FORT SASKATCHEWAN, Alta. – When customers at the Agricore United elevator in Fort Saskatchewan requested seed treating services, staff saw an opportunity. To capitalize on it, they had to develop a seed treating system that fit their operation.
Don Reiter, a customer service rep with AU, said accuracy was the first concern. Then he had to figure out a cost-effective system for the elevator’s seed bin arrangement. He settled on a personally designed mobile seed treater.
“The mobility part came from the fact that we don’t have the setup to move bins around and create a permanent system,” he said.
Read Also
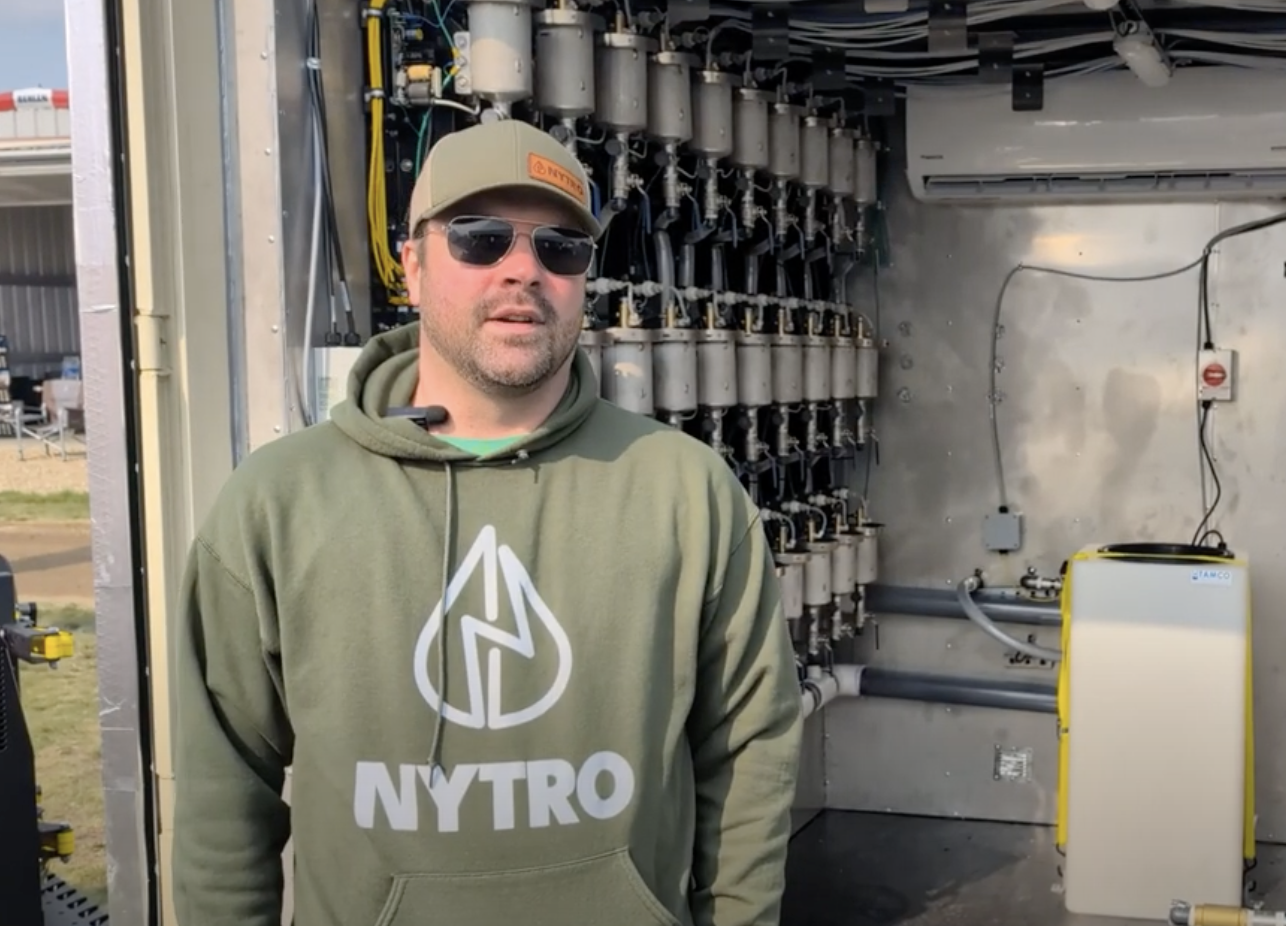
VIDEO: Green Lightning and Nytro Ag win sustainability innovation award
Nytro Ag Corp and Green Lightning recieved an innovation award at Ag in Motion 2025 for the Green Lightning Nitrogen Machine, which converts atmospheric nitrogen into a plant-usable form.
“The ability to move it around was the compromise.”
Graham Seed Farms, which manufactures the G3 and G4 seed treater, gave Reiter photos of other mobile setups to give him ideas for his design.
“We wanted it to be accurate and have a decent enough capacity that we wouldn’t have lineups, or farmers waiting all day to get their seed treated. But accuracy was the first criteria,” Reiter said.
“The heart of the unit is the Graham G4 seed treater. Doing research into what seed treaters are out there, it was the simplest, most accurate and cost effective.”
The Graham seed treater is a hollow cylinder with a cone inside. A hollow-cone spray nozzle inside the unit shoots a stream of seed treatment onto a curtain of grain.
Each kernel should have some seed treatment on it after the initial spray. The seed then proceeds up a grain auger to the box of a farmer’s truck.
The auger acts as a mixer that continues to move the seed treatment around, ensuring an even, consistent application on all kernels.
Cones on the treater restrict the grain to a certain flow, which helps calibrate treatment rates.
“The frame was custom made at a local machine shop. I drew up some rough specs on dimensions and they built it from the ground up,” Reiter said.
“The frame is six-inch I-beam, with expanded metal for a grate to walk on. The hopper on top holds about 20 bushels of grain. There’s a 16-foot six-inch auger that goes up to the farmer’s truck. That has a three horsepower electric motor on top to drive it.”
The hopper on top of the treater was built from scratch. Grain sits in the hopper and gravity feeds it into the treater unit below.
The auger is braced about six feet up from the base, with cabling from the hopper to the top of the auger.
“The motor on the top of the auger has a bit of weight to it and when we were moving it around, we felt the auger was flexing a little too much. That’s just to add extra strength and support.”
The mobile treater has two product pumps.
“At the time we built it, the water soluble products were just coming in and you can’t mix the solvent-based and water-soluble products through the same pump. It just gums things up,” Reiter said.
“Now, we have one major product set up through drums, then have some secondary products through the second pump. We wanted to get away from the jugs, which add an extra delay. But we do have the ability to go from jugs for smaller quantities or using a drum for someone who wants to pick up a semi load of seed.”
Everything on the seed treater operates electrically. The pumps that meter product through the treating chamber are standard 110-volt units, while the electric motor on the auger uses 220.
“Because we treat different types and varieties of grain, the auger is reversible and there’s a clean-out hatch on the bottom. Once the treating is done, this is reversed. Whatever comes out the bottom is caught in a tub and it’s put into the farmer’s truck. There’s no waste and no environmental issues.”
The unit has two large automotive wheels and two small castor wheels for steering. AU staff generally use a forklift to move it around.
“We can do between 20 and 25 bu. a minute. That’s not too bad. I’d like to see it a little better, but we can treat a fair bit of grain in a day, with minimum lineups.”
It’s not a setup that can be turned on and left to run for the day. Reiter said an operator is always at the seed treater when it’s working.
“We’re treating directly into farmer’s trucks and the farmer is there at the time we’re treating. The operator is there to fill the hopper and set the pressure for the treatment pumps.”
Sight gauges on the hopper allow the operator to stand beside the bin and turn the auger on and off.
“It’s all electric, so it’s a matter of hitting a button. It also takes him away from any fumes or the noise of the treater.”
Having a good operator is important, Reiter said.
“You have to calibrate it to know how fast your grain is flowing through and you have to have a good eye on what the colour of the grain is and how fast the chemical is going out,” he said.
“Another thing is to make sure it’s always level. If you’re out of level, you’ll have more grain flowing on one side than the other and that will cause problems with getting even coverage.”
The elevator in Fort Saskatchewan sticks to cereal grains and uses all the seed treatments that are registered. It hasn’t applied seed treatments or inoculants to oilseeds or pulse crops.
Reiter said the treater cost $10,000 to build, including materials and labour. He said he would do a few things differently if he were building it again.
For 2004, he raised the platform by 18 inches to provide more clearance into semis and wishes he had originally built a step to get up to the platform. He’d also put a larger hopper on top.
“When I first designed it, we were going to have a scale up there so we could scale it through. But cost was prohibitive. That would be better for a permanent setup, but not for a mobile treater.”