Parts of the Prairies are wet this spring while others are dry. In other words, it’s a typical prairie spring.
How do these extreme wet or dry conditions affect the way farmers make their tractor tire adjustments?
Reed Turner, a recently retired engineer with the AgTech Centre in Lethbridge, says making adjustments for optimal tire performance is much the same for either condition.
“The same factors that provide optimum efficiency in dry conditions also provide the best flotation in wet conditions,” he said.
Read Also
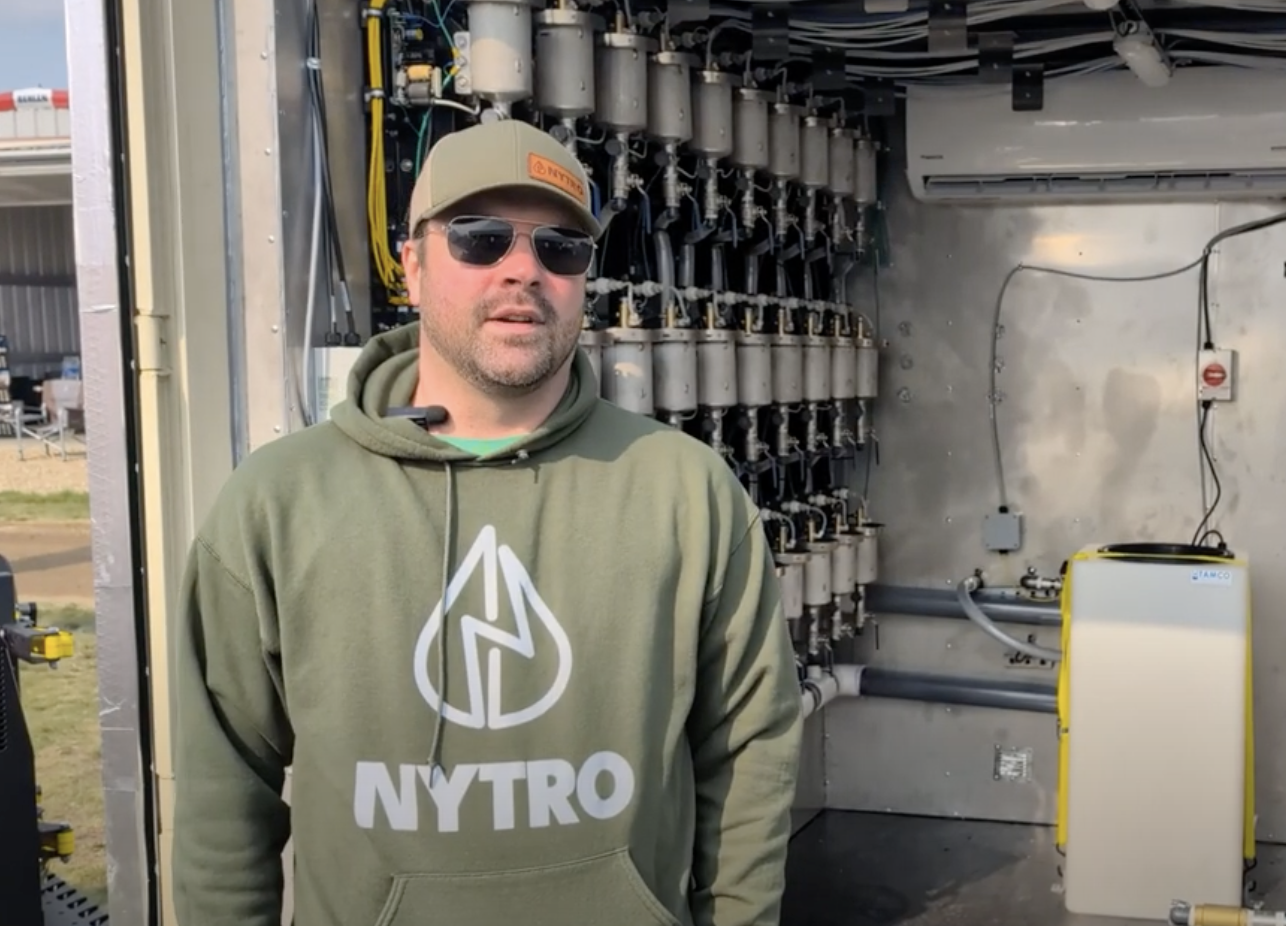
VIDEO: Green Lightning and Nytro Ag win sustainability innovation award
Nytro Ag Corp and Green Lightning recieved an innovation award at Ag in Motion 2025 for the Green Lightning Nitrogen Machine, which converts atmospheric nitrogen into a plant-usable form.
“Those factors are low tire pressure and a wide footprint. The only thing you might consider changing for wet conditions is less ballast. If you take weight off, you can go down with air pressure and get a wider footprint. Six psi is the lowest you should consider.”
Turner said removing ballast is a nuisance and a producer might not put the ballast back in when conditions dry. Also, lower ballast limits how much producers can pull.
The ideal setup is for seeding equipment to weigh 40 percent of the tractor’s weight. For example, a 30,000 pound tractor should pull a 12,000 lb. implement.
In areas that are muddy most years, Turner said producers might be able to finish seeding earlier if they use a lighter tractor with a smaller seeder.
In an Alberta AgTech Centre report published two years ago, Turner said most producers reach the upper limits of their tractor’s power only 10 to 20 percent of the time.
With diesel prices increasing, it makes sense to ballast a tractor for typical conditions rather than extreme conditions.
Turner said excess ballast is the most common error. An overballasted tractor will feel sluggish, burn excess fuel and be more prone to early drive train failure.
“Most guys want to ballast for their worst situation, but that might account for only 10 percent of the work, with the tractor weighing too much 90 percent of the time.”
He said an underballasted tractor wastes fuel and cannot deliver full horsepower to the drawbar because of tire slippage.
“It’s very rare that a guy changes ballast. Once it’s done, it’s done. That’s why it’s so important to get it right the first time,” he said.
“On a good day, about 70 percent of the power delivered by the engine translates into power at the drawbar. Tires are the conduits through which that power is delivered to the ground. How efficient that delivery is depends on the condition and inflation pressure of the tires.”
Turner said farmers who consider buying new tires for their tractor should ask themselves if they really need them.
“If you’re in a dry zone and your tires still hold air, you probably don’t need to buy new ones,” he said.
“Tests we’ve conducted in dry conditions prove that tires which are nearly worn out are more efficient than brand new tires. What do you see when you go to a tractor pull? It’s dry, so they run tires with no lugs, yet they generate tremendous pulling power.”
Turner said farmers definitely need lugs when they encounter mud because it’s the moisture in the ground that limits a tractor’s ability to float. However, lugs do consume fuel.
“If it’s really muddy, you shouldn’t be in the field anyway. You can’t do a good job of seeding. The air seeder sinks. You have no depth control. You rut up the field. You break equipment and you’re going to get stuck no matter what tires you have.”
Turner said air pressure affects fuel economy, performance and tire wear, but farmers often overlook its importance.
“People don’t check tire pressures. They’ll check the oil every day but only check tire pressures once a year,” he said.
“Or they check one and then assume the other three are OK. With duals, they might check the easy tires and leave the insides because it’s too hard to get at them. It’s even worse with triples.”
While a radial tractor tire is six to eight percent more efficient than a bias ply tire, the radial requires better management and closer attention to inflation.
Radials should be inflated to the lowest pressure allowed by the manufacturer for the load they will carry.
Highly accurate gauges are critical for tractor tires. A gauge that is off by two lb. per sq. inch on a tire that is ideally filled to 30 psi is less of a problem than it is for a tire that holds 10 psi.
He said a 20 percent error is not acceptable and hurts field performance and fuel economy.
Turner recommended removing additional tires if they aren’t required in the field.
“Typically, when fields are dry and traction is good, the more tires you add, the less efficient your tractor is. Duals are worse than singles and triples are worse than duals. Farmers should stay away from triples. If that much flotation is needed, larger radials installed as duals are more efficient than smaller tires installed as triples.”
But what about those Trelleborgs?
Nearly every farmer who has installed a set of Trelleborg tires says they improved tractor performance.
Trelleborgs have a bias ply style sidewall with a radial ply style footprint. The company says this combination gives higher efficiency and less compaction while eliminating power hop.
Turner is not convinced.
He said when a farmer installs a set of Trelleborgs on his tractor, he is nearly always going to significantly larger sizes.
“It might be that their tractor does actually perform better, but that might be because the Trelleborg they installed is a bigger size than the tire they took off. We (AgTech Centre) tested equal size to equal size, Trelleborgs to radials. There was no advantage to the Trelleborgs. Trelleborgs are not bad tires, but size for size they’re not as good as a radial.”
According to the 1998 report, the Trelleborgs acted like the bias ply tires that they are.
On the positive side, they showed no problems with power hop and could carry weights and transmit torques similar to radials.
On the negative side, they operated at higher inflation pressures than some of the radials, pulled less for the same ballasted weight and were a few percent less efficient.