EDMONTON – While all farmers are feeling the pinch from increased energy costs, greenhouse operators may suffer the most.
That’s why energy prices were a hot topic at the Alberta Horticulture Congress held in Edmonton last week.
The Alberta greenhouse industry boasts nearly 400 operations that cover 285 acres, generate $135 million of annual gross revenue per year and employ 5,000 full and part-time workers.
While some greenhouses heat with coal, propane and other energy sources, 82 percent use natural gas. With natural gas prices on the rise, greenhouse operators are keen to find ways to conserve energy.
Read Also
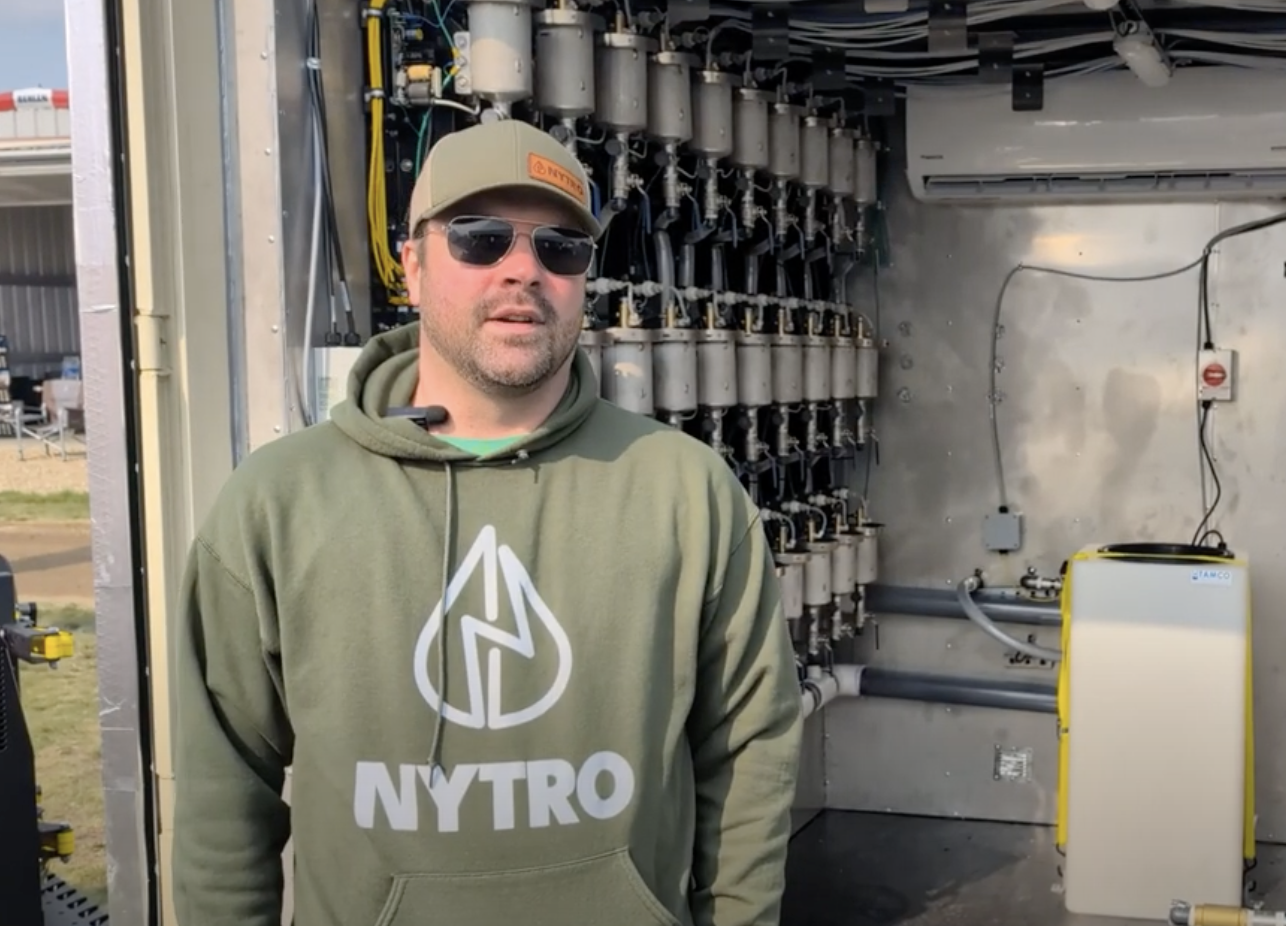
VIDEO: Green Lightning and Nytro Ag win sustainability innovation award
Nytro Ag Corp and Green Lightning recieved an innovation award at Ag in Motion 2025 for the Green Lightning Nitrogen Machine, which converts atmospheric nitrogen into a plant-usable form.
Mohyuddin Mirza, a greenhouse specialist with Alberta Agriculture, hosted a series of speakers, who all presented various energy conservation aspects. Mirza started the presentation with a few observations of his own.
“Sixty to 80 percent of the heat is lost through the roof,” said Mirza. “Thermal curtains can drop heating costs 20 to 30 percent, but they are still quite expensive.”
He said winds of 25 km-h can double heating costs in greenhouses. Windbreaks are a simple, but cost-effective solution to control energy costs.
“Curtains are the number one thing you can do to save heat, as long as you can retrofit your greenhouse,” said John Bouw with Dentoom’s Greenhouses in Red Deer.
“We have to start decreasing our air temperatures in our greenhouses about an hour before sunset because we get such a spike (in temperature) when the curtain closes. Our boilers, on a cold winter day, are going full blast all day. When the curtain closes at night, they’re silent.”
The curtains also provide shade in the summer, reducing the load on cooling fans, Bouw added.
Darren McPherson with Modine Heating Equipment in Edmonton said greenhouses must get the most out of their forced air furnaces. Because many greenhouses operate with high carbon dioxide levels, oxygen for the furnaces may be lacking.
“You have to have adequate combustion air to your unit heater. You need one sq. inch (of inlet) for every 1,000 BTUs of input rating on your furnace. If it’s 400,000 BTUs, you need 400 sq. inches.”
Gas pressure can also affect burn efficiency.
“With natural gas, off the main regulator on the upstream side of that gas valve, you should have six to seven inches of water column. On the downstream side of that gas valve, that should be 3.5 inches Ð no more and no less,” McPherson said.
“LP gas is 11 to 14 inches, with 10 inches downstream.”
Three other presentations dealt with alternative heat sources that would require large capital cost conversions, but could provide fuel sources that are more stable and economical than natural gas.
Rob Rimes with Energy and Material Solutions Inc. in Edmonton, said biomass, including waste wood, is fairly new and no greenhouses are operating with it yet, although some are considering it.
Wood sources include sawdust and waste wood from mills. Considering that an estimated 180,000 to 360,000 tonnes of waste wood are delivered to Edmonton landfills annually, Rimes said using this material to generate heat would have multiple benefits.
He said his waste wood boiler could provide a 64 percent energy saving over natural gas at current prices.
Terry Dewhurst with Foss Fuel Heating in Edmonton sells or leases a mobile coal boiler on skids. The large model produces two million BTUs while the smaller unit produces 750,000 BTUs. He said the system would work best for greenhouses smaller than 20,000 sq. feet.
Dewhurst said with natural gas at about $10 per gigajoule, 40 percent of a greenhouses operating cost is consumed by energy. With coal costing around $3 per gigajoule delivered, energy costs drop to 12 percent of operating costs.
He said it costs approximately $1.40 per sq. foot to heat a greenhouse with natural gas, while coal costs about 46 cents per sq. foot.
Dewhurst and Rimes admitted their cost savings don’t include the capital cost of converting from existing systems. However, the stable cost of their energy sources could make their units attractive.
Jim Jones, a biogas specialist with Alberta Agriculture’s agri-industrial branch, said there are opportunities for biogas production, but an economical model would probably have multiple users and use a range of feedstock to produce electricity, heat and other salable products.
He said Germany has more than 4,000 biodigesters, which use municipal garbage, sewage and other feedstock. While the western Canadian focus has been on animal manure, he said it will probably be necessary to blend agricultural, municipal, rendering plant and other materials to make biogas digesters economically feasible here.