Heat stroke is a possibility when the temperature inside a grain bin is double the outside summer temperature.
“I took temperature readings in all kinds of bins when we were developing the FreshAir Ventilator,” said
Kevin Perry. “If it’s a sunny day and it’s 30 C outside the bin, you can pretty well expect the temperature inside to be 50 to 60 or higher.
“With this thing, we bring the inside temperature down to within a degree or two of the outside temperature. The ventilator changes all the air every two minutes in a typical 3,000 bushel bin.
Read Also
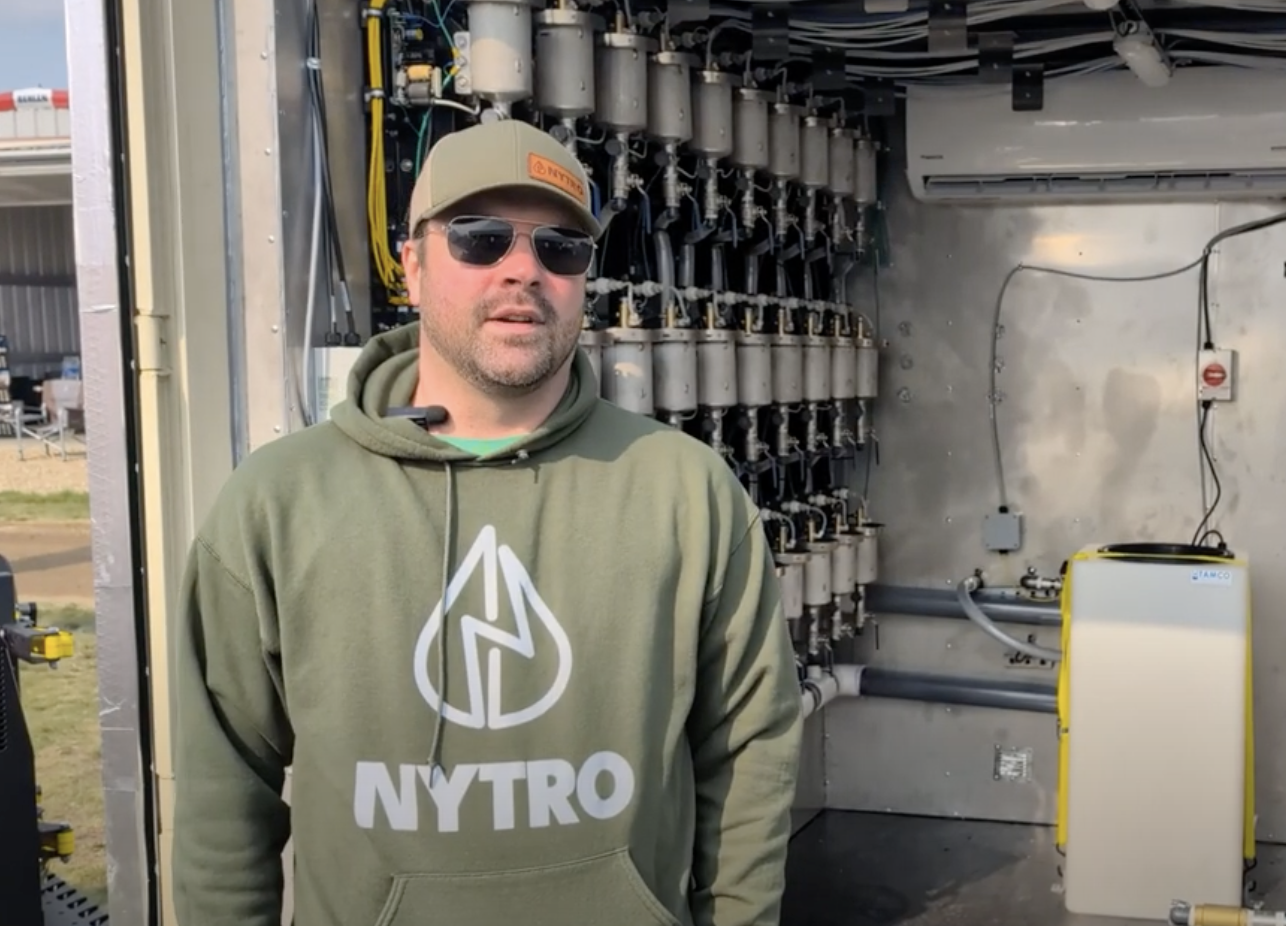
VIDEO: Green Lightning and Nytro Ag win sustainability innovation award
Nytro Ag Corp and Green Lightning recieved an innovation award at Ag in Motion 2025 for the Green Lightning Nitrogen Machine, which converts atmospheric nitrogen into a plant-usable form.
“It’s not just about comfort, it’s about safety and reducing heat stroke,” Perry said.
The FreshAir Ventilator, a 12 volt fan temporarily set in place over the fill opening at the top of the bin, blows fresh air down into the bin while people inside are shovelling, using the drag auger or cleaning the bin.
Perry did the engineering work on the FreshAir Ventilator for his family’s business, Perry Industries in Hawarden, Sask. In the past few years, he has tested the equipment in just about every type of grain bin found on the Prairies.
In addition to stacks of data, he discovered another benefit they had not anticipated.
“You actually feel cooler. Obviously you don’t have the sun beating down on you when you’re in the bin, so that helps. But the surprise for us was how much cooler you feel with that stream of fresh air flowing over your skin. There’s a great deal of evaporative cooling we had not counted on. We often hear that same comment from our customers.”
A growing number of producers refuse to haul grain when the weather is too hot. The risk of heat stroke while working inside the oven-like bins is too great. In severe cases, the results are fatal.
Perry said staying cool is only part of the story. With fresh air blowing in from the top, there is enough positive air pressure inside the bin that the dust is blown out the door, along with the hot air.
“The air pressure inside the bin isn’t enormous,” said Perry. “The main point is that it’s positive pressure. It’s just slightly over 0.1 or 0.2 inches of water gauge. The fan itself is capable of pushing up to one full inch of water gauge if it’s in a restricted, controlled container. But blowing into a big grain bin like this, all we need is enough pressure to keep air and dust moving out the door.
“Air volume is far more important than air pressure in this kind of situation. The fan moves 2,200 cubic feet per minute. This gives the inside operator clean air to breathe, it keeps him cool and it prevents him from becoming caked with dust.
“The air flow is actually moving dust away from the operator. That means it’s also moving dust away from the intake of the person’s breathing filter and that has to have significant health benefits. When I get out of the bin now, I don’t have to go searching for an air hose to blow myself off. I’m clean enough to go jump in my pickup.”
By testing the system in a variety of bins, Perry said a common pattern for the air flow was found. The fresh air moves down toward the operator. When it nears the end of the drag auger, the air turns and pulls the dust and then runs sideways toward the exit door.
The clouds of dust billowing out the door are proof the FreshAir Ventilator is doing the job it was intended to do.
Perry added that the system is also useful when it’s not hot. When the temperature is moderate in the fall and spring, the fan still provides the operator with a good supply of fresh air and keeps the dust away. And, in the winter, when the temperature might be -30 C, the system is just as useful.
“If you’re all suited up with the heavy winter boots and insulated coveralls and lots of sweatshirts underneath, you work up a real good sweat in that bin. You really heat up. When you’re done, you step out into that -30 again, and that’s not good. A lot of our customers tell us they run this thing in the winter and it helps keep their body temperature down.”
A few farmers have been known to turn on their aeration fans while emptying bins in hot weather. It’s not a good practice because they disturb dust that has settled into the bottom regions of the bin.
With the aeration system turned on, the dust is blown up into the air in which the person is standing and out the top. It may provide cooling, but the overall impact on the person in the bin is negative.
Some producers with older style aeration fans will remove the unit and reverse it so it functions similar to the Perry FreshAir Ventilator: it draws fresh air in from the top and extracts dust and hot air out the bottom.
While this may be a viable option with some types of fans, it is time consuming and will not work with most centrifugal fans used for bin aeration.
“When the air flow comes from low in the bin and moves upward toward the face of the operator and then out the top, it creates more problems than it solves. In fact, that’s the situation we inadvertently created with our first version of the FreshAir. We had that one sucking air out the top of the bin. That was a mistake.
“If this was a bin with no seals under the eaves, then it would just suck air from under the edge of the roof-line. If everything was sealed up tight where the roof meets the top of the wall, then we’d end up sucking dust up from the bottom and drawing the dust right over the operator. That was no good. We’ve changed it so now the fan blows into the top rather than suck out the top. The fan now pressurizes the bin rather than trying to depressurize the bin.”
Perry Industries introduced the first version of its FreshAir system last June. These first units were made of steel and weighed 14 kilograms. There was a handle that the operator grasped to carry it up to the bin roof or to tie on a pull rope. About 200 of these early units were sold, and the company still has an inventory of these heavier steel fans for customers who don’t like the plastic upgrade.
Perry said the second version is made of plastic and weighs only nine kilograms. Although it is lighter than the previous steel model, it has outperformed the older steel fan in durability comparison tests. The plastic Ventilator features a back strap so the operator can buckle it on to safely climb the ladder.
Nearly 400 of the newer plastic fans have sold since it was introduced in March.
Because there are some situations when a producer may want to suck air out the top, the FreshAir fans are made so they can be simply flipped over to push air the opposite direction to become extraction fans.
Perry said forming a good seal where the FreshAir mates with the opening is not a problem. The weight of the fan is enough to ensure that no air escapes sideways.
The current version of the FreshAir works on any bin with an opening diameter of 18.5-23.5 inches. Perry said the company is working on an adapter for larger openings.
“To date, we have successfully tested the system on grain bins up to 6,500 bu.,” said Perry.
The fan is a 12 volt, 23 amp unit that comes from California. It’s an outdoor fan designed to run continuously in rain, dust, heat, vibration or extreme cold.
Once the fan is set in place on the opening, the wire harness is tossed down to the ground where it’s connected to a pickup or grain truck, tractor, semi or car. The fan runs a higher volume of air if the support vehicle is idling.
“You should not run your FreshAir off the electrical system on your auger,” Perry said. “It cannot put out sufficient power. You run the risk of burning out both your auger charging system and your FreshAir fan motor. Run it off a vehicle, for sure.”
Perry is the fifth generation on the family farm, so moving grain is not a novelty. Since the family moved into manufacturing, it has concentrated on the business and rented out the farmland.
“But we do a crop share rent, so we’re still hauling grain and handling grain every year. That part hasn’t changed. We still spend our fair share of time working in the bins.”
Perry emphasizes the Perry Industries FreshAir fan is not the same as air conditioning a bin. It won’t make the crew line up to draw straws to see who gets to work in the bins.
“It just makes a nasty job a lot more tolerable and much safer.”
The FreshAir Ventilator sells for $450 and carries a one year warranty.