WINNIPEG – A new farm in the west Arizona desert is engineered to be a self-contained energy island. It does not rely on outside fossil fuel or electric energy, so its products have a substantially lower break-even cost.
When it swings into full production later this year, the XL Biorefinery is expected to house 7,500 dairy cattle, which will produce 24 million gallons of milk annually for the market in nearby Phoenix.
But milk production is actually secondary to energy production at this farm. Products normally considered byproducts are the primary sources of income.
Read Also
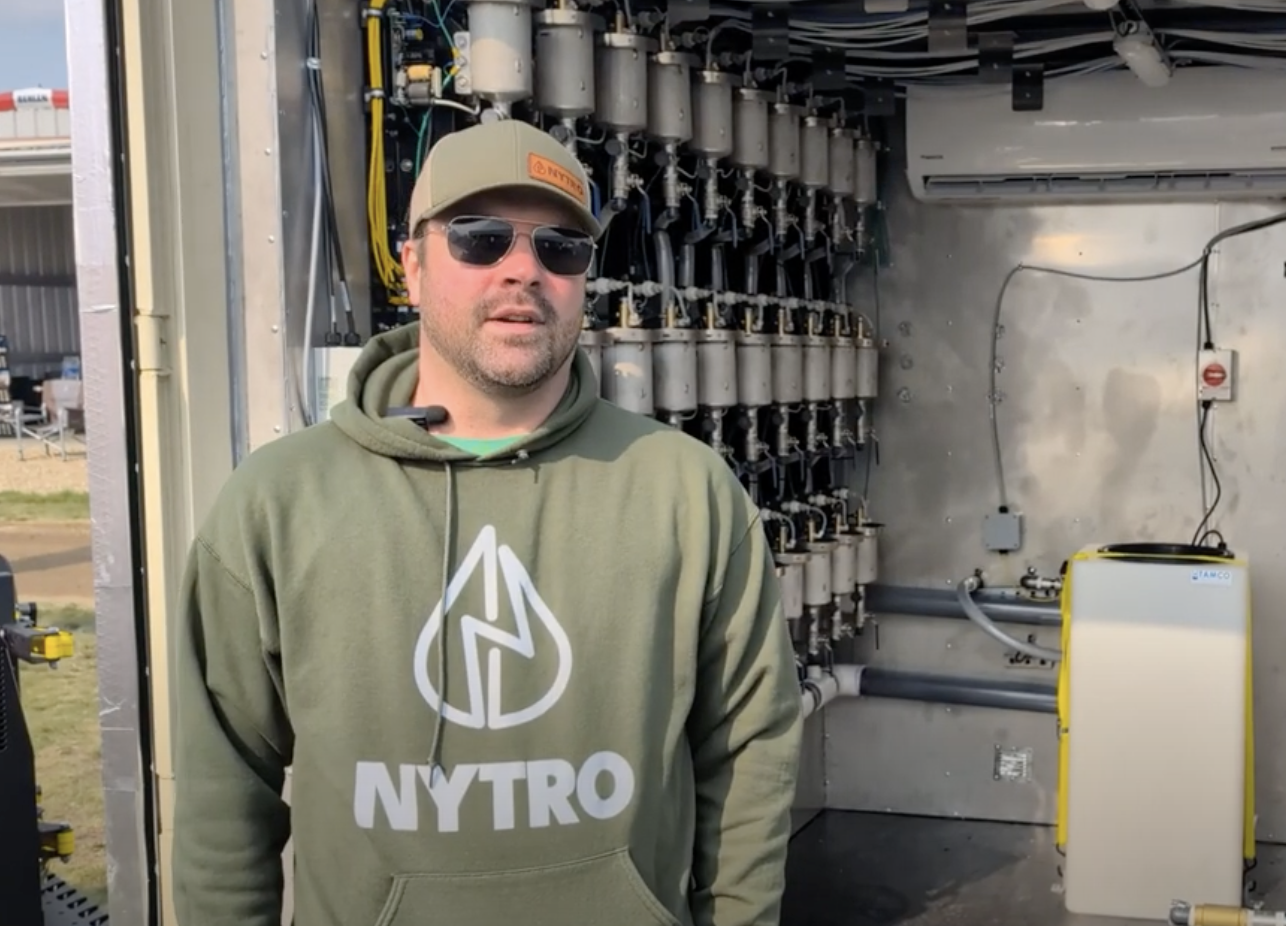
VIDEO: Green Lightning and Nytro Ag win sustainability innovation award
Nytro Ag Corp and Green Lightning recieved an innovation award at Ag in Motion 2025 for the Green Lightning Nitrogen Machine, which converts atmospheric nitrogen into a plant-usable form.
In addition to milk, the energy-integrated XL Biorefinery farm has nine other products it sells each year:
- Denatured ethanol (50 million gallons US).
- Biodiesel (five million gallons).
- High protein distillers grain (100,000 tonnes).
- Grain corn bran (40,000 tonnes).
- De-oiled germ cake (48,000 tonnes).
- Carbon dioxide (145,000 tonnes).
- Carbon-balanced compost (4,700 tonnes).
- Bull calves (3,500).
- Heifer calves (2,800).
The strategy brings together the energy consumption and energy production components from each part of the farm.
The farm works on the premise that a cow is inefficient at using the energy from a bushel of corn and that wastes potential profits.
In contrast, highly manipulated extraction, called fractionation, can capture more energy and more potential profit.
“I’ve often thought we could use a dairy cow that produces more manure and less milk,” said Thomas Byrne, XL project manager and chief financial officer for the business. “In terms of energy, the waste is worth more than the milk. Dairy waste, especially, has a very high energy rating.”
Byrne said that in contrast to Mother Nature’s biological digestion in the cow, synthetic extraction can capture more energy and more potential profit from the same bushel of corn. The process is called fractionation.
The plant buys about 510,000 tonnes of corn annually, mainly from the midwestern states. At the on-site fractionation plant, the corn is broken down into cornstarch, corn bran and corn germ. Corn germ and corn bran are non-fermentable.
Corn germ is pressed to separate the oil, leaving germ cake. Germ cake is a quality livestock feed that goes into the XL dairy operatons or it is sold to nearby livestock operations.
Corn oil goes to the on-site biodiesel plant, where it contributes to the production of biodiesel fuel and also to glycerol, which helps fuel the on-site energy plant. Corn oil can also be sold into the edible oil market.
Cornstarch goes into the on-site ethanol plant, and contributes to the cash flow of the operation.
Corn bran is separated and sent to the energy plant where it supplements the methane fuel from the dairy herd. Some of this electricity then feeds back power to the fractionalization mill.
With corn going through the fractionation process as it arrives, cows eat only feedstocks that are tailored to their dietary needs.
As well, the XL farm funnels the manure generated by the dairy herd into an on-site energy plant that can meet all of the farm’s needs.
Even with all the additional processes, the dairy component remains important. The cash flow generated from the 24 million US gallons of milk is significant.
According to the company website, the XL strategy recognizes that a constant supply of high quality milk depends on a constant supply of high quality feed for the herd. The cattle depend on a blend of distillers grain and germ cake produced on-site.
As corn goes through the fractionation process, each kernel is separated into distinct components, which are moved into their own bins.
This allows XL nutritionists to give their dairy herd precise feed rations for optimal production. It also lets XL sell precise feed blends to other livestock operators.
The fractionation mill leaves about 25 percent of the corn oil in the germ cake, creating a high energy value feed.
Although equipment is available to extract more oil and leave less in the feed, the company maintains a higher oil content in the feed to provide better quality feed to the dairy cattle.
The distillers grain byproduct is also important to the feed operation. By processing the refined starch into ethanol, the remaining distillers grain has a higher protein and lower fat content, both of which are desired by local livestock operations.
The ethanol plant can produce more than 54 million gallons of ethanol on the same supply of 510,000 tonnes of corn, but higher biofuel production would diminish the feed quality of the distillers grain.
Instead, XL has cut the ethanol plant production back to 50 million gallons per year.
Byrne said it’s a continual balancing act that can be adjusted as market conditions change.
The ethanol industry as a whole does not have a high efficiency rating using the conventional dry-grind system for converting corn to automobile fuel. Ethanol production sucks up a lot of power, with energy cost the second most expensive input behind corn.
However, the technology developed by XL has a precedent-setting energy efficiency ratio of 10 to one. That means that every BTU of fossil fuel that feeds into the XL system creates 10 BTUs of salable energy.
“That ratio is only possible because we use waste from all the operations on the site. And we don’t burn any energy drying down the grain,” said Byrne.
The ethanol plant provides an obvious cash crop, which only needs to travel about 150 kilometres to the lucrative Phoenix market.
It also turns out distillers grain for on-site livestock and for sale to local markets, such as dairies and poultry operations.
Plus, the ethanol plant produces thin stillage which is consumed by the energy plant.
The project aims to show that energy self-sufficiency on a large scale is possible. The on-site energy plant uses waste and low value products to create energy.
According to the plan, the facility will reduce the cost of milk production by 50 cents per hundredweight, reduce the cost of ethanol production by 30 cents per gallon and save the farm an estimated $16 million per year in energy costs.
One hundred percent of the electricity, heat and steam for the facility is produced by the plant, which includes a methane digester, biomass boiler, steam turbine generators and backup generators.
The energy department receives liquid manure from the dairy and thin stillage from the ethanol plant. These are converted to natural gas in the methane digester. This methane gas fuels the boiler system and generators.
Manure solids from the dairy, glycerol from the biodiesel plant and corn bran from the fractionation plant are all fed into the biomass boiler to create 155,000 pounds of steam per hour to power the ethanol process.
The biomass boiler also yields ash, which is then composted with manure to create a marketable organic fertilizer.
To ensure a constant supply of steam and electricity, the back-up boiler can be fueled by any combination of methane, corn oil or off-grade biodiesel.
The sunbelt of western Arizona and southeastern California could become a centre for algae-based biorefineries managed in conjunction with livestock operations, according to the XL website.
Algae use a photosynthesis process similar to that of higher developed plants such as corn.
However, the algae make more efficient use of sunlight so they grow quickly.
Corn contains approximately 68 percent starch, four percent oil and 20 percent proteins.
Algae contains only 50 percent starch, 25 percent oil and 20 percent protein. This means that one pound of algae will produce less ethanol and more biodiesel than a pound of corn.
The company has developed a low-cost system for large volume production of commercial grade algae. When the patented algae go into production next year, XL plans to produce it at a cost less than $100 per tonne.
Carbon dioxide and fertility water from the methane digester will feed the 2,400 acres of algae fields adjacent to the XL Biorefinery beginning in 2009.
Photosynthesis converts the carbon dioxide to oxygen, resulting in rapid algae growth. Algae will be processed on-site into biodiesel, ethanol and livestock feeds.
Because carbon dioxide is a main contributor to greenhouse gases and global warming, the algae farm is viewed as environmentally friendly.
The farm employs 175 full-time staff.
For more information, visit www.xldairygroup.com.