FARGO, N.D. – Mathews Company representative Michael Larson says his firm’s dryer offers two attractions to farmers – fuel savings and immediate grain cooling.
He said this was achieved by MC engineers in Illinois working with Mother Nature rather than trying to harness her.
The highest capacity unit of the Vacuum Cool Tower Dryer from MC is 4,000 bushels of grain per hour. The unique design is capturing attention by slashing fuel consumption 30 to 40 percent while simultaneously cooling grain before it’s binned.
For farm-scale operations, the MC Vacuum Tower dries 1,400 bu. an hour and costs $110,000 US. It measures 10 feet in diameter, stands 60 feet high and requires concrete pilings to keep it in place.
Read Also
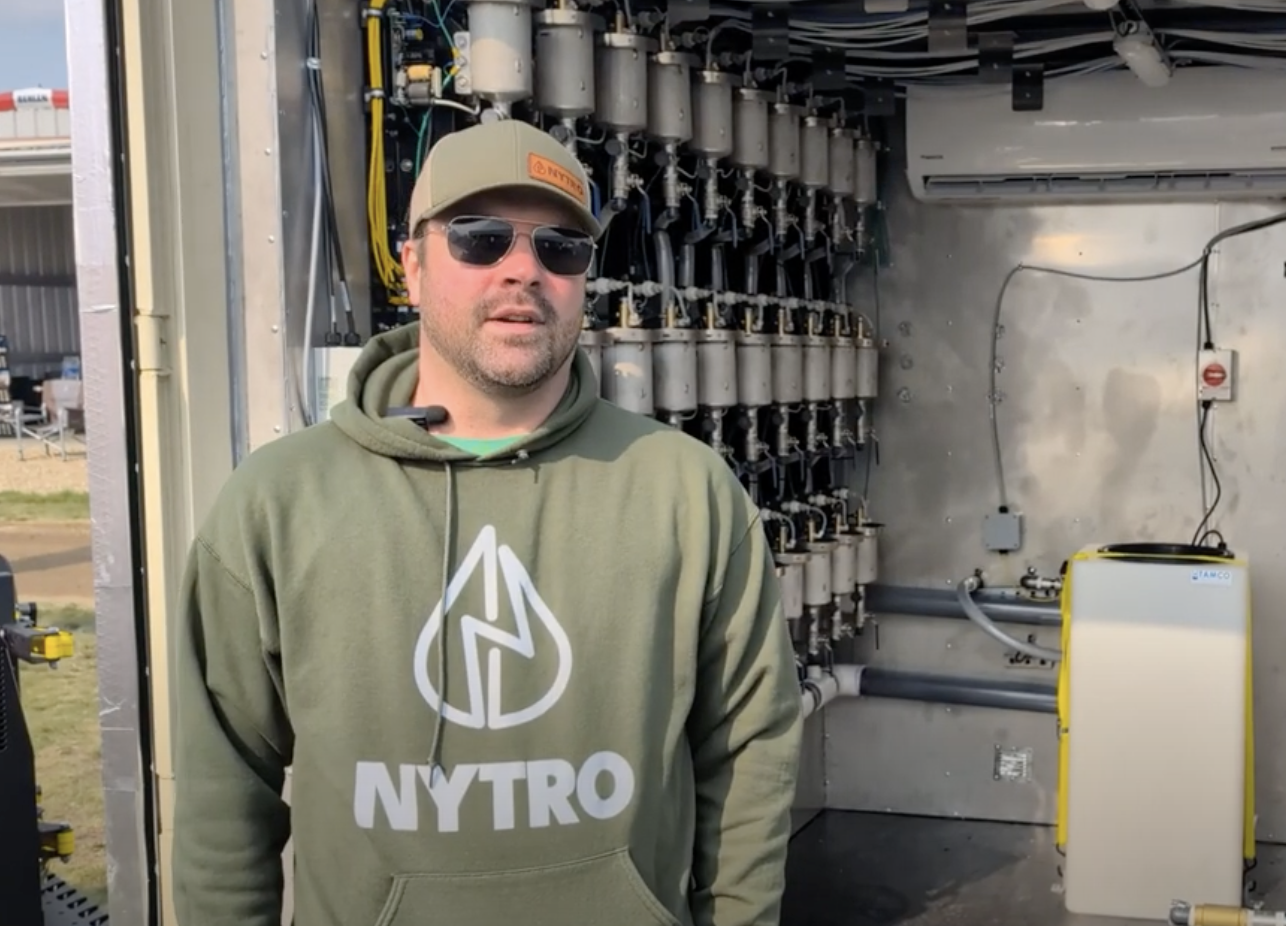
VIDEO: Green Lightning and Nytro Ag win sustainability innovation award
Nytro Ag Corp and Green Lightning recieved an innovation award at Ag in Motion 2025 for the Green Lightning Nitrogen Machine, which converts atmospheric nitrogen into a plant-usable form.
For smaller farms, the basic dryer handles 560 bu. an hour and costs $65,000 US.
Larson explained why the tall rocketship shape is necessary.
“The wet grain is in the top two-thirds of the tower. That’s the only section that gets heat. The burners are just below, blowing heat up to wet grain.
“So it’s only natural that the driest grain is at the lowest level of this dryer compartment. When we want to transfer this dry grain down to the cooling compartment, we let it gravity feed from the floor of the drying section down to the cooling section.”
The gravity flow is controlled with a rotating sweep system at the bottom of the drying compartment. The rotating sweep receives all instructions from the Nema IV microprocessor panel, which can be located right at the tower or hundreds of feet away.
Sensors in the drying section know when the lowest level of grain has reached the temperature and moisture content set by the operator.
Sensors talk to the computer, which then decides how many bushels the sweep should send down to the cooling section on that particular round. The sweep is always rotating, sending some grain down for cooling with movement depending on how fast the cooling occurs.
The microprocessor can instantly dial up any sweep speed, and thus any grain volume to be dropped into the cooling chamber.
Larson said it’s necessary to calibrate the microprocessor at the beginning of harvest season. When there are major changes in weather or harvest conditions, it needs to be calibrated again.
“You manually set it up at the start, (of the run) with air temperatures, moisture content of grain coming in, air temperatures, humidity and things like target moisture content you want in the bins.
“Then you move to automatic mode. Six sensors up in the drying tower continually take their readings and send data down to the microprocessor.
“As incoming grain gets warmer and drier during the heat of the day, the microprocessor stays informed and speeds up the sweep. Later, when incoming grain becomes cooler and damper, the microprocessor tells the sweep to slow down so grain stays in the heated chamber longer.”
The microprocessor also controls the intake at the gas manifold so plenum temperatures remain at the level set by the operator, regardless of outside temperatures.
Larson said the lower third of the tower is the cooling section and it is located below the burners. No heat transfers from the burners down to the cooling section.
“Instead, we take the heat we extract from warm grain just deposited in the cooling chamber and we channel it back up to the top drying chamber. We call the whole process reverse cooling.”
Reverse cooling is the point where the vacuum principle enters the scene, although it is not a true vacuum.
To supply combustion air for the burners and fresh dry air for the fans to blow up into the heated chamber above, the tower sucks in outside air through the bottom of the dryer floor.
“Fire in the gas burners requires oxygen. The bigger the fire, the more atmospheric air it sucks up through the floor. This is the vacuum effect.
“When pulling fresh atmospheric air up through the warm dry grain that was just dropped into the cooling chamber, we quickly cool that grain. It’s reverse cooling.
“And that process creates warm air. Air pulled out the top of this grain pile is now (4 C) degrees warmer than when it was pulled in. In effect, we reclaim (4 C) of temperature. It’s free heat because you need to run the fans anyway for wet grain in the top chamber.”
Larson said that if this heat accompanied grain into the bin, it could cause immediate moisture problems. It would cost energy and fan time to aerate those bins and waste the heat off into the atmosphere.
“The Vacuum Cool Tower Dryer puts that heat back to use to dry the next bunch of grain coming down the dryer tower.”
Larson explained a typical scenario in which the ambient outside temperature is -1 C.
Reverse cooling adds another 22C to air coming out the top of the cooling chamber. The temperature going up into the drying chamber is now 21 C.
“If we’ve got our dryer set at (93 C) and we have (-1 C) outside, then we need to make up(94 C) of heat with our burners.
“But with reverse cooling, we’ve got this extra (22 C) of recaptured heat available to us. So now we only need to make up (72 C) of heat.
“In real life, on farm conditions, this system cuts fuel consumption by 30 to 40 percent.”
Larson said bringing the grain temperature down before it goes into the bin allows farmers to ignore their aeration obligations for a while so they can concentrate on the harvest at hand.
In some conditions, grain that augers out of the MC cooling chamber is already at a temperature low enough for long-term storage. Less aeration means less hassle and further reductions in energy consumption.
Larson has one word of caution: “The system works well in grains with lots of air space between kernels. Things like wheat and corn.
“But on crops that pack tight and have high static pressure, it just does not work. Don’t try it. It will not work on canola or flax because the air will not pass freely between those seeds.”
For more information, call Michael Larson at 815-342-1492 or visit www.mathewscompany.com.