The trend toward self-lubricating plastic bushings in farm equipment comes as a welcome relief to farmers who have had to grease all those zerks. Ignore the task and bushing failure is the inevitable result.
For the companies that build the equipment, the advantages of plastic bushings are even greater. Plastic is maintenance free and lubrication free so there are fewer warranty hassles and fewer disgruntled customers.
Plastics generally have a lower coefficient of friction, which means the implement they’re installed in should function more efficiently and the bushings should last longer. Dragging bushings leads to performance problems in any machine.
Read Also
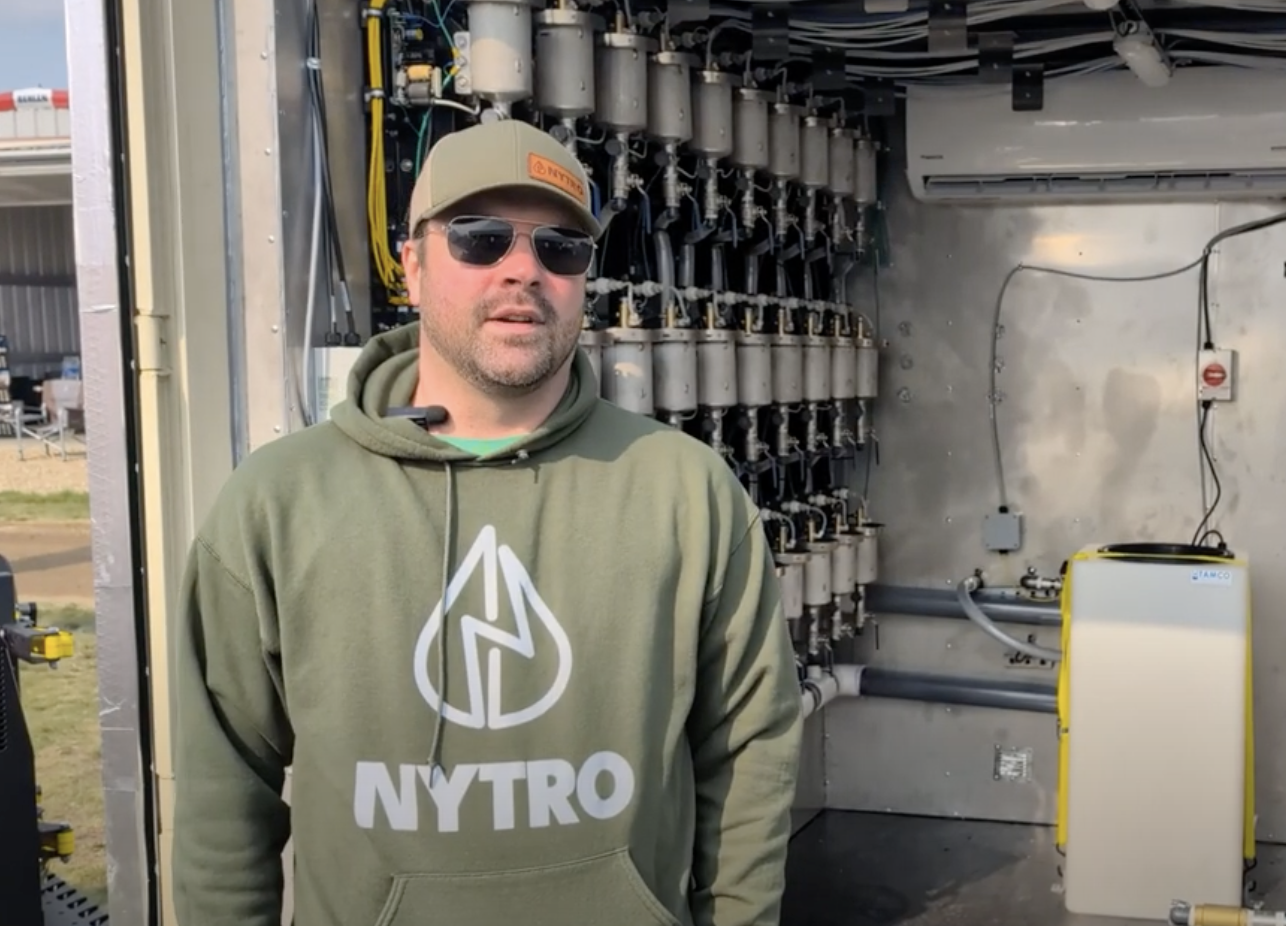
VIDEO: Green Lightning and Nytro Ag win sustainability innovation award
Nytro Ag Corp and Green Lightning recieved an innovation award at Ag in Motion 2025 for the Green Lightning Nitrogen Machine, which converts atmospheric nitrogen into a plant-usable form.
Most of the latest composites have a higher load capacity and they dampen vibrations. They are resistant to corrosion caused by chemicals, water and salt. They are not as susceptible to damage from dirt, sand and dust. In extreme conditions, where heat is a factor, some composites continue to function in temperatures up to 250 C.
Igus Manufacturing supplied plastic bushings to Conserva Pak before that company was sold to John Deere and they now supply plastic bushings to Honey Bee.
Igus says their bushings are made with a mixture of thermoplastic materials, embedded reinforcing fibres and solid lubricant. These compounds are blended in the mixture rather than applied in layers.
The fibre-reinforced materials maintain the bearing’s strength and provide resistance to high forces and edge loads. Edge loading caused by lateral force is a chief factor in bushing failure, especially in agricultural equipment.
The radial pressure or pivoting movement is less destructive than lateral force. Pivoting movement is managed by the plastic base material.
Solid lubricants are embedded as microscopic particles in millions of tiny chambers in the composite. The material releases tiny amounts of solid lubricant during movement.
Honey Bee
Honey Bee Manufacturing has begun the transition to plastic bushings. It installs one common size Igus bushing in six pivot points on the flex draper table it introduced in 2006, according to company owner Greg Honey.
“This is a header designed for cutting crops like beans, so we went looking for the best new composite bushing we could find that would stand up in dirty conditions without lubrication,” says Honey.
“Previously, we would have installed something like an oil impregnated bronze bushing or rubber encased bushing, but we opted for this plastic bushing from Igus instead.
“So far, the ones we picked have been doing a real good job for us. No breakdowns or problems yet, but it’s only been three harvest seasons so far.”
He said after the first year of production, Honey Bee found a bushing made from a different compound that was more suitable, so the company switched.
Honey Bee hasn’t gone all plastic. And those pivot points where it has begun to use plastic are not fast moving applications. The shafts just slowly oscillate back and forth about 25 degrees.
“I wouldn’t try to say we’ve got the best plastic bushings in there yet, but it’s working for us without giving us any problems, so we’ll stick with it for now. If it ain’t broke, I ain’t fixing it.”
Honey says the plastic bushings are in a common size that’s interchangeable with other common brands and sizes of bushings in case there are problems. He says the bushings have a standard width and length and are easy to install.
He adds that bushings make up such a small part of the total parts list that cost isn’t a big consideration compared to longevity. He says longevity and reliability are top priorities.
Does Honey think plastic bushings are tough enough to outlast bronze?
“Well, they’re using plastic and carbon fibre now to make driveshafts and leaf springs for trucks, so I think it’ll stand up.”
Conserva Pak
Conserva Pak started putting plastic into the pivot points on its drills about 10 years ago, says Conserva Pak inventor Jim Halford.
“We designed our Platinum opener with no metal-to-metal contact between moving parts. Every pivot point that might potentially seize someday has plastic bushings.”
He says seized bushings might be considered as nothing more than a minor nuisance in Canadian conditions, but it’s a major problem in Australia where a lot of Conserva Pak drills have been sold.
“Over there, the equipment sits out in the open through the summer, which is sort of like our winter. And we found that metal-on-metal bushings were seizing.
“I can’t say for certain, but I suspect it has something to do with the farmland being close enough to the ocean that salt is carried inland on the wind. We tried steel on bronze and steel on brass, but metal-to-metal just didn’t work in Australian conditions.”
There were bushing failures after initial conversion to plastic, but that was a matter of not knowing which composite to select. Halford says plastic bushings work in ag equipment. The issue is matching the proper composite to the job at hand.
He says Conserva Pak has installed both injection mould bushings and machined plastic bushings. The self-lubricating plastics seem to work the best, and are maintenance free. He says another consideration is how dust and particles get in and out of the contact area.
“Some of these composites test out to be harder than steel. Then you actually get your steel components wearing faster than the bushing itself. So you really need to get good information before you order the bushings.
“The Igus company we dealt with comes from Germany. They’ve been doing plastic bushings for years in all kinds of corrosive and heavy duty applications like mining equipment.
“So I think they should be good around the corrosive materials we see, such as granular fertilizers.”
For further information, visit www.igus.com.