LETHBRIDGE – The food versus biofuel debate should be expanded to include bioplastic, according to an Alberta government official.
Ed Phillipchuk of Alberta Agriculture’s bio-industrial development branch describes bioplastic as plastic manufactured from biopolymers, which are small chemical units called monomers.
“Bioplastics aren’t necessarily biodegradable. I think this is important because some people use these terms interchangably,” Phillipchuk said.
“Bioplastics originate from an organic material. Biodegradability is a performance characteristic. Even petro plastics could be made biodegradable, but they’re not. They’re (simply) degradable.”
Read Also
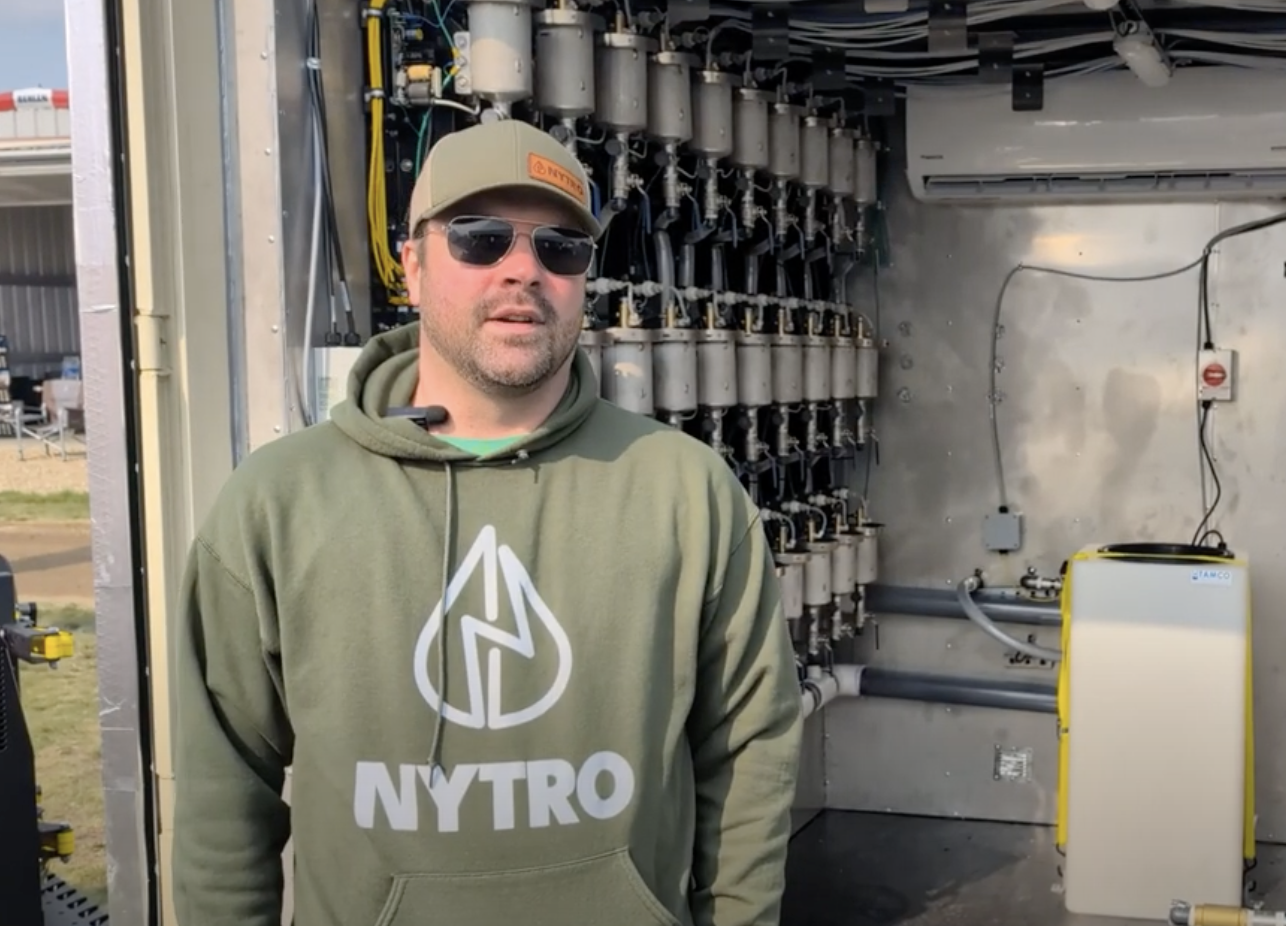
VIDEO: Green Lightning and Nytro Ag win sustainability innovation award
Nytro Ag Corp and Green Lightning recieved an innovation award at Ag in Motion 2025 for the Green Lightning Nitrogen Machine, which converts atmospheric nitrogen into a plant-usable form.
Phillipchuk said the plastic industry has come up with innovative ways to market these performance characteristics.
For example, chemicals can be blended into the styrene molecule of polystyrene, such as a Styrofoam cup so that when exposed to air and light, they break down into styrene.
“You no longer see the Styrofoam cup, but there’s the persistence of styrene in the environment,” he said.
“With bioplastics, we can take that molecule and under light and water it breaks down to carbon dioxide and water. That is truly biodegradable.”
Phillipchuk said biopolymers have two synthesis groups -biological and chemical.
“You can use micro-organisms. As they grow on wheat, corn or other organic substrates, they have the capability to make plastic granules within their cellular structure,” he said.
While it would require a lot of bacteria to produce a pound of plastic, researchers can use biotechnology to transfer that capability from the micro-organism to a plant to make plastic.
“Another synthesis pathway, where you can take wheat, corn, potatoes or whatever, involves fermentation,” he said.
“You convert the starch into alcohol, or go one step further and make lactic acid. Cargill has taken this lactic acid, polymerized it to make larger molecules and created a product called PLA (polylactic acid). PLA is 100 percent biodegradable. You can also look at triglycerides or vegetable oils. In the U.S., a lot of the bioplastics are soy based. Our technology is more canola based. We’re also looking at flax.”
Petroleum prices are helping drive this market. In 2006, Phillipchuk said world plastic prices increased 30 to 70 percent.
“We have to keep in mind that out of a barrel of oil, we do not get an equivalent amount of plastic. We only get 50 percent. The other 50 percent is used to create energy to make plastics.”
He expects the global market for plastics to increase to 260 million tonnes from 200 million per year in the next three years. Polyethylene polypropylene is worth 65 cents a pound while polypropylene polystyrene is $1.10 per lb.
Phillipchuk said the global annual consumption of plastic is expected to increase from 25 kilograms per capita to 37 kg per capita in the next three years.
“Where’s that plastic going to come from? In the next 10 years, we feel we can capture from two to five percent of the marketplace. But the success is going to be driven by functionality and cost,” he said.
“Historically, bioplastics have been two to three times the price of petro plastics. Having said that, PLA is only 10 percent more expensive than petro plastics. So the price gap is changing.”
In the past three years, announcements from Toyota, Cargill, DuPont, ADM, BASF and John Deere suggest bioplastic is here to stay. Phillipchuk said the side panels of John Deere combines are already being made out of soy plastic.
“The bioplastics market is only about one percent of the total plastic market right now, but when you get people like Cargill investing, over the last 10 years, $750 million into PLA, with a capacity now of almost 200,000 metric tonnes, it creates economies of scale that end users are willing to accept,” he said.
“In Europe now, 90 percent of new automobiles have to be recyclable. That’s why they’re looking at bioplastics and ag fibres. In the U.S., their government has a procurement policy that says if bioplastics can compete on price and functionality, the U.S. government will buy that product. So that’s another incentive.”
Phillipchuk said Alberta has established an Alberta Bioplastics Network to study bioplastic.
“This project is part of a larger project called the Alberta Lipid Utilization program, where research on the use of canola, flax and oilseeds is being driven on the food side and the industrial side,” he said.
“We’re looking at about $50 million over the next three years put into research and oilseed expertise.”
The University of Alberta is driving the science, with chemists and other scientists converting the oils into industrial products and studying the performance of those products.
“It’s nice to have laboratory research, but how do you take it to commercialization? Our capability at present is about one or two kilograms of monomer per day,” Phillipchuk said.
“One of our clients, a major automobile manufacturer, wants 45 gallons of monomer a day. So we’ve got a bit of a problem, but we’ve solicited about $2 million for a pilot plant at the University of Alberta, to look at scale.”
Market plan
The group has also agreed on three strategic market areas it wants to explore:
- A high volume, low priced commodity, such as plastic bags or garbage bags.
- The biomedical field, with a smaller, high end market such as medical implants made out of plastics.
“Rather than using stainless steel pins, we can develop a bioplastic pin that as the bone heals the pin degrades.”
- Automotive biocomposites, which Phillipchuk said is a large, fastidious market that’s tough to get into.
“If you don’t deliver on time once, that’s the end of the business.”
Phillipchuk said one of the group’s clients, Bunge, is not interested in being in the plastics business.
“They’re interested in converting canola oil into a monomer and passing the monomer on to someone else for value added. Hopefully we’re on schedule.”