There’s a high school in Winnipeg where Grade 11 and 12 students learn to weld stainless steel and aluminum, two metals notoriously difficult for welders to master.
The program has attracted students from as far away as Camrose, Alta.
“You can be an excellent welder when it comes to mild steel, but when you try stainless steel or aluminum, everything changes,” said Jason Feal, one of the welding instructors at Winnipeg Technical College.
“It’s not something you learn by trial and error.”
Feal said welders are just guessing if they don’t have a good comprehension of the exotic metallurgy.
Read Also
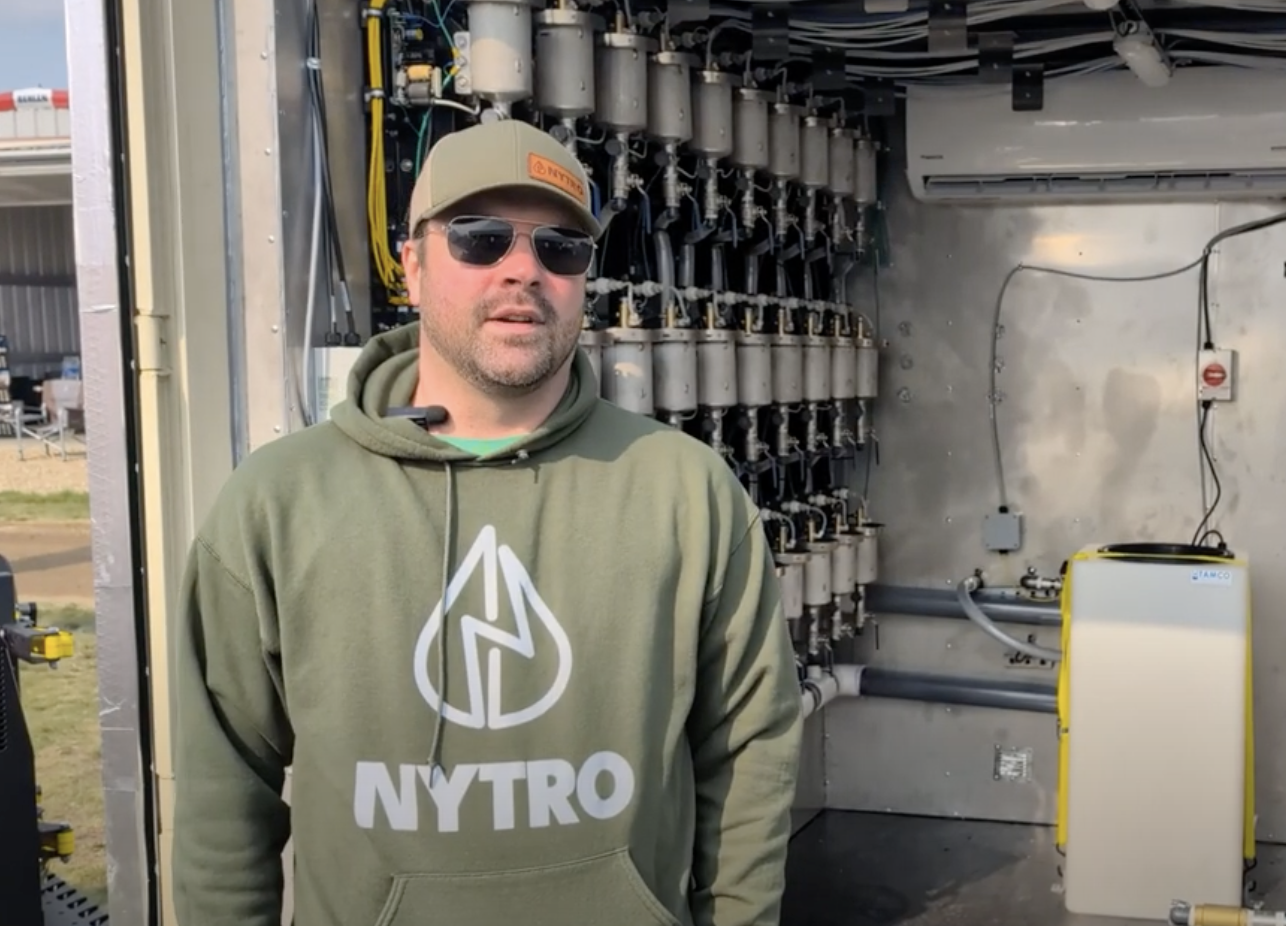
VIDEO: Green Lightning and Nytro Ag win sustainability innovation award
Nytro Ag Corp and Green Lightning recieved an innovation award at Ag in Motion 2025 for the Green Lightning Nitrogen Machine, which converts atmospheric nitrogen into a plant-usable form.
“Stainless steel, especially, presents some major challenges. It has four distinct characteristics that are all working against you simultaneously as you try to weld,” he said.
“Any one of these factors by itself is enough to ruin your weld job.”
- It has a lower melting temperature than mild steel.
- It does not conduct heat away from the weld point.
“The heat stays at the weld point and the rest of the piece remains relatively cooler. You can pretty well imagine that’s not good. Stainless steel conducts heat at about half the rate of mild steel, so the piece you’re welding doesn’t want to warm up.”
- It has a higher resistance to electrical conductivity.
- It has a higher coefficient of thermal expansion.
“The thermal expansion of stainless steel is two to three times that of mild steel. It’ll expand like mad if you’re not careful. It’s extremely difficult to control distortion. You’ve got to have your pieces jigged firmly. They’ve got to be held into position from every possible angle. Tight.”
Feal said it’s important to get the amperage right the first time. Too cold and the weld won’t hold. Too hot and it burns right through. Welders need to figure out in advance the lowest amperage to do the job.
“It’s a combination of skill and chemistry. It’s all a matter of doing your homework. You can only learn these things from a textbook or from the charts or in some kind of class.”
Another unique characteristic of stainless is something welders call the interpass temperature. If they lay on a second bead while the parent material is still glowing hot, they can easily change the structure of the stainless steel.
“For example, the 300 series stainless has 12 percent chromium to help it resist pitting, rust and abrasive wear. Chromium also gives the weld a high ductility so it won’t crack. But if your interpass temperatures are too hot, you are literally changing the properties of your stainless steel. You could deplete the chromium from 12 percent down to two percent without even knowing it.
“When that happens, what good is stainless steel? You’ve lost all those special properties you paid to get in the first place.”
Feal said the biggest difficulty with stainless is cracking at the weld zone, mainly because of wrong choices in welding rods and amperages.
“Those are all things you need to know before you even turn the switch on.”
By the time his students move into stainless and aluminum, they have already mastered welding mild steel with stick, TIG and MIG in all positions, he said.
“Once we get into the exotic metals, then we become very heavy on classroom work. We get pretty deep into the theory of the composition of the different series (of metals). We cover everything from the lower grade D300 series for things like stainless steel car exhausts, all the way up to the 900 series stainless for things like pressure vessels.”
Types of stainless steel are generally classified as ferritic, manteusitic, austemtic or duplex, depending on the presence of chromium, which can be 11 to 30 percent. There are more than a dozen straight chromium stainless steels.
As well, nickel, carbon, manganese, and molybdenum can also be found in some specialty types of stainless, which should be factored into the welding plan for each job.
When selecting a welding rod, welders must match its identity number with the stainless steel. These numbers are found on the rod’s flattened end.
The preferred process for stainless is gas metal arc welding, commonly known as MIG. In this process, the filler material is in a wire fed coil.
The weld bead is protected from the atmosphere by gas.
Second on the preference list is shielded metal arc, also known as basic stick welding. This process uses a consumable electrode coated with flux. As the flux burns, it creates a gas that shields the arc from the atmosphere.
Feal said the most challenging process used in welding stainless steel is the gas tungsten arc, commonly known as TIG.
This process depends on a non-consumable tungsten electrode. The weld area is protected from the atmosphere by a shielding gas, usually argon. The welder usually adds filler to the weld puddle.
“TIG welding stainless is very similar to gas welding, except that electricity is used to form the arc, versus gas fuel. This is the most difficult way to weld stainless.”
Selecting the TIG’s tungsten electrodes can be difficult. Although there are nearly a dozen different types of electrodes, the two percent Thoriated is the most common. These are the electrodes coded with the red flag at the top. They can be used for mild steel, stainless steel and chrome moly.
Feal said stainless and aluminum take practice and cost a bit more, so good advice or some training are useful.