BIGGAR, Sask. – Richard Elenko values his time when seeding.
Seeding his crops early has multiple benefits, so efficiency is a priority. One area of concern for Elenko was getting timely fills for his air carts without adding manpower. He said it all started with proper crop agronomics.
“Placing phos (phosphorus) with the seed is the optimal place for it,” said Elenko, who farms near Biggar.
“If you blend your phos with your nitrogen and place it with the seed it can get too hot. If you double shoot, you have to put your phos with your blend, away from the seed, if you’re concerned with fertilizer burn on germination, which I am.”
Read Also
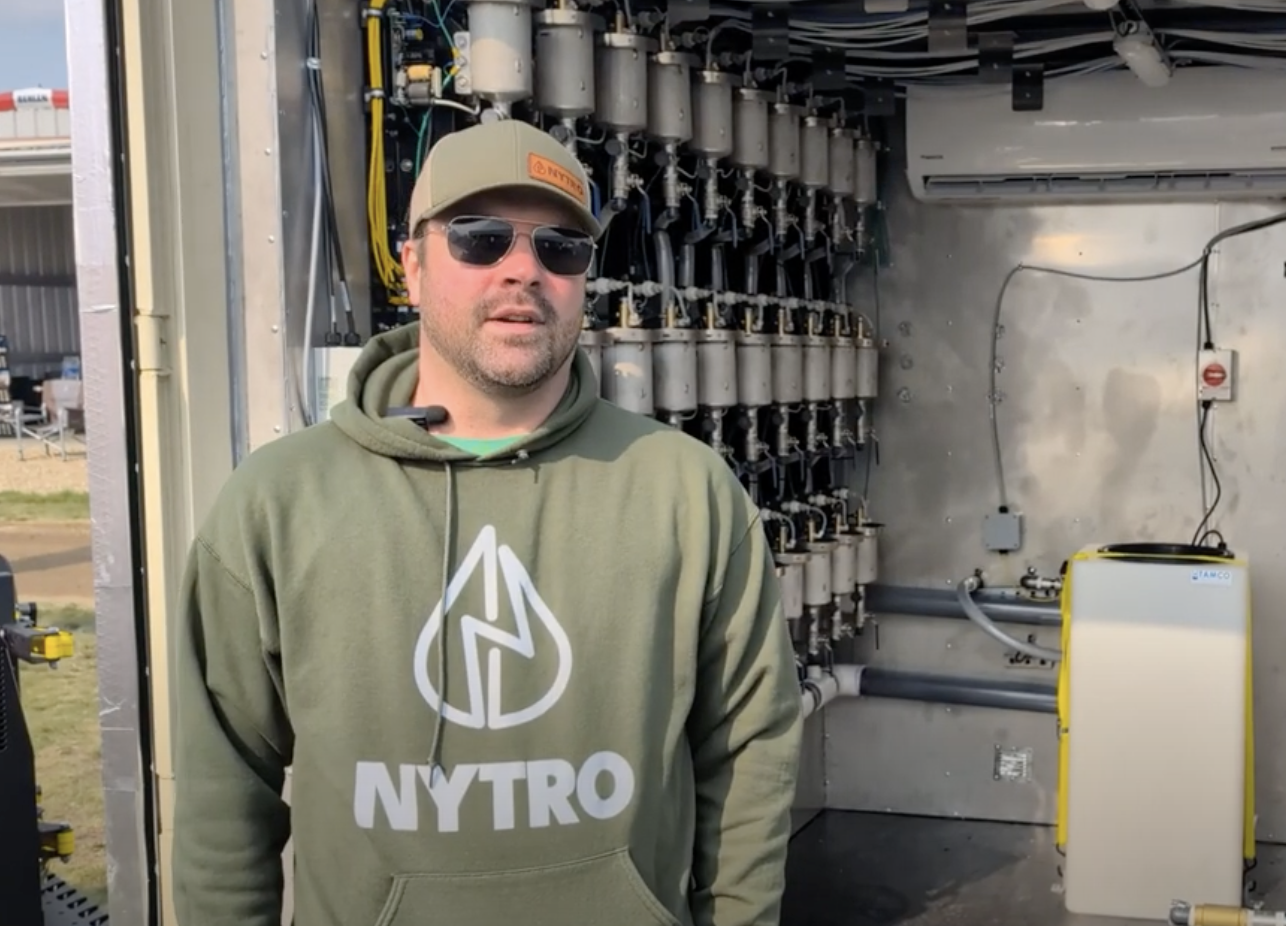
VIDEO: Green Lightning and Nytro Ag win sustainability innovation award
Nytro Ag Corp and Green Lightning recieved an innovation award at Ag in Motion 2025 for the Green Lightning Nitrogen Machine, which converts atmospheric nitrogen into a plant-usable form.
To accomplish this, Elenko had to haul product to the field with three trucks, or two trucks if one had two compartments.
“You’re backing up a cereal grain truck, a phos truck and your nitrogen blend. To load a 440-bushel air seeder took too much time.”
Before developing the four-compartment conveyor trailer that he now uses to deliver seed and fertilizer to his drill, Elenko said he’d be up and down his 12 foot high air cart a couple of times for each truck.
With four compartments on his air cart, it was a minimum eight times up and down for each fill. Often it would be more like 12.
“Then you have the logistics of moving three trucks and getting them all spotted. We’re taking around 45 minutes to fill the unit by yourself. If you’re seeding 38 to 39 acres an hour, you’re losing a lot of time,” he said.
The operator would have to back up each truck and position the auger over the air seeder tank. Then he would need to open the end gate, start the system and climb to the top of the tank.
After filling, he would have to climb back down and shut the end gate.
“We solved all that up and down with electric controls on the end gate and hoist. That was the first phase of what we did on all our trucks. That saved a little time but not a lot.”
Elenko felt the solution was to back up one truck and fill from three compartments.
“Having two compartments in a truck is fairly common,” he said.
“But then you’ve got to have one guy running back and forth to your supply source for product, so you’re back to two men again. That may be fine if you’re nursing two units and you can afford that guy.”
Elenko started thinking about using a trailer with enough capacity for the day, or at least three or four fills.
“So it started from wanting to have three products coming in separately – seed, phos and blend – and enough capacity.”
At that point, Elenko discovered Cancade, a company that builds truck boxes and trailers in Brandon. It was developing a similar idea, but had used a hopper trailer with two compartments. An auger inside each compartment in the trailer extended out the back in a fixed position.
Elenko wasn’t keen on that setup because he felt the inside augers wouldn’t completely clean out the hoppers. After a number of long discussions with company representatives, he eventually built what he has today.
“Using peas and lentils with augers isn’t the best thing to do, even though most guys do because air seeders have augers,” Elenko said.
“That’s what gave birth to the belt concept.”
Elenko and Cancade expanded their discussions to include Convey-All of Winkler, Man.
“We talked about how the design at the back of the machine should be,” he said.
“The auger has to swing. We have a 10-foot arc, because after you back up with it, you have to go from compartment to compartment. You also have to be able to see your (conveyor) when you back up to the air cart.”
Before backing up, Elenko swings the conveyor out to the driver’s side so he can see it. With the hose hanging down, he knows when he’s backed up far enough.
“The first ones they built were rigid, but you can’t back up a trailer over an 18-inch hole without jumping out of the truck half a dozen times. That’s part of the time issue,” he said.
“Then we wanted controls from the top as opposed to the bottom. The prototype with the augers was built with controls on the bottom, but no remote control.”
Elenko’s trailer includes controls at the back, at ground level and a console of switches mounted at the top of the elevation conveyor. All functions can be controlled from the ground or from the top of the air cart.
“We’ve gone through several variations of the remote control. We’re running electric over air over hydraulic. We started with air over hydraulic and were having trouble with that, due to switch issues. Eventually I think a guy could go to electric over hydraulic, but cost is an issue there.”
Upper controls include four switches for the hoppers, a swing toggle, lift, upper and belly conveyor switches, a light and an emergency kill switch, for a total of 10 separate functions.
Each hopper slide can be opened separately with a hydraulic ram. All three conveyors are driven hydraulically. The bottom conveyor runs horizontally and carries product from the hopper chutes to a small transfer conveyor, which lifts the product to the base of the elevation conveyor. It’s set up this way because the elevation conveyor has to swivel in an arc.
Hydraulics come from the truck.
“We run a big pump off the truck. We’ve got a bigger pump than specs call for, about a 35 gpm pump, and we run the truck about 1,450 rpm to run this. We modified the (hydraulic) reservoir on the truck to carry all (the oil capacity) we need for our wet kit.”
To gauge how much the hopper slides are open, Elenko uses a physical indicator system for each chute.
“When you control your gates with hydraulic cylinders, if you open them too much you can overload your belts and plug the system. You need something for the eye to see. We use cables hooked onto a weighted slide in a track (for each hopper). You open it a little bit, then adjust it by watching the inclined belt.”
The system’s efficiency depends on the crop.
“Untreated wheat is difficult to load up that belt. If you slow it down so it doesn’t slide, then it takes too long to load. Treated wheat, barley or peas, there’s no issue.”
Elenko’s air cart includes three main tanks and a smaller inoculant tank. On the main tanks, his split is 80 for phos, 140 for seed and 220 for his nitrogen blend.
His trailer is designed along the same ratios, but has a fourth hopper that he usually fills with nitrogen.
“For seeding, we’re running 1,500 bushels plus. We made that trailer particularly high on the sides, so we get more than three fills with it.”
Elenko said the four-compartment trailer, with remote controls at the top of the elevation auger, means he backs only one truck up to the cart and has to climb up and down only once.
“With the remote controls and the hydraulic gates so we can open and close things all by remote, we now have our time down. I can do it in 16.5 minutes and we can do it even quicker than that if my driver is around. We’ve knocked half an hour off the fill time. That is, in my view, a substantial achievement.”
On a normal day, Elenko seeds about 90 acres per fill and about 38 acres an hour. If he stops for 15 minutes, he loses 25 percent efficiency and is down to 30 acres an hour.
“We’ve gained 30 minutes a fill, so that’s close to 20 acres. Over four fills a day, that’s an extra two hours a day. If I start a half section in the morning, I’m out of there by suppertime. You can have a breakdown, move to another field and still get set up before dark.”
He can use the extra time to seed another 80 acres, give himself extra time to move between fields or do other jobs.
“Over a 20-day period that’s 1,600 acres. That starts me thinking that I can get by with one unit, or a unit and a half with rentals.”
To move the unit, Elenko folds the elevation conveyor down and slips it neatly behind the trailer. One change he might make is to have it fold up and lay on top of the trailer to improve ground clearance.
He said the assembly is fairly simple to remove if he wants to use the trailer to haul grain after seeding.
The middle transfer conveyor stays on, but the bottom and elevator conveyors come off and the trailer can be used as a regular highway unit.