WINNIPEG – Fossil fuel energy to power machinery and produce nitrogen fertilizer has been gobbling up an ever-larger slice of the profit pie since the petroleum crisis of the 1970s.
An alternative that’s receiving more attention lately is the closed loop system that sees farmers producing more of their own inputs on the farm rather than buying inputs based on fossil fuel. Two obvious areas of self-sufficiency are biodiesel and manure fertilizer.
Growing their own inputs may seem like the smart thing for farmers to do, but what about the practicality and the economics of such endeavours? If it is feasible, how much of a dent can a farmer reasonably hope to make in his annual fossil fuel bill?
Read Also
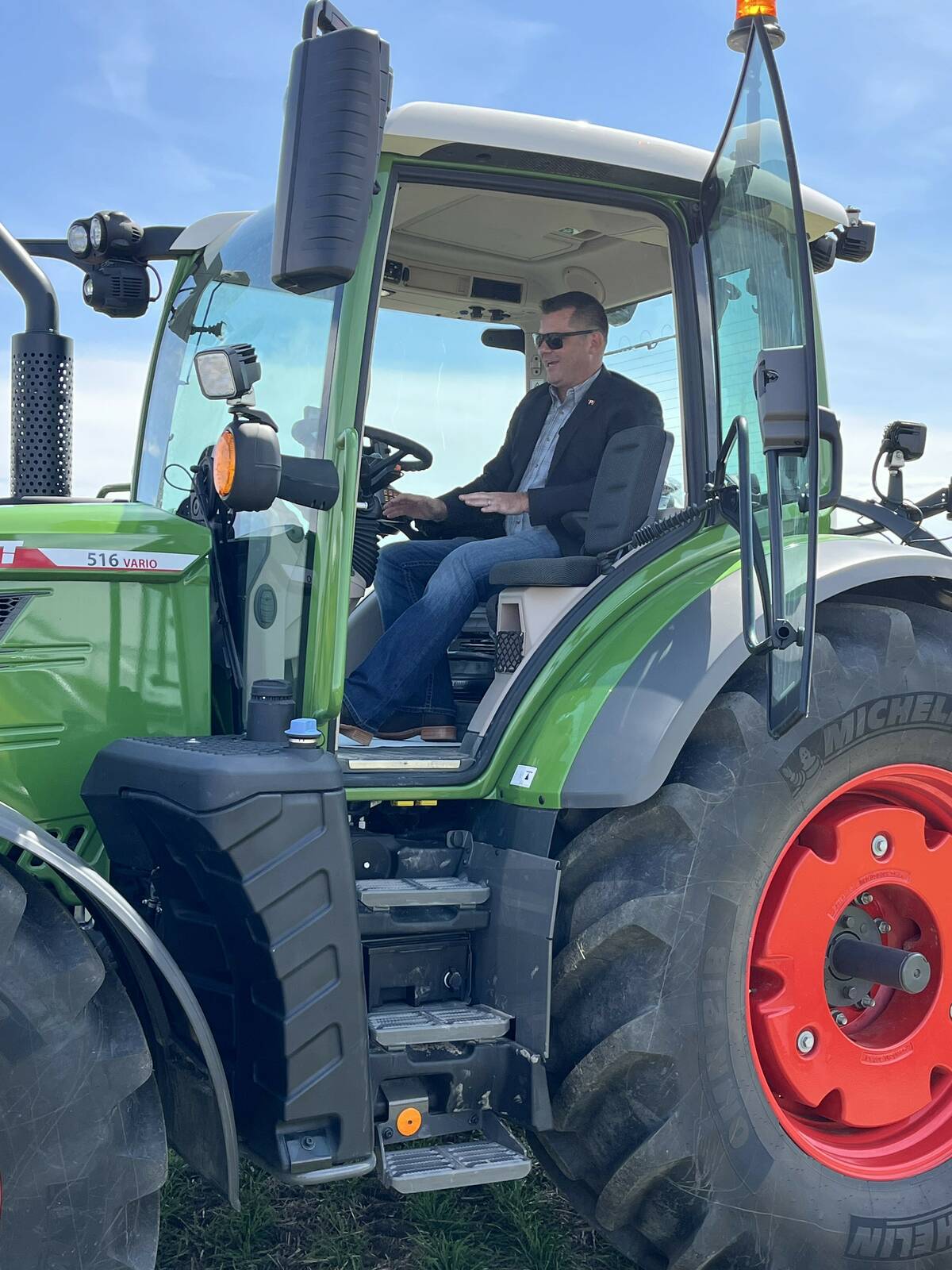
Farming Smarter receives financial boost from Alberta government for potato research
Farming Smarter near Lethbridge got a boost to its research equipment, thanks to the Alberta government’s increase in funding for research associations.
Many angles need to be explored, and it’s not likely anyone will have a firm conclusion in the immediate future. However, one researcher at the University of Manitoba is delving into the manure-fertilizer aspect of the question.
Matthew Wiens, research associate in the university’s plant science department, has been studying the use of liquid hog manure to fertilize forages in beef production systems. He studied energy use and also the relative efficiency of that energy in a hog-beef system.
The study, which Wiens explained at a recent U of M plant science seminar, measured the energy used in beef production systems that employ liquid hog manure as a fertilizer source.
He also checked the efficiency of such a system by measuring the amount of beef produced for each unit of energy input.
This wasn’t a computer modeling exercise. Wiens conducted the research on a Manitoba farm that was interested in much the same question he wanted to study.
The Hytek hog operation at La Broquerie, Man., raises feeder hogs and cattle and applies liquid hog manure to grazing and hay land.
Hytek wanted better information on how to make the best use of the manure it gets from the 25,000 feeder hogs that run through its barns each year.
The barns are typical for the Prairies, with a 10,000 hog capacity and 2.5 cycles per year. They produce 6.5 million imperial gallons of hog manure a year. Phosphorus content is the factor limiting how much manure can be applied per acre.
In the case of this particular location, Hytek was able to apply 7,257 gallons of manure per acre to the target forage stands, which is roughly the equivalent of 110 pounds of nitrogen per acre.
Like many hog producers, Hytek wanted information on how best to manage the combination of hog manure and beef production.
Because the Hytek barns and surrounding fields so closely resemble other hog-beef scenarios, researchers from the U of M animal science and plant science departments had already been using them for other research.
Wiens explained that energy inputs are nearly always tied closely to dollars spent. Producers cannot expend energy to do work or grow food without spending money. However, to simplify the study, he concentrated solely on energy – how much energy was used to create a certain amount of food.
Specifically he focused on megajoules, the unit most commonly used in energy studies. It’s small – one MJ is about the amount of energy used to produce and transport an ounce of urea fertilizer to a farm.
Wiens looked at a grazing system and a haying system, with both systems taking their liquid hog manure from the Hytek lagoon and transporting it to forage fields in the immediate area surrounding the barns.
The average haul in the study was 1.125 miles. Because of high energy requirements in moving liquid manure, distance is always a major factor in a manure-fertilizer equation.
As a control, Wiens also documented energy input and output in both grazing and haying systems that did not receive manure or other fertilizer.
“The manure was applied to a perennial forage stand and then either baled in the haying system or grazed in the grazing system,” Wiens said in his presentation.
“For the energy study two different manure application systems were analyzed. A drag hose system was used for the hay system because it seems that this has become the more common manure application system for hay. And a slurry wagon system was used for the grazing system, since getting in and out of fenced off paddocks is easier with wagons than with drag hoses.”
Wiens used a combination of direct measurements and extrapolated data to get a handle on energy inputs.
Documented energy inputs for the haying system include manure spreading with a drag hose, hay cutting, hay baling and hay hauling. Total energy expenditure for producing 5.3 tonnes of hay per hectare was 3,228 MJ per ha.
Documented energy inputs for the grazing system included manure spreading with a slurry wagon, fencing and watering. Total energy expenditure in the grazing system was considerably less at 2,279 MJ per ha because there were no baling costs.
“The grazing system harvested the forage using only 75 percent of the energy of the hay bale system because we did not have to start up any tractors to make hay,” he said.
On the control haying system, Wiens measured only cutting, baling and hauling because there was no fertilizer factor. Energy consumption was 424 MJ per ha. On the control grazing system, he measured only fencing and watering. Energy consumption was 93 MJ per ha.
“Energy input included not only all the fuel that was consumed, but also all the energy embedded in the equipment. Embedded energy is all the energy to produce the raw materials and manufacture the equipment,” he said.
“As you account for every piece of equipment involved, it starts to add up, but … nevertheless, fuel use consumes by far the largest proportion of the energy. About 90 percent of the energy use is fuel consumption. Only 10 percent is embedded in the equipment.”
Growing conditions in the first two years of the study were not typical, he added. There was too much rain in 2005 and then drought in 2006. With more typical weather, production could be expected to be higher, which would mean more energy use.
Energy output was measured as live weight gain, which was measured in the grazing system. In the hay system, yields were measured and converted to live weight gain with a feed-to-gain ratio of 8.7 lb. of hay for each lb. of gain.
“The story with energy output has a similar pattern to energy input. Where manure is applied, energy output is higher than where no manure is applied,” he said.
“Energy efficiency is where we get to see how the improved productivity with manure measures up in terms of output per unit of energy. We compare weight gain per MJ of energy input.”
This part of Wiens’ study looked at how many MJ are used to put one kilogram of available nitrogen in the ground.
In the grazing system and the haying system, it takes less than 18 MJ of energy to put one kg of available nitrogen in the ground.
With banded anhydrous ammonia, it takes nearly 55 MJ of energy. With broadcast urea, it takes more than 76 MJ.
“If we look at how much energy we use to provide nitrogen to our crops, we see that hog manure is much more efficient than chemical fertilizer,” Wiens said.
U of M researchers have been studying the impacts of hog manure on forage productivity and the long-term impacts on soil nutrients.
For more information, contact Matthew Wiens at 204-803-0881 or mattj wiens@yahoo.ca.
What is a megajoule?
The word joule is showing up more in agriculture research because it represents an exact way to measure energy in all stages of food production. The joule can be applied to diesel fuel, nitrogen fertilizer, a bowl of oatmeal or a cow grazing on a pasture.
The joule is a unit of measurement that defines the relationship between heat, electricity and mechanical work, as first unraveled by James Prescott Joule.
One joule is the amount of energy required to lift one kilogram to a height of 10 centimetres. One megajoule equals one million joules.
Here are some real-world comparisons:
One megajoule equals:
- The work done to produce power of one watt continuously for one second.
- 0.278 kilowatt-hours or the amount of energy your desktop computer uses in two hours.
- The amount of energy required to produce and transport 29 grams of urea fertilizer to your farm.
- The energy contained in 30 millilitres of gasoline. Looking at it from a different perspective, one litre of gasoline contains 34.6 MJ of energy. It takes five MJ to extract, refine and transport that one litre of gasoline to the pump.