Fargo, N.D. – All main conversion components on the North Dakota State University Challenger MT525B can be ordered from specialty supply houses.
The question is how to put them together to safely run a diesel engine on hydrogen.
Bob Pieri urges farmers not to try.
If NDSU succeeds in making its test tractors run on a high ratio of hydrogen, the certified-as-safe conversion kits will be available as a dealer installed option.
Tyler Stousland, an engineering graduate student working on the project, says the university gets its wind-generated hydrogen from the NDSU research centre at Minot.
Read Also
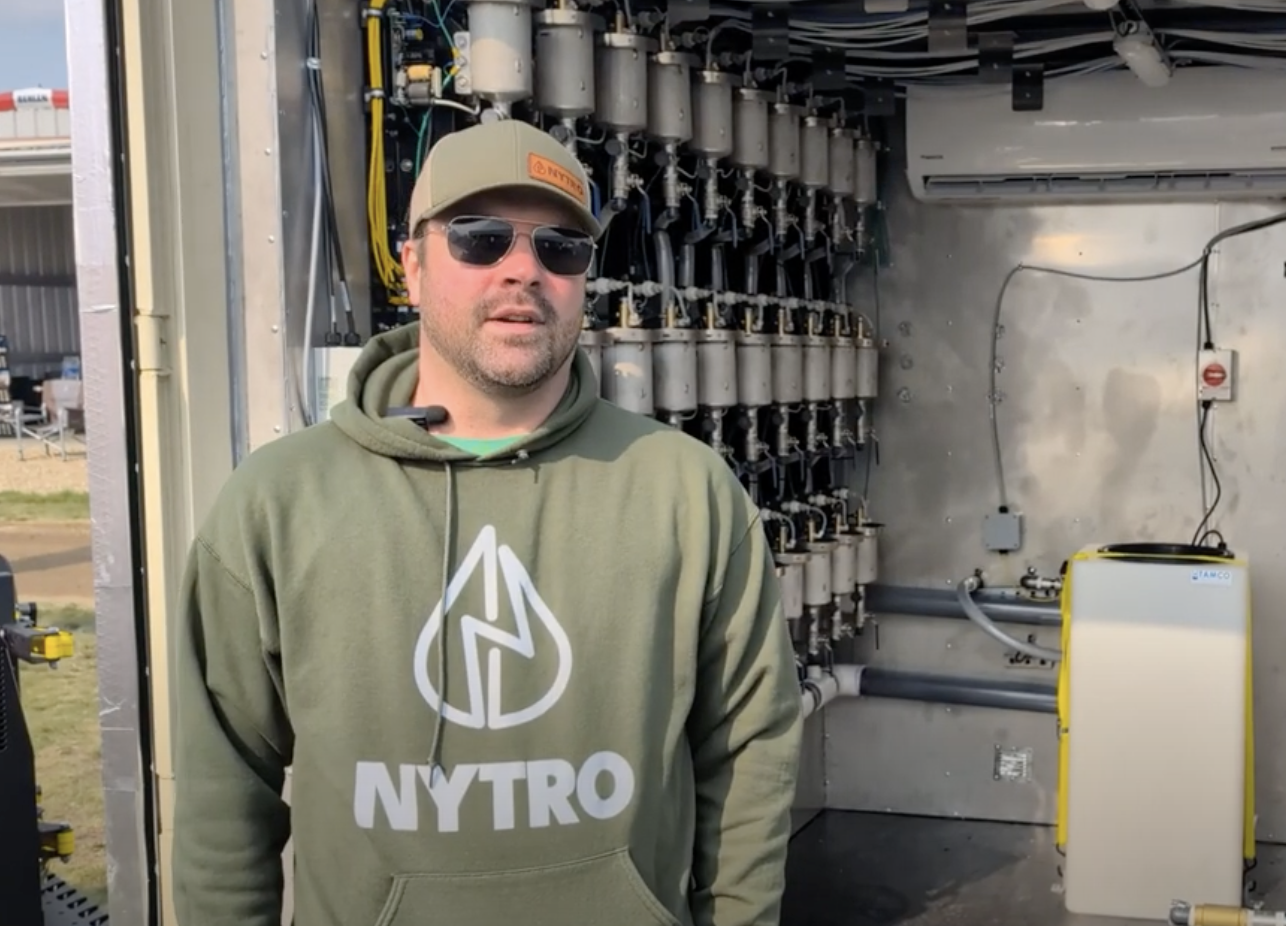
VIDEO: Green Lightning and Nytro Ag win sustainability innovation award
Nytro Ag Corp and Green Lightning recieved an innovation award at Ag in Motion 2025 for the Green Lightning Nitrogen Machine, which converts atmospheric nitrogen into a plant-usable form.
When approached with the Challenger challenge, NDSU had to find a way to use the hydrogen it was getting from wind, in a diesel engine.
Hydrogen is shipped from Minot to Fargo in the same type of tanks used in industry. It’s off loaded into the tractor tank as needed. All transfer couplings are the same OPW brand fueling components as used in industry.
Aluminum core
Stousland said the hydrogen tank at the front of the Challenger has an aluminum core wrapped in a fibreglass composite weave for strength.
It’s only coincidence that it looks like the Hindenburg.
“Hydrogen comes out of the tank through an electronic control valve,” said Stousland. “This is just straight on or off. From there, it goes into a holding area where we monitor the pressure.
“That’s where we have the second solenoid to regulate the pressure down to 90 psi. Then we have another gauge just to make sure it’s at 90 psi and that everything is working properly.”
Once researchers are sure the system is stable at 90 psi, hydrogen flows to the right side of the engine, where two valves regulate the flow to the intake.
The bottom valve carries most of the gas and is used for major adjustments.
The top valve is for fine-tuning the volume. Each valve has its own pressure gauge.
“To make this practical for farm use, we’ll have to integrate hydrogen adjustment into the existing proprietary software.”
From the control valves, the hydrogen flows to the front of the engine and then through a nozzle plumbed into the intake. This injection nozzle is located downstream from the turbo and upstream from the cast iron intake manifold.