MORTLACH, Sask. – When Philip Simrose built his shop in 2003, he wanted to be able to drive in the door with the header still on his combine.
“I wanted to make it accessible to the different machines I have. I figure if you’ve got a shop, you should be able to take the equipment you have into it,” said Simrose, who farms near Mortlach.
“I had seen in different magazines where people had built doors similar. I was planning to build a hydraulic door that you can open in one piece.
Read Also
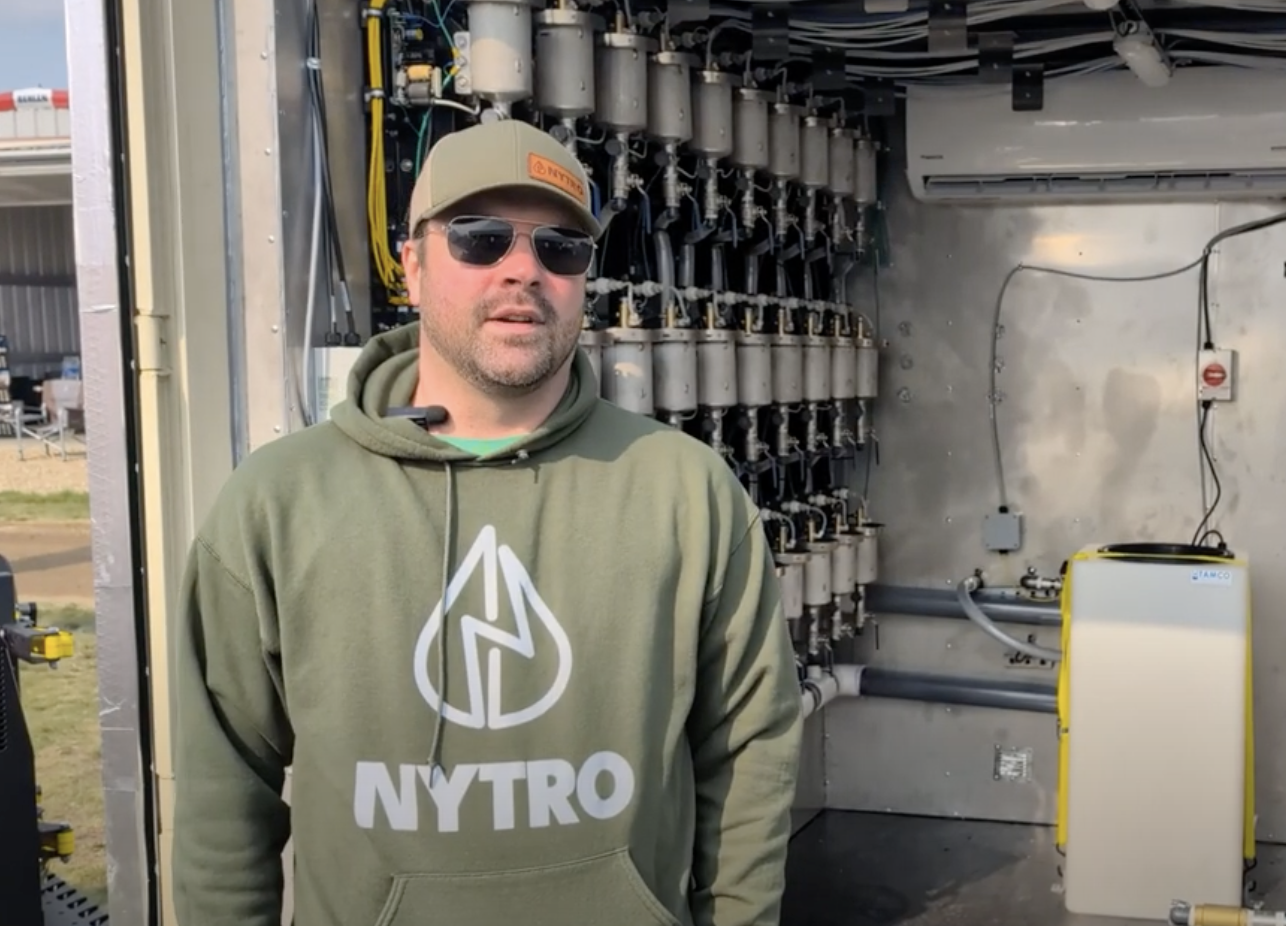
VIDEO: Green Lightning and Nytro Ag win sustainability innovation award
Nytro Ag Corp and Green Lightning recieved an innovation award at Ag in Motion 2025 for the Green Lightning Nitrogen Machine, which converts atmospheric nitrogen into a plant-usable form.
“The other reason for that is you’d save on heat because you can put a fairly thick door there, for insulation. And you don’t have as many openings as an overhead door. You don’t have as much chance for wind to get into the building, which is important in this country.”
The building is a pole shed, with square poles. The door fits into heavy angle iron, bolted to the wood door frame.
“The two sides have heavy angle irons bolted into them. Then they’re welded together to the cross angle iron, which goes across the top. That piece is bolted into a double truss. Then it’s all welded together,” Simrose said.
“(The door is) hinged at the top with five hinges. They’re made with one-inch shaft and one-inch internal diameter pipe.”
Simrose used three by three gauge material to build the steel door frame.
“I made two channels with that and made the channels on the uprights, as well. I set in my steel tubing, put the channels in and welded them together,” he said.
“I had seen an ad for these sandwich panels. I phoned them up thinking of doing the whole building with the sandwich panels, but eventually decided to just put them in my door. They’re fairly light as well as strong.”
The panels are 16 feet long by three feet wide, made of three inch polyurethane foam, with an aluminum panel on each side.
“I made two grooves in the door – one on the top and one on the bottom – and set them in place that way. They overlap with each other and I pop riveted them together.”
Simrose added truss work on the outside of the door, with a truss along the bottom and three trusses running from top to bottom, to give it strength.
“The door is 16 feet by 42 feet and it opens with two hydraulic cylinders. I had an old hydraulic unit I got at an auction sale that I use,” he said.
“In order to keep the door so it opens evenly on both sides, I put a flow divider in. Even so, it does flex some from side to side. That’s probably the main reason I wouldn’t go with the styrofoam panels again. I’d do a steel frame, tin it on both sides with insulation in between.”
The original door design shut straight up and down, but after problems Simrose changed it so that it closed on an angle.
“When it shut, it was originally vertical. But I had trouble with gravel pieces getting underneath it. They’d jam the door and it wouldn’t open. So I changed it – set it at an angle – so it’s out about three feet at the bottom.”
If he was to build the door again, Simrose said he’d angle the door even more.
“The reason for that is so you wouldn’t catch the rocks underneath, plus when you angle it out, the weight of the door holds it down,” he said.
“To do it again I’d put (the bottom) out about six feet. With the angle out there, the door starts lifting immediately, so you don’t have the trouble with the rocks. Plus, I could lower my hydraulic cylinders down because they wouldn’t have to go as far. They’d be pushing at a lower angle, and there would not be as much strain on it all.”
The lower end of the cylinder is attached to the door, not quite half way down. The top end fits about two feet from the top of the door, right at the edge of the door frame. The whole setup is also braced to each side wall of the shop.
To help seal the door when it’s closed, Simrose used rubber from an overhead door dealer.
“You get a base plate you screw to wherever you want to put it. Then you get rubber that’s made to slide into the base plate that makes a bubble. It makes a nice seal.”
Simrose can open the door in less than 30 seconds. When it’s up, he gets 16 feet of clearance.
“When you lower it, you slow it down a bit. If you try to lower it too fast, one side will come down uneven,” he said.
“With overhead doors, you’ve got the rail and everything in the way, so it will cut your shop height down. With this, you’ve got full clearance.”