cutter, making room for the pulley, and opened up the front so the belts would clear,” said Hallman.
“Next we put this all together and set the engine into place. We lined up the pulleys, levelled and squared the engine and prepared to mount it. We went back to the MF combine and took out the channel iron that the bell housing had bolted to. This piece was drilled and tapped for this engine. We cut about three inches off one end, bolted it to the engine and welded it in between the two cross members.”
The front inside motor mount was sitting flat and square on the front cross member of the swather. A hole was drilled through the cross member and bolted down.
For the rear front engine mount, he drilled a piece of three-inch channel iron to bolt on the motor mount. This was cut to length and welded between the two swather cross members.
The engine was removed, painted and reinstalled along with the belts and air conditioner compressor. The original alternator fit perfectly into the MF bracket and lined up with the pulleys, while the tightener strap was perfect for the alternator.
“Length was our biggest problem, as the diesel was about six inches longer than the gas, so the rad would have to be relocated. The whole side wall containing the rad and coolers was just bolted onto the swather. We took out all the bolts and it came loose, but the lower rad tank was now sitting on top of the frame,” said Hallman.
“We cut out about 2.5 inches off the top of the frame for about 25 inches. We then welded this piece back in at a lower level and gusseted both ends to ensure the integrity of the frame.”
The original fan and rad were adequate to cool the diesel engine, but the water pump pulley on the diesel was drilled for six bolts, while the swather fan was a four-bolt mount. Hallman had a local machine shop cut the centre hole in the fan larger and redrill it to a six-bolt configuration.
“The front crank pulley on these combine engines is a four groove pulley, but we only needed two – one for the alternator and one for the AC compressor. We took the two extra pulleys off, shortening the engine about 2.5 inches,” he said.
“The fan bolted directly onto the water pump pulley without spacers and we still had a half-inch of clearance on the front of the engine.”
The hoses to the oil cooler and air conditioning rad were long enough that none had to be lengthened. Hooking the lower rad hose to the engine involved a 90 degree hose and a curved piece of steel pipe from the combine engine to get across from the opening in the rad, and a 90 degree rad hose fit over the steel pipe and into the rad.
“The top rad hose didn’t look good. The top of the thermostat housing on the engine where the hose went was lying flat and going toward the rad at 45 degrees. A Perkins engine from an 8800 White combine engine had a piece that sent the coolant straight up vertically. This brought it out just below the rad opening. Using a 90 degree rad hose from the combine, a piece of the swather top rad hose and some pipe adapters solved this problem,” he said.
With the new engine upright, unlike the slant six gas engine, the fan met the rad in a different place. Sheet metal and the original shroud were used to fabricate a new setup.
“The exhaust pipe bolts to the manifold with three bolts, so it can be rotated. We rotated the pipe one-third of a turn and bolted it on. This went to the front right hand corner of the hood, where we wanted to go. We cut a hole in the hood and extended the original pipe so it came through the hood. We found a JD combine muffler that had the inlet come in at 90 degrees to the muffler, so we mounted the muffler parallel to the hood, which worked beautifully.”
Hallman said the air cleaner system was a challenge. The intake opening on the intake manifold was pointing at 45 degrees straight toward the rad. He was unable to use any of the combine steel pipe due to space restrictions, so he mounted the combine air cleaner where the original air cleaner was. But the problem was to hook the air cleaner to the manifold.
“All the three-inch hose we could find locally was rad hose, which collapsed as soon as you bent it, and would certainly collapse under suction. … But I knew that liquid fertilizer hose sealed well when clamped onto steel fittings. It bends easy and will not collapse if used for suction. Four feet of three inch fertilizer worked fine,” said Hallman.
The original throttle rod and pivot plate worked with the new engine. For the engine stop, the original choke cable was exactly the right length, so it was used for the engine shutoff.
“We reused the original gas engine oil pressure and heat temperature senders in the diesel. It took some adapting, but it wasn’t a problem. We try to always use the original sending units that match the gauges. If you mix and match, sometimes they will work, but often you will get a fictitious reading on your gauges.”
Hallman said the left hand hood that goes over the engine compartment is hinged and can be opened up for servicing. After moving the side wall out seven inches, he thought the outer edge of the hood would hang in mid-air and more fabrication would be necessary.
“When we went to close it, it came down right on top of the side wall, closing the gap almost like it was planned that way. When the side door was reinstalled, the whole thing looked like a factory job.”
The large rear door on the engine compartment of a JD swather provides more screen for incoming air to the rad. It would have to be lengthened seven inches to get back to where it sealed on the side door. Hallman decided to leave it off. He screened the opening on the side door where these two joined and left the door off.
Hanson picked up his swather in August and used it for the full season on about 3,600 acres of crop. He said fuel consumption has improved dramatically.
“I’m using a little over half the fuel I was and the farm diesel is quite a bit cheaper than gas. I think one more fall and my costs will be looked after (in fuel savings),” said Hanson.
“It’s like a brand new swather. Before, you’re always lugging if you had a little hill. Sometimes I’d pull back because it was lugging. Now it walks right along. This year it was so wet and we plowed mud. We’ve got ruts all over. My little gas job, I wouldn’t have been able to do anything with it.”
He said this conversion saved him the cost of either buying a newer swather or redoing the gas engine.
“I had 3,200 hours on that gas job and it was starting to use oil. I would have had to give it an overhaul.”
Hanson said he expects to get another 20 years out of the modified 1985 swather.
“It was just like buying a new swather, only it just cost around $6,000. That was the best $6,000 I’ve spent in a long time. Anyone that’s got one like it, they can’t go wrong by doing what I did. They’ll be 100 percent satisfied.”