Container shipping is an integral part of the business for many farms and agricultural operations in Western Canada.
Without containers, they wouldn’t be able to operate.
Can-India Pulses International operates a pulse processing and lentil splitting plant in Zealandia, Sask.
“We’re in the process of trying to figure out how we’re going to load two containers at one time. It’s going to run 24 hours a day and one line puts out 3.5 tonnes per hour, so there’s going to have to be a lot of movement,” said company spokesperson Joseph Perault.
Read Also
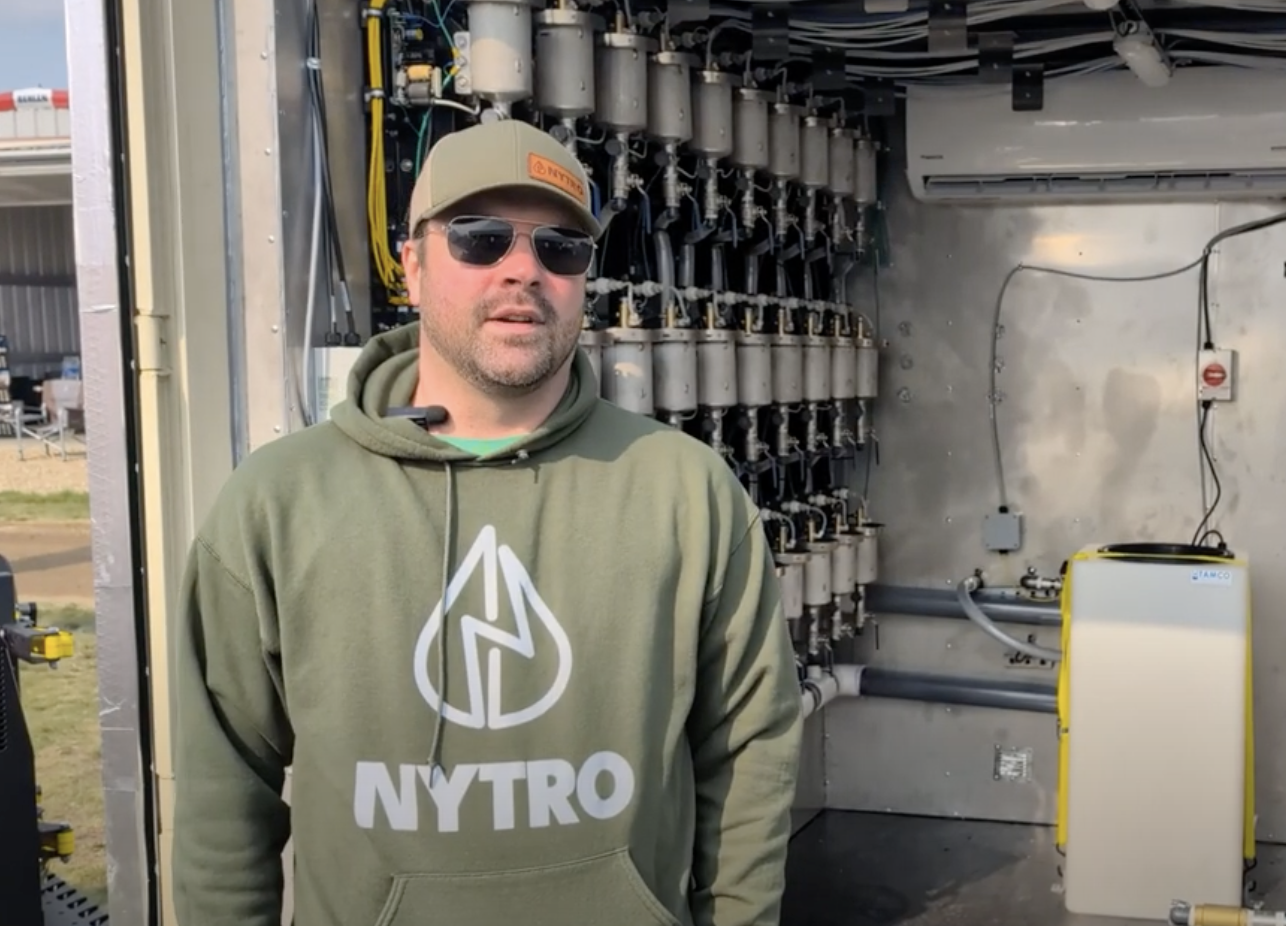
VIDEO: Green Lightning and Nytro Ag win sustainability innovation award
Nytro Ag Corp and Green Lightning recieved an innovation award at Ag in Motion 2025 for the Green Lightning Nitrogen Machine, which converts atmospheric nitrogen into a plant-usable form.
“We also have customers that want whole lentils, so there’s always going to be a lot of container action around here.”
Perault said nearly all the company’s production goes out by container. Can-India recently built a 1.2 metre high ramp for loading containers, using conveyors. He said loading them on the ground is definitely an option for pulse processing plants such as his.
While he hasn’t seen how the Can-Jack works, he said a system that would allow him to load containers on the ground might be of interest.
“If you’re using forklifts to load pallets, or whichever way to handle them, (loading from the ground) makes it a lot more viable,” he said.
“It would save us a lot of work and other expenses. Things like spitters are $20,000. Nothing comes cheap.”
Alex Galarneau is an organic farmer and processor who operates Prairie Heritage Seeds in Radville, Sask.
Galarneau sells organic products overseas and typically ships three or four containers a day in the busy season. About 85 percent of his production moves by container.
“We live load them on trucks, so the truck stays. When we’re doing bags, we forklift the bags into the container with a pallet, then hand bomb them in,” Galarneau said.
“If it was ground level, we could just drive the forklift right in. That’s the advantage I see. There’s a lot less handling and you could do it at your leisure.
“There’s another advantage of off-loading containers. If there’s a shortage of containers, you can store a few in your yard, then load them when you want.”
Ideally, Galarneau would prefer to load containers on his own schedule.
“Give us a day so we can spread out the work. When we’re loading bags, we’ve got 1.5 hours to load that container by bag. We have to hustle, get it done and get it out of there.”
Galarneau said if he could, he’d rather see 10 containers delivered and dropped off, have his employees load them when they choose and then have the containers picked up at a later date.
He said a dedicated container loader that would be able to lift and lower a full 48,000 pound container would be expensive.
“You’re talking $80,000 for a well worn out, used one that’s not dependable,” he said.
“The other thing, too, is safety. How safe is this thing? I just stopped one of my guys from putting his hand in between a hopper car wheel and a steel rail. There was some grain on the track they were trying to sweep off and he had his hand in there.”
Galarneau said loading at ground level would be an improvement over the current system he uses to load containers.
“Having said that, we’re going to be digging out a hole to build a dock. We’ve got a natural hole at the back of our warehouse. We’ll back them up there, open a door and we’re at ground level,” he said.
“We’re also looking at buying some chassis to rotate them. A truck comes in, leaves a container with a chassis, hooks onto a full one and takes off.”
When contacted a month after Can-Jack was introduced, Galarneau said he was already aware of it and was considering whether it might work in his operation.
“I looked at the product and the only questions I have are, how quick it is to attach and can a guy do it by himself,” Galarneau said.
“I’m not even there at the price yet. I’m looking more on how easy it is to work. If one guy could put those legs on himself, in a reasonable time, I’d be interested.
“If they could make a frame and connect them all together so the truck just goes in between them, that would help. It’s a new idea but it has good potential.”
The Can-Jack system doesn’t work for everyone.
SeedHawk manufactures air drills at Langbank, Sask. In the past two years, the company has been selling and delivering air drills to Russia in containers.
“We can ship a 40 foot seeder with a 400 bushel tank in one 40 foot high-cube container. But to do that it’s a jigsaw puzzle to get it all in there properly,” said SeedHawk president Pat Beaujot.
“We had to be able to load the container in two hours or we pay demurrage on the truck. And in Russia, they don’t have forklifts, wheel booms and all that. They want to be able to set the container on the ground, hook on with something and pull the contents out.”
SeedHawk bought flat deck trailers that aren’t roadworthy, added a skid plate and set them up to bolt all the parts of each drill directly onto the decks. Then they put a hydraulic winch on the trailer.
“When the container comes, we use the jack on the front of the flat deck to line it up the right height with the container, then winch it into the container with hydraulic winches. So when the container gets here, we’ve done all our work and just have to slide everything in. We’ve got that process working and when a container arrives, it takes 15 or 20 minutes to load it,” Beaujot said.
“If you want to drive in and out (of the container) with a forklift and load it one pallet at a time, I could see that being pretty slick. It’s easier to work on the ground than up on a flat deck. But for what we’re doing, we’ve found a way to do it now that works for us.”