Conventional anaerobic biodigesters do a fine job of breaking manure down into basic elements, but they need temperatures of 35 to 40 C.
For high-speed biodigesters, it’s more like 50 C.
All of this biodigestion is good for the environment, but the supplemental heat is a major operating cost, no matter what fuel is burned.
To further complicate matters, conventional anaerobic digesters become chemically unstable and lose their ability to function should the temperature fluctuate.
Read Also
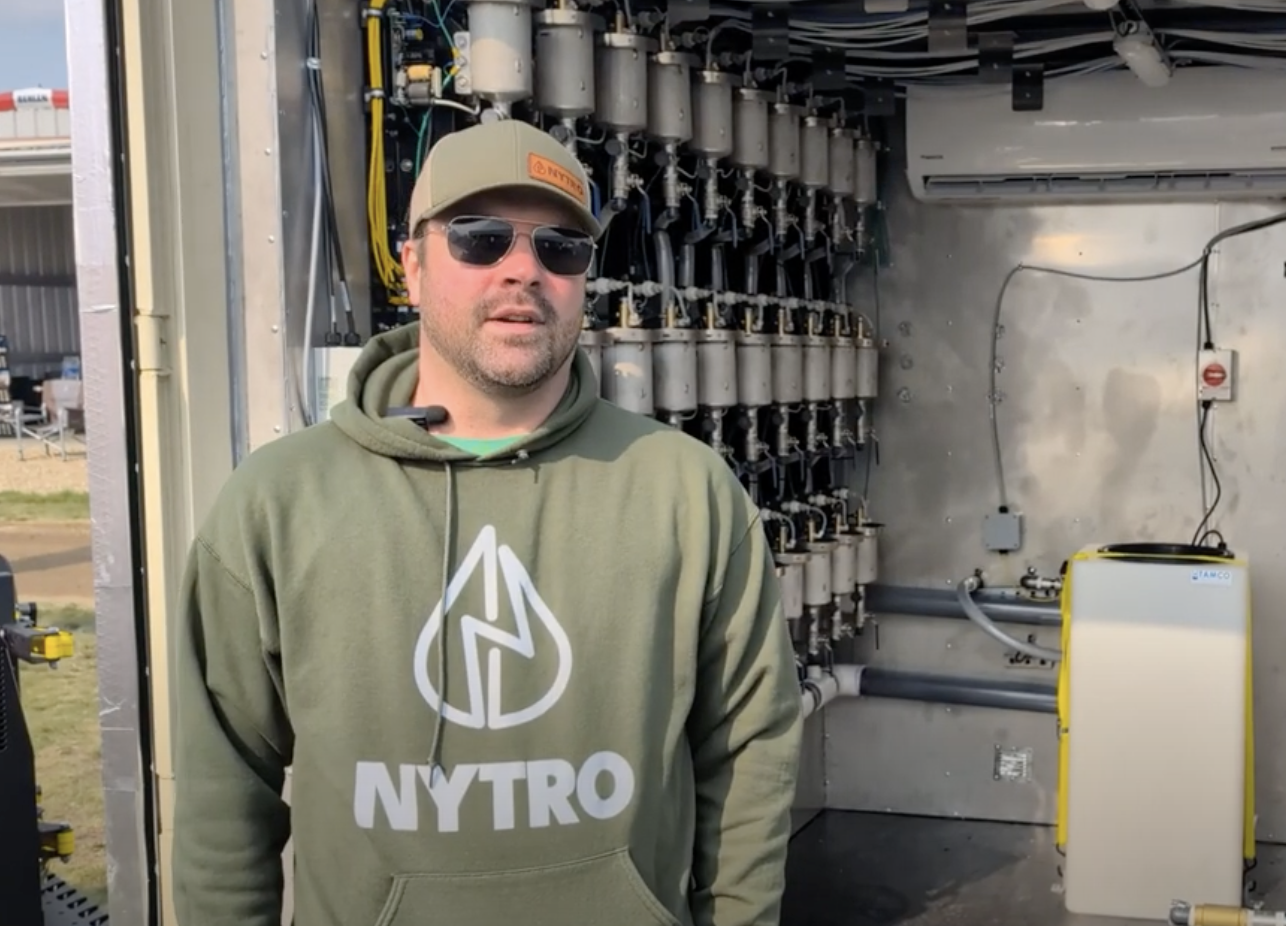
VIDEO: Green Lightning and Nytro Ag win sustainability innovation award
Nytro Ag Corp and Green Lightning recieved an innovation award at Ag in Motion 2025 for the Green Lightning Nitrogen Machine, which converts atmospheric nitrogen into a plant-usable form.
However, a biological breakthrough has eliminated the need for energy input. It’s called low-temperature anaerobic digestion and requires temperatures of 20 to 25 C.
The gravy is that the special organisms injected into the pig slurry tank generate enough heat to meet the digesters’ needs.
A further benefit is the creation of surplus heat that can be used for other purposes on the farm.
Dennis Hodgkinson, owner of DGH Engineering in St. Andrew, Man., and one of the founding partners in Bio-Terre Systems, holds patents on the original technology. He said the company has two low-temperature digesters running round the clock on hog farms in Quebec.
The smaller operation is a nine-year-old 1,000 head finishing barn and the other is a three-year-old 5,000 head finishing operation.
“We’ve learned a lot from these first two hog operations. The most noticeable change is that the odour is significantly reduced,” Hodgkinson said.
“With the extra heat we generate, they have totally eliminated their fuel bills for heat. Plus, they keep the barns warmer. There’s better feed conversion because the animals are warmer, so that translates to better weight gains.
“The extra heat lets them increase the ventilation and run more fresh air into the barns. So they have lower humidity, less mould and less respiratory disease. It all works very well.”
Hodgkinson said winter temperatures were Bio-Terre’s main challenge. Microbes that work in areas with year-round warm weather do not survive in Canada without adding costly supplemental heat.
He said his company’s low-temperature process works because it identified and cultured special groups of microbes that do not require a lot of heat to break down organic waste.
They not only perform their work in a cooler tank, but they are more stable and more tolerant to variations in their environment than microbes typically employed in anaerobic digestion.
Hodgkinson said the overall plan isn’t new.
“We convert organic matter into a fuel gas – methane. This biogas fuels an internal combustion engine that can run a generator or a vehicle. Plus, it provides heat for the barns.”
Although the system can burn methane directly to fire a boiler, as one of his Quebec clients does, Hodgkinson said it works just as well to heat barns with the excess heat from the co-generator engine, as done by the other client.
It runs the engine coolant that would normally pass through a radiator into the barn’s heating system instead.
Once the barn’s heating needs are met, the liquid still carries surplus heat. In addition to the generator, this farm also uses methane to fuel a boiler.
Alex Singbeil, an engineer working on the Quebec project, said that if the bacteria population is organized correctly, the same tank can handle all types of waste produced by a livestock operation, including manure and dead animals.
“The bacteria live in the tank and eat organic material – all types of fat, protein and carbohydrates.
“But they don’t eat much cellulose, so cereal straw and wood chips aren’t suitable. Corn silage is fine because it breaks down. We find that when anaerobic digestion is complete, the cellulose is left over. That tells us that cellulose isn’t right for the system.”
Singbeil said the bacteria that Bio-Terre isolated and cultured is found in dairy manure and are the same organisms found in the rumen of a cow.
The company has worked mainly with hog operations, but the bacteria in hog manure don’t work in the digester.
“The whole magic is how we identify and develop those bacteria and then set up the right environment,” Singbeil said. “We monitor them and ramp them up to high concentrations so they’re effective in quickly treating the waste. To some people, it seems like we’re trying to duplicate a cow’s anatomy, but actually our biodigester operates at a temperature lower than a cows anatomy provides.”
Singbeil said energy self-sufficiency and electrical production are two reasons why the Quebec hog farmers got involved with the low-temp anaerobic project. Phosphorus is another.
He said interest in the Bio-Terre project is high in Quebec because producers are concerned about phosphorus released into the environment.
“This system gives you better control in managing the phosphorus in manure,” he said.
“Phosphorus is concentrated and retained in a solid form. It stays behind in the bottom of the tank. This means you stop spending energy to agitate the tanks.
“The liquid has very little phosphorus so it can be applied to nearby fields through regular irrigation nozzles if you want. The nitrogen level is the same as from any lagoon. Nitrogen isn’t affected by the anaerobic process.
“But the phosphorus is gone, so you don’t need to spend money to transport the slurry great distances moving it away from your farm.”
Singbeil said Bio-Terre has conducted cleanouts at the Quebec sites, and lab tests show the digester reduces phosphorus to two percent of the total volume of manure.
“The two percent of solids at the very bottom of the tank contain 50 percent of the phosphorus,” he said.
“So after a period of years, a farmer can collect the highly concentrated phosphorus and economically transport it to a site far from the point of origin. You can’t afford to do that if phosphorus is mixed in with liquid slurry.”
Another benefit of the digester is that the methane that is produced has a dollar value if markets for it are developed.
“The methane is always pure enough and clean enough to burn straight. There’s no further refining or anything,” he said.
“Coming out of the tank, the product is 60 to 70 percent methane. There are trace amounts of hydrogen and other long chain hydrocarbons. But there are significant amounts of hydrogen sulfide. That’s a contaminant. That’s an issue.”
Singbeil said the rest of the gas is carbon dioxide.
In Europe, where environmental regulations have been stricter than in North America for a longer period of time, the low-temperature anaerobic biodigester technology is more advanced.
“They produce pipeline quality methane gas straight out of the biodigester,” Singbeil said.
“That’s with a combination of animal waste and non-cellulose energy crops.”
Hodgkinson said a few low-temperature biodigesters are working in Western Canada, but he thinks it’s only a matter of time before the technology becomes commonplace on the Prairies.
He said the digester does not require an operator to build a new manure handling system from scratch. It can easily be inserted into the existing flow.
As well, Hodgkinson said the Bio-Terre system eliminates 99 percent of pathogens from waste material.
“We already know that the technology works very well, even in colder climates,” he said, although the initial investment is still a factor.
“It costs enough that it’s hard to make it economical right now without some movement in the market for green energy.”
For more information, phone Alex Singbeil at 204-334-8846 or visit www.dghengineering.com.