LANIGAN, Sask. – Dean and Gary Klatt, who farm with their father Ernie near Lanigan, have switched to liquid nitrogen fertilizer from dry in an effort to improve seeding efficiency and seedling safety, plus reduce fill time. Part of the switch involved adding a liquid cart to their drill, a 49-foot Morris Maxim with a three-tank cart.
“Just for more capacity, we decided to go to a liquid cart,” Dean Klatt said.
“It looked like a fairly easy project, so we decided to build it and save some money.”
Read Also
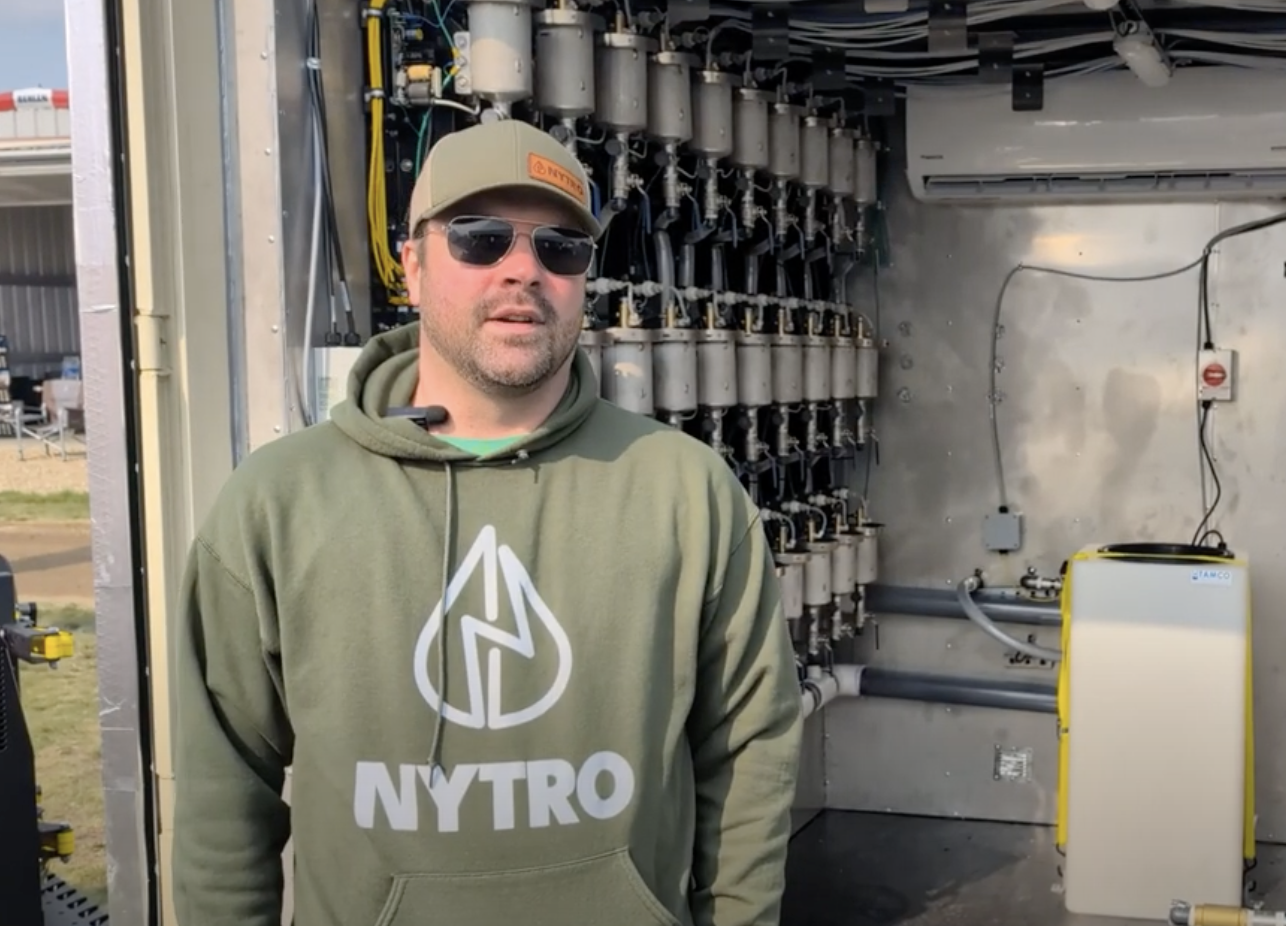
VIDEO: Green Lightning and Nytro Ag win sustainability innovation award
Nytro Ag Corp and Green Lightning recieved an innovation award at Ag in Motion 2025 for the Green Lightning Nitrogen Machine, which converts atmospheric nitrogen into a plant-usable form.
They had already switched to zero till and found they could cover only 40 or 50 acres per fill on their canola fields when applying the fertilizer dry with higher rates of nitrogen.
“The extra capacity comes from our nitrogen in liquid form,” Klatt said. “We have so much more room for seed and phosphate in the air cart. Now we can go up to 120 acres on wheat or 90 acres on canola before we have to fill up again.”
He said the new setup takes about 20 minutes to load, the same as without the liquid cart.
“It doesn’t take us any longer to fill up because we can start filling the liquid cart and leave it. Then we start the seed and dry fertilizer and by the time we get the seed and dry fertilizer filled up, the liquid cart may have a couple of hundred gallons to go and it’s full.”
The Klatts had looked at different carts being used in the neighbourhood before building their own. A trip to an auction sale yielded bargain-priced steel to get them started.
“There was this large square tubing: probably eight by 12 inch. It was so big not a lot of people were bidding on it. It was bigger than most people would use, so we bought that. It went really cheap and that’s what we built the frame out of.”
Two lengths were used for the main frame rails, while the cross members were made from the same eight by 12 tubing by splitting it to make lengths of ‘U’ channel that were welded between the main rails.
A 2,100 Imp. gallon tank was bought new from Polywest in Saskatoon. Metal hoops that loop over the tank and are bolted to the frame hold the tank in place.
“There’s four hoops on the tank,” he said.
“They want steel hoops to help support the tank, but wanted $1,200 for the four. So we took some muffler pipe, made a form and bent them around the form. They give a little side support to the tank.”
The front axle is made from six-by-six square tubing with a heavy, half-inch wall.
“We took the hubs off a small pull-type combine, I think it was a 9600 Co-op Implements,” he said.
“Inside the square tubing we welded in brackets so the axle shafts would slide in and get held in. That same square tubing is the up-and down tube that holds the front axle. Then we built a pivot in there. There’s a shaft that goes inside and we made bushings inside that up-and-down tube for it to pivot on when turning. Then there’s just a shaft for your lateral pivot if you’re going through a ditch or something.”
The rear axle came from an International 1482 pull-type combine. The Klatts welded a beam on the bottom to give it extra support and widened it about a metre.
A new John Blue ground-drive pump delivers liquid fertilizer to the openers on the drill.
“It’s a fairly big pump, but if we ever go to liquid phosphate as well, we have the capacity to pump that much more liquid, as opposed to putting one on that would just do what we need now.”
The pump drives off the left rear wheel. The Klatts bolted a sprocket to the inside of the hub that drives a shaft leading to an electric clutch. It comes from an old combine and engages and disengages the pump.
“I believe when you buy the pumps, you either get them with an optional electric clutch or the pump runs all the time and you bypass when you’re turning at the end of the field,” Klatt said.
“But the disadvantage to that is when you go down the road, you have to take your chain off. We had this electric clutch sitting around from a different project we’d done, so we put it on.”
The clutch is mounted on top of the rear axle and is connected to the pump by a chain.
“When you engage the clutch, it continues the connection on to the last chain that goes up to the pump.”
Tires for the front of the cart are new, the same size as those on the front of the air cart. The Klatts started with the diamond tread tires that originally came with the 1482, but had squat and compaction problems. As a result, they switched to larger lug-style tires and find they reduce compaction and carry the weight better.
The new tires, from a Gleaner combine, are 30.5L Ð 32, while the originals, with the diamond tread, were 28L Ð 26.
The Klatts fill the tank with a two-inch Honda pump mounted on the back of the cart.
“The reason the engine is on the cart is, when you’re done loading, you crack the line at the truck and it will suck air,” he said.
“That way, the pump will suck the line dry and you don’t have fertilizer dripping everywhere.”
After seeding is finished, the pump is moved to a water truck to fill the sprayer.
“We’re considering going to a three-inch just for extra capacity.”
For extra insurance, they added supports on the cart’s rear axle where it attaches to the drill. Klatt said it pulls on the main frame, but they also have to pull from lower down, so they put supports with box steel to better triangulate the rear axle.
The family blends liquid nitrogen and liquid sulfur when seeding canola but only liquid nitrogen on cereals. Granular phosphate and potash go in the air tank.
“It’s a three-tank Morris cart,” Klatt said.
“We also made the front tank larger. It’s just about double in size over the original, from 32 bushels to around 54. We made it a foot taller, and also added to the front, making it a foot deeper front to back.”
He said they had done that even before building the liquid cart so the front and rear tanks would run out closer to the same time.
“It would be more evenly balanced,” he said.
“Our seed and fertilizer would also run out closer to the same time. Now we run our seed in the small front tank and large back tank. The granular phosphate and potash are in the centre tank.”
The seed tanks are metered so they both run at the same time. Seed from both tanks, plus the granular fertilizer from the middle tank, single shoots through the seed tube.
Using Atom Jet openers, the liquid fertilizer shoots out a tube behind a wing, above and to the side of the seed.
“Another reason we went to liquid is we were using a paired row opener and we weren’t happy with our seed placement with canola,” he said.
“We were getting some bounce and I’d tried cutting the air down, but we weren’t happy. When you’re putting your nitrogen down lower, you’re breaking up your seedbed. With a paired row opener, you have a point that goes down quite deep so your nitrogen goes down below. This way, with a single shoot opener, we have a firm seedbed and we find our canola placement is quite a bit better. It’s more accurate on the depth.”
Klatt said an additional benefit is the longevity of the openers they’re now using.
“The wear is absolutely phenomenal on these Atom Jet openers. With the paired row opener, the regular one would get at the maximum 1,800 acres. Then we went to carbide tipped paired row openers and at 7,000 acres they were wore out. These Atom Jet openers, we’ve got 15,000 to 18,000 acres on them now and they’re still fine. They’ll go at least another 5,000 acres.”
It took two men three weeks in the shop to build the cart, which required $12,000 worth of materials.
“It was a simple project and very straightforward,” Klatt said.
“We haven’t had any problems with it and are really happy with the liquid use, even though liquid nitrogen is a bit more money. The crop safety is way better with liquid, being able to use those openers for so long, plus it’s nice to handle. Just hook up a hose, turn a pump on and you’re done.”